CyberOptics 003 WML-C40 User Manual 20171102 v1 11 11616692 AMS 8023533 REV E 2
CyberOptics Corporation WML-C40 20171102 v1 11 11616692 AMS 8023533 REV E 2
Contents
- 1. User Manual
- 2. Users Manual
- 3. User Manual_20171102_v1 - 11_11616692 AMS-8023533-REV_E (2)
- 4. User Manual_20200121_v1 - 11_APS3-8025869-User-Guide-REV_A resize
User Manual_20171102_v1 - 11_11616692 AMS-8023533-REV_E (2)
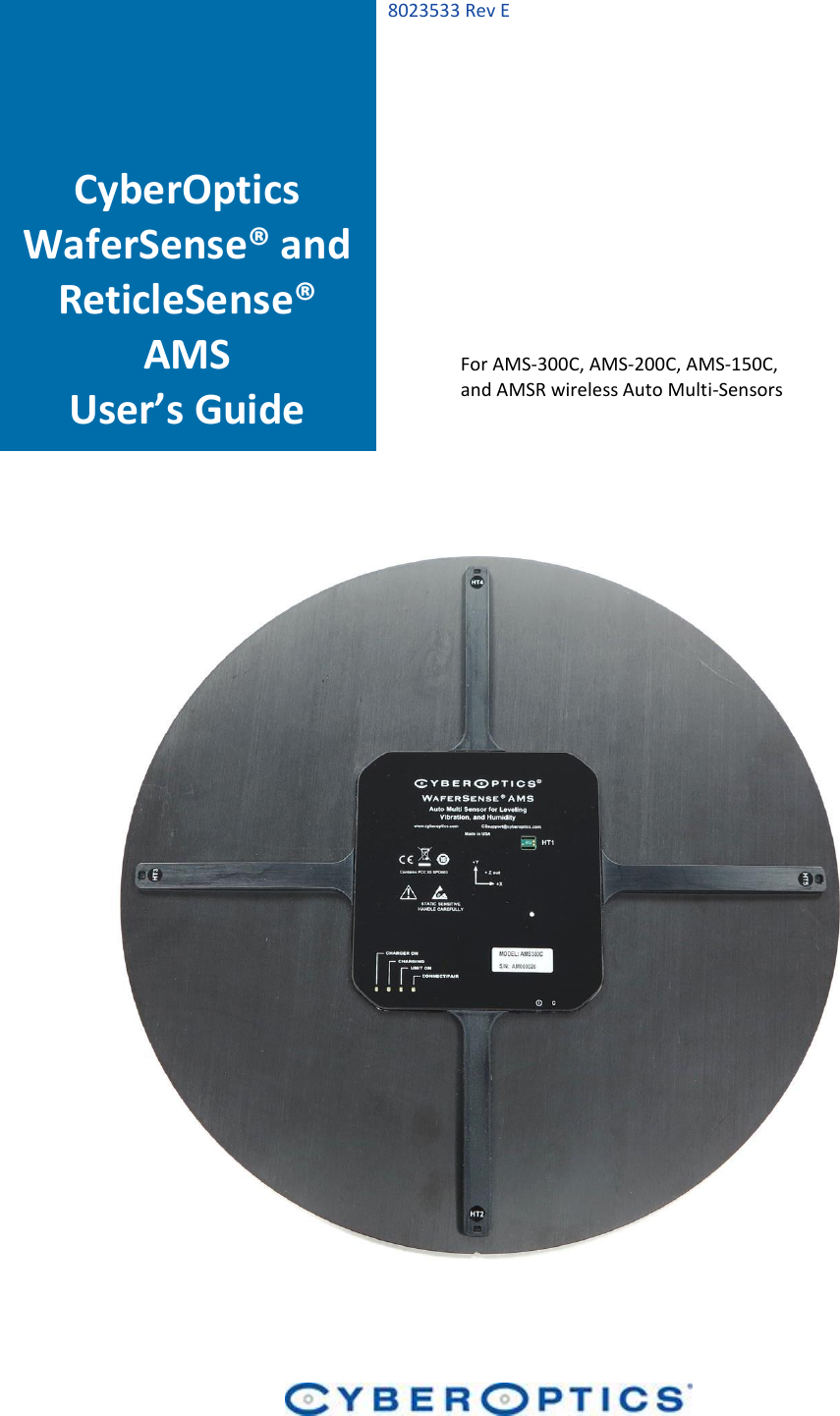
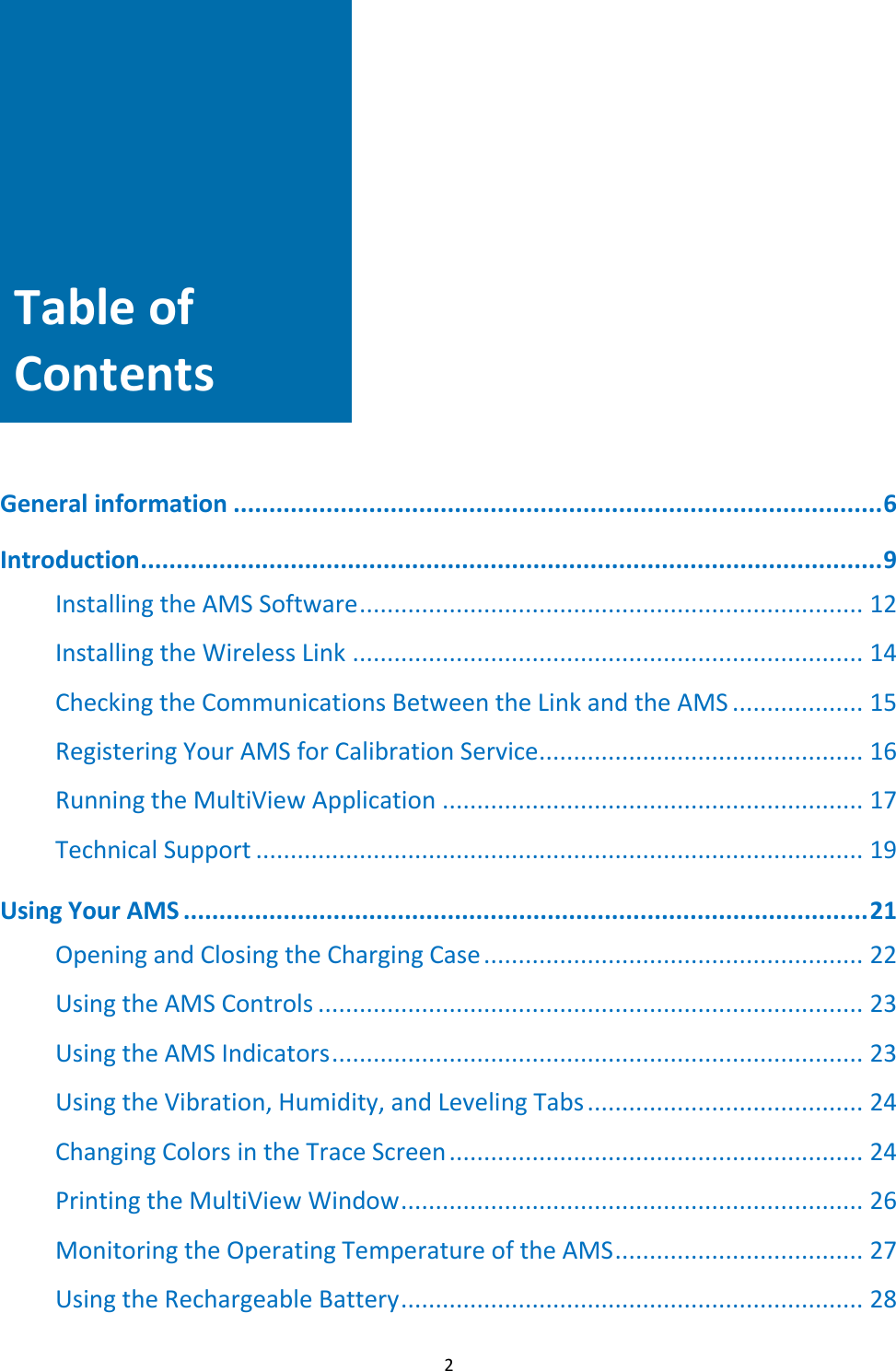
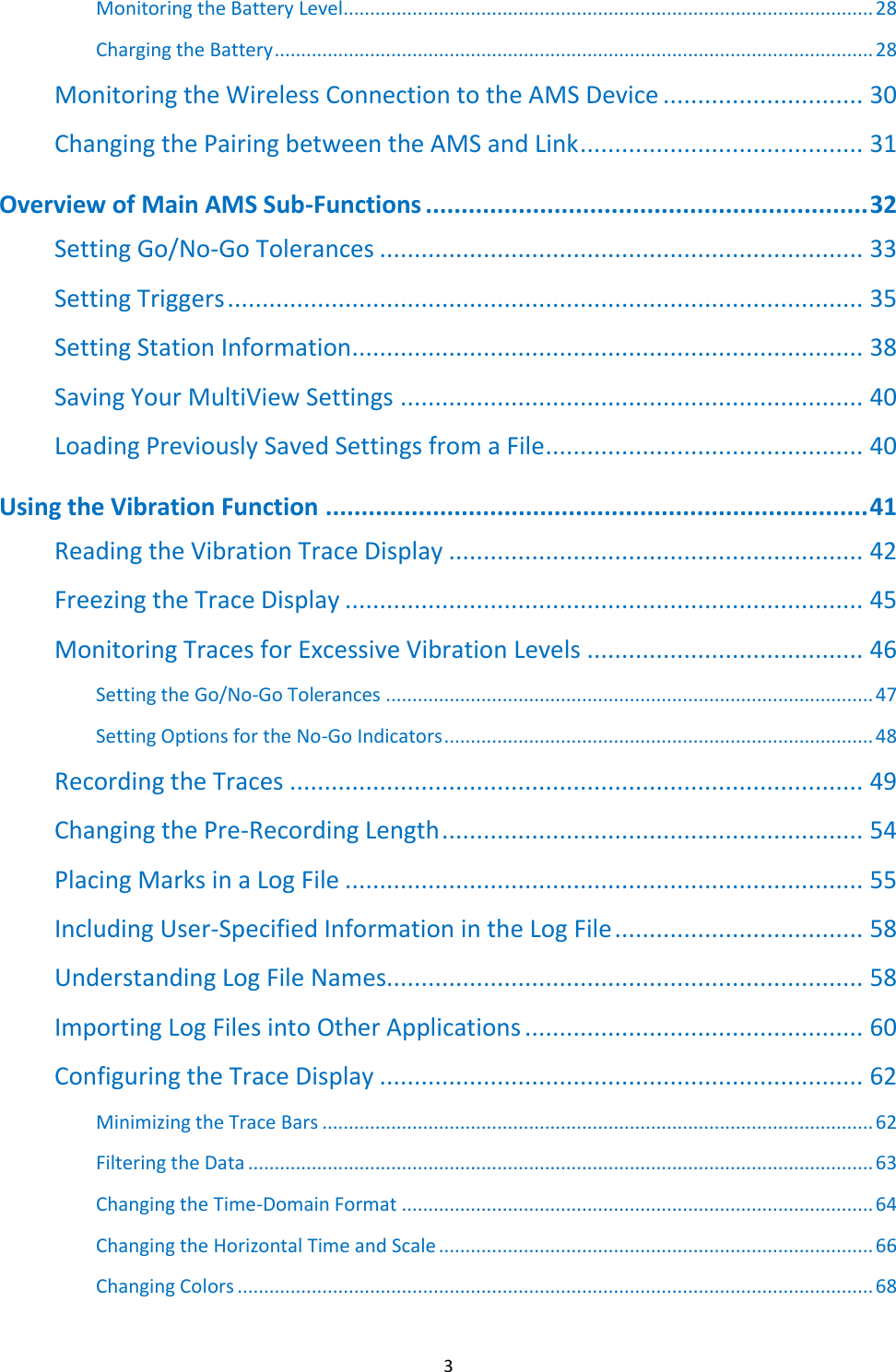
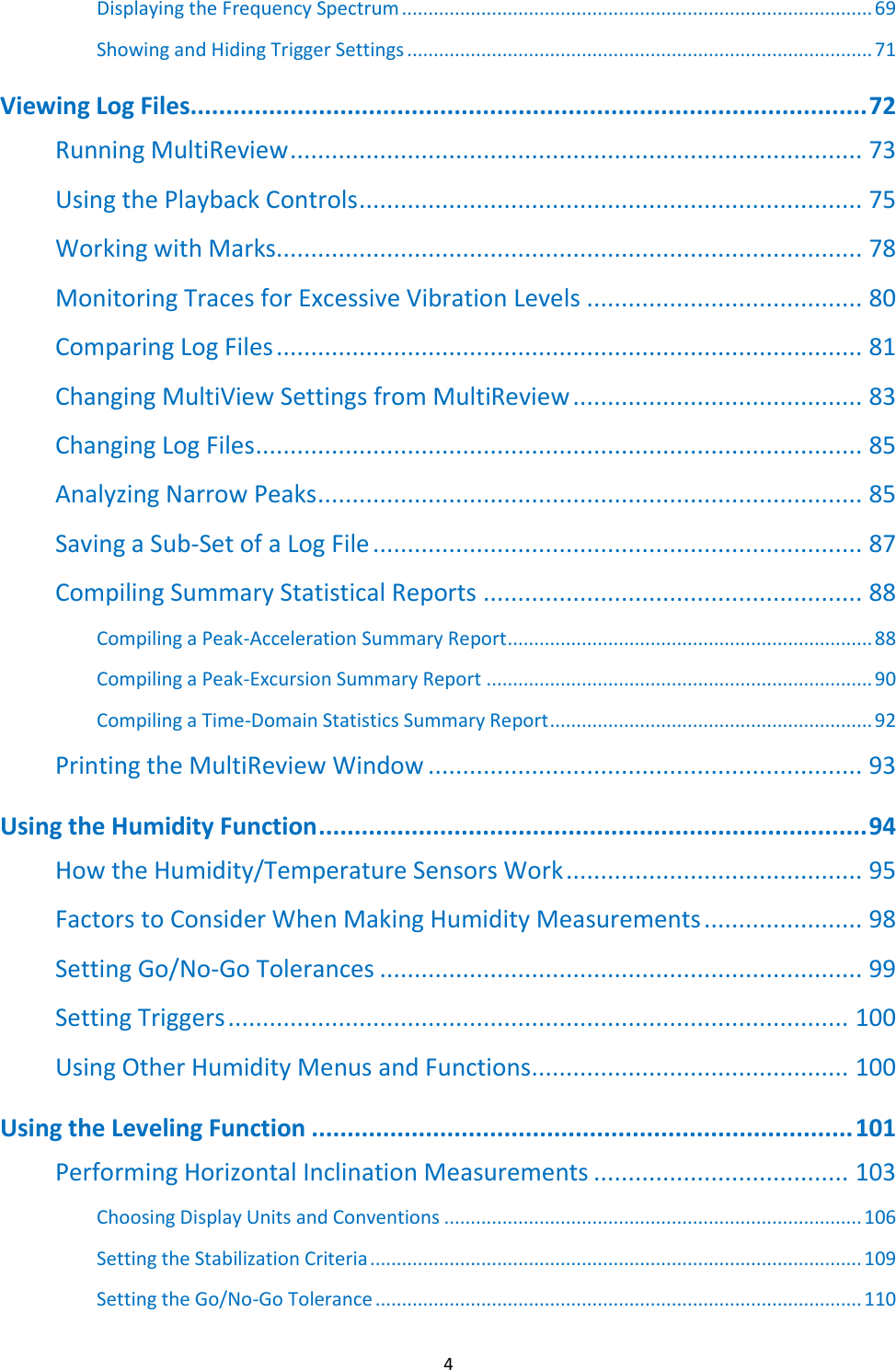
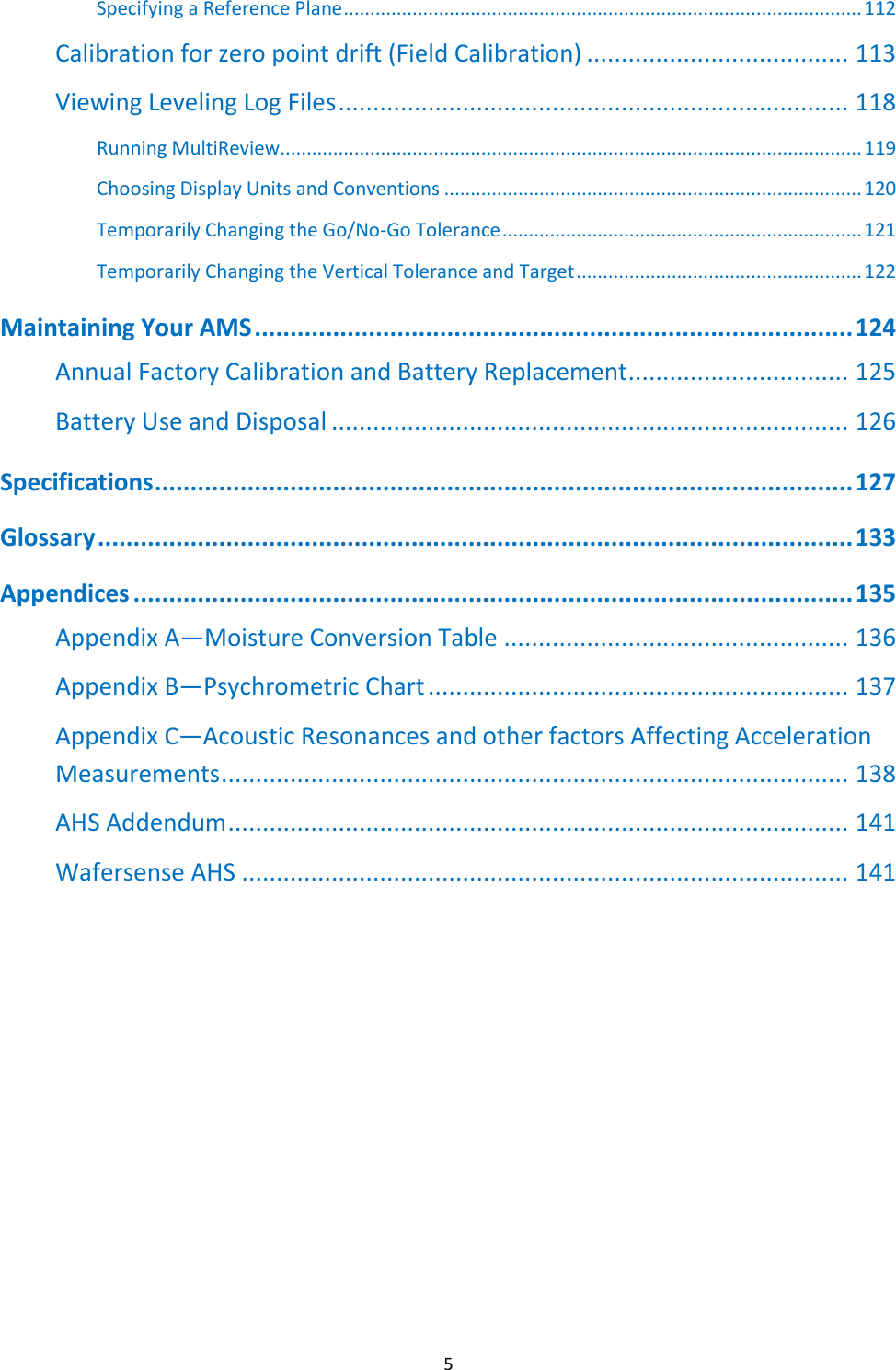
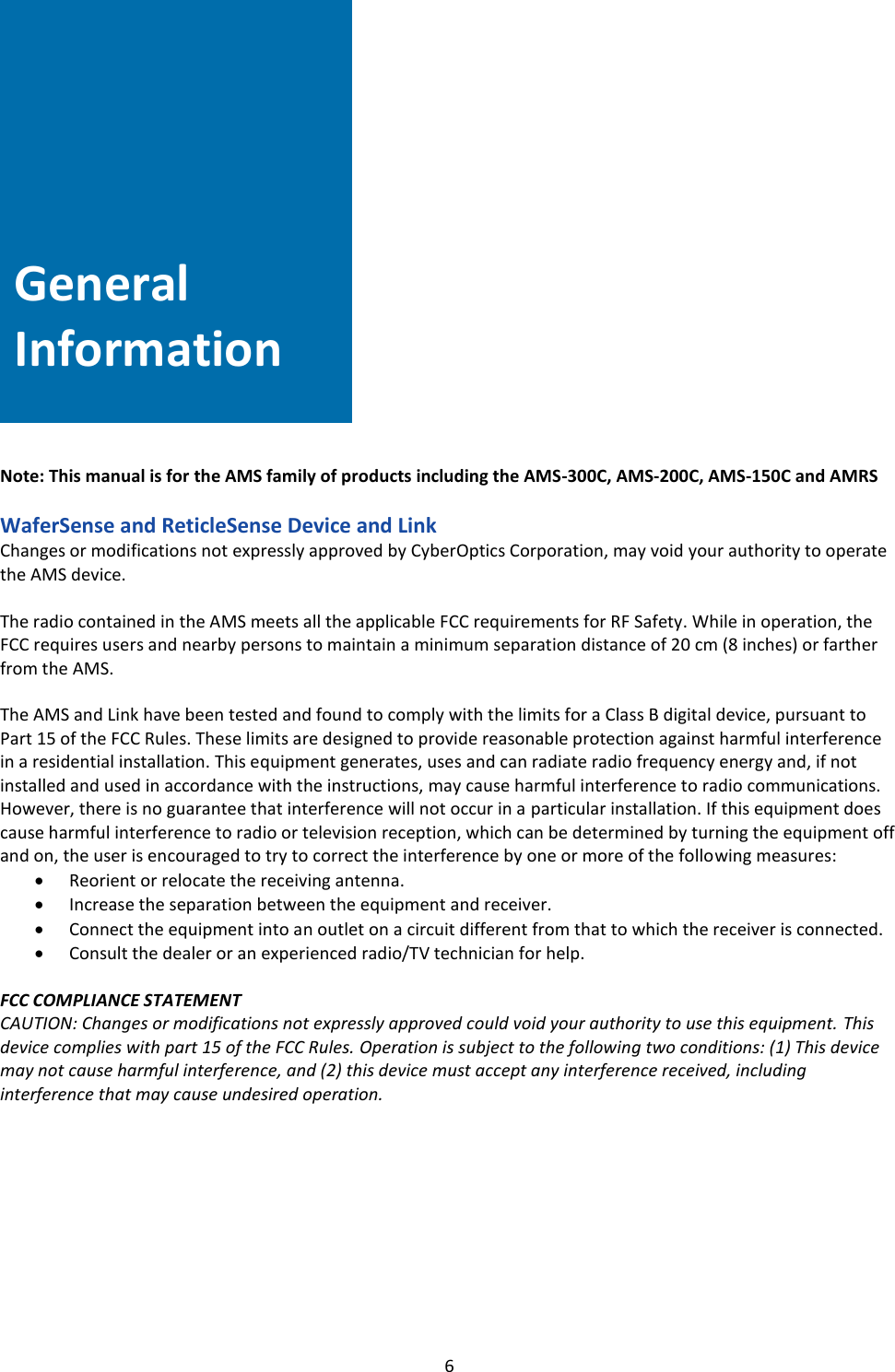
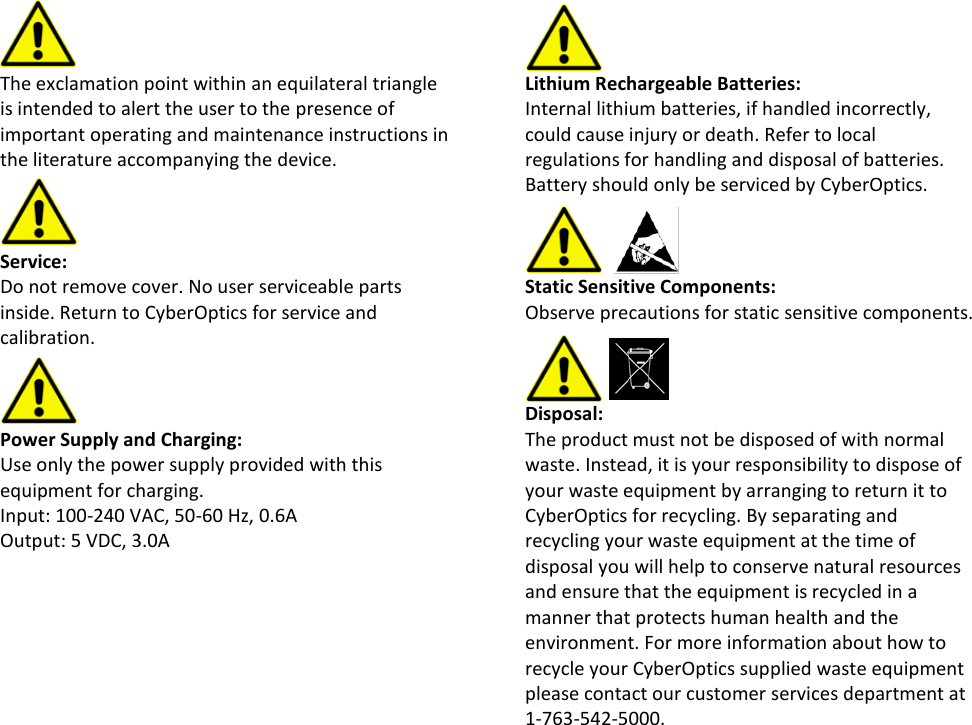
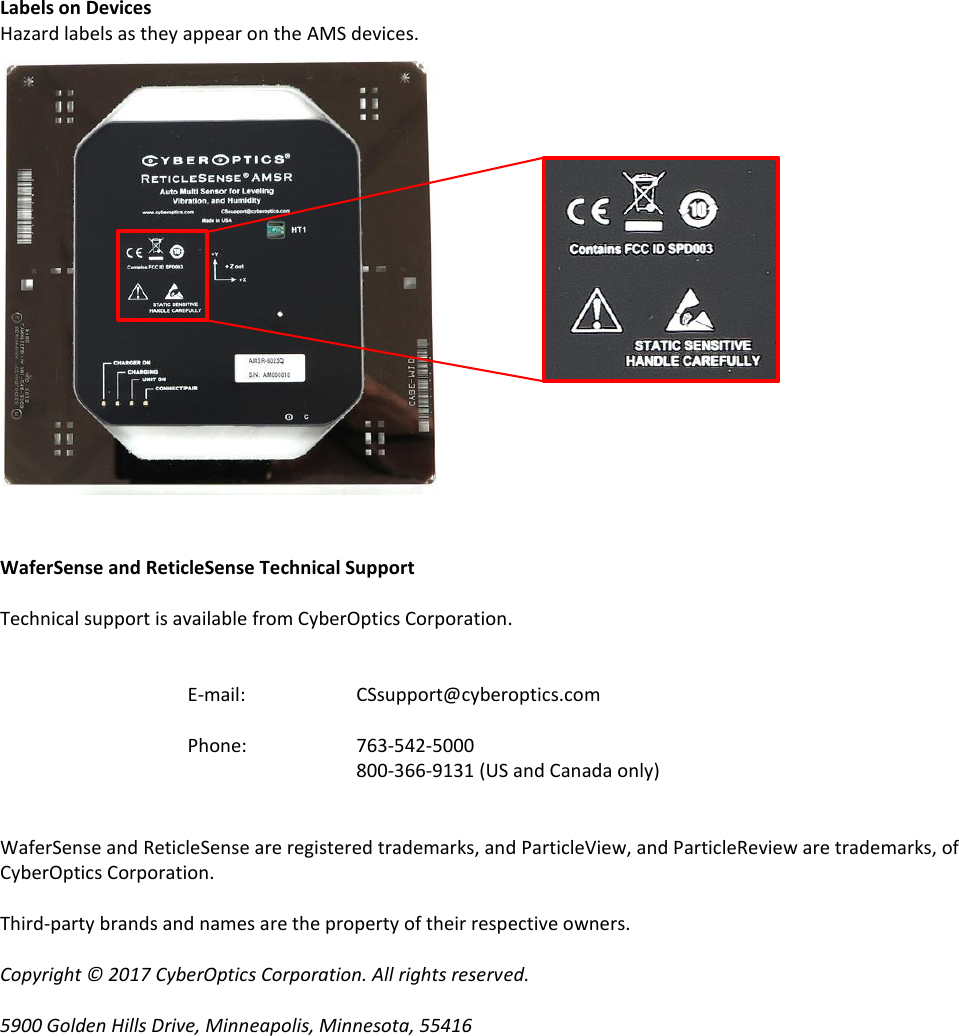
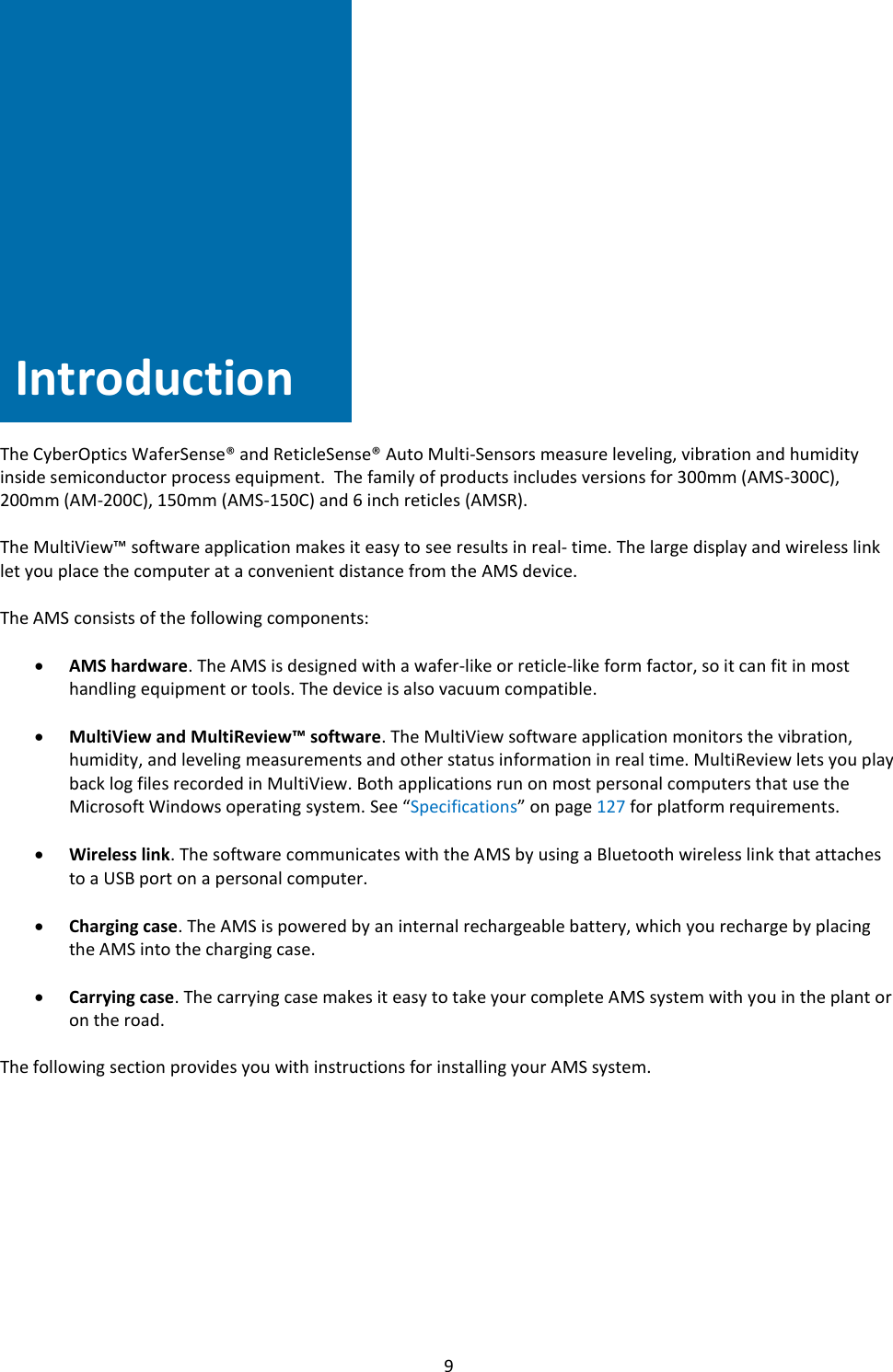

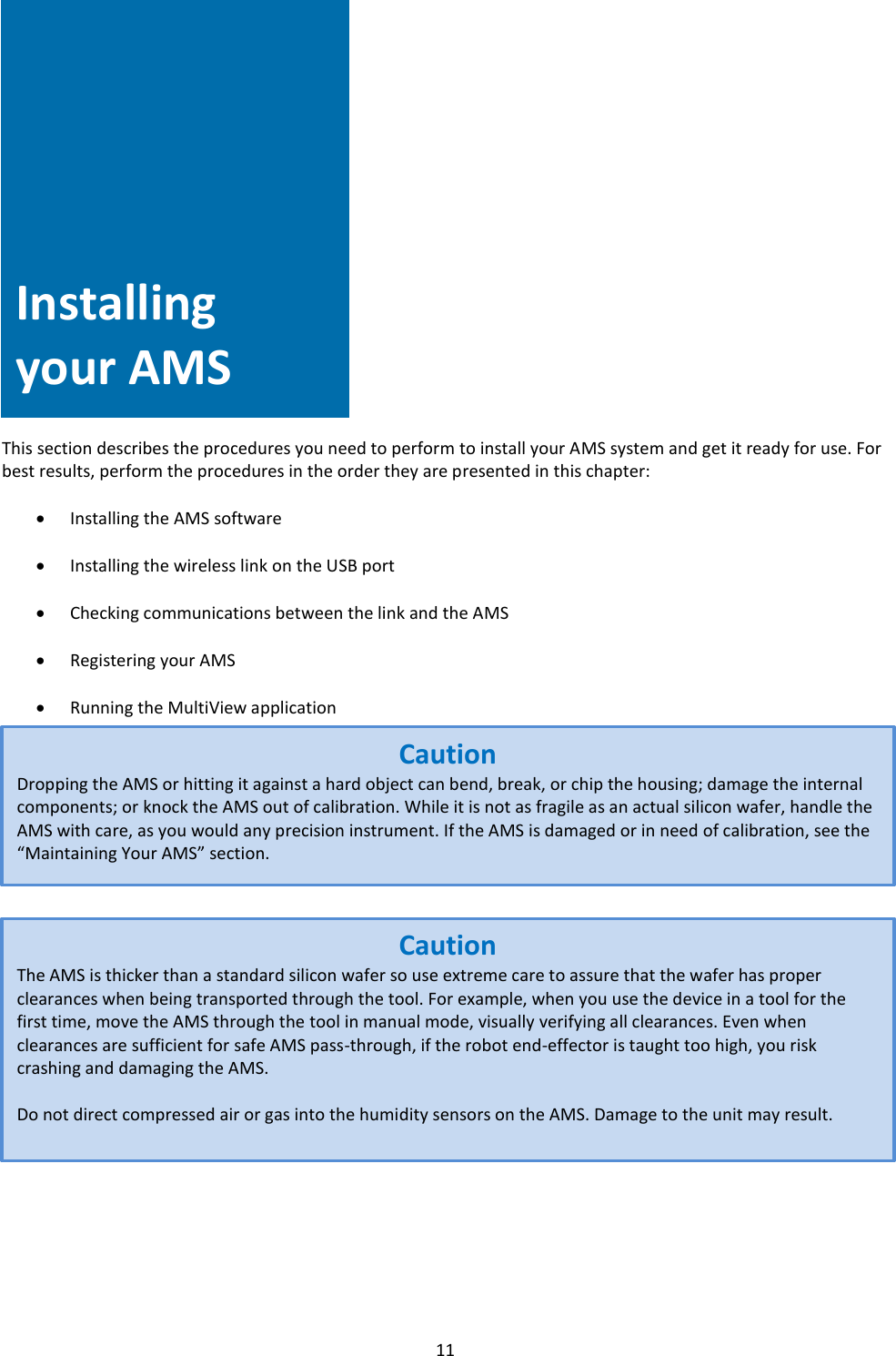
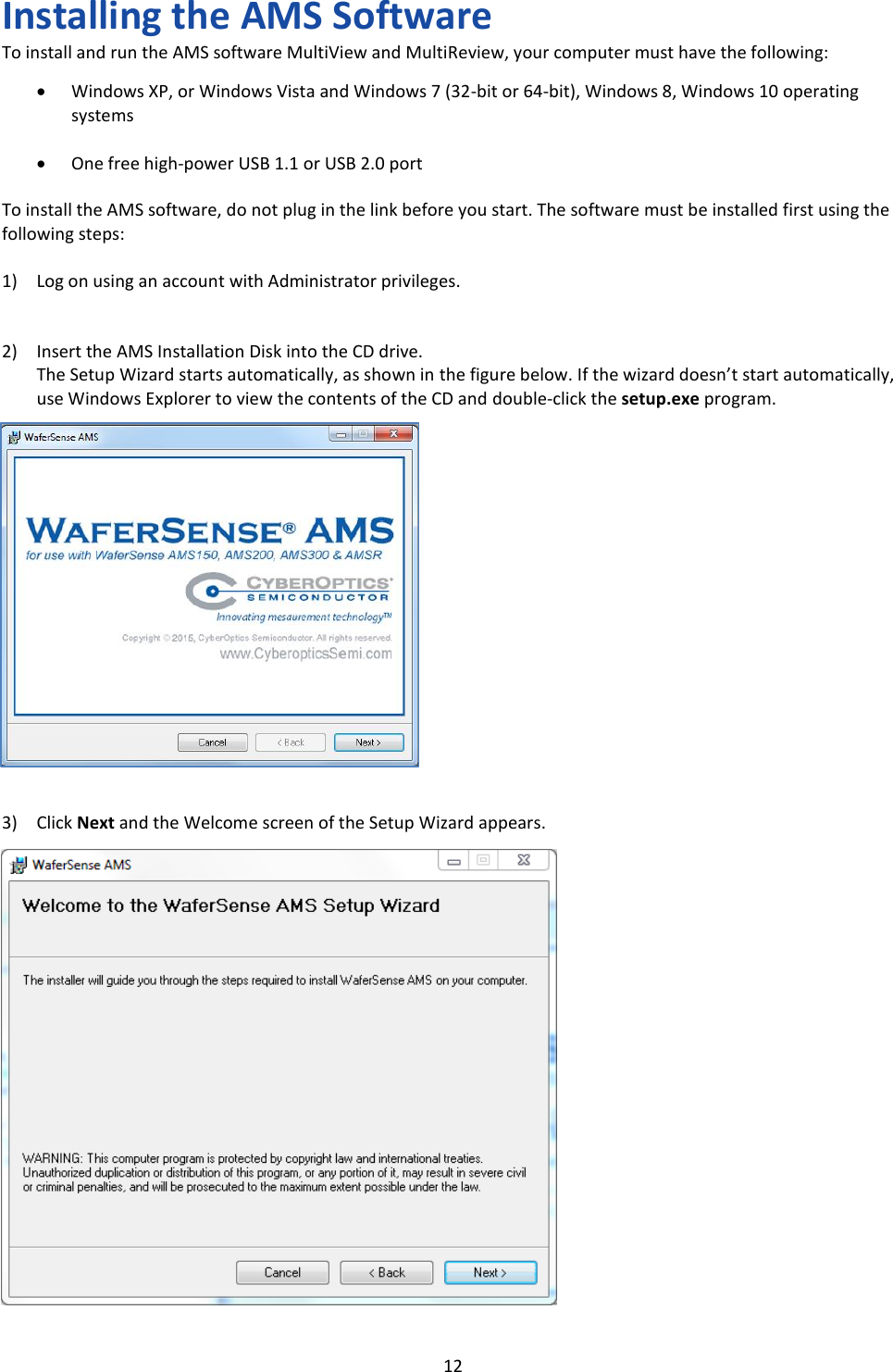
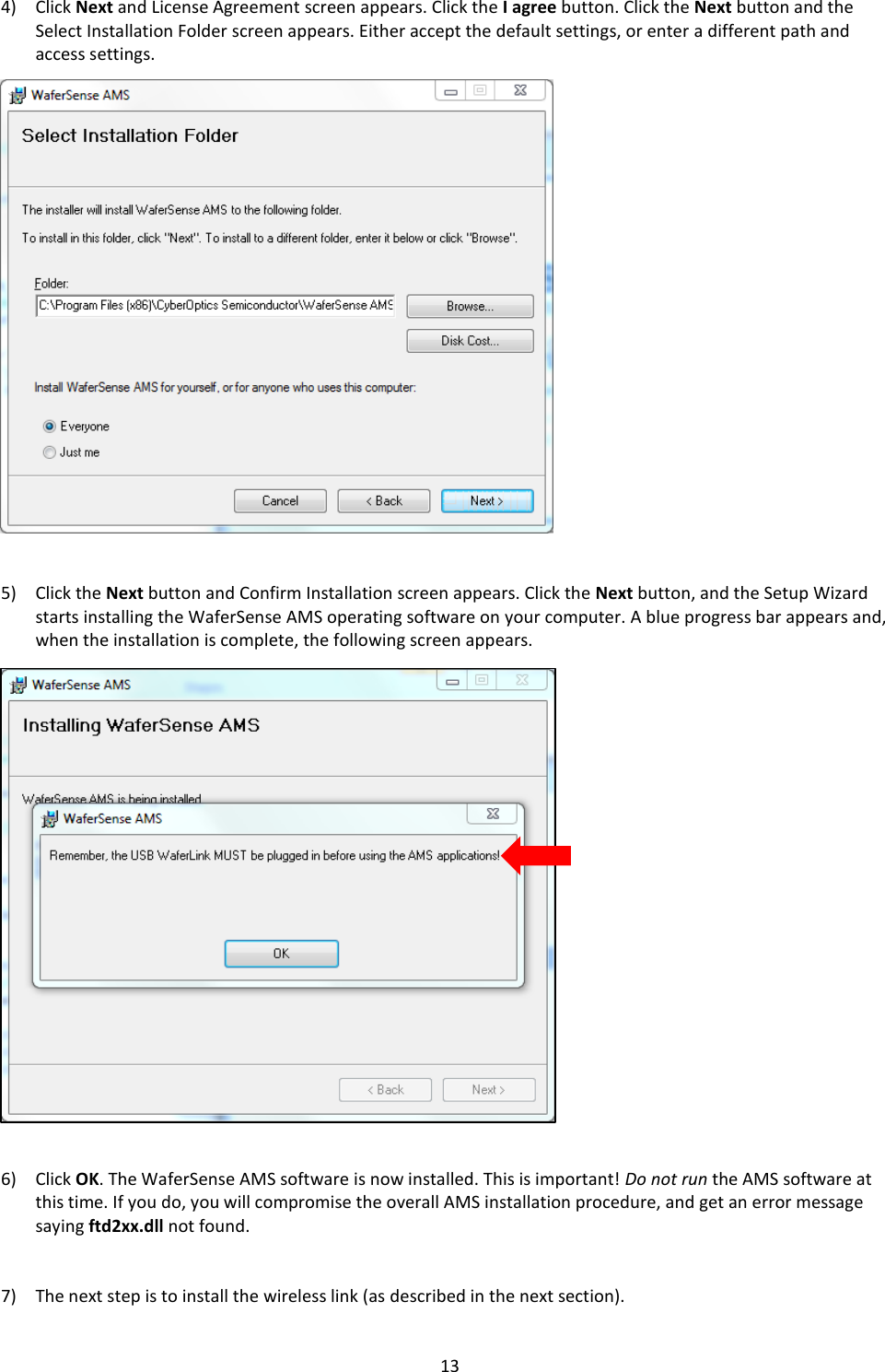
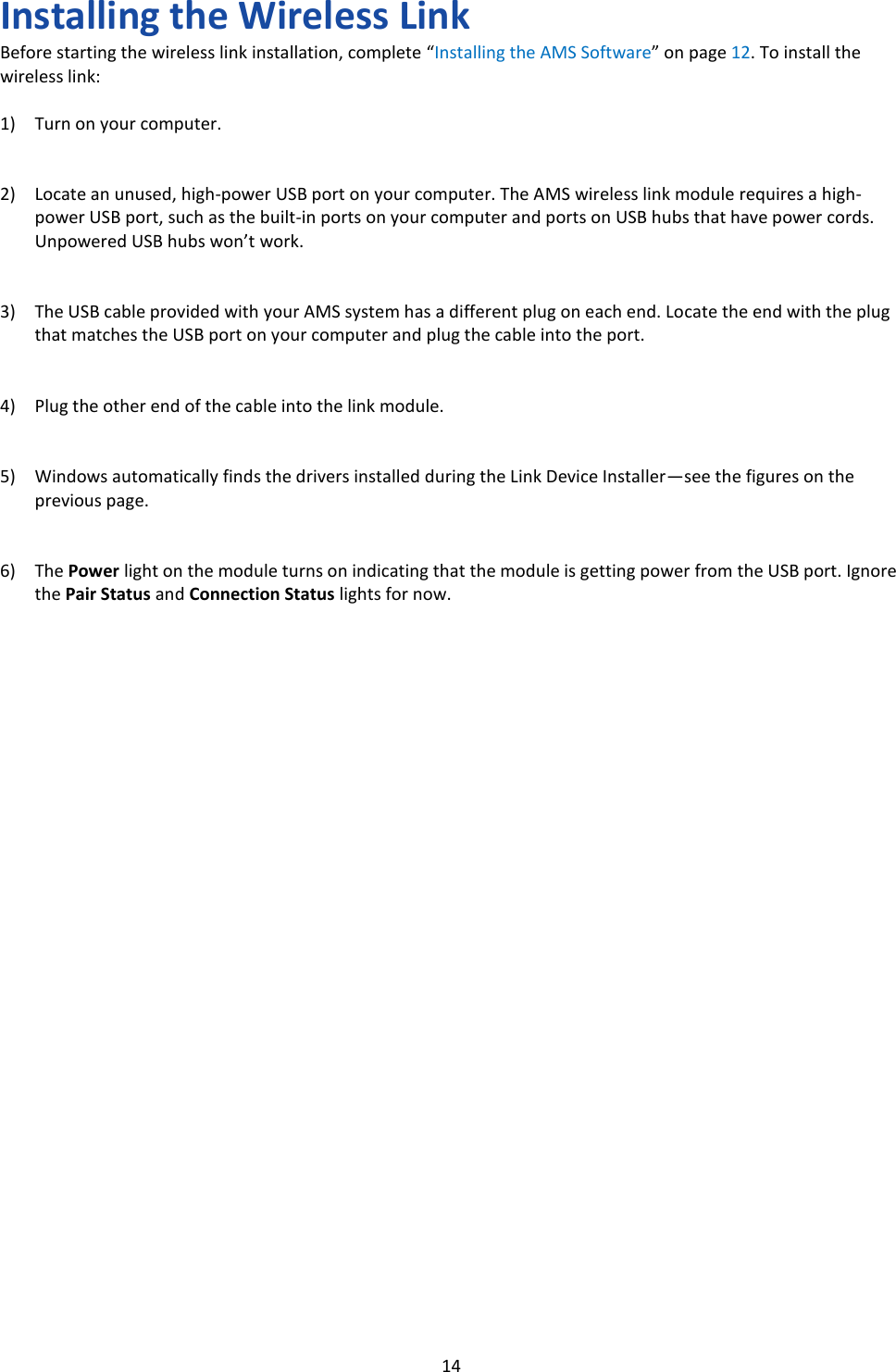
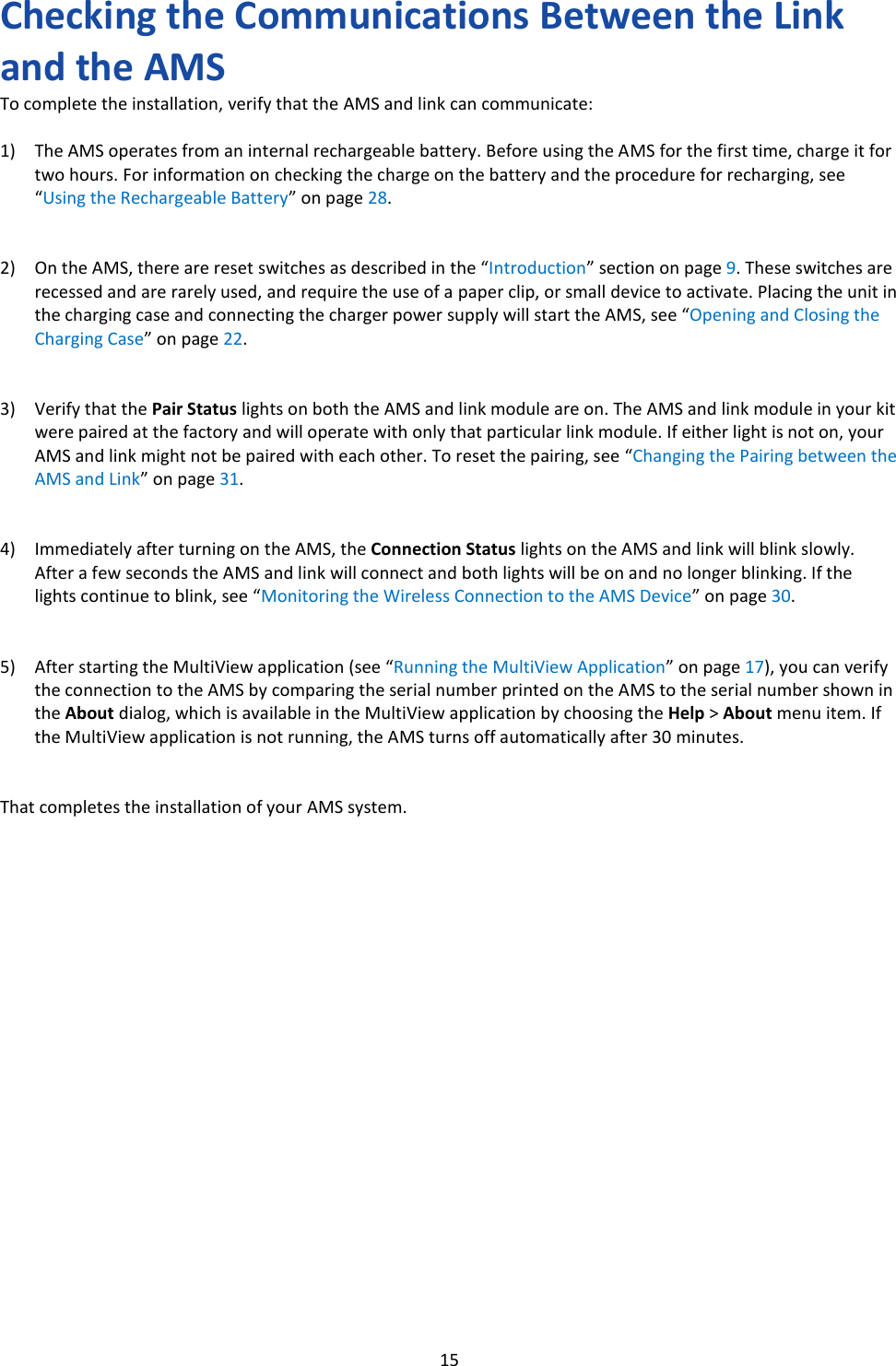
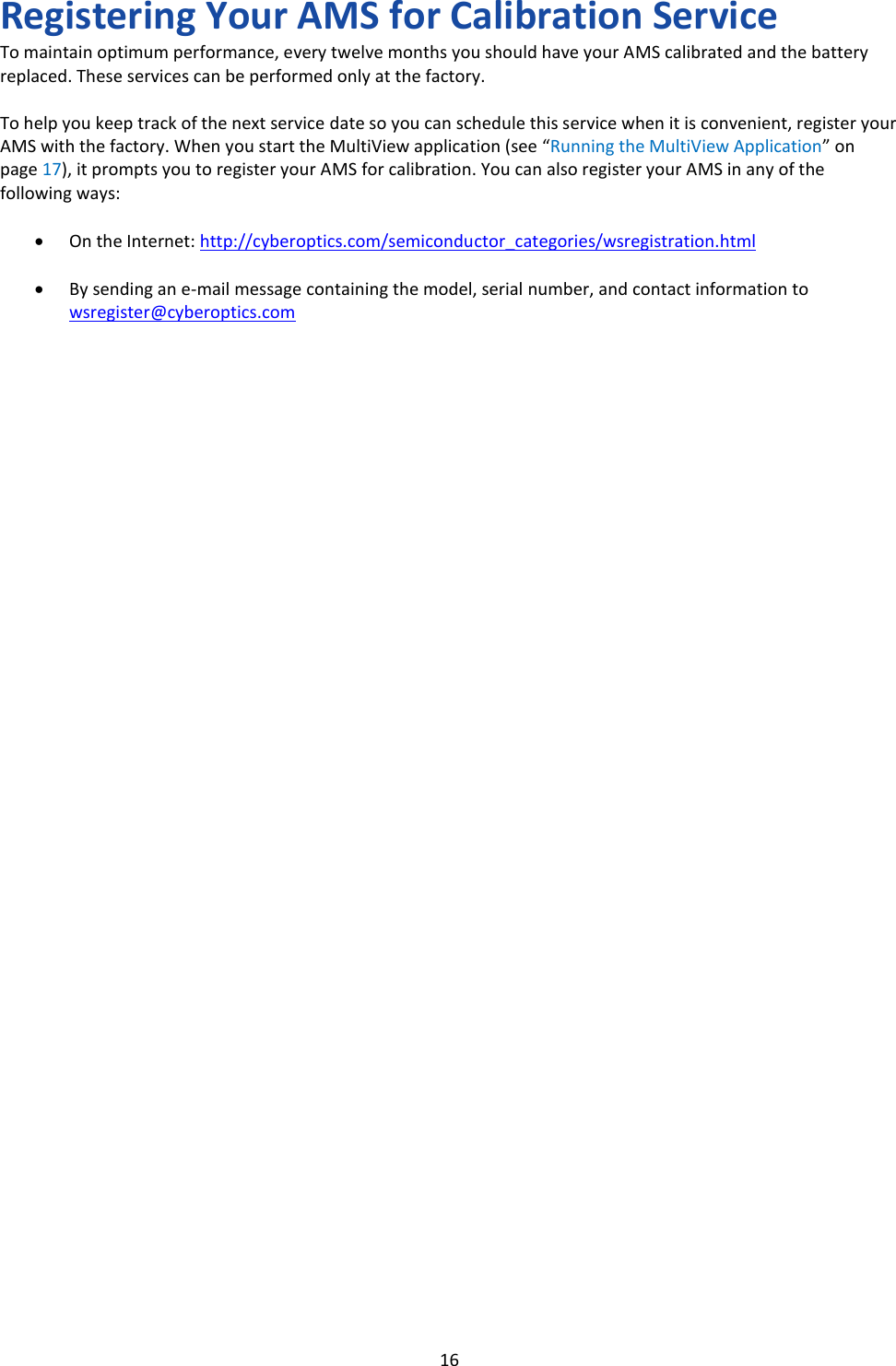
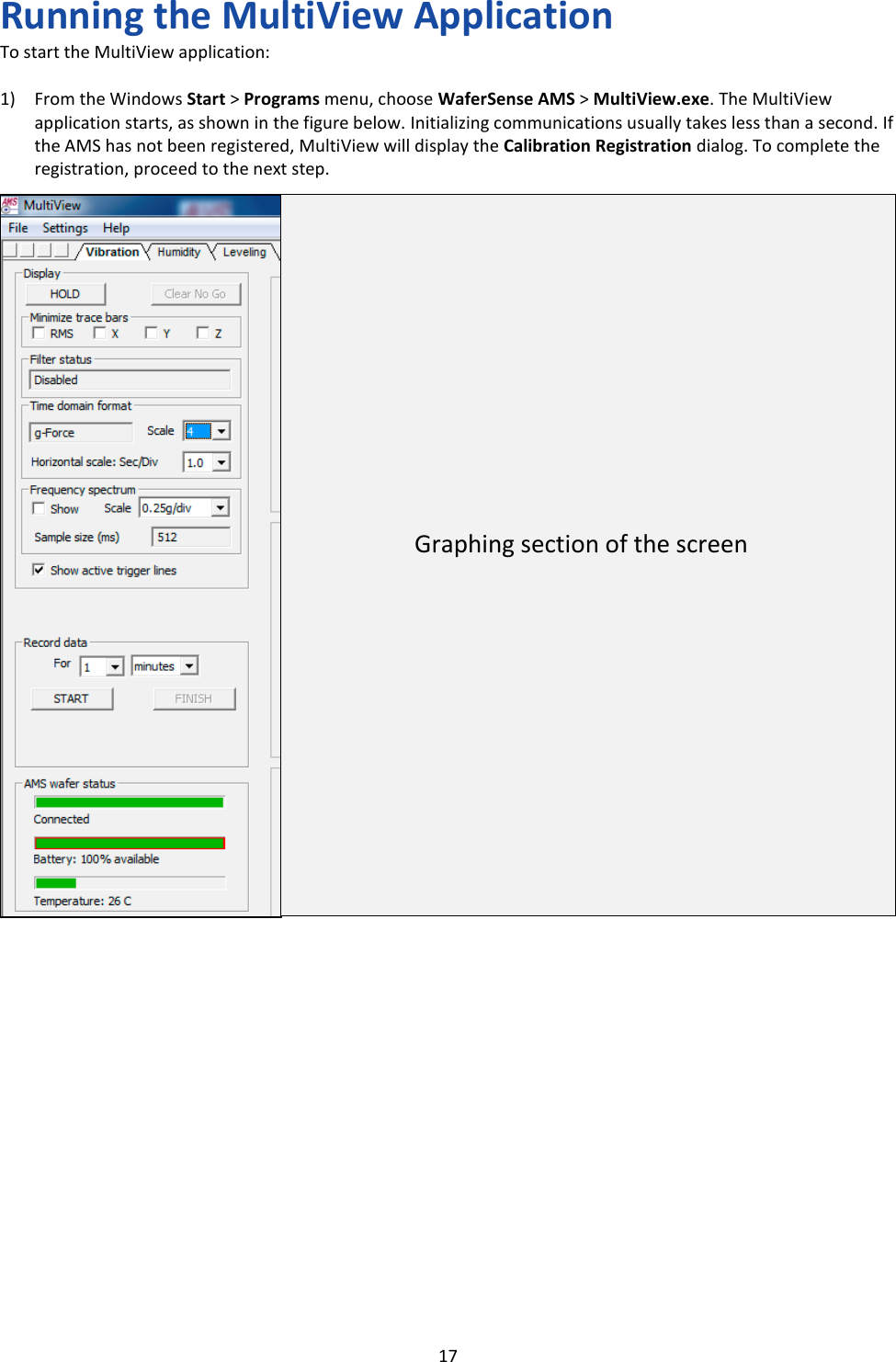
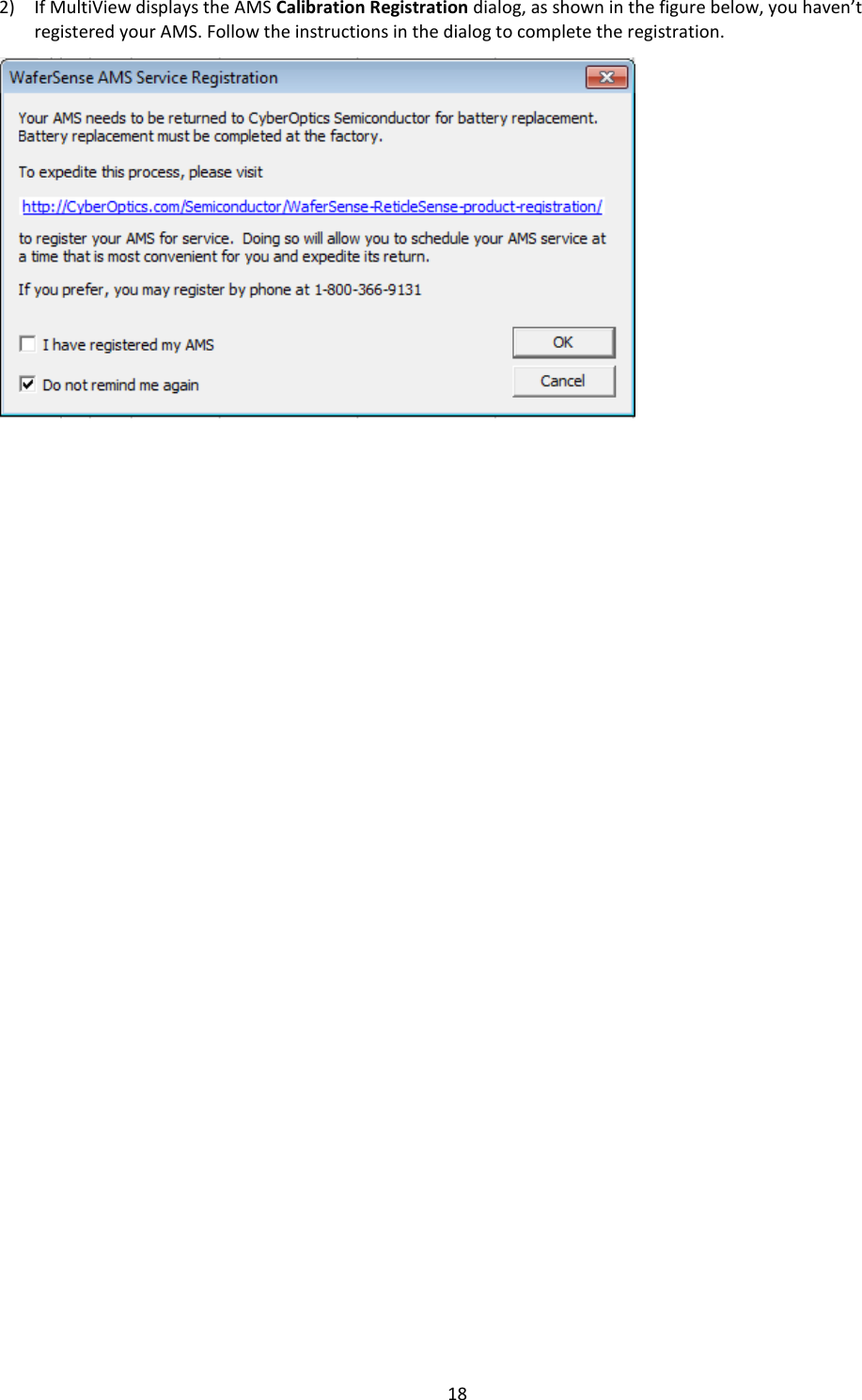
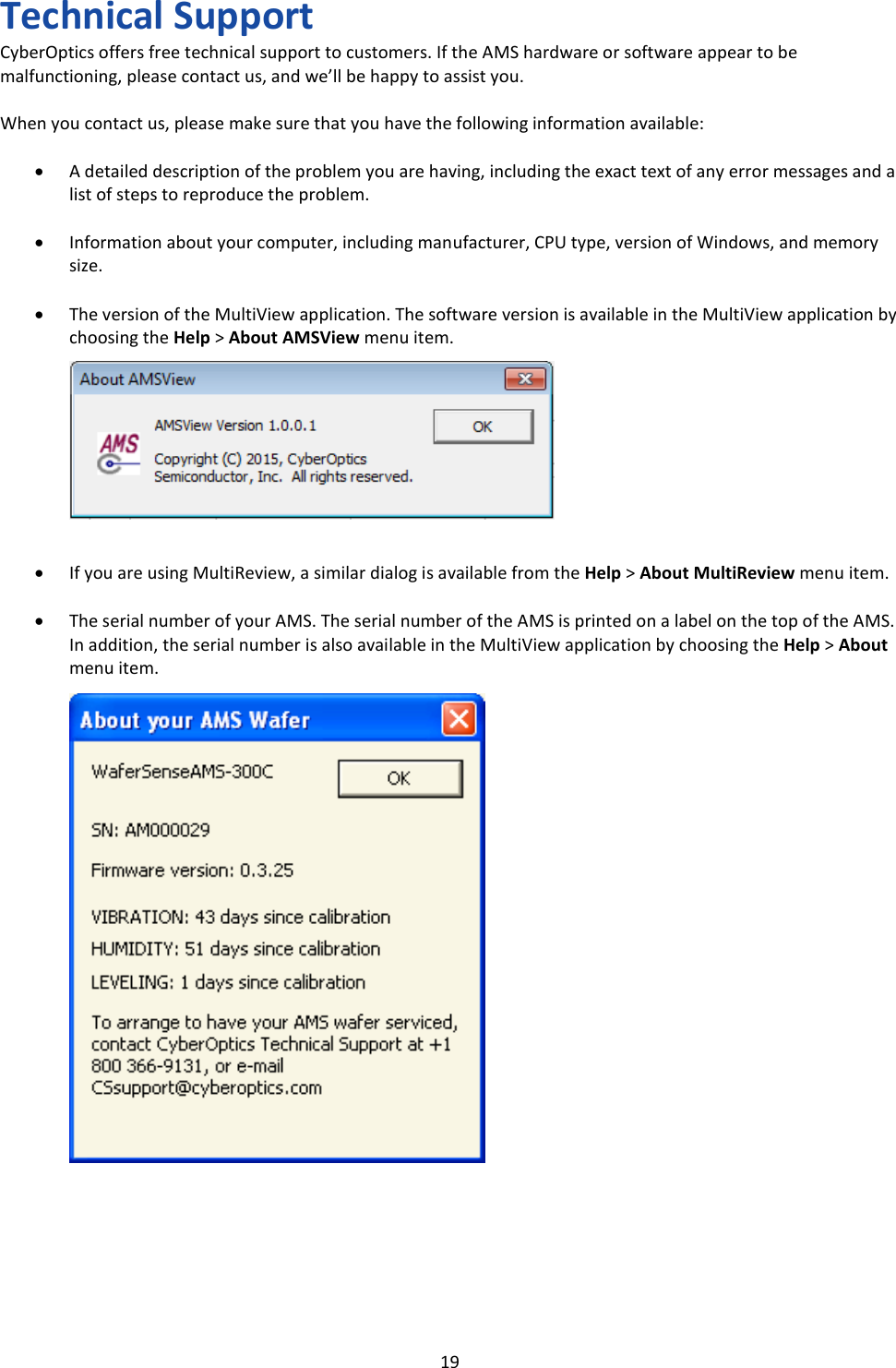
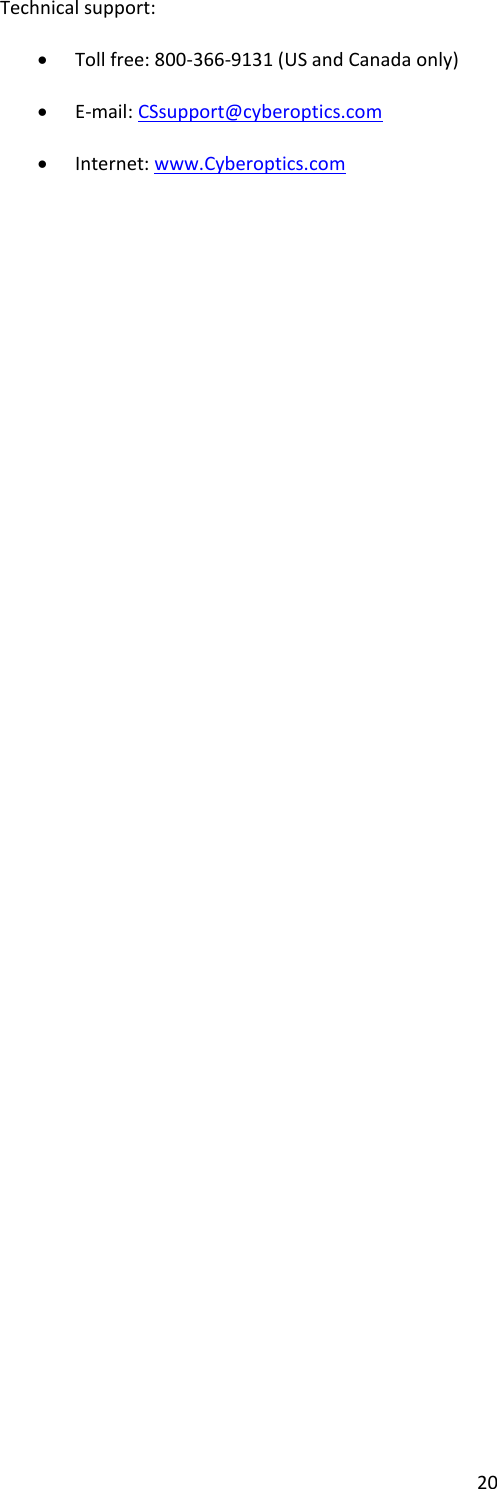
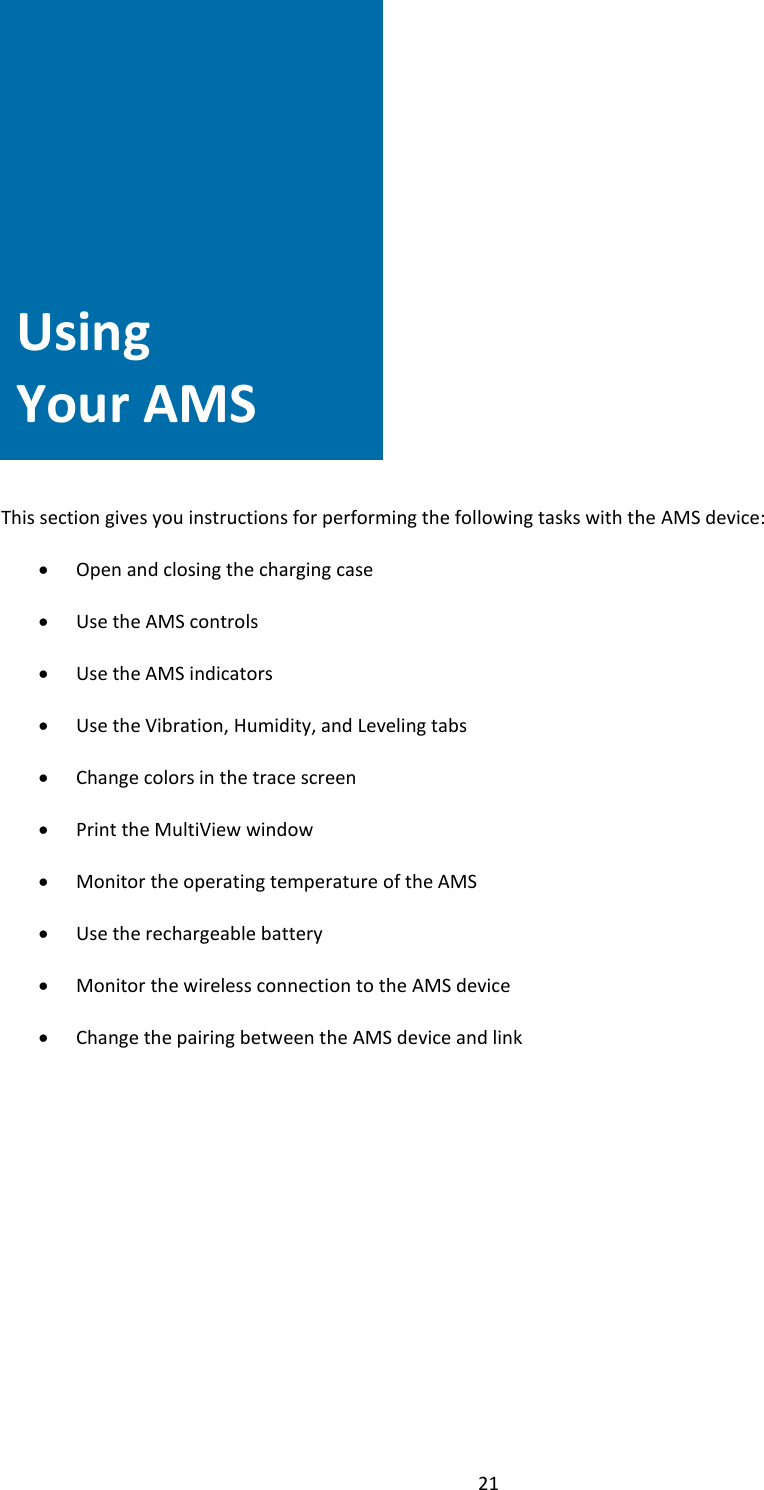
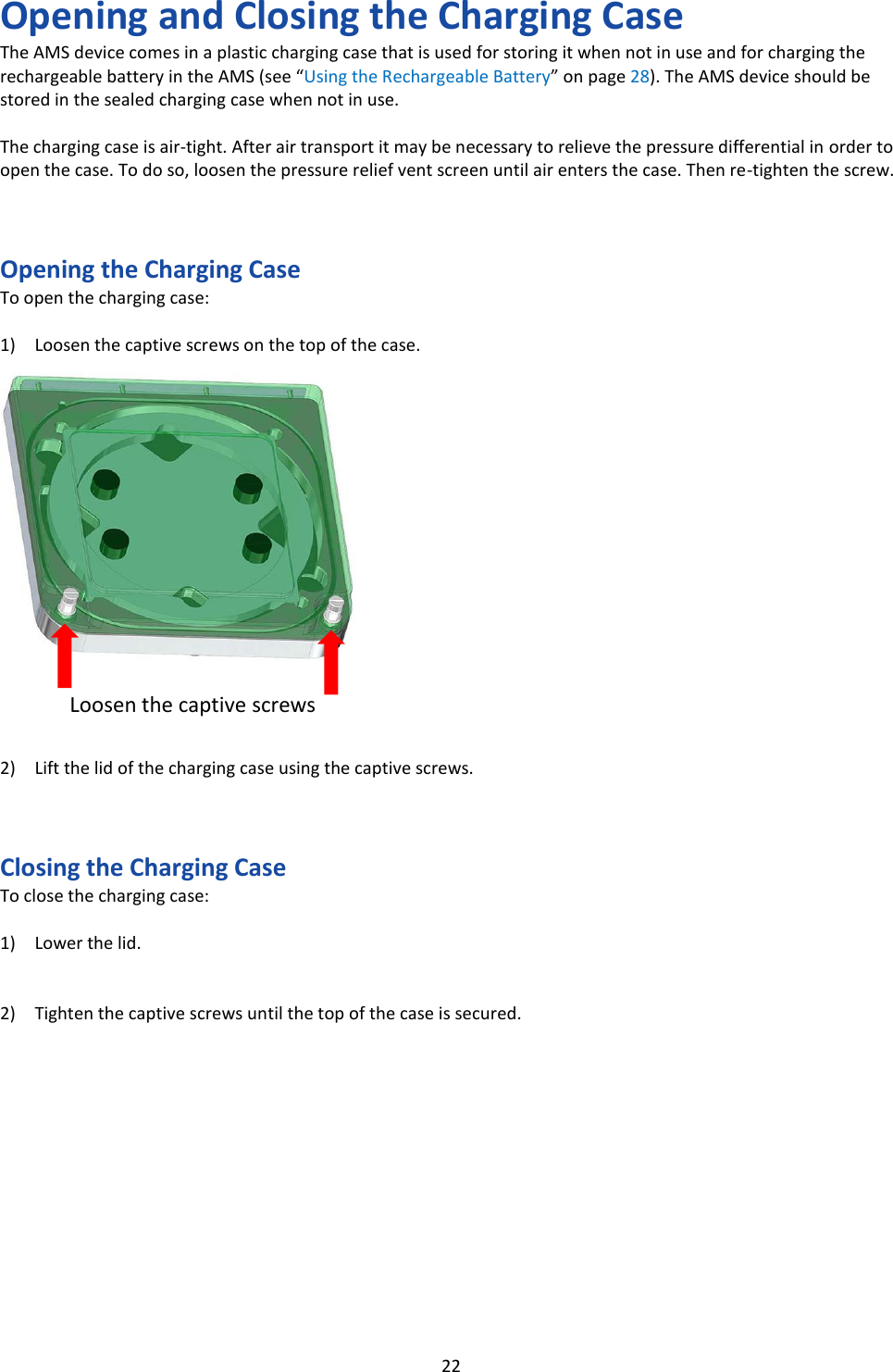
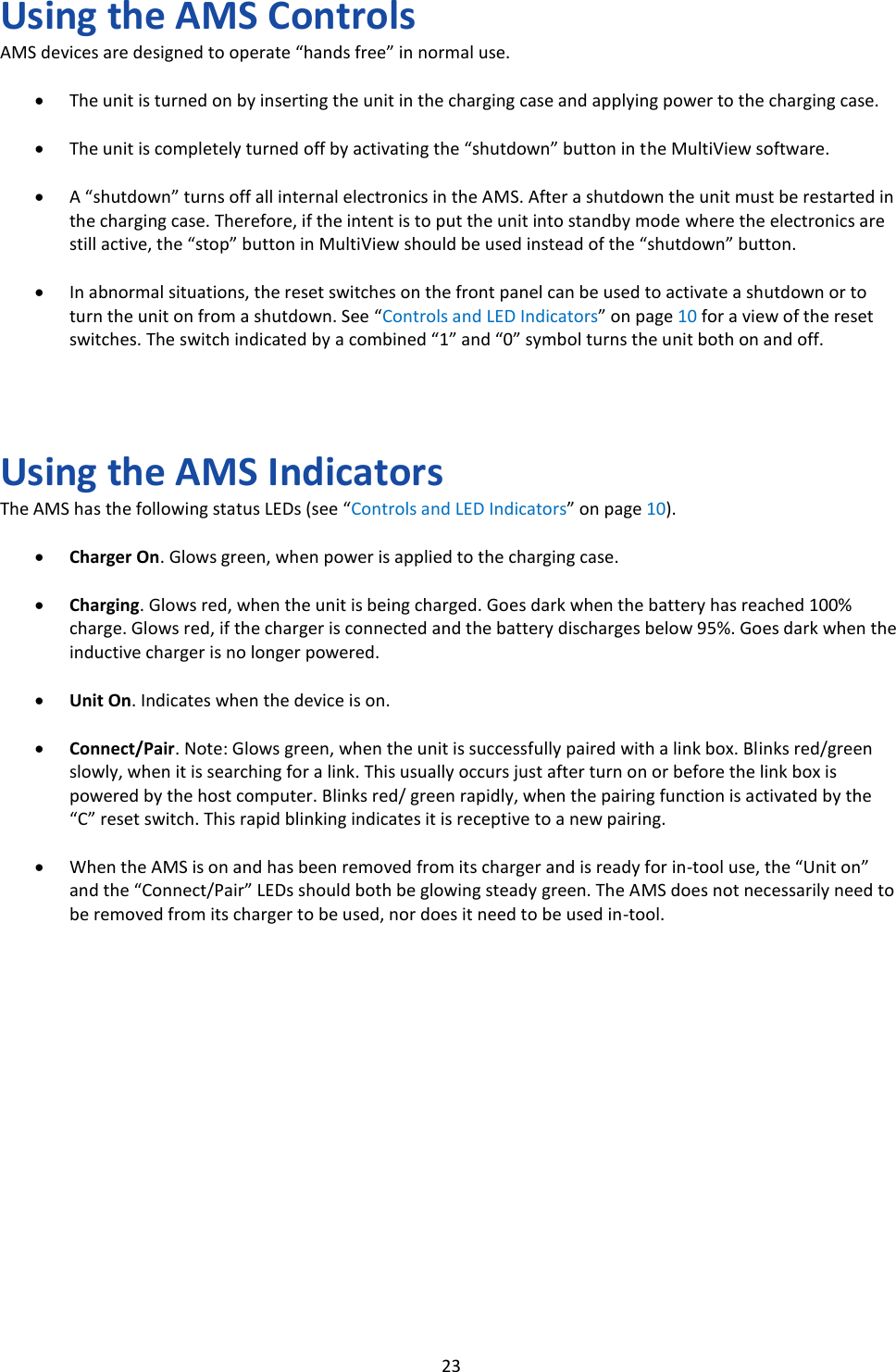
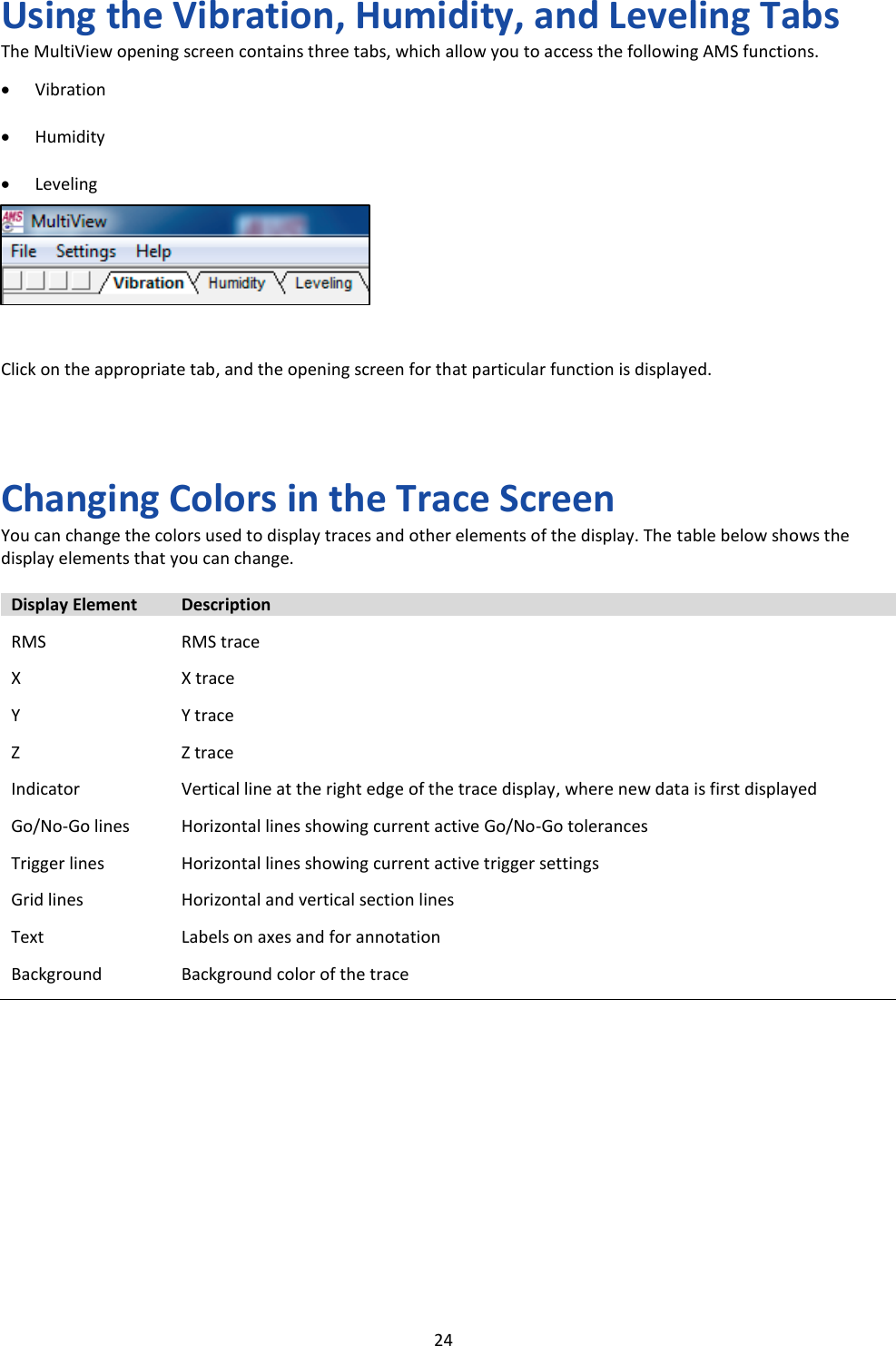
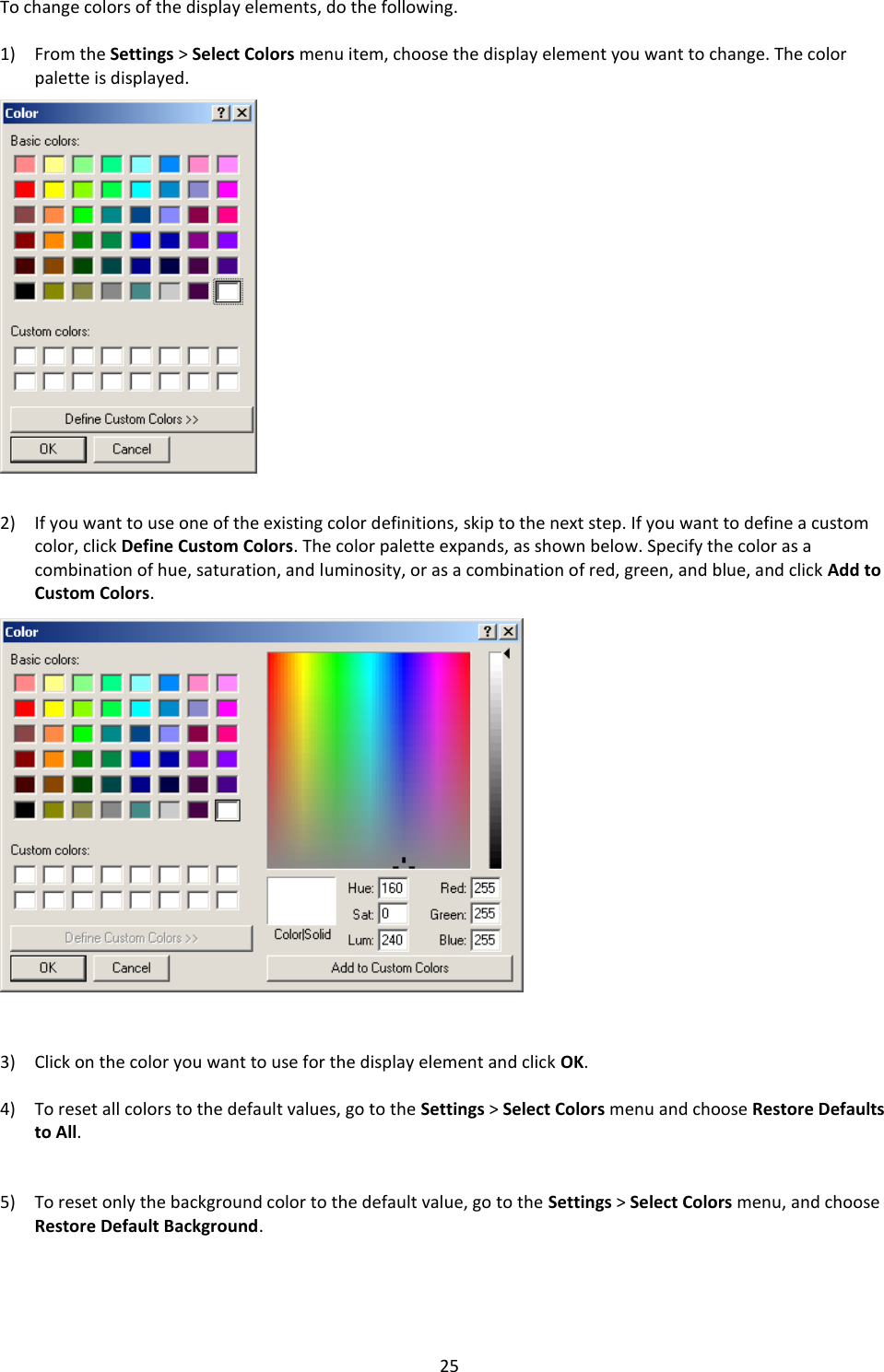
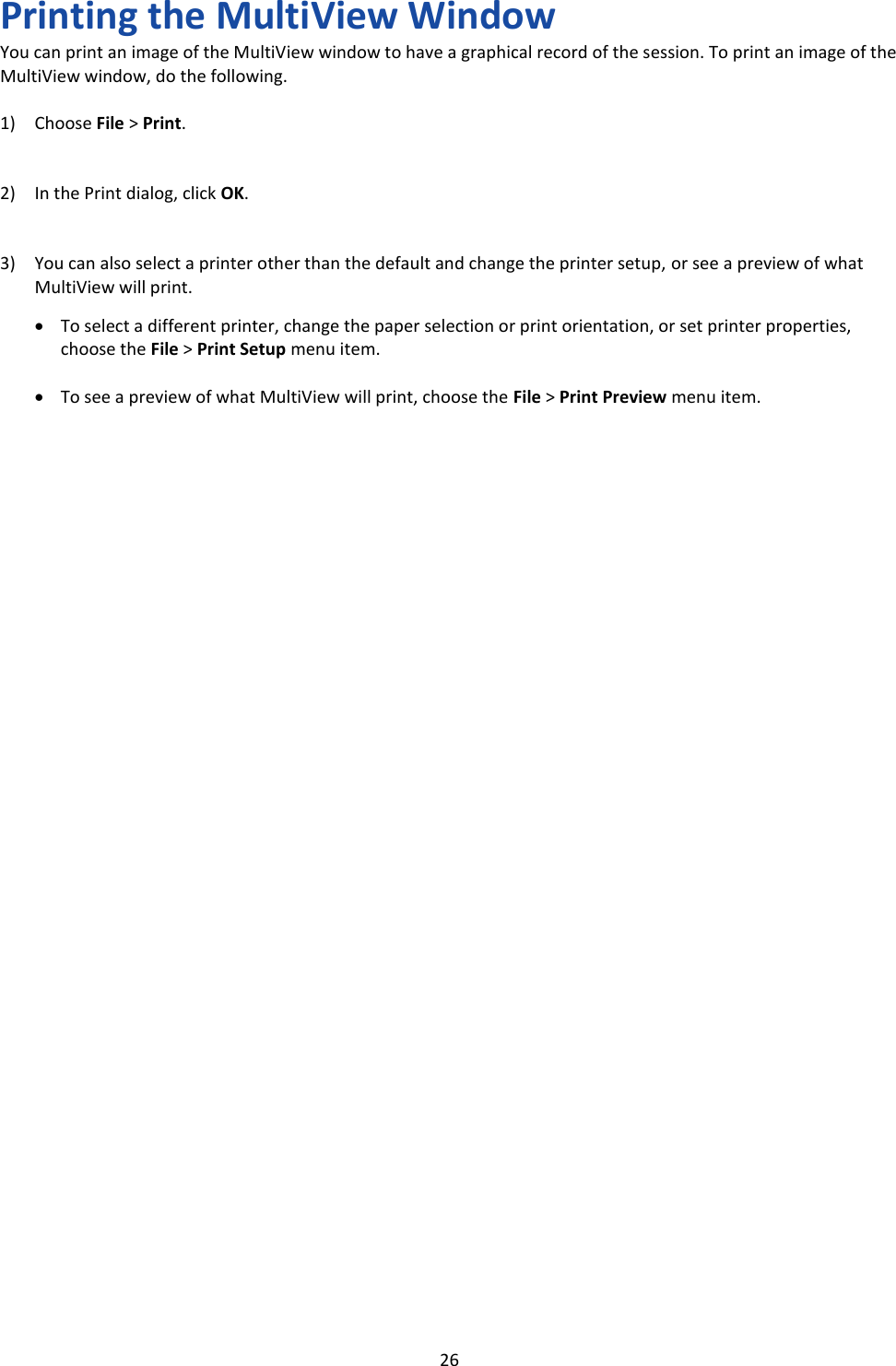
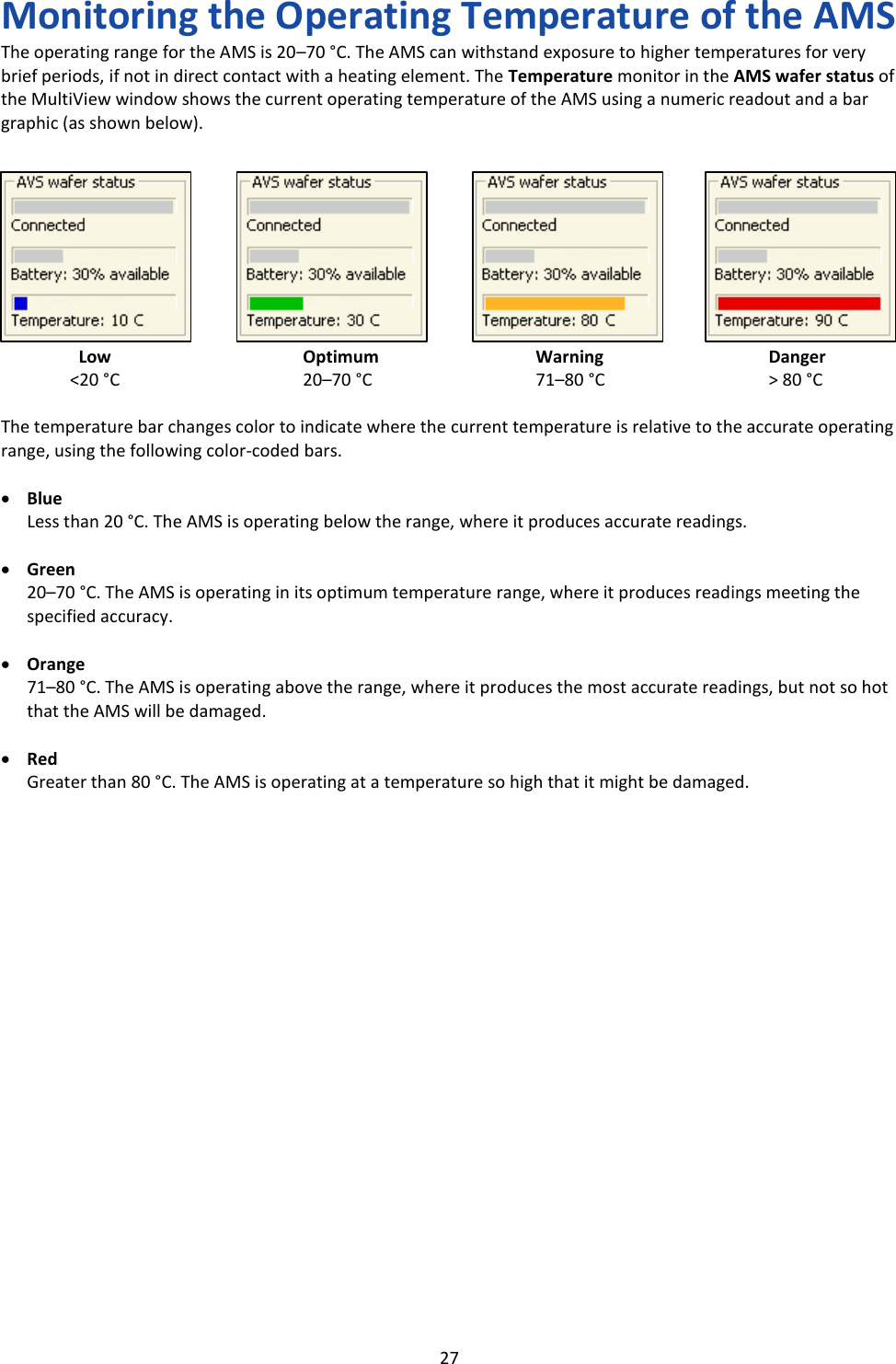
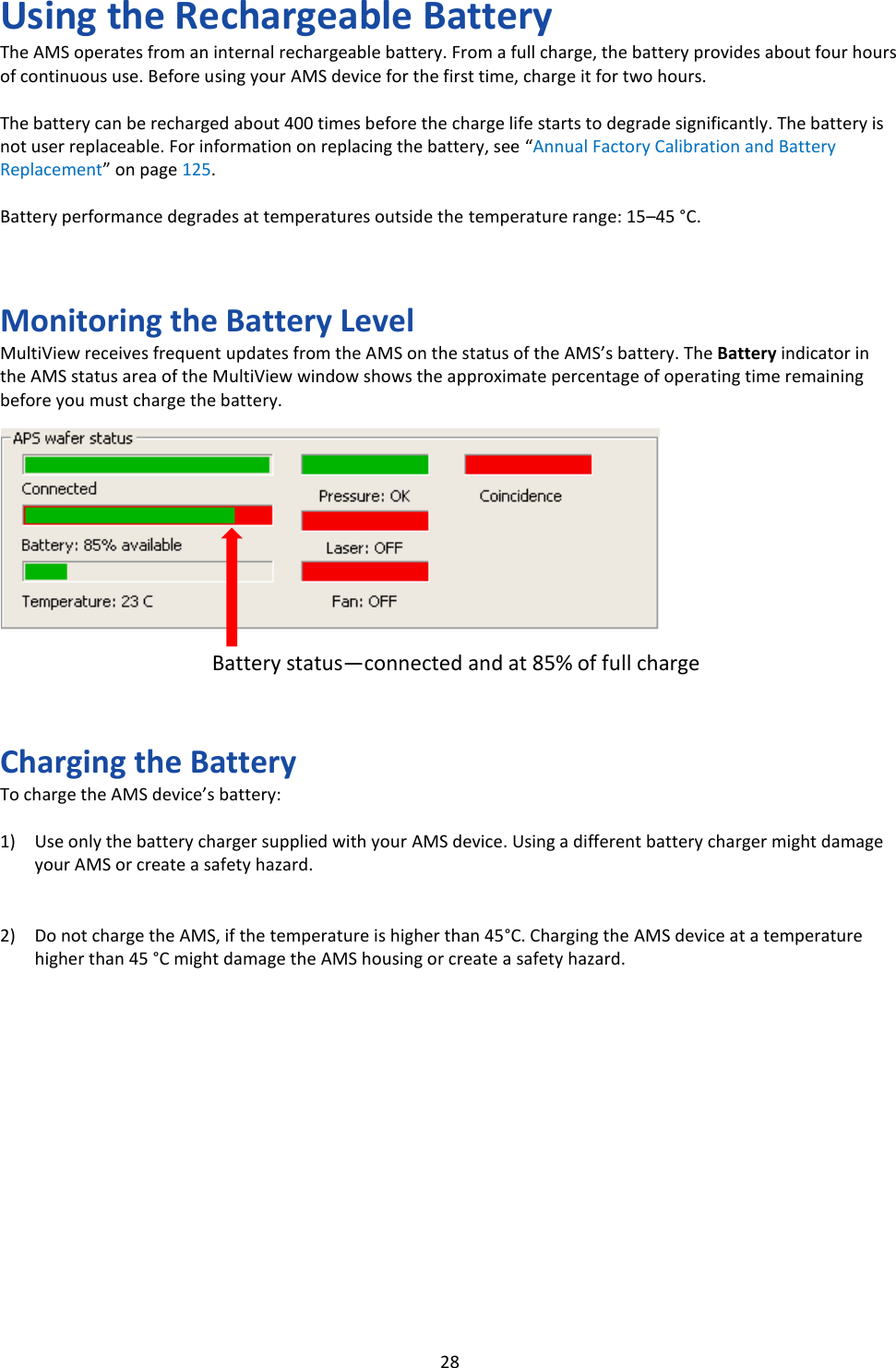
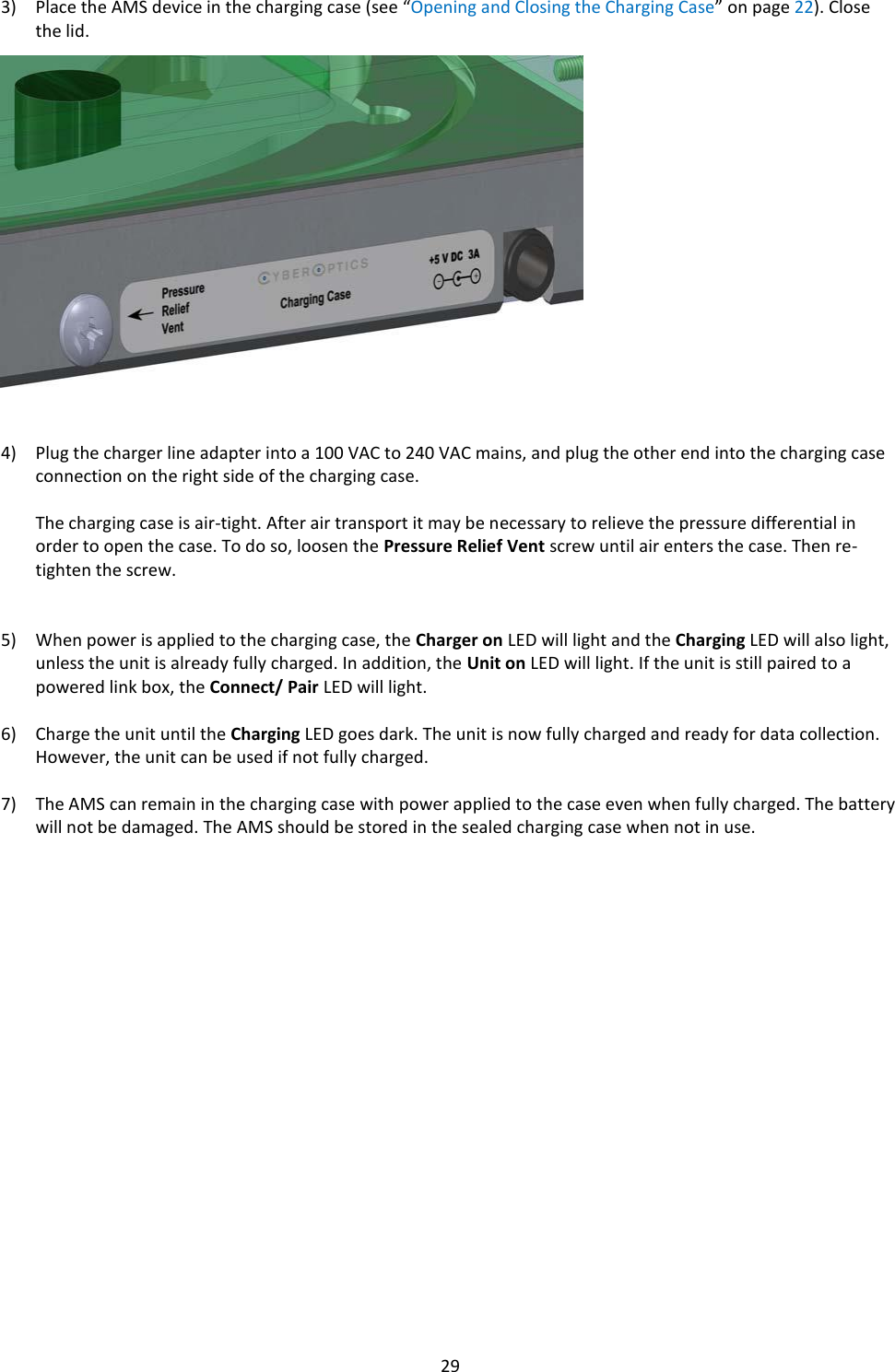
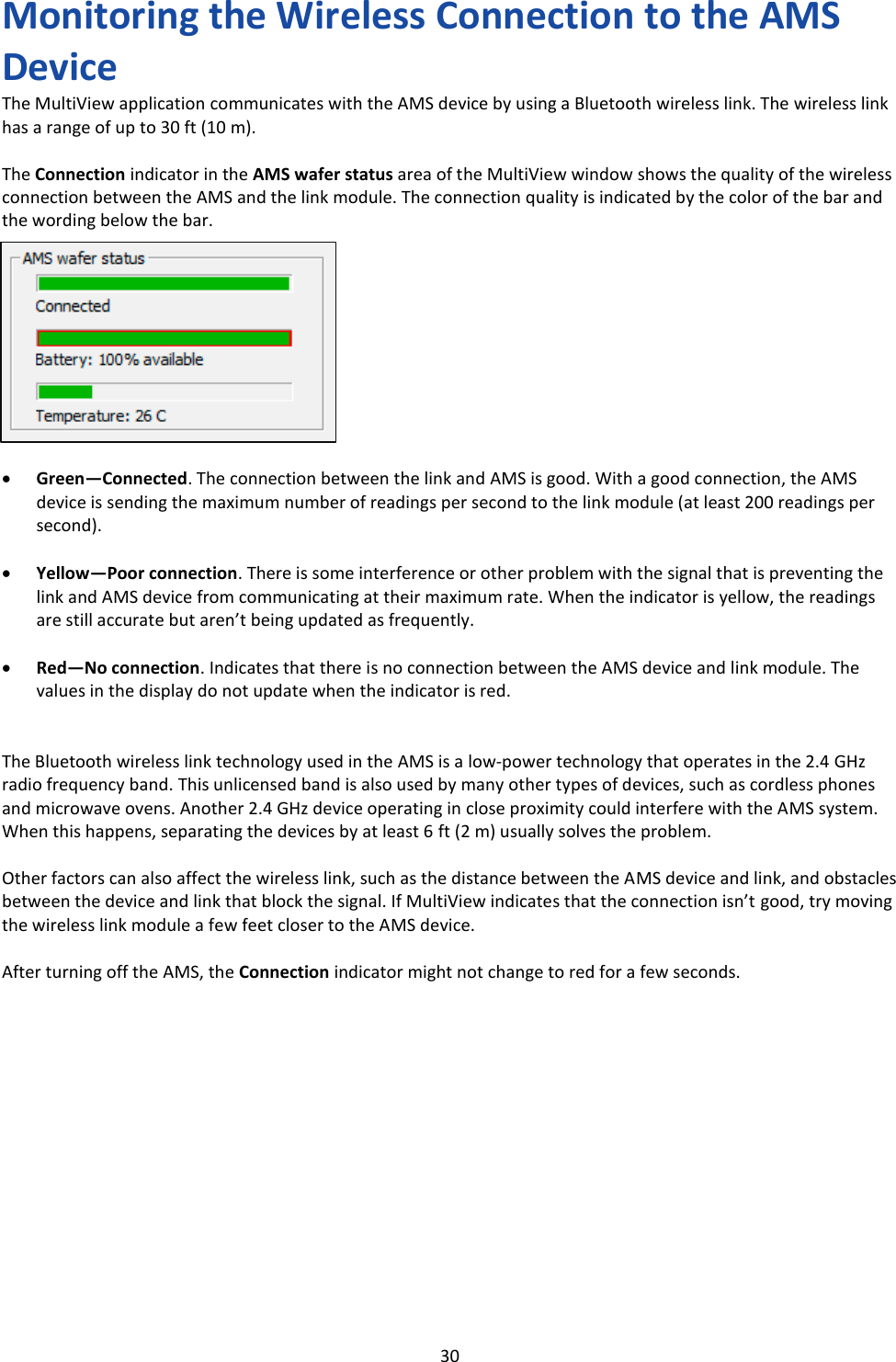
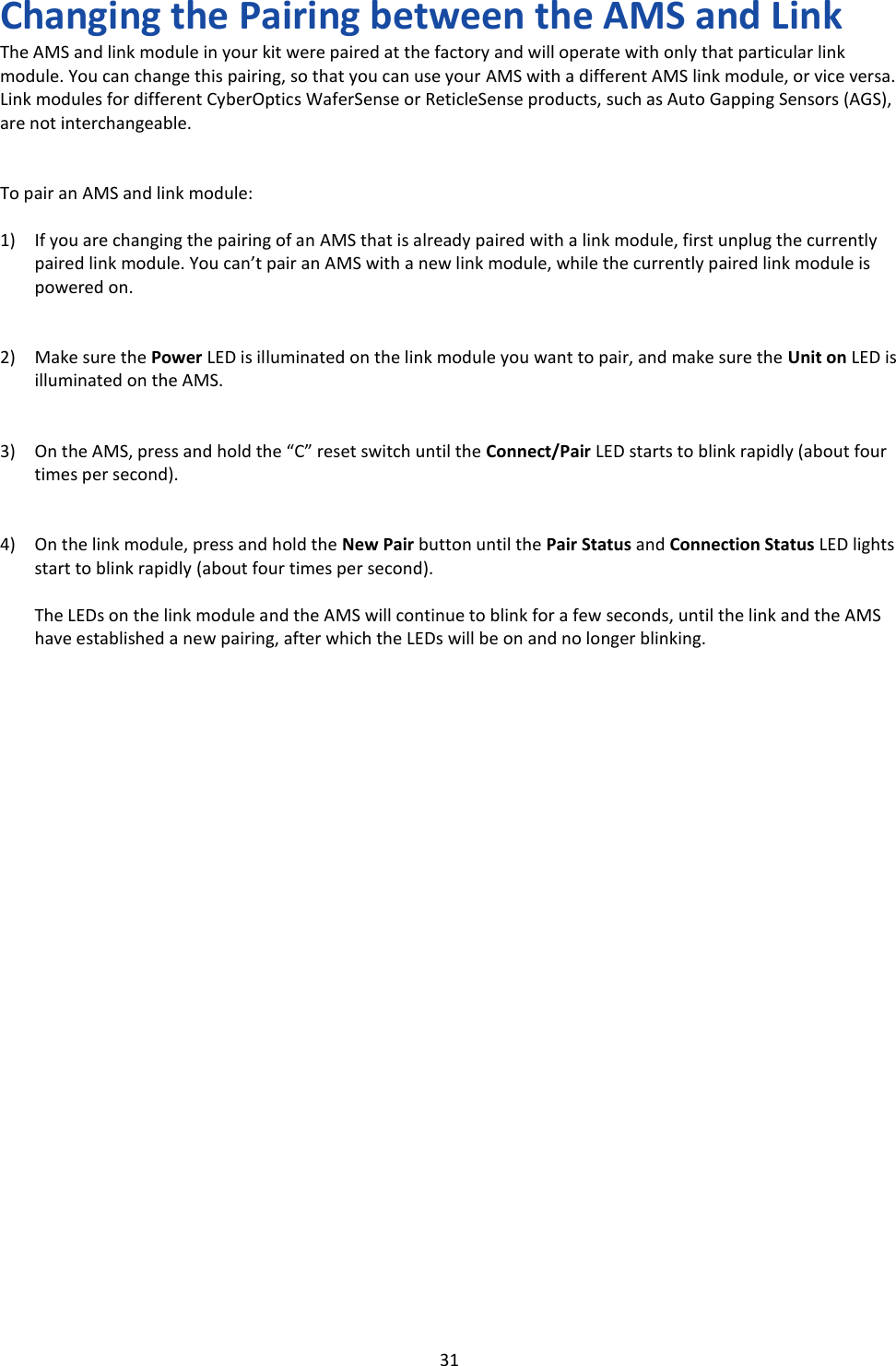
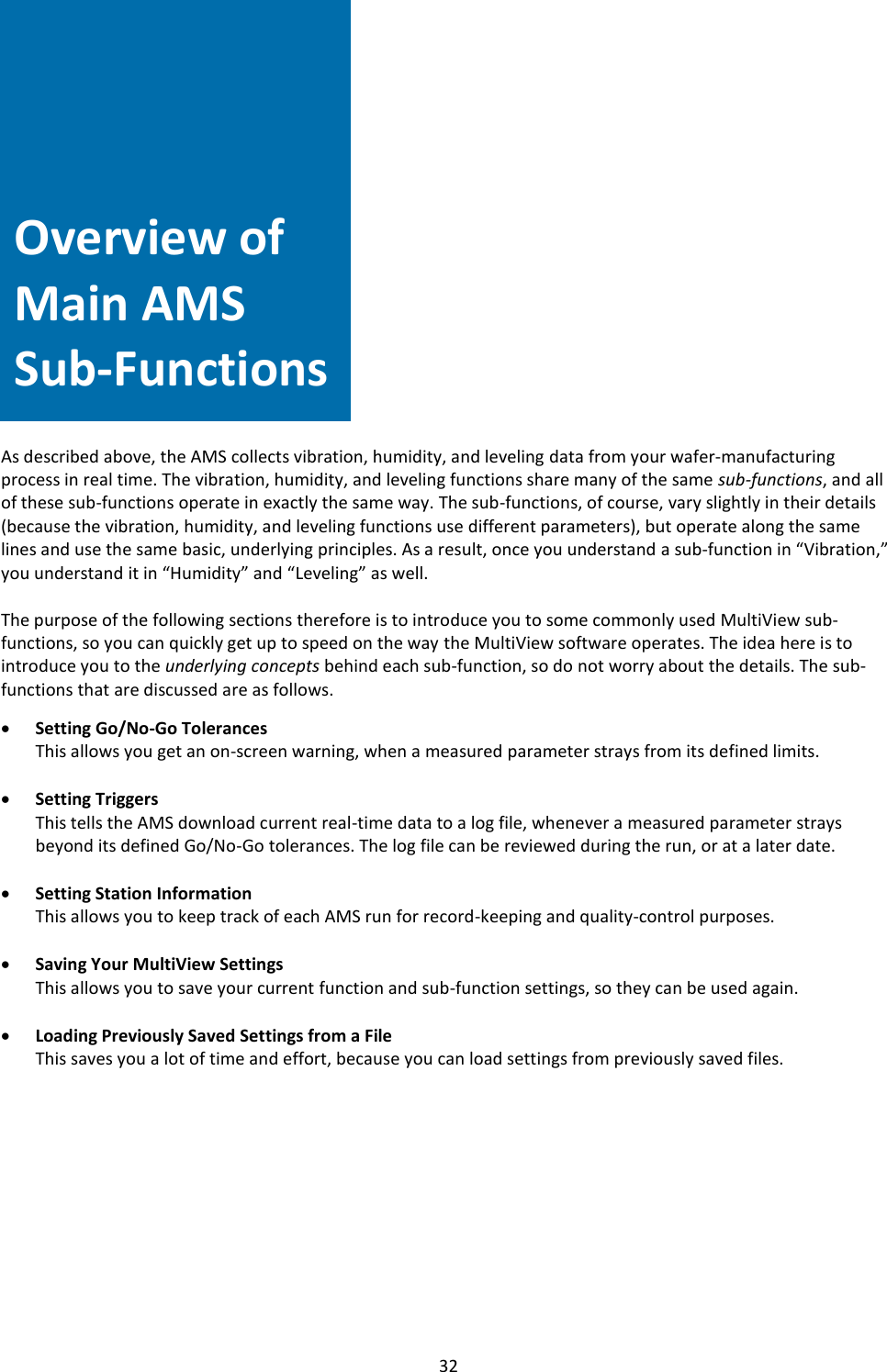
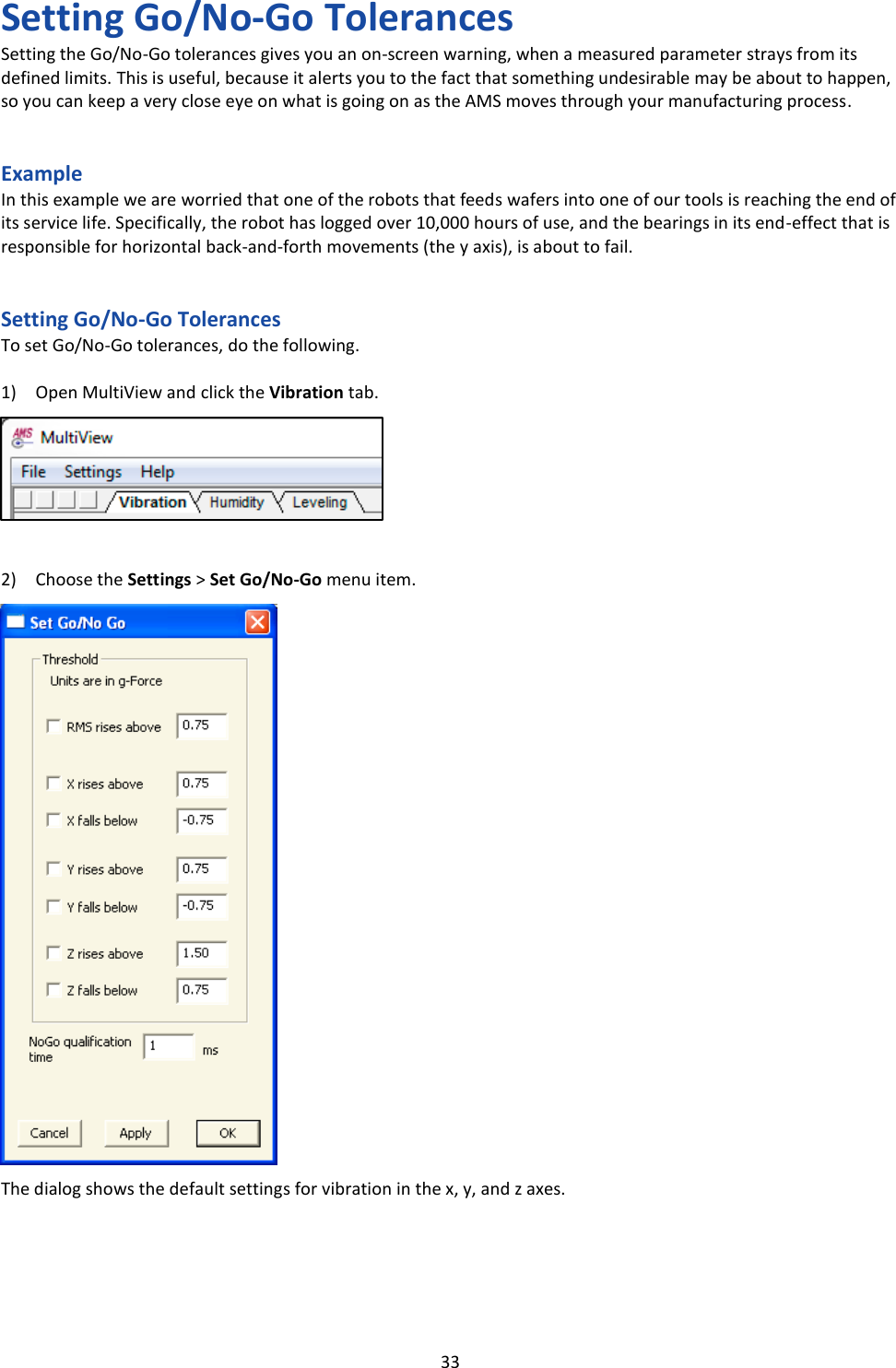
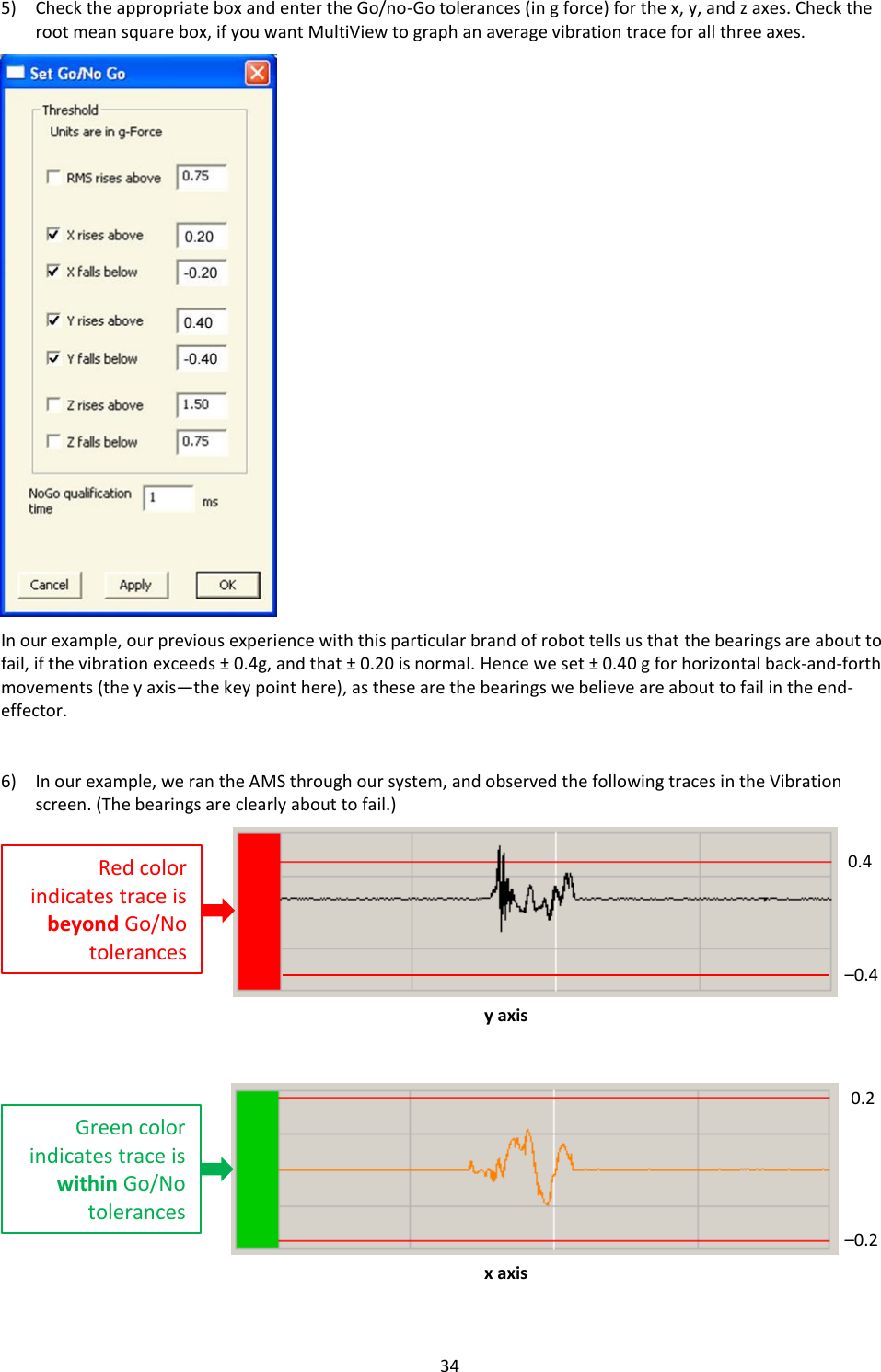
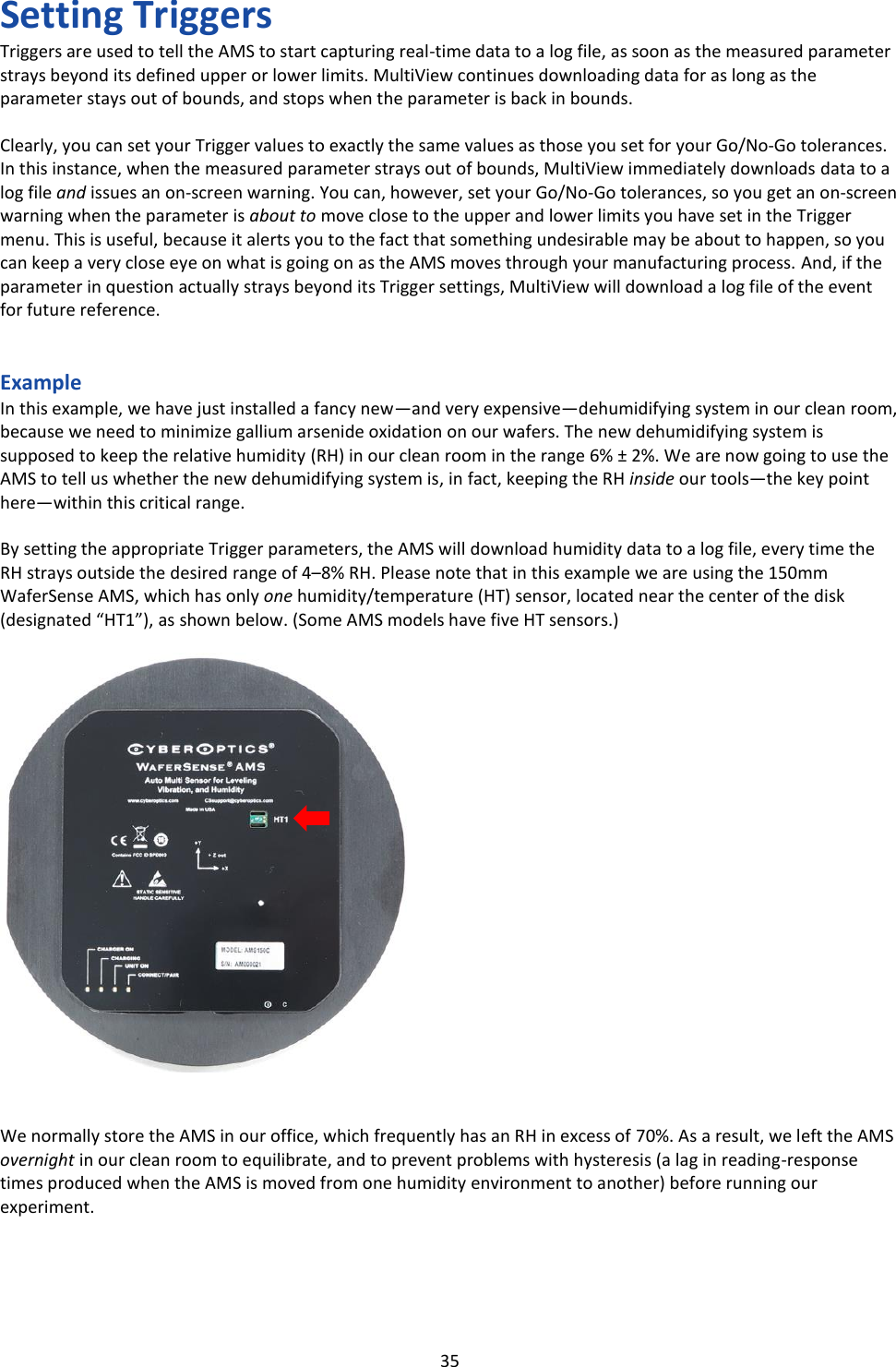
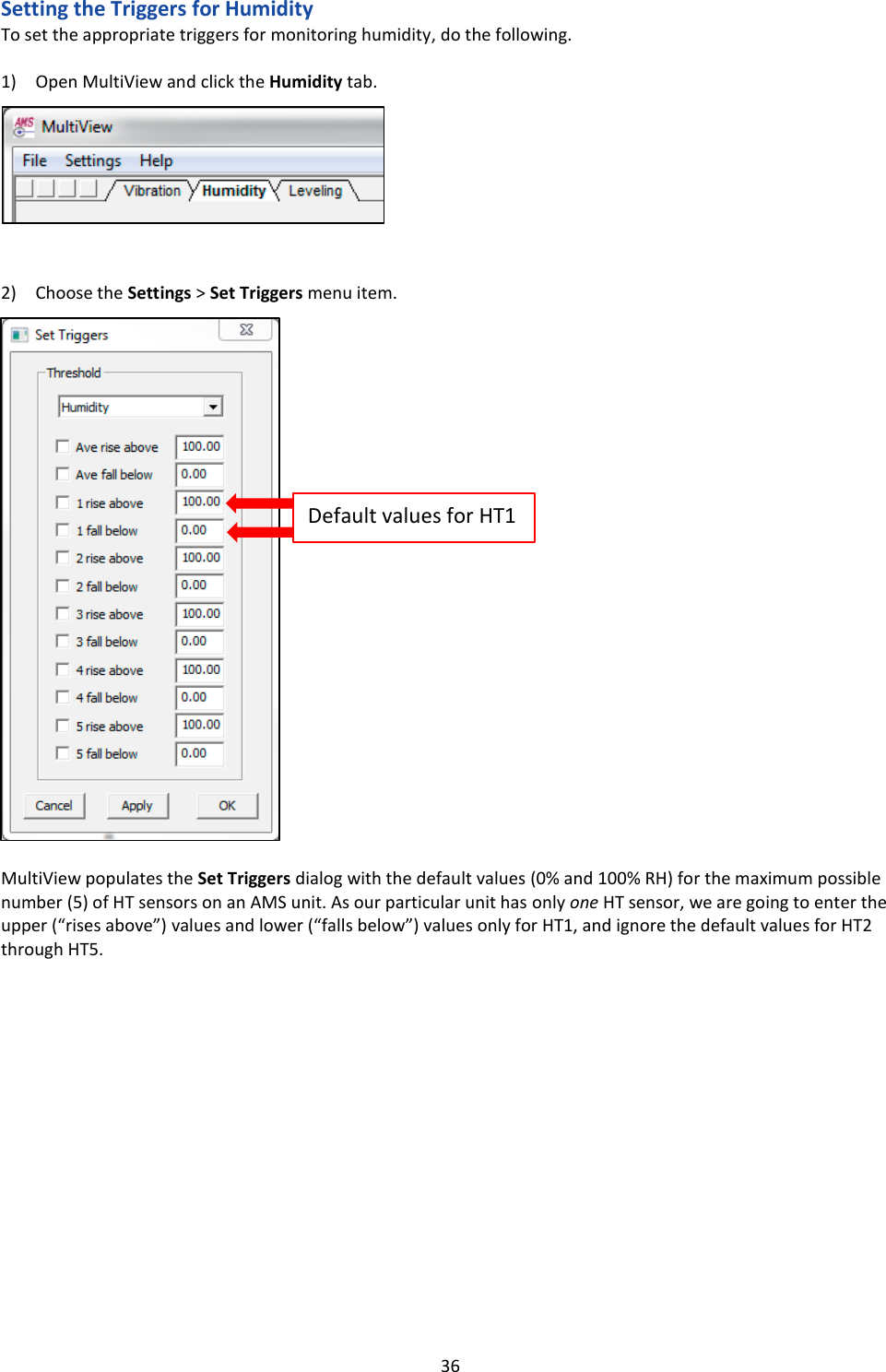
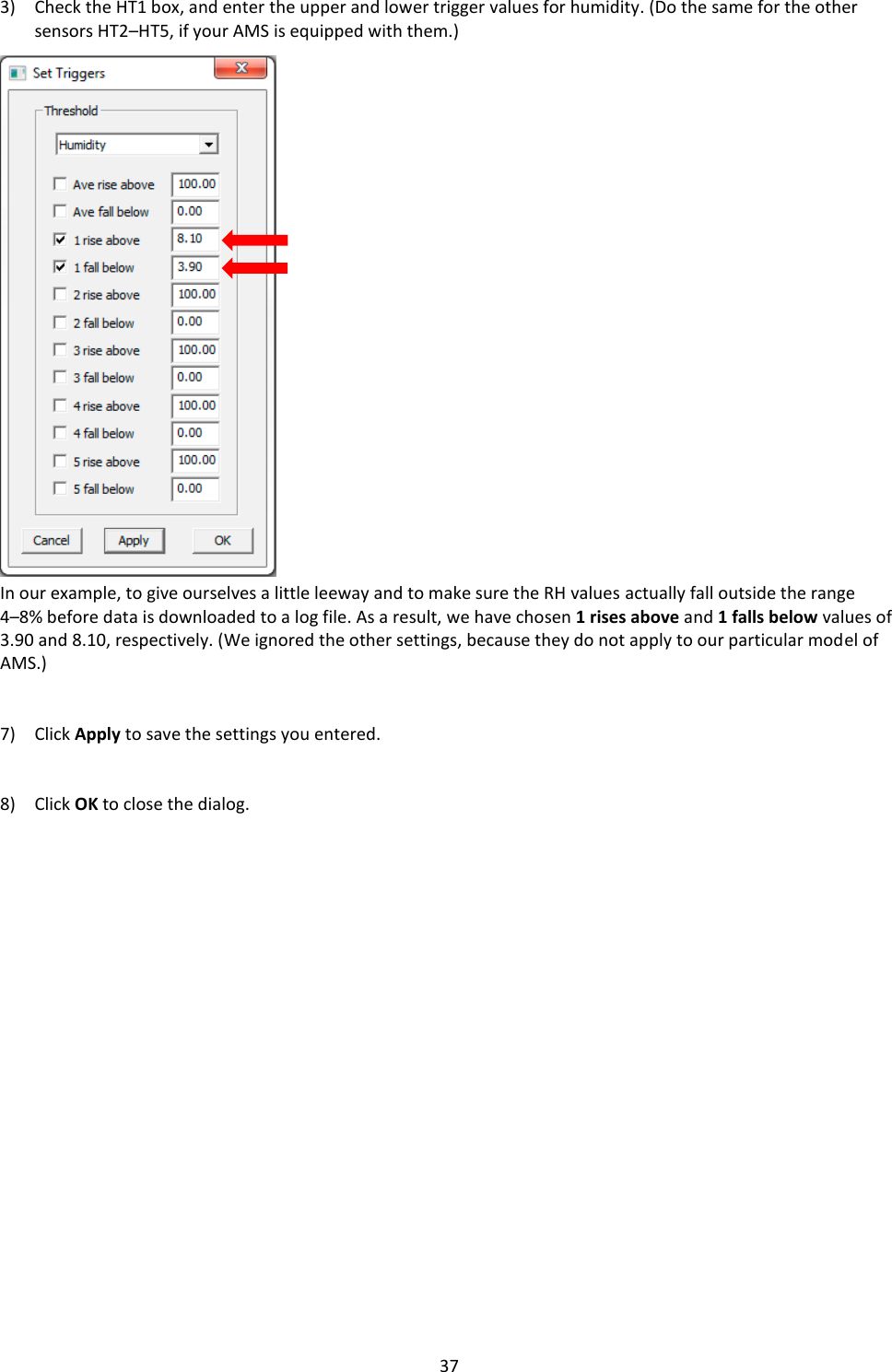
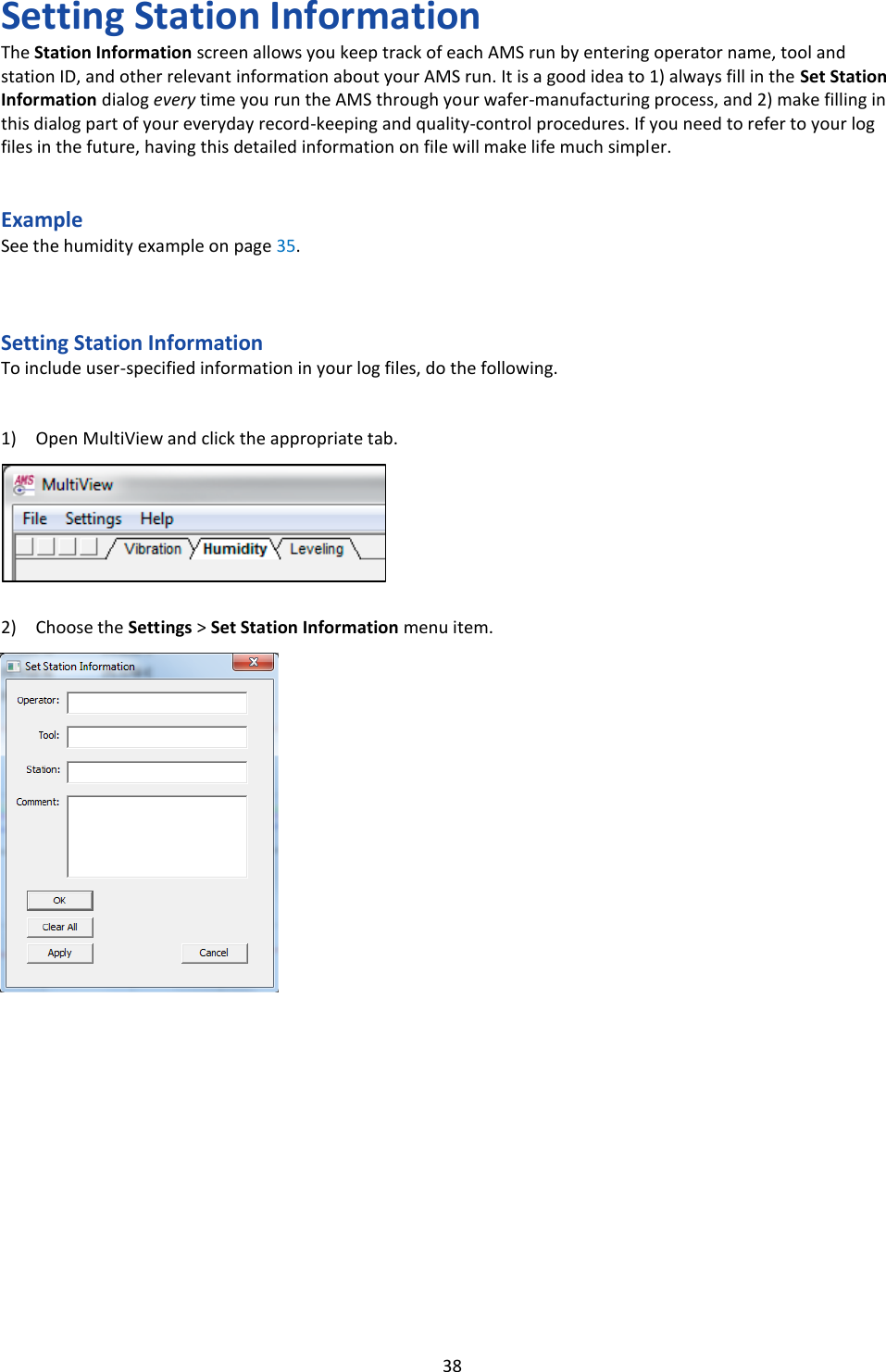
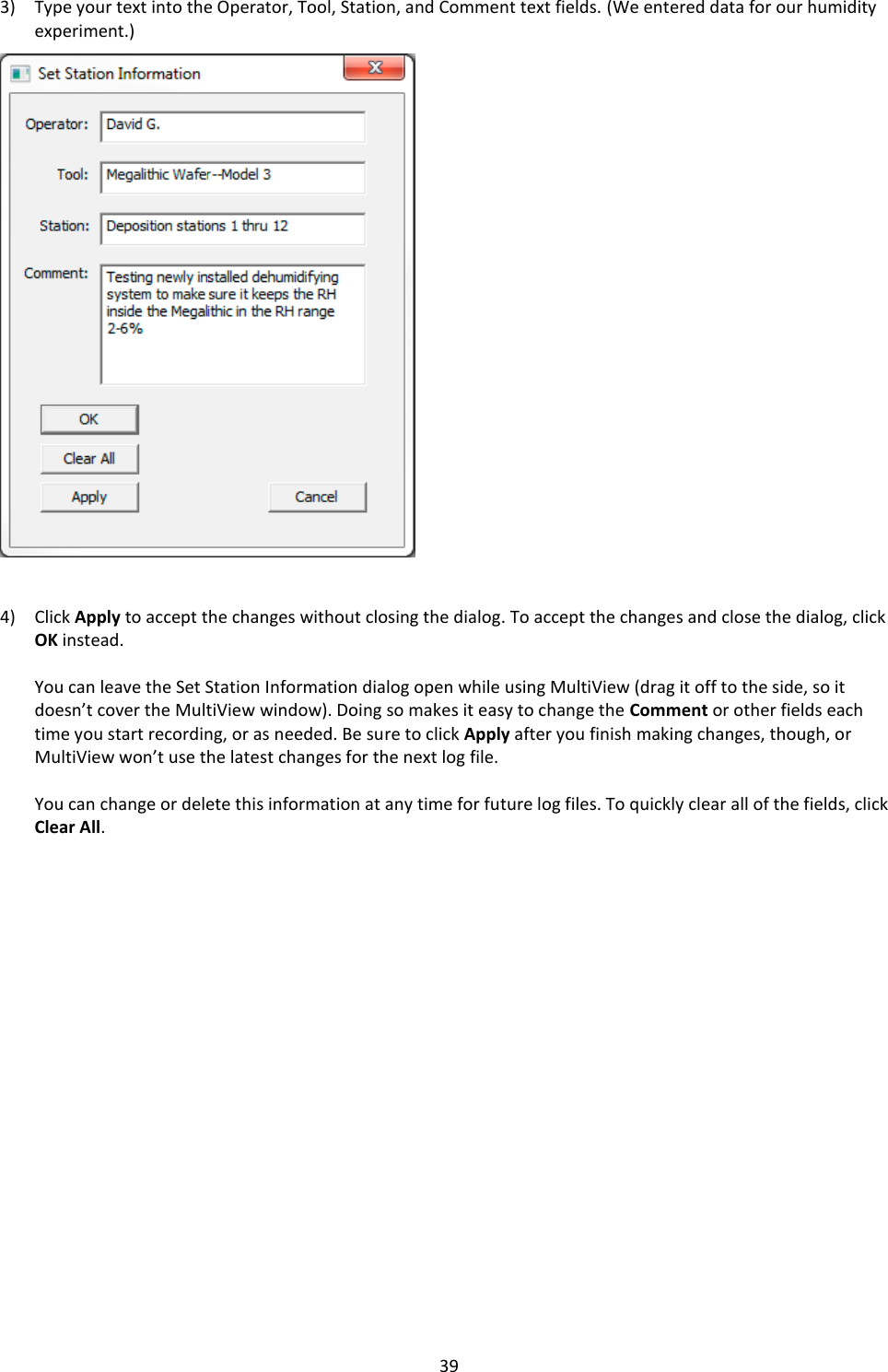
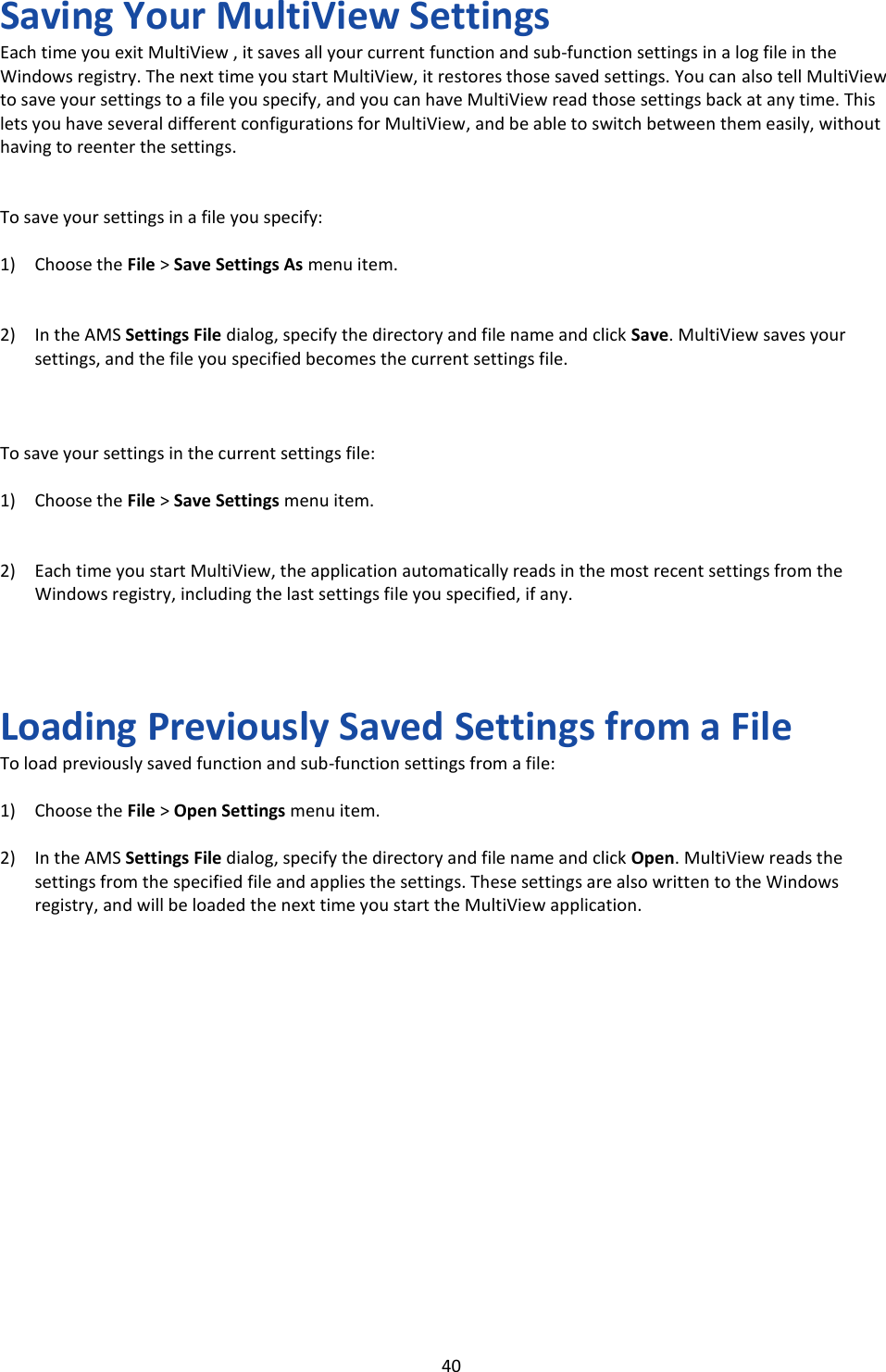
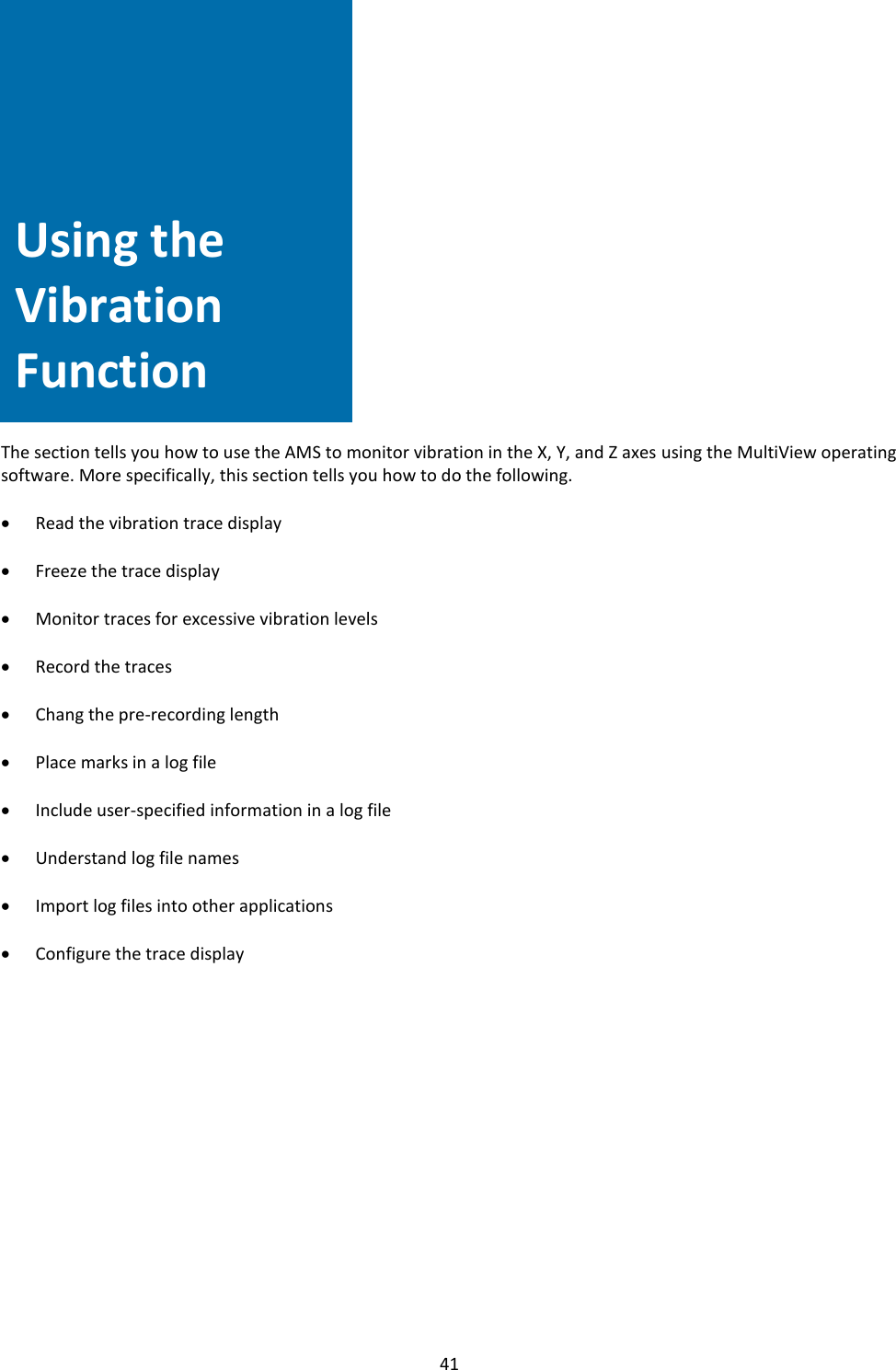
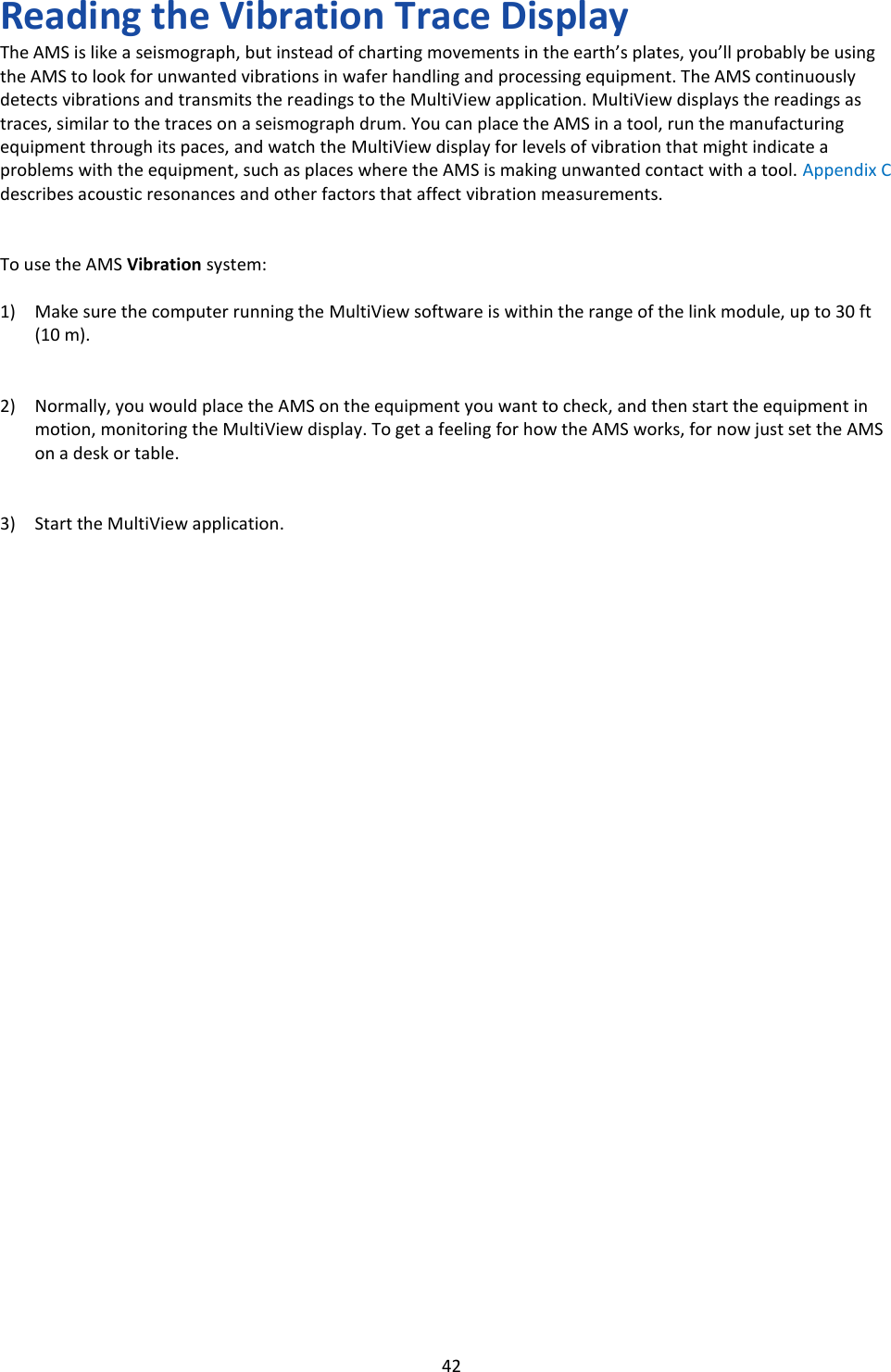
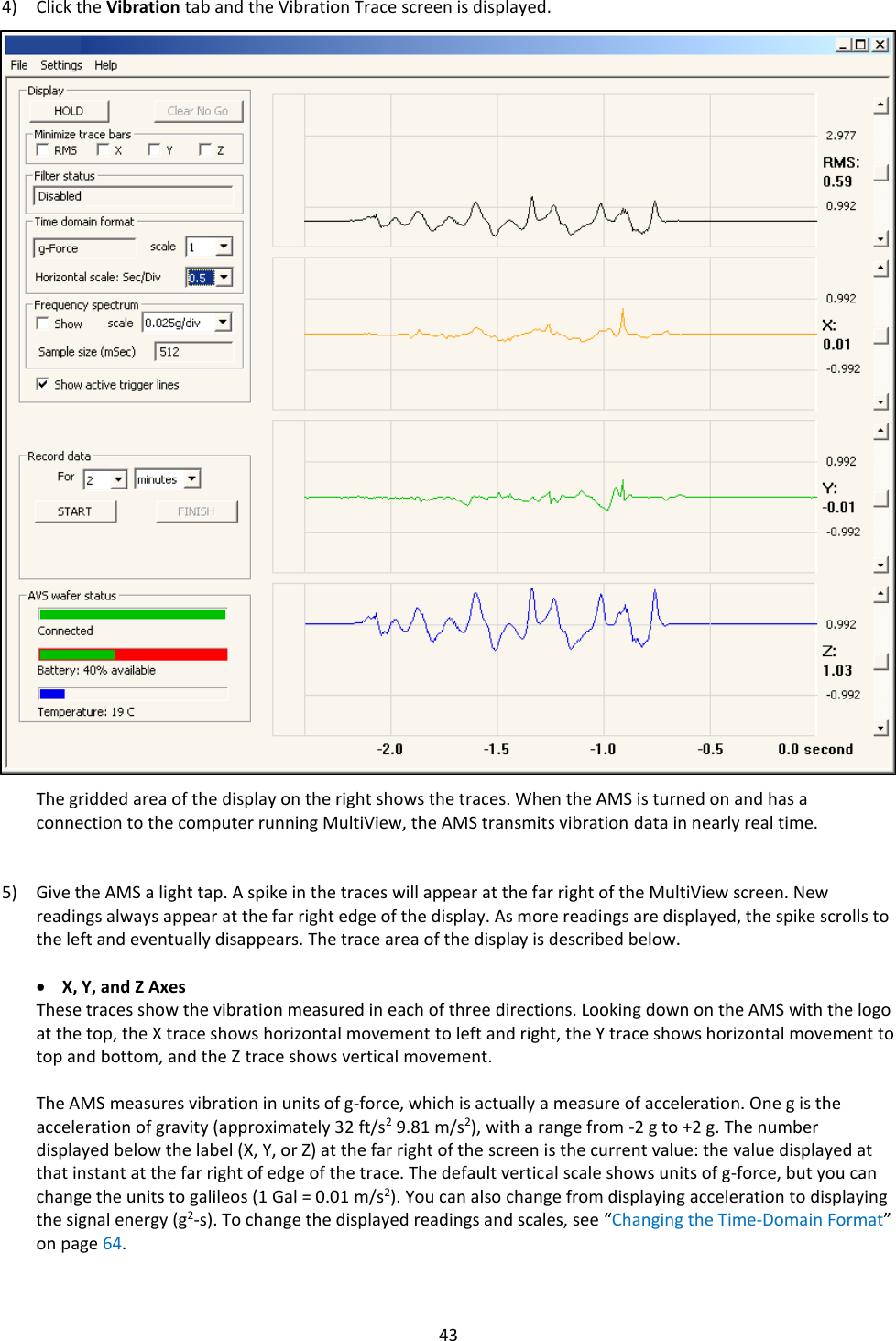
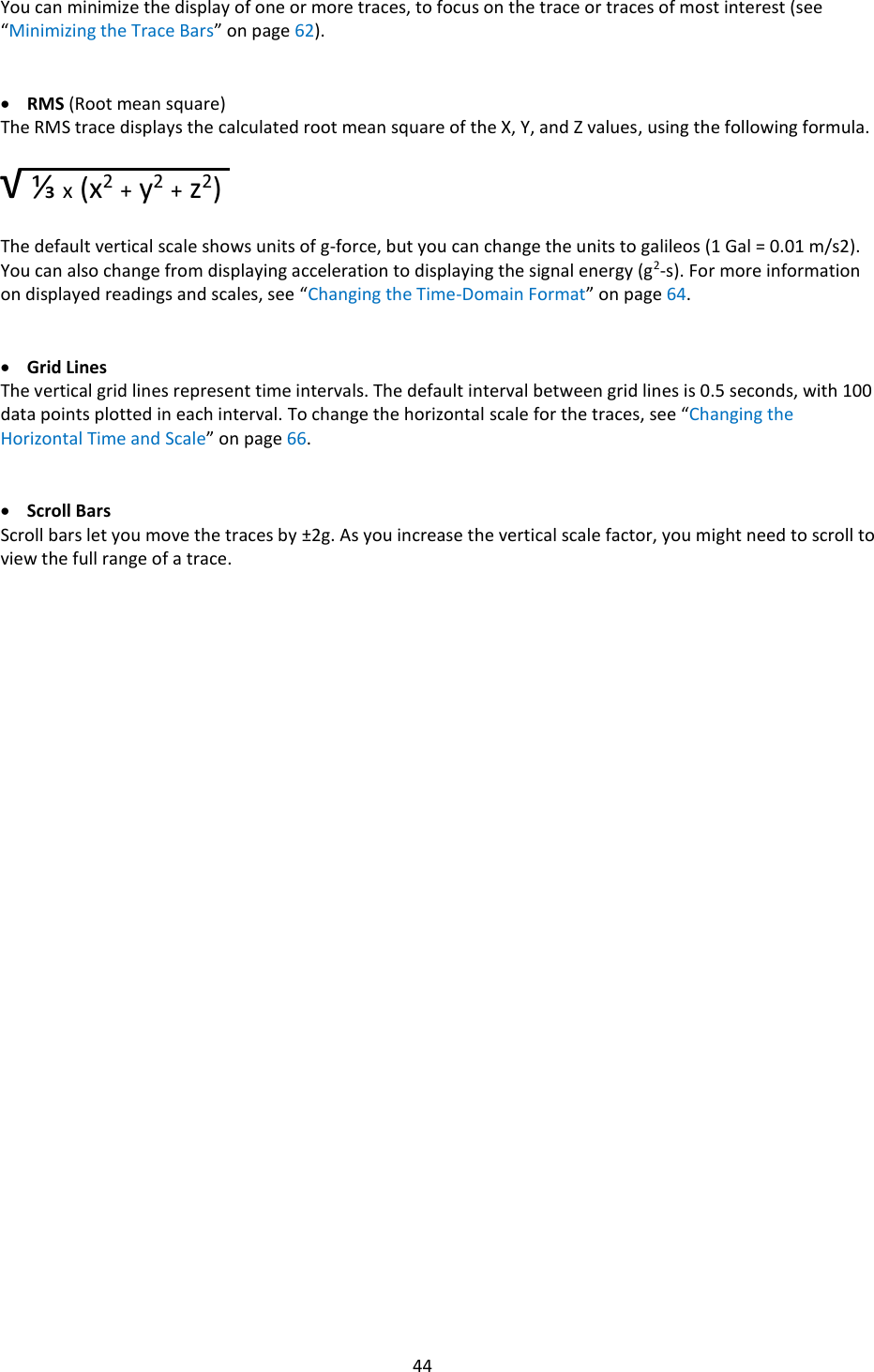
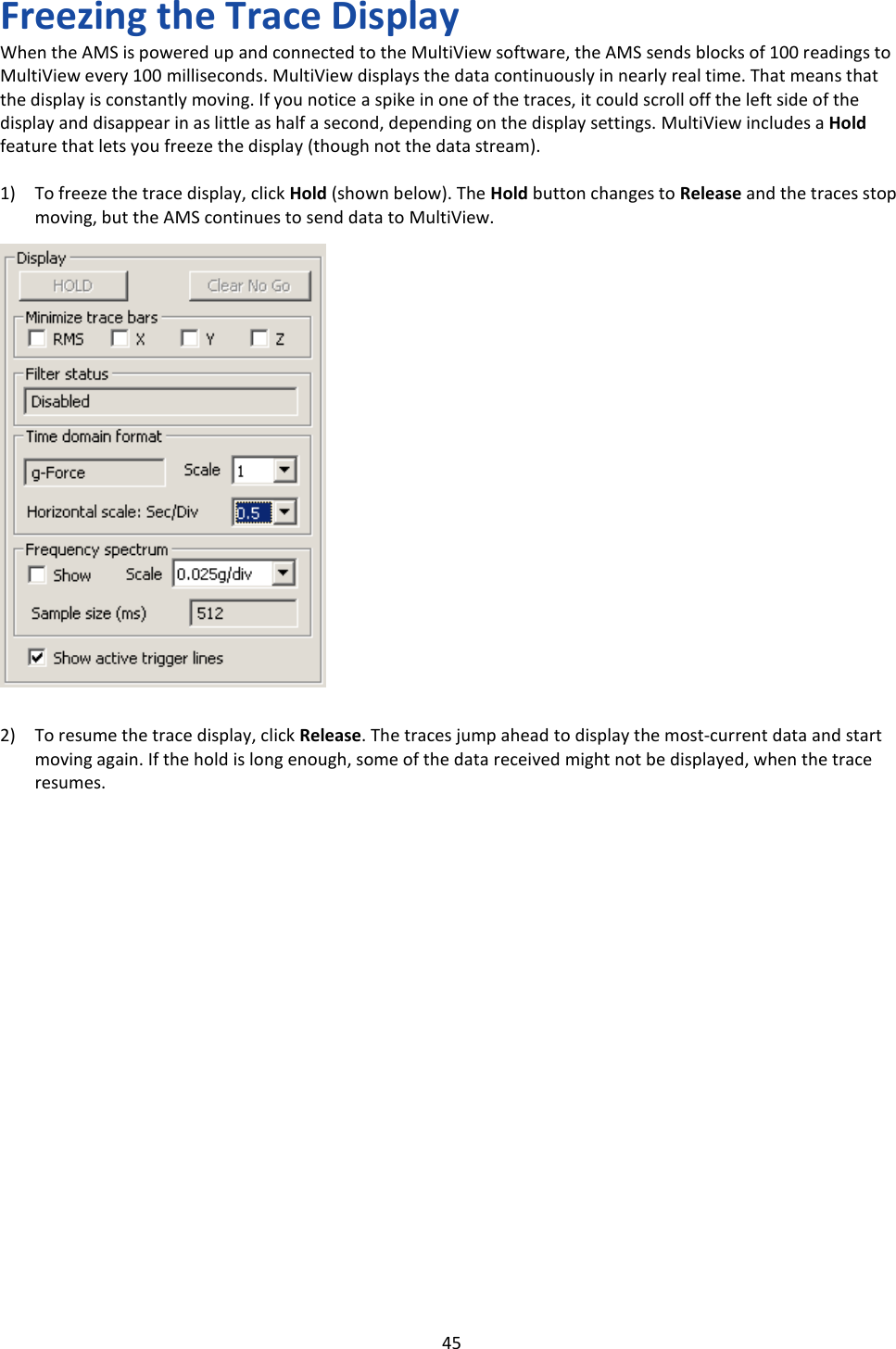
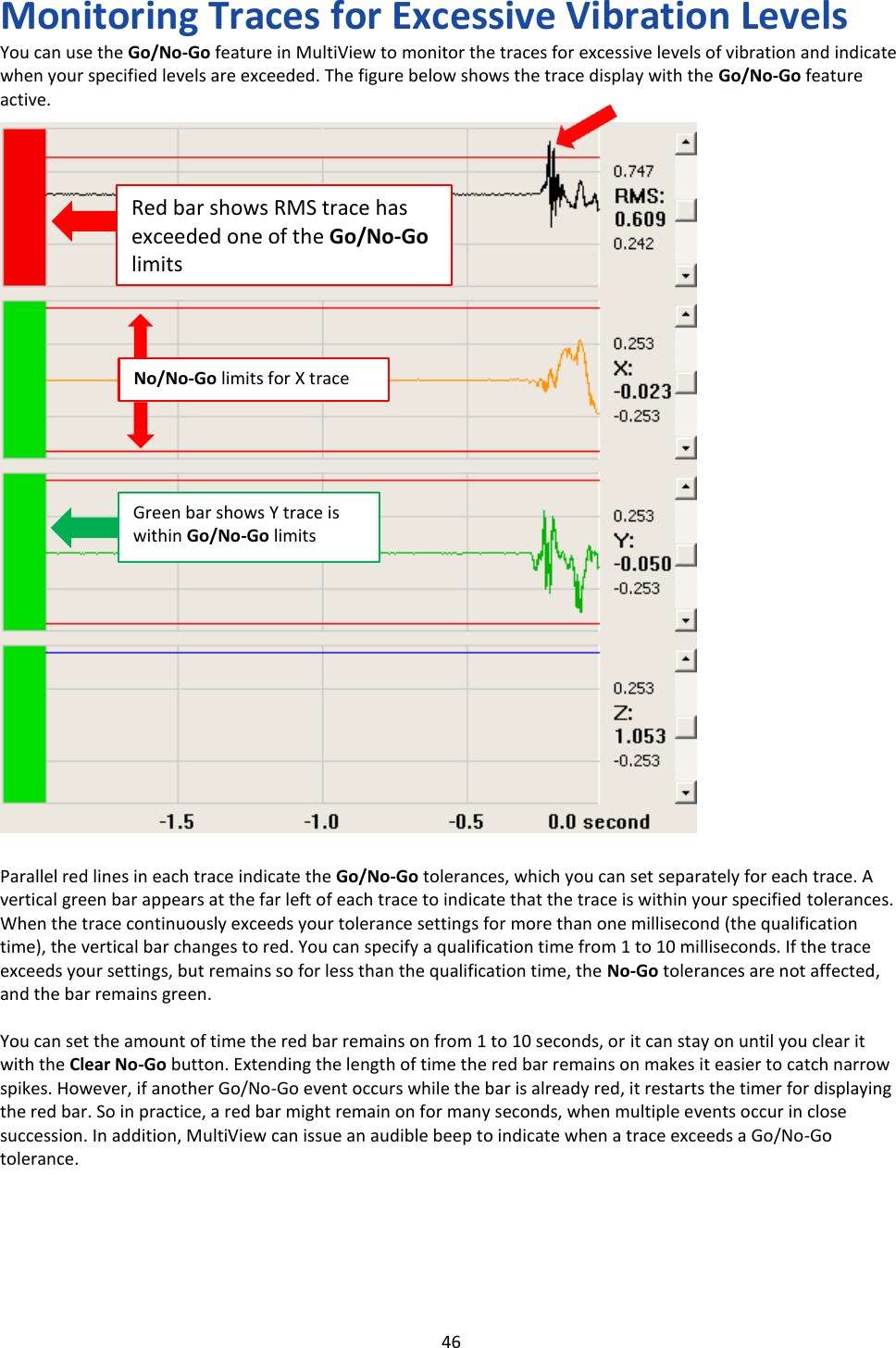
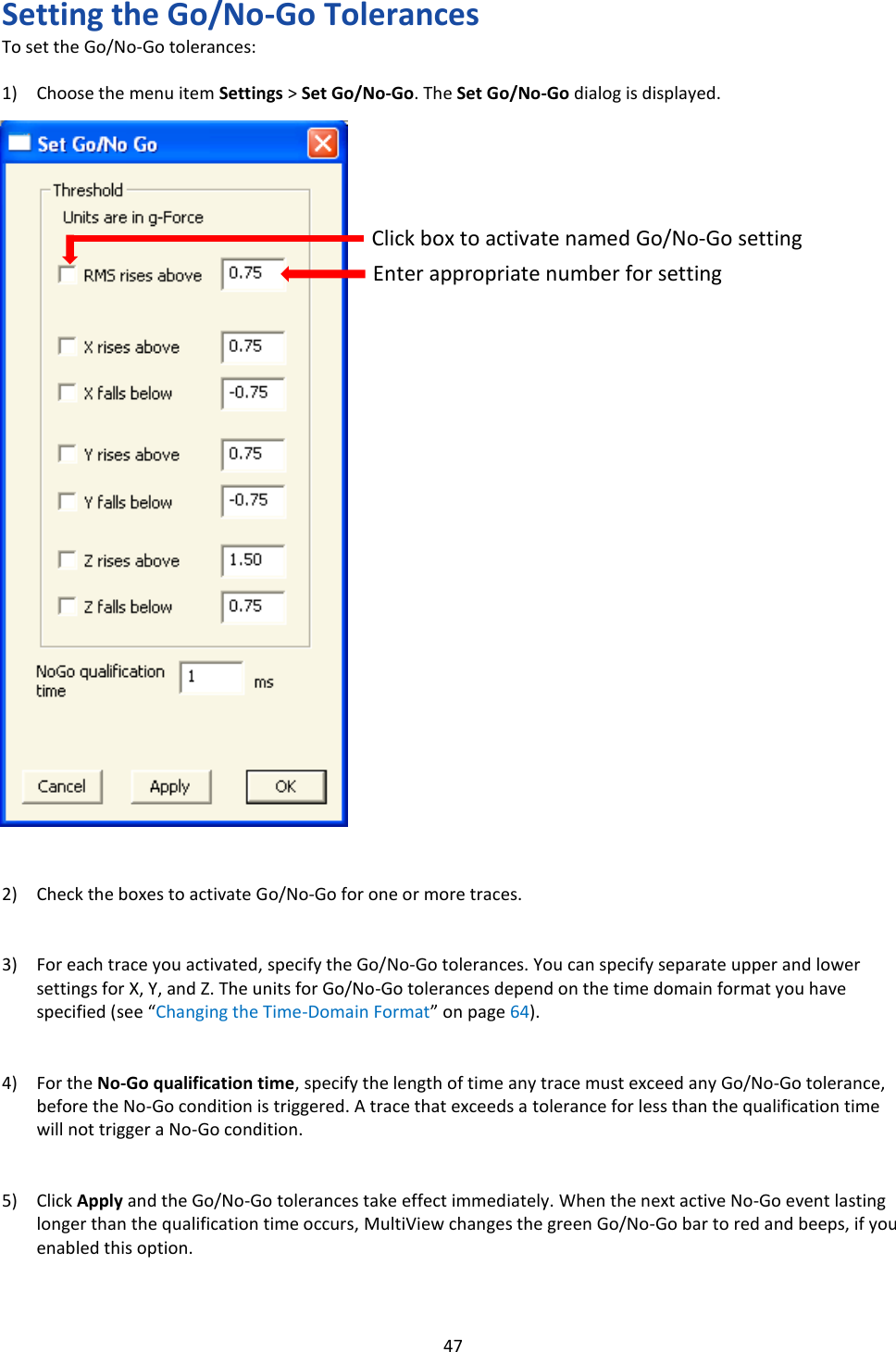
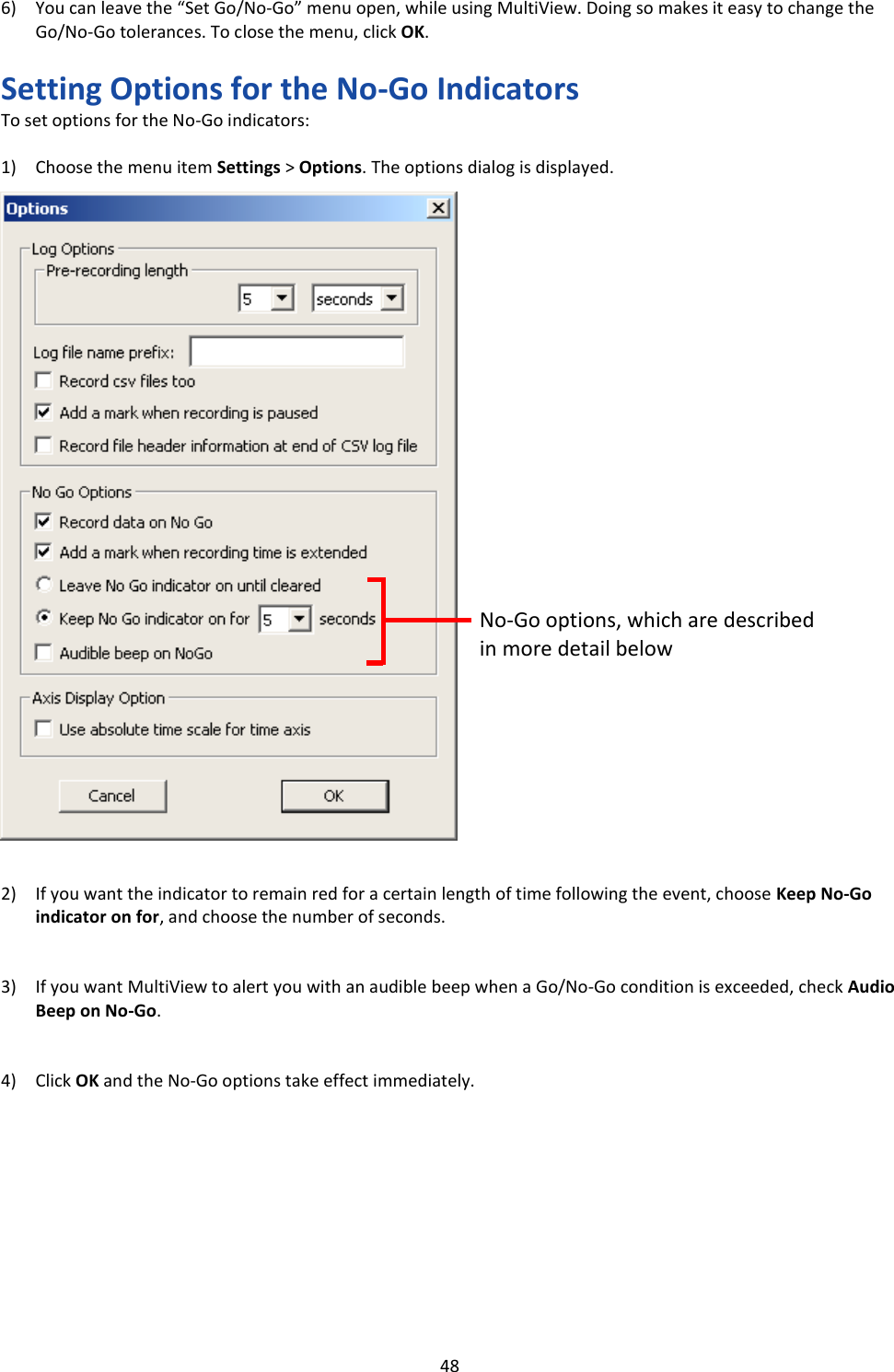
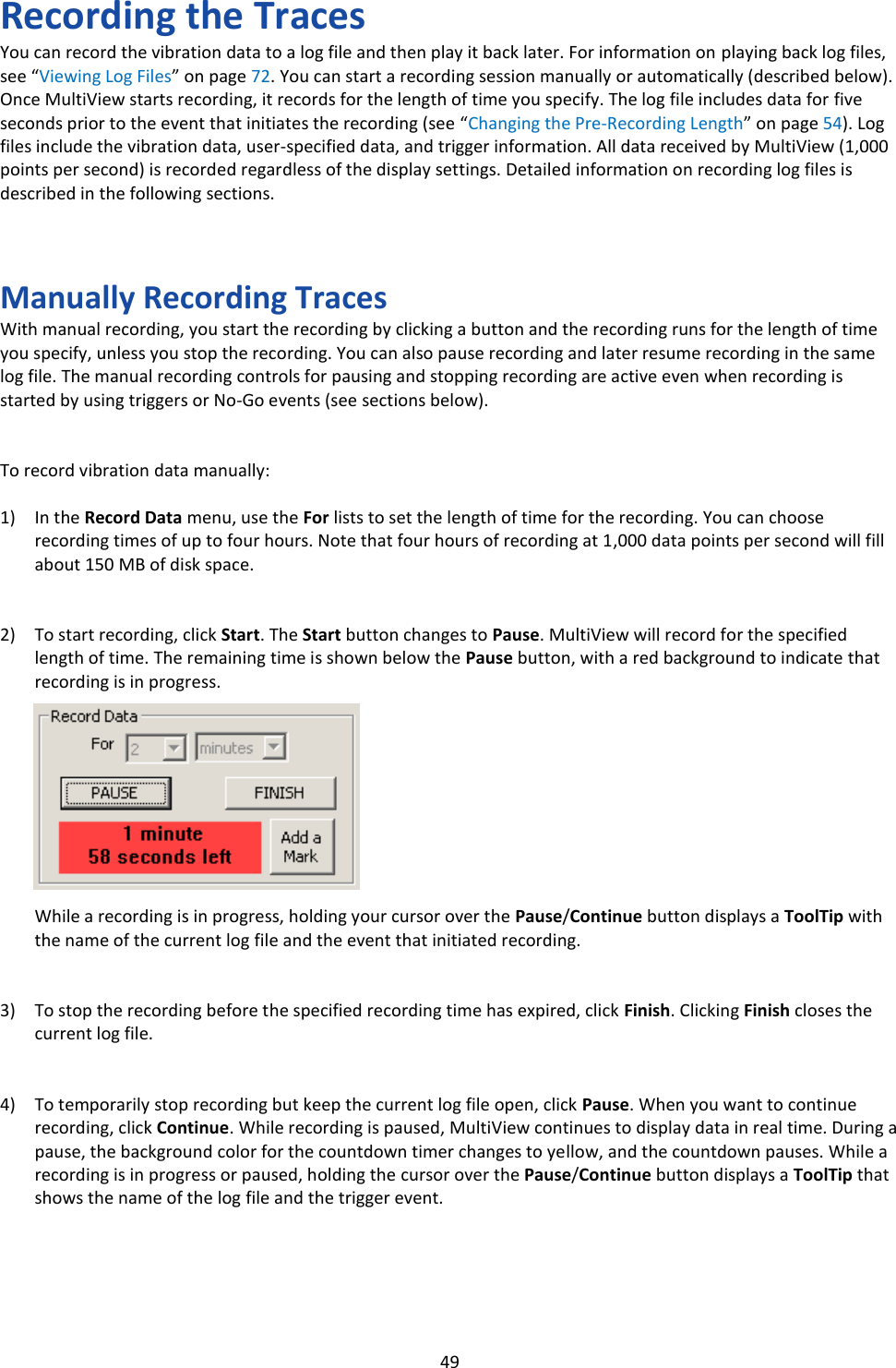
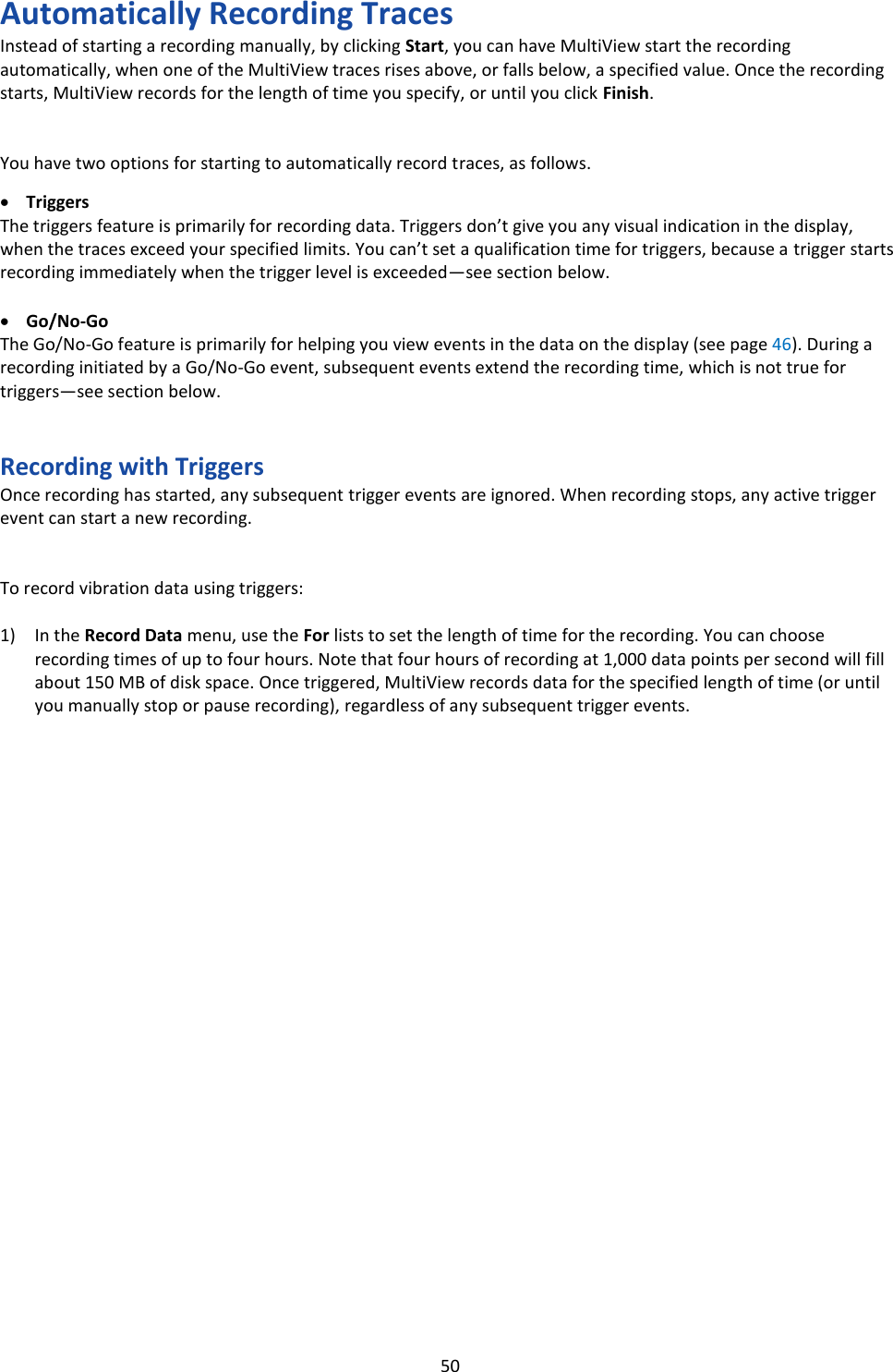
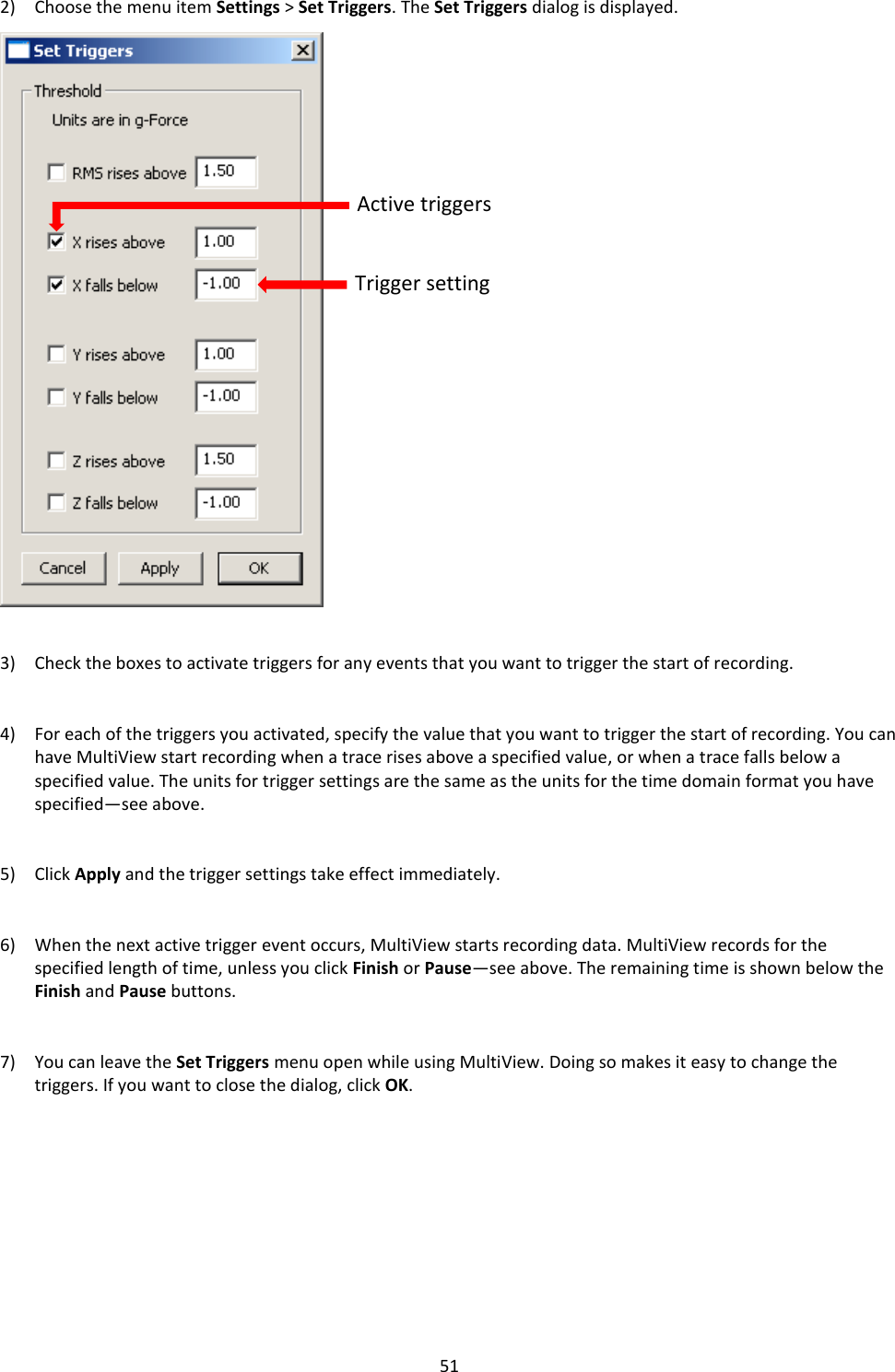
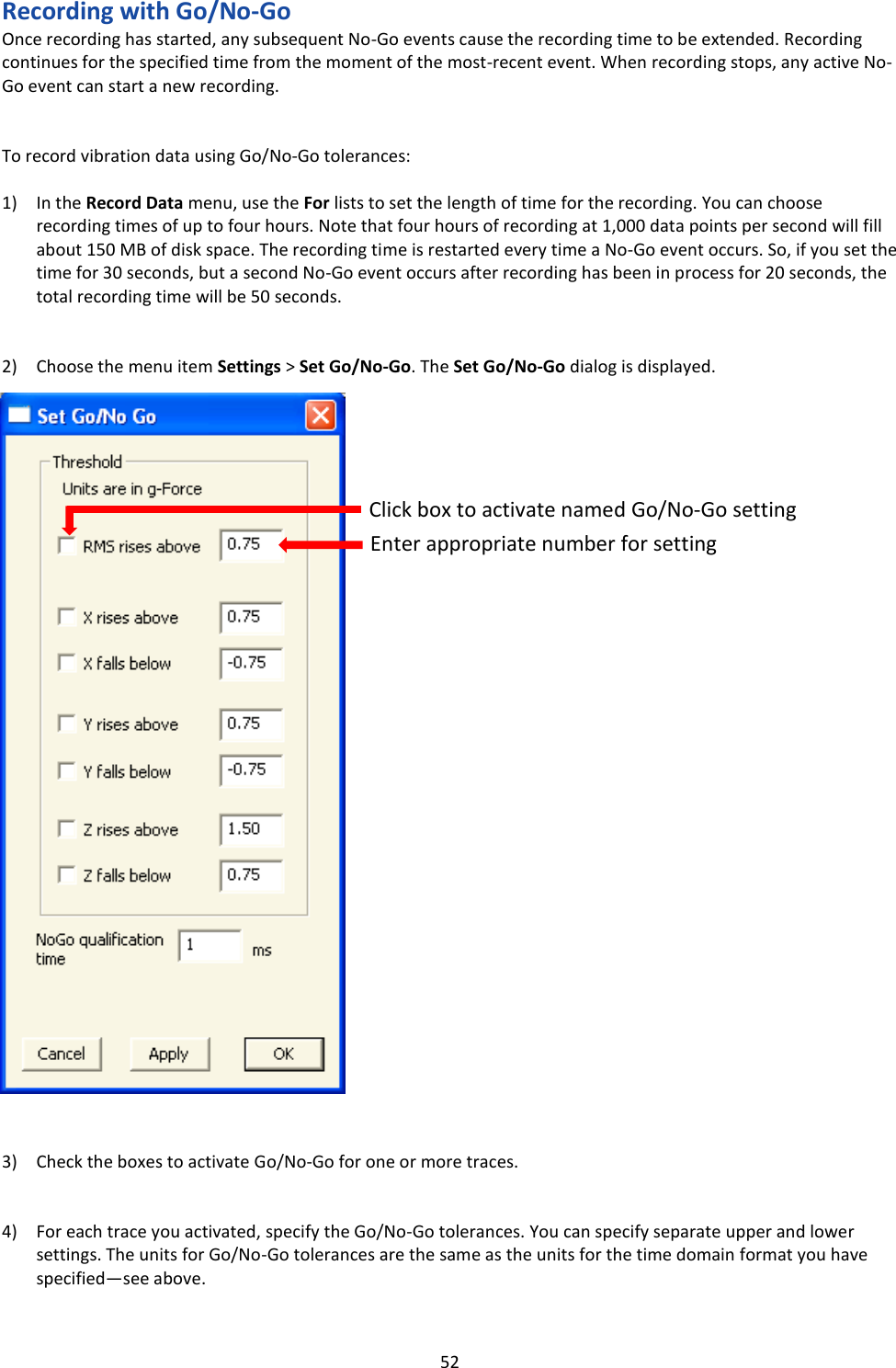
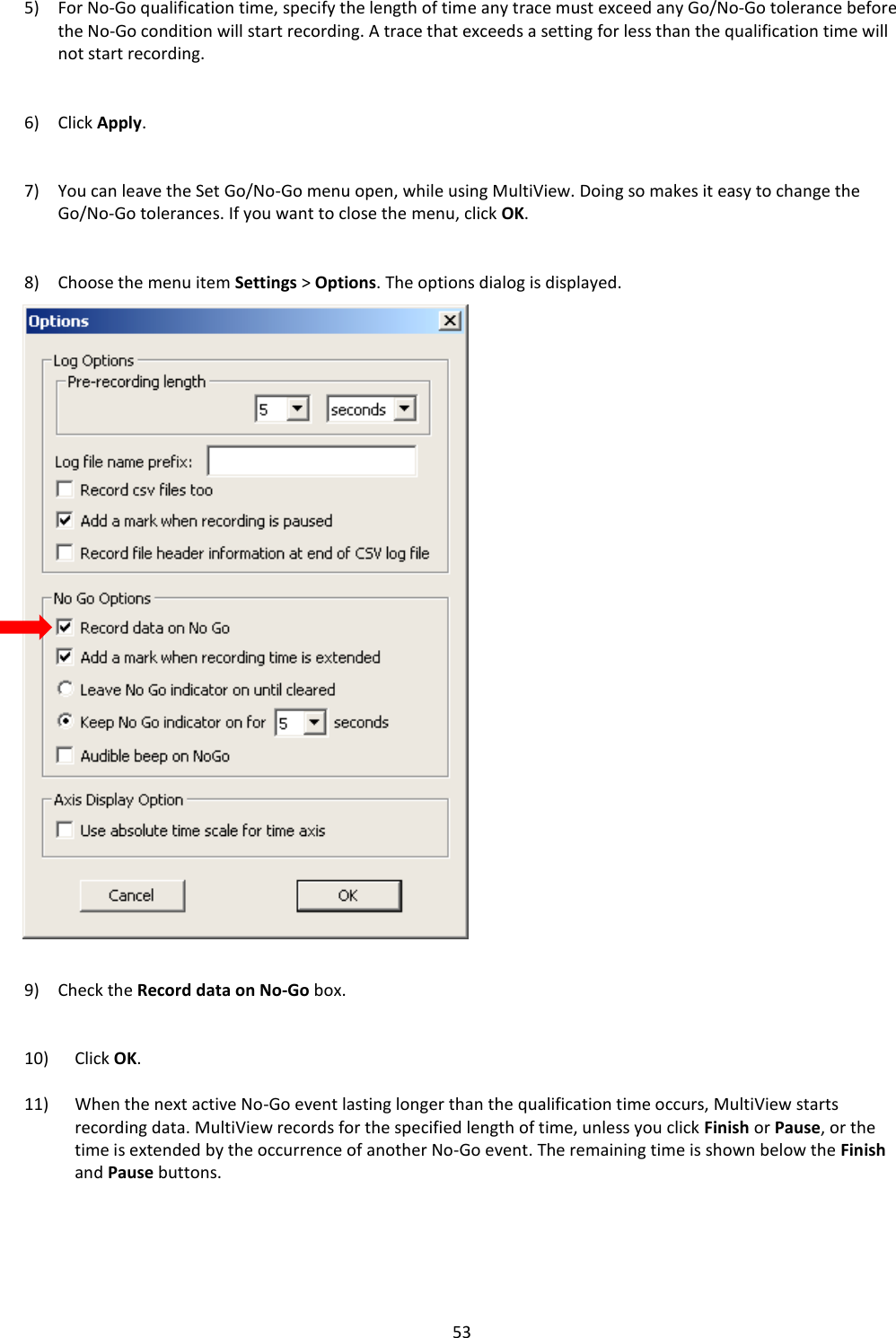
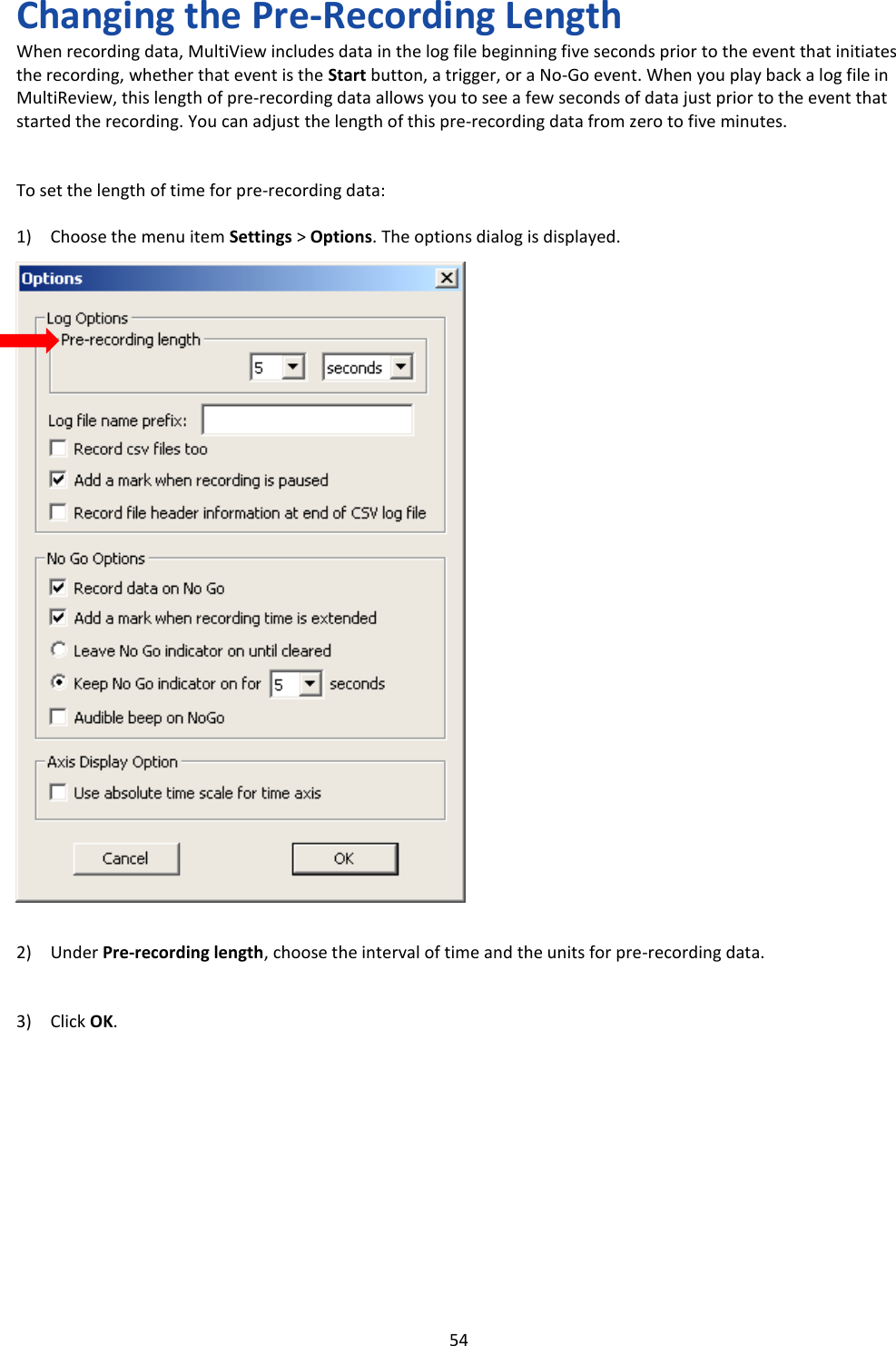
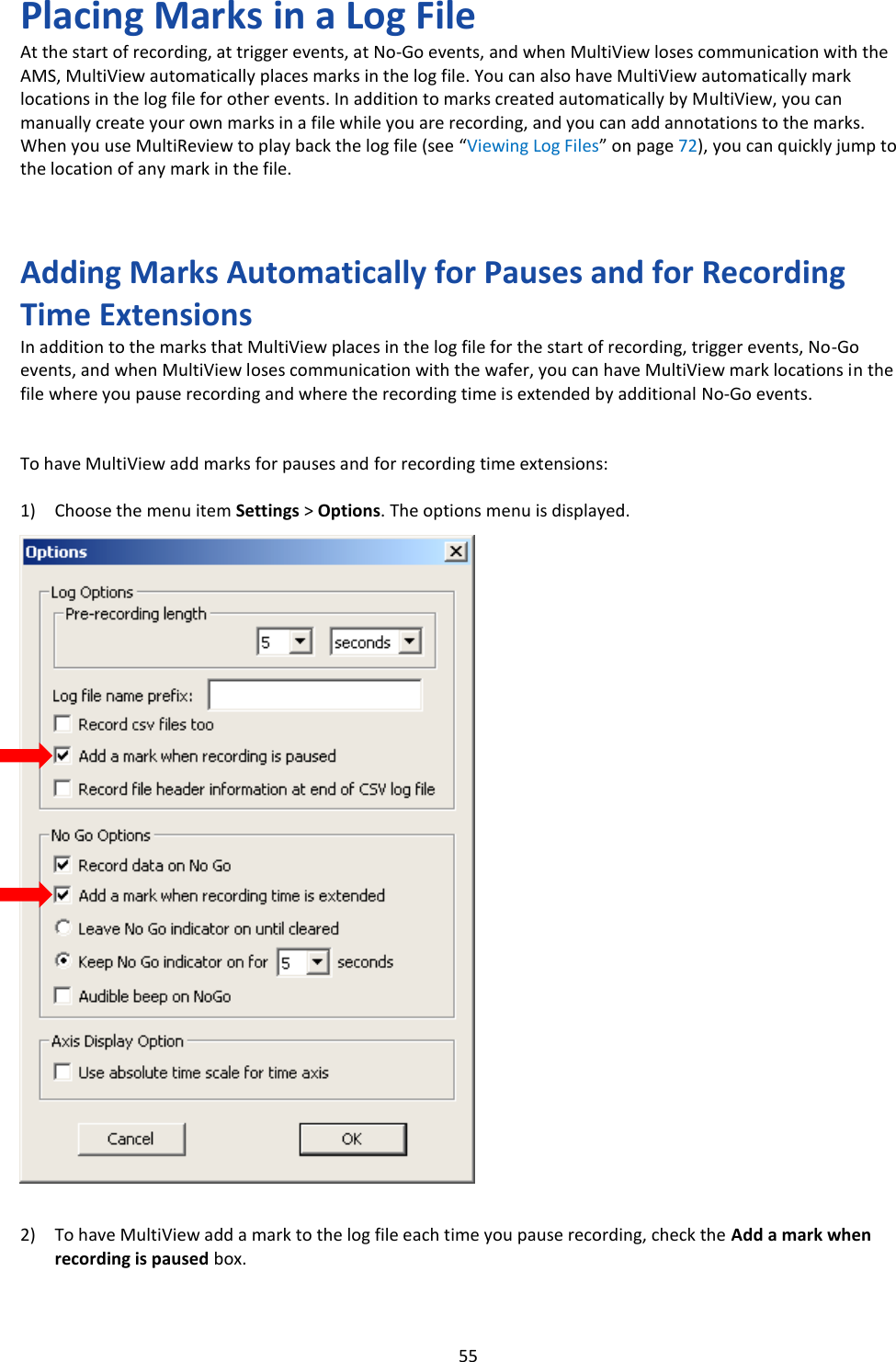
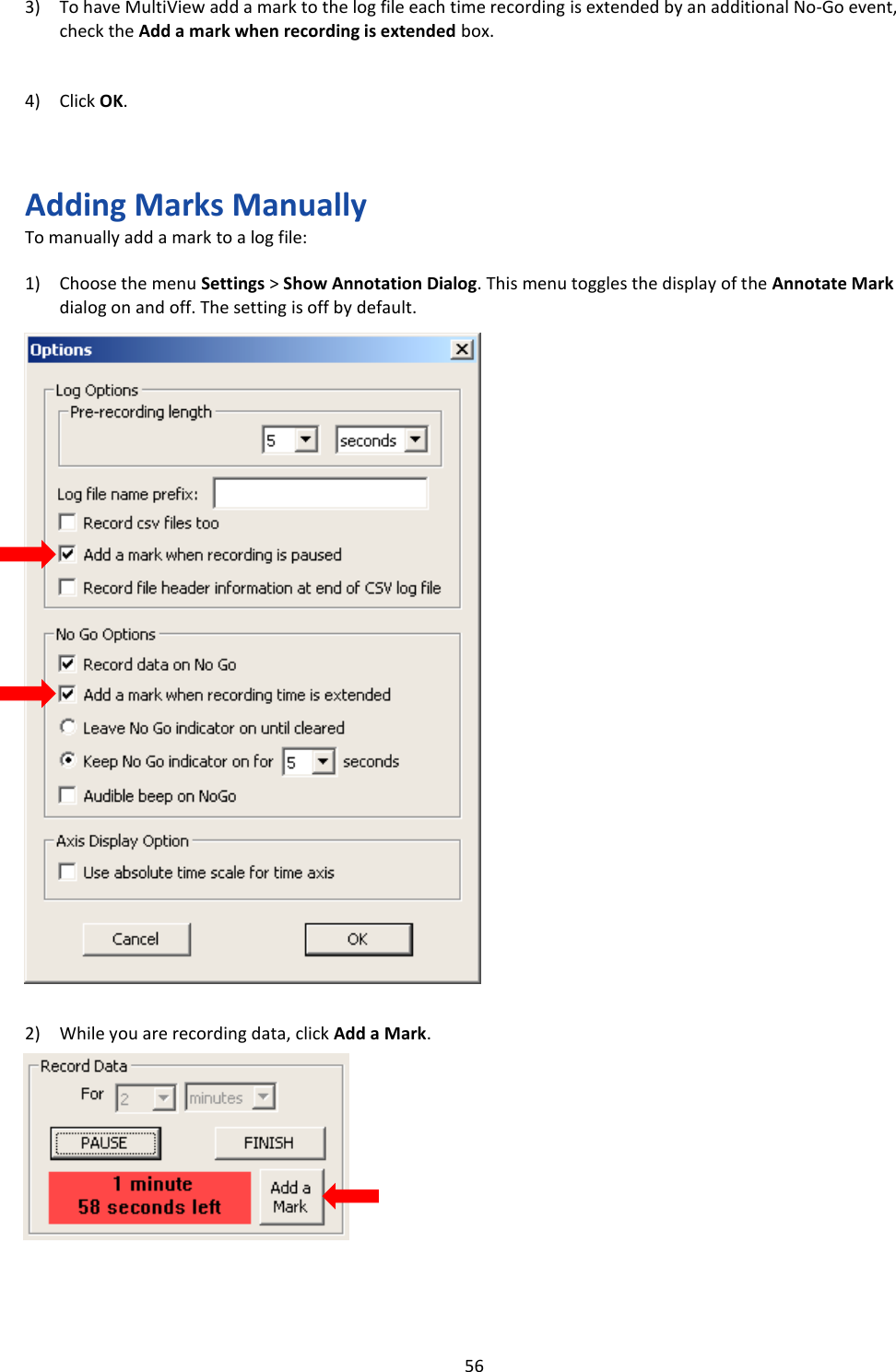
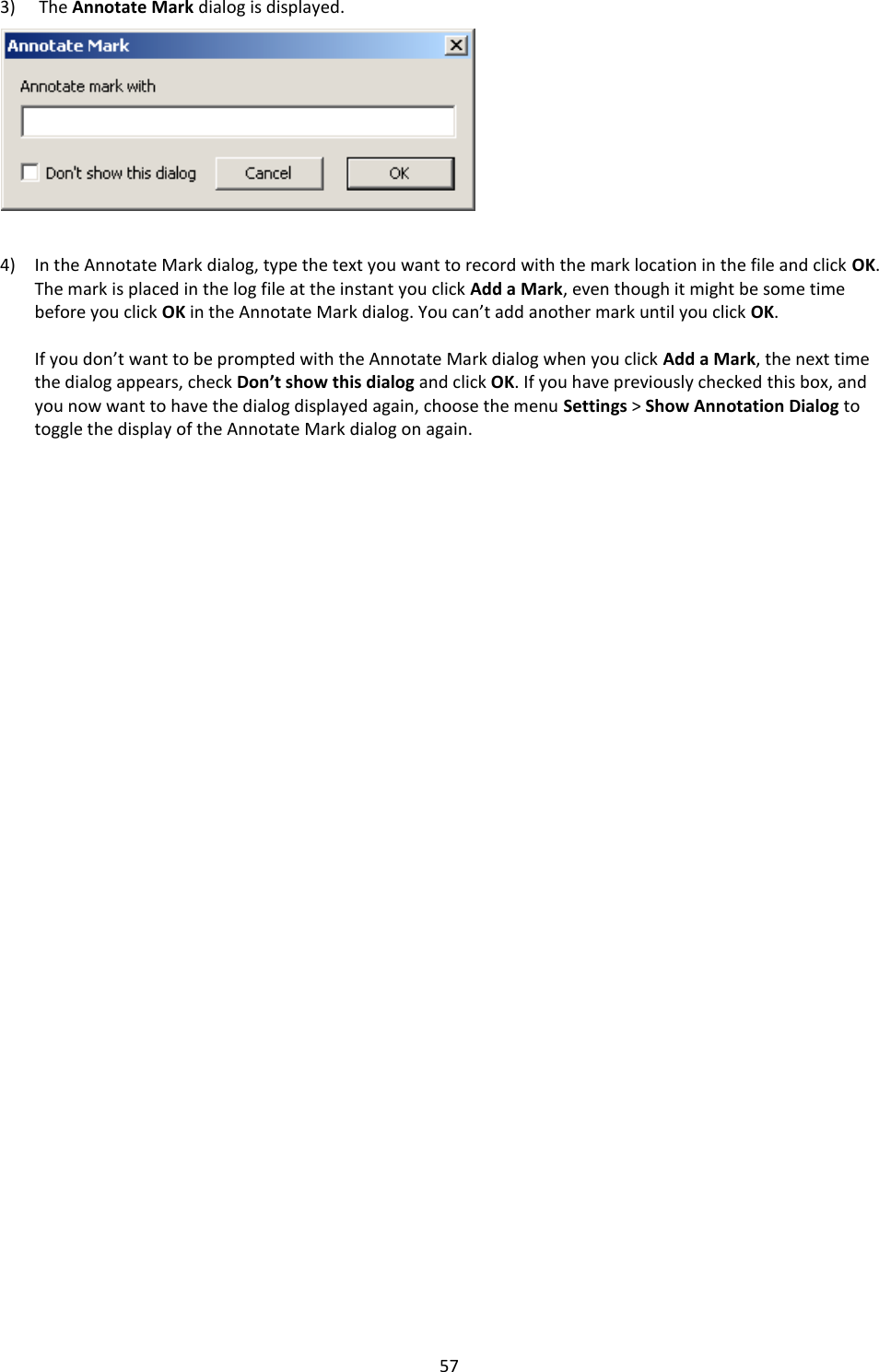
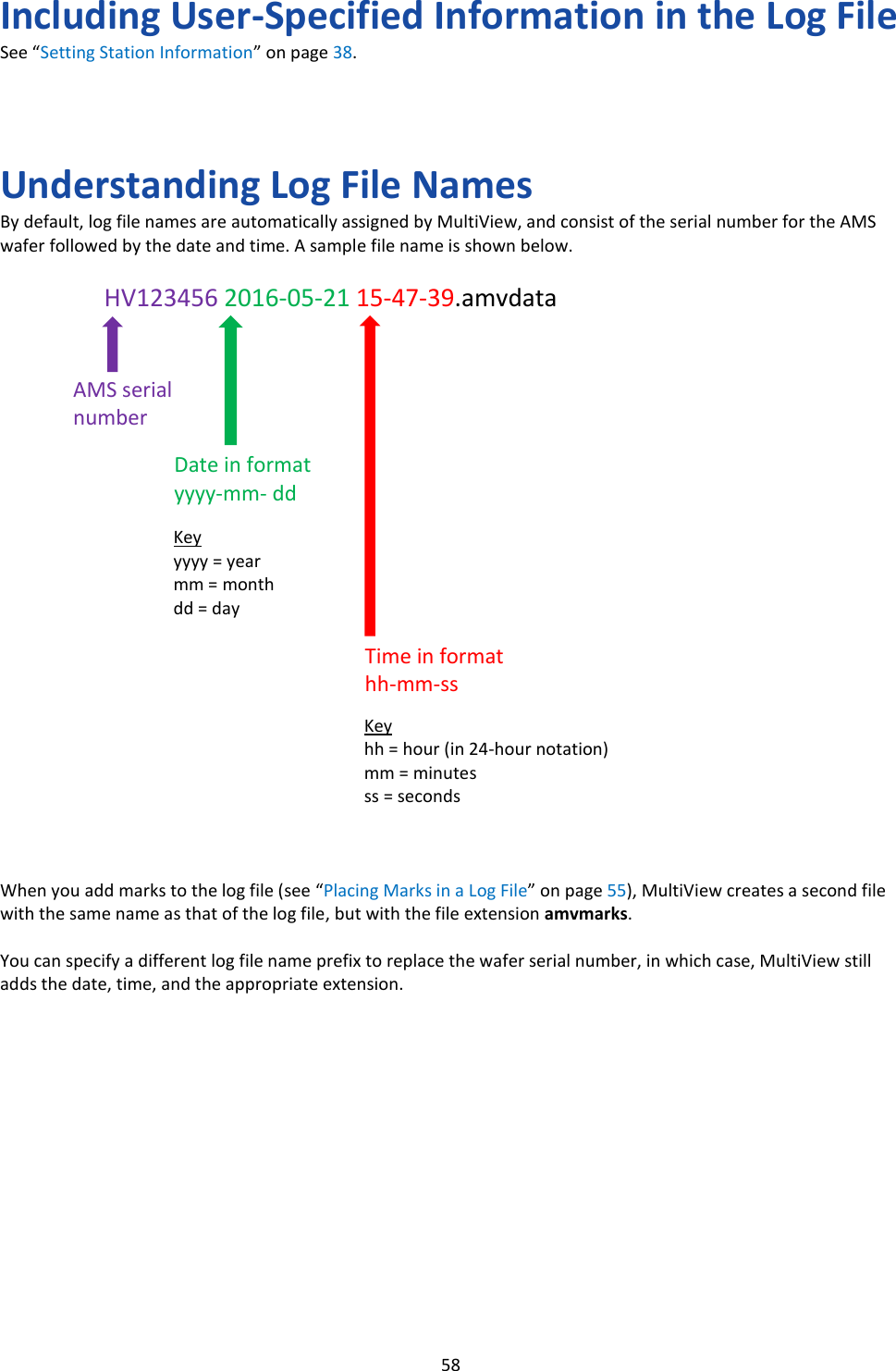
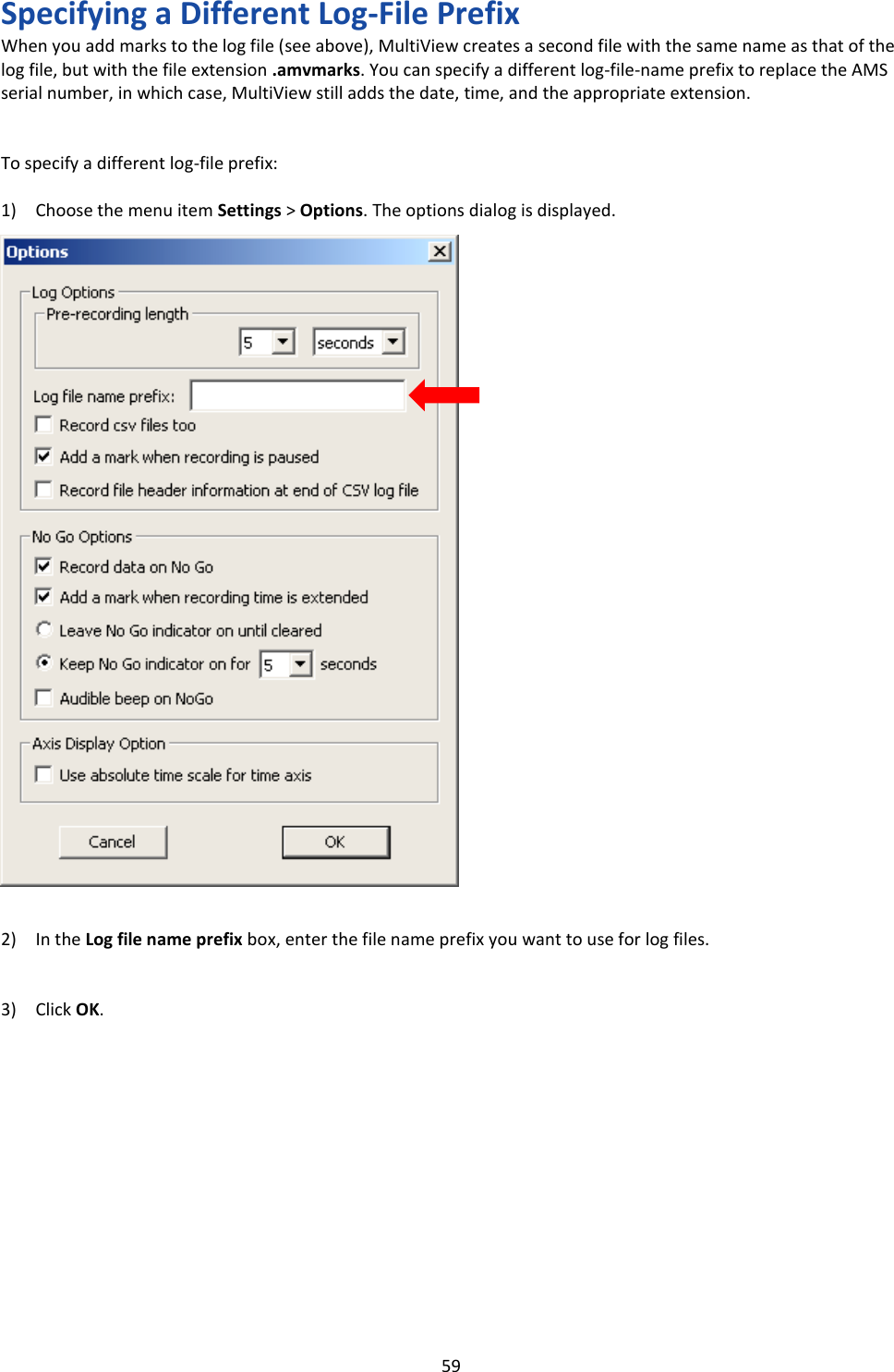
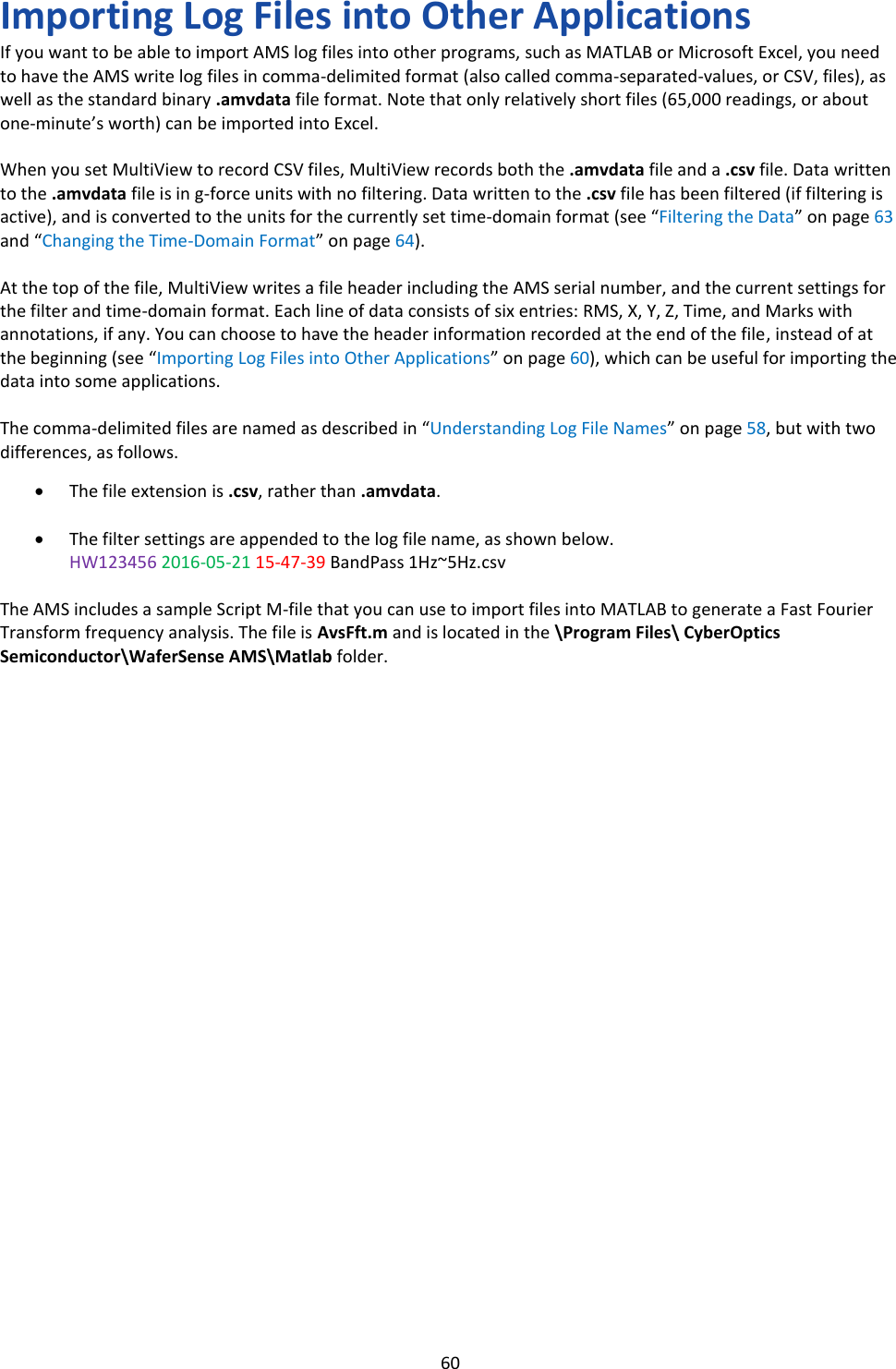
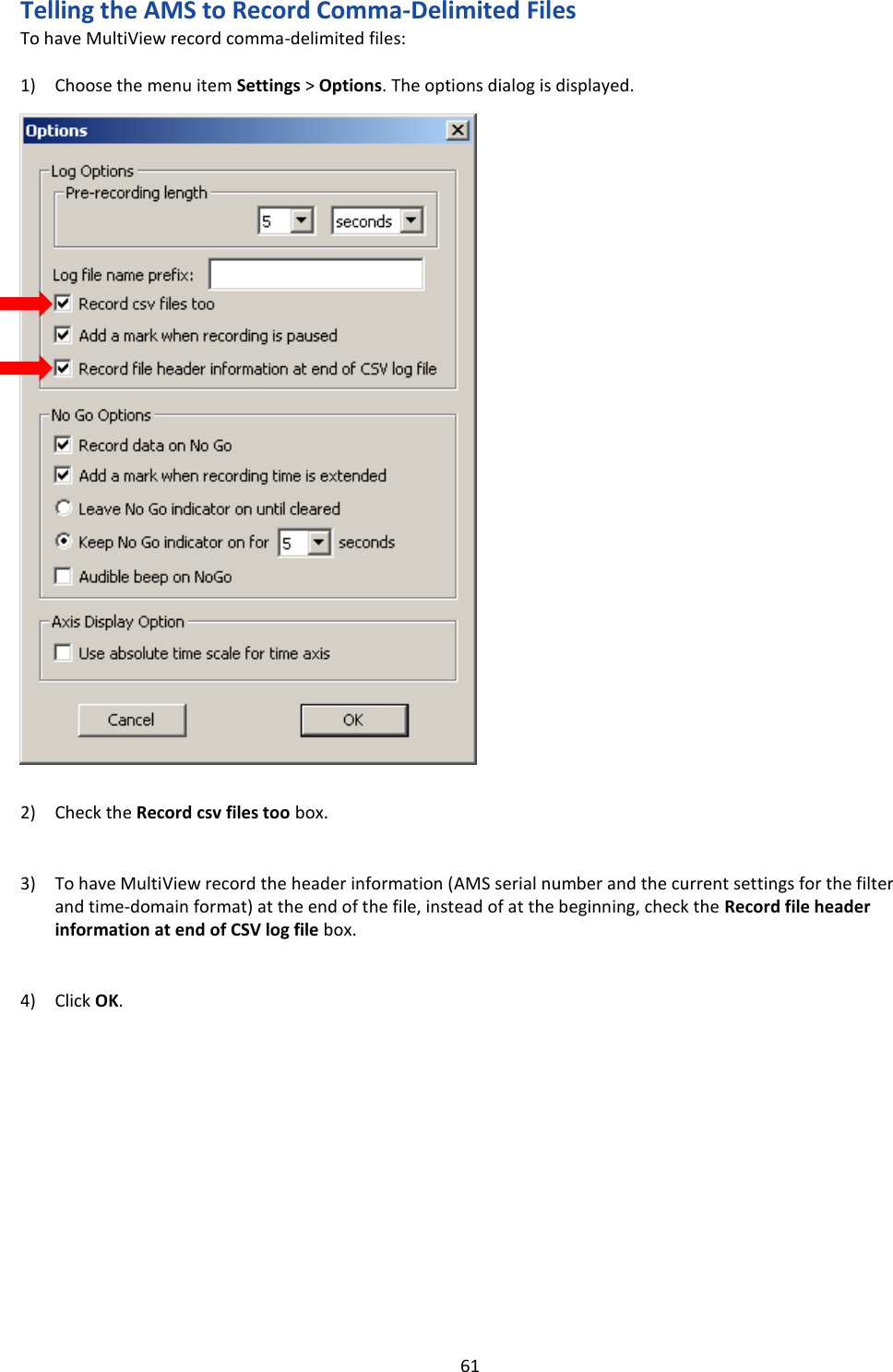
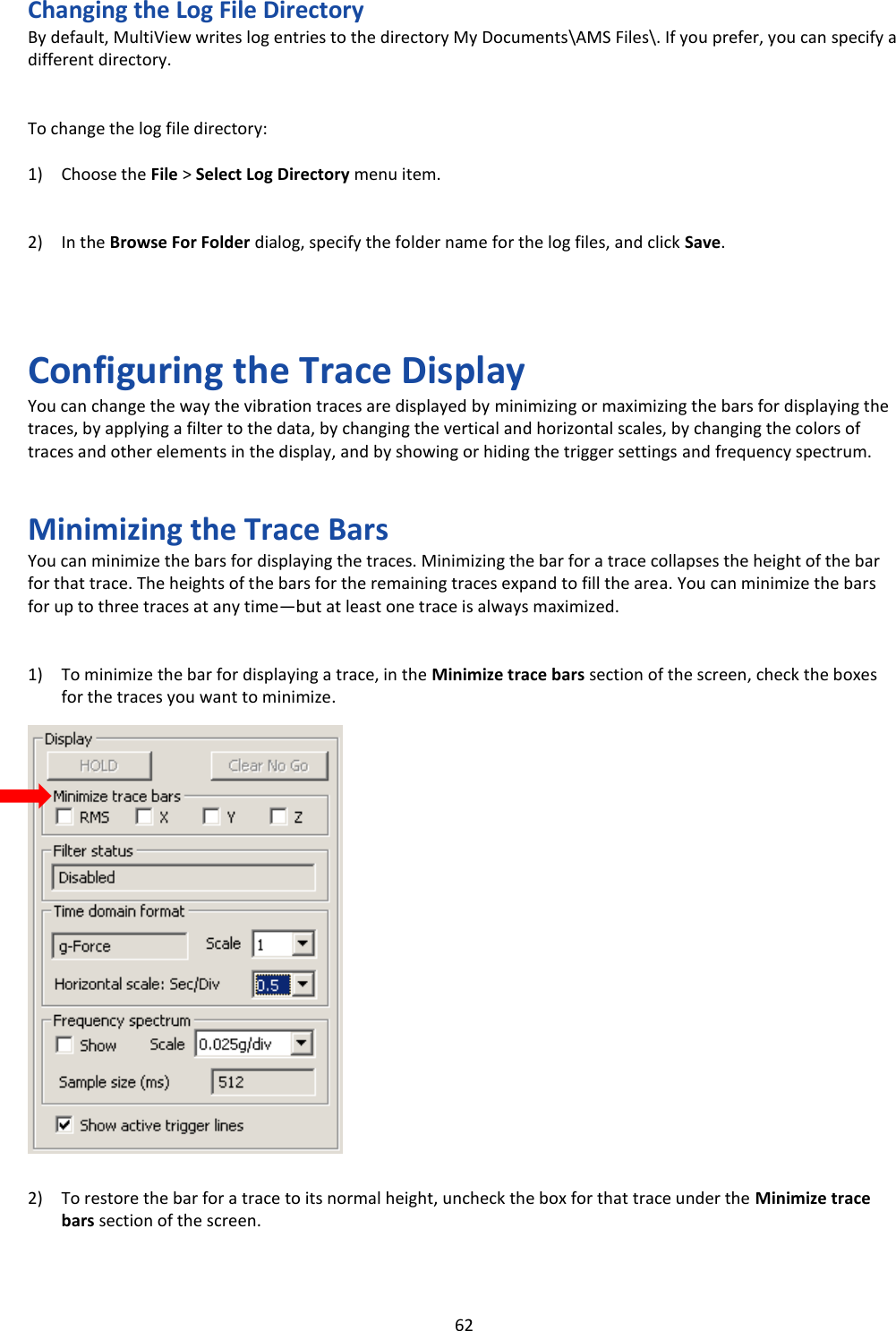
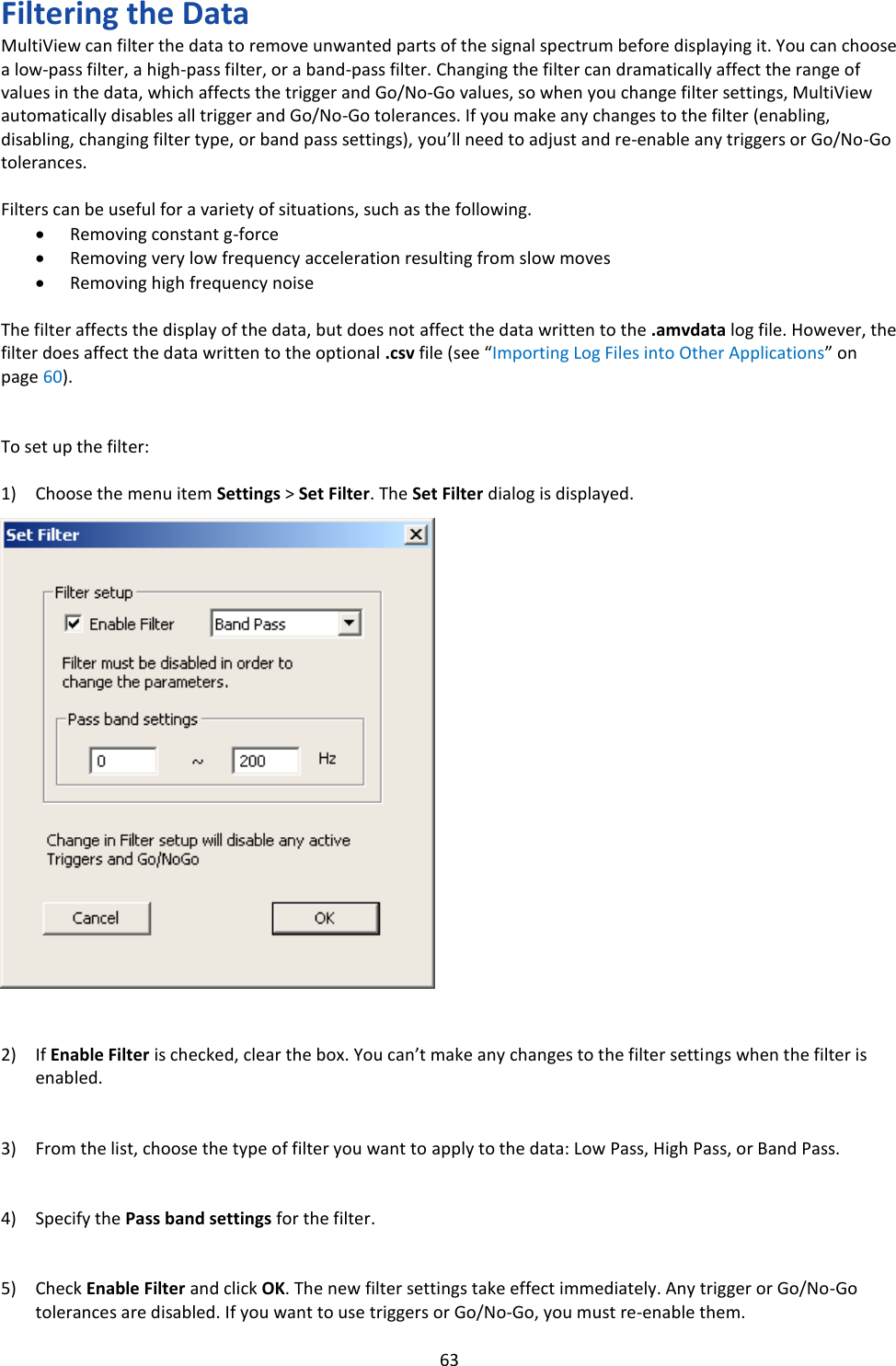
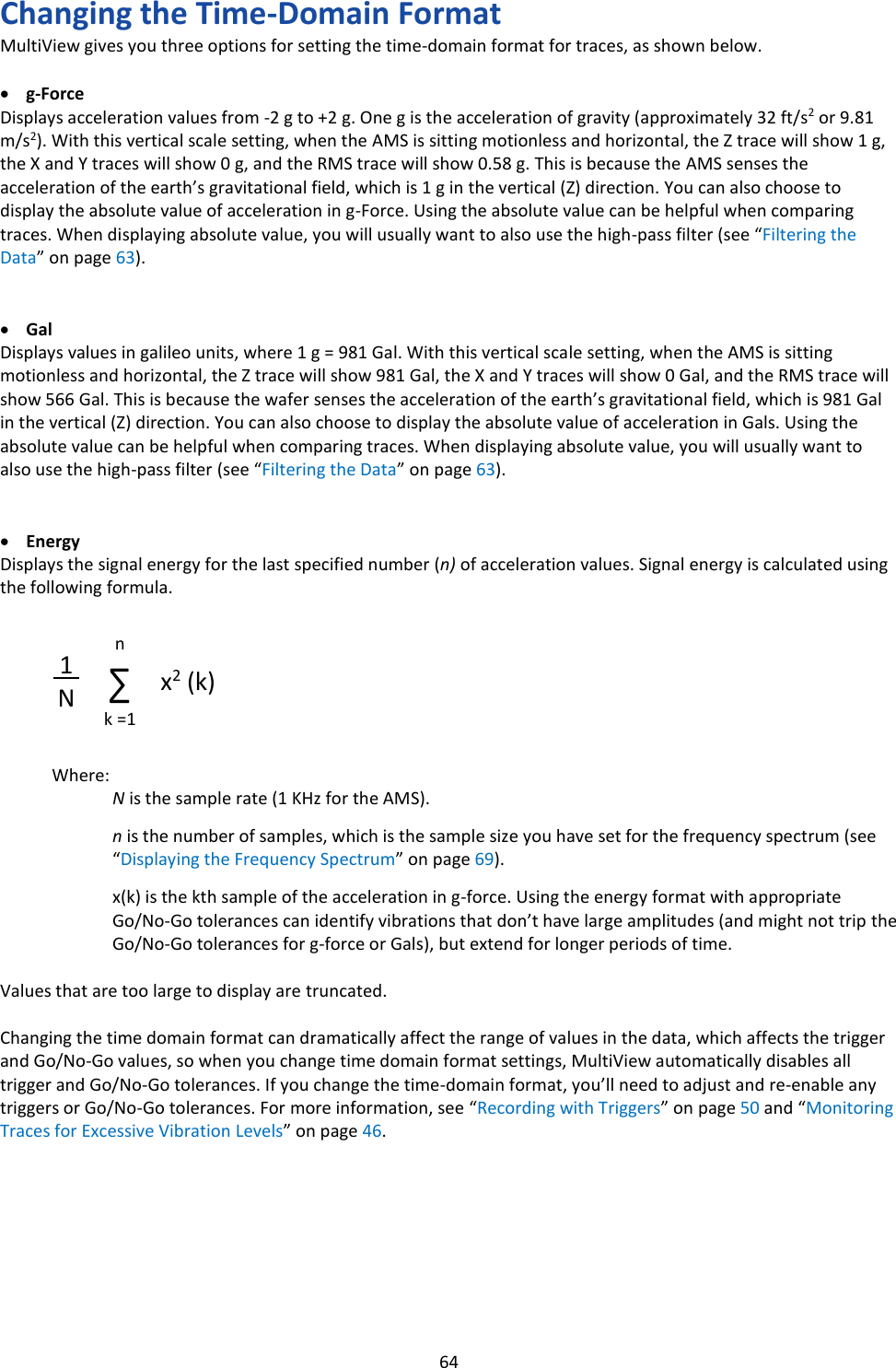
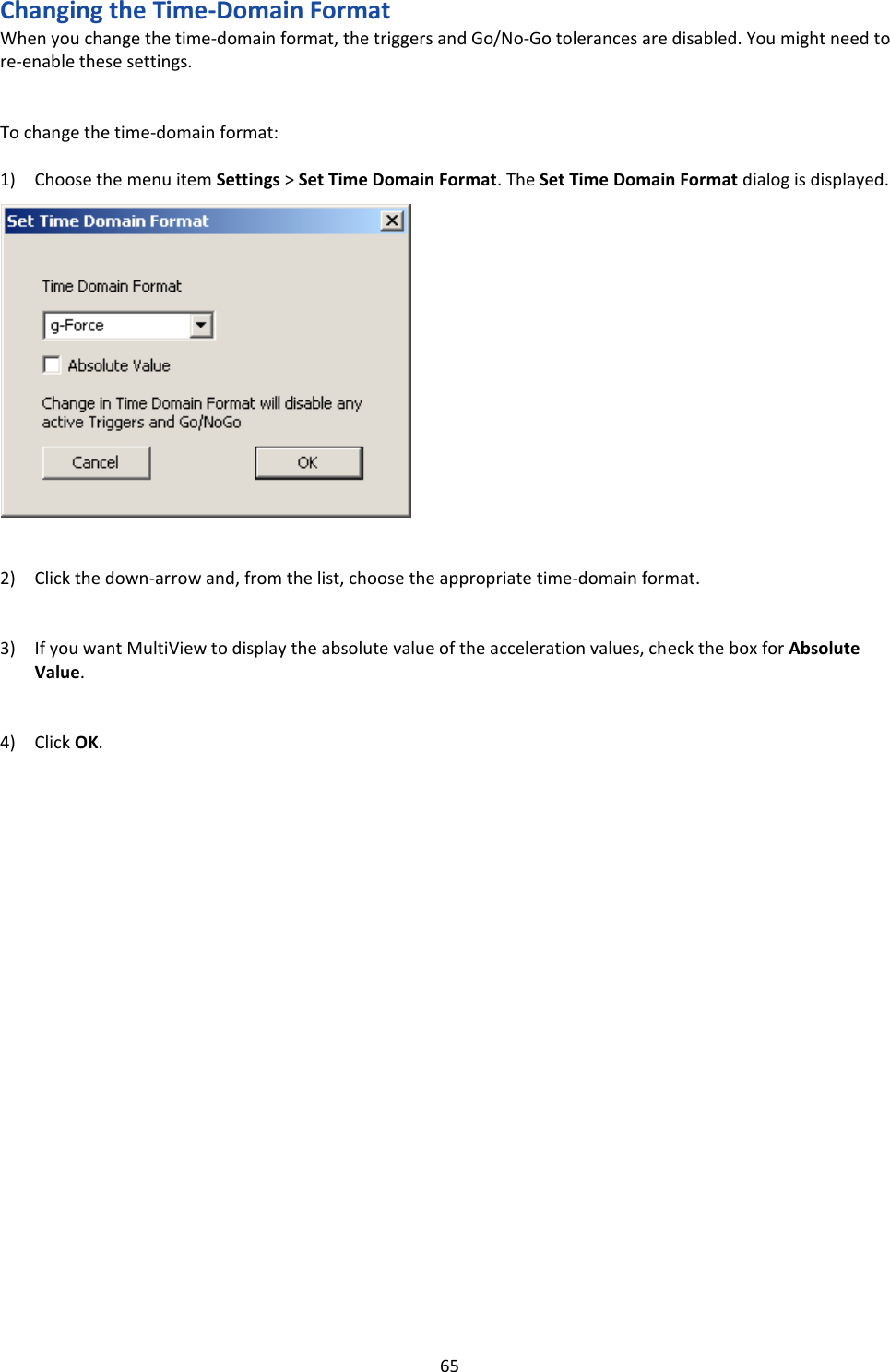
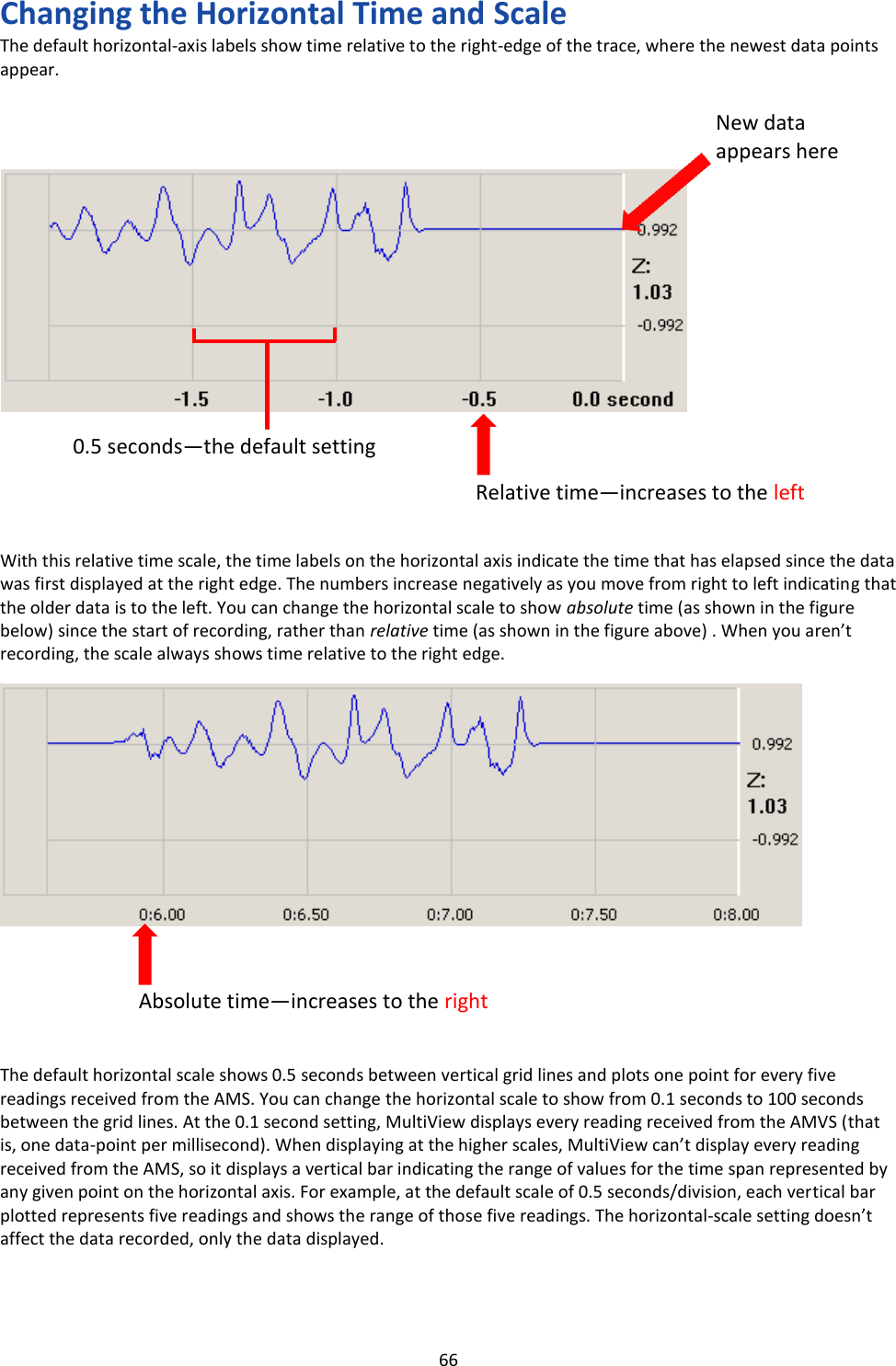
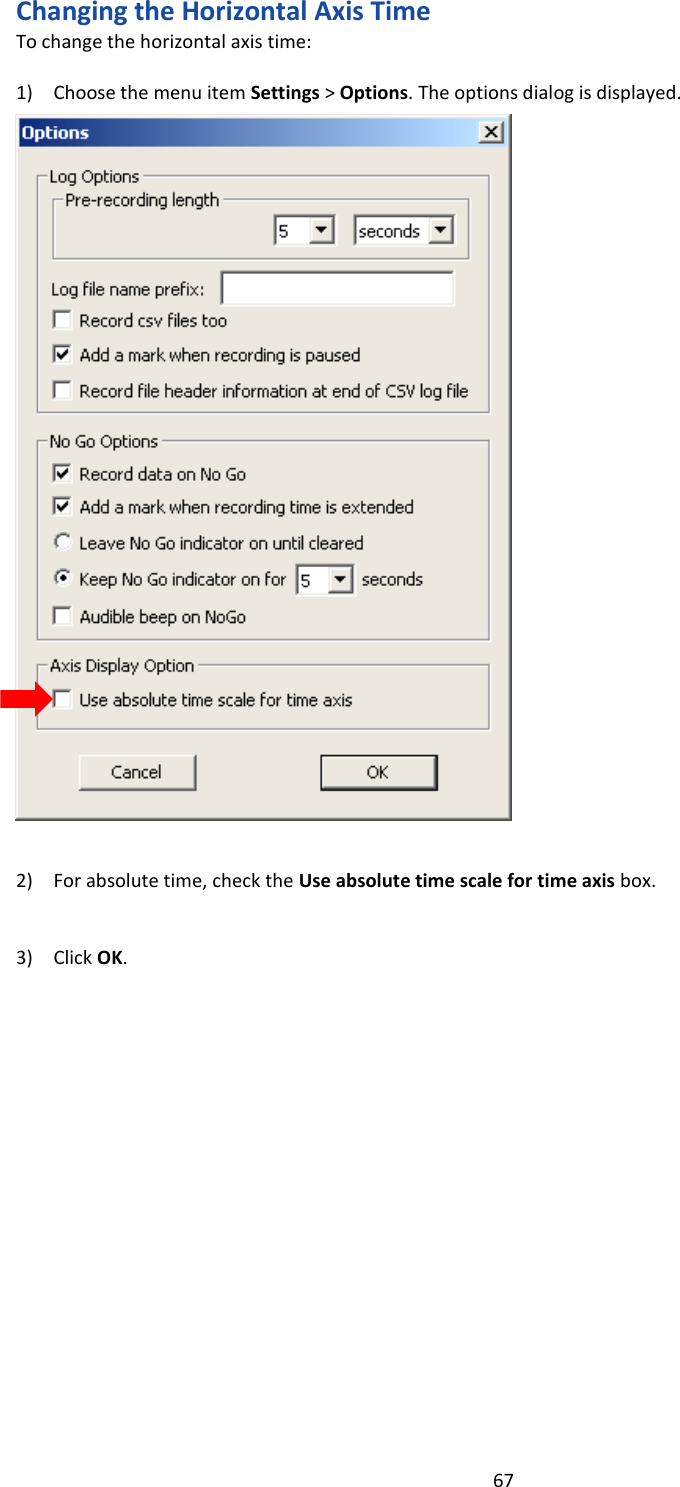
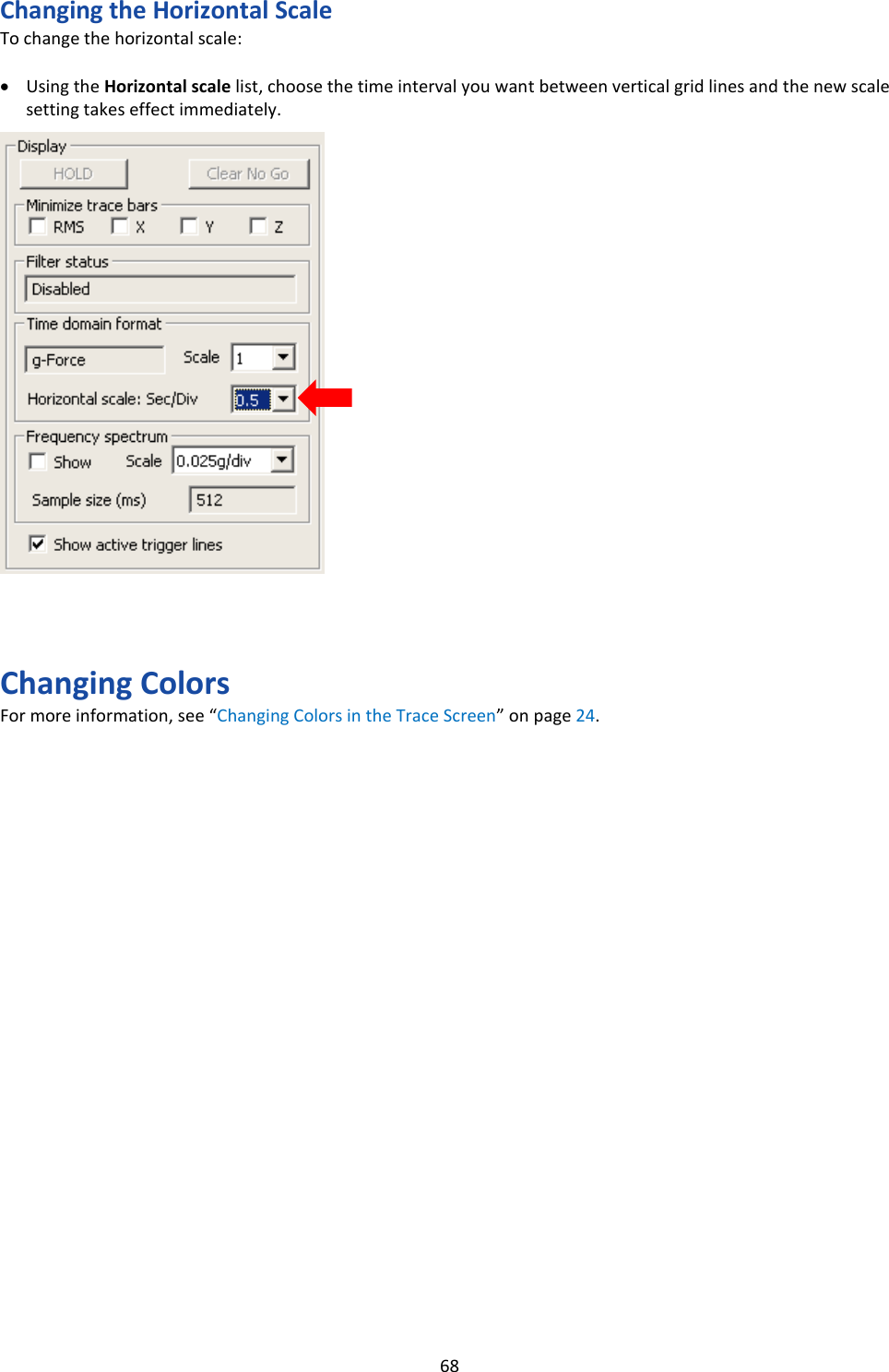
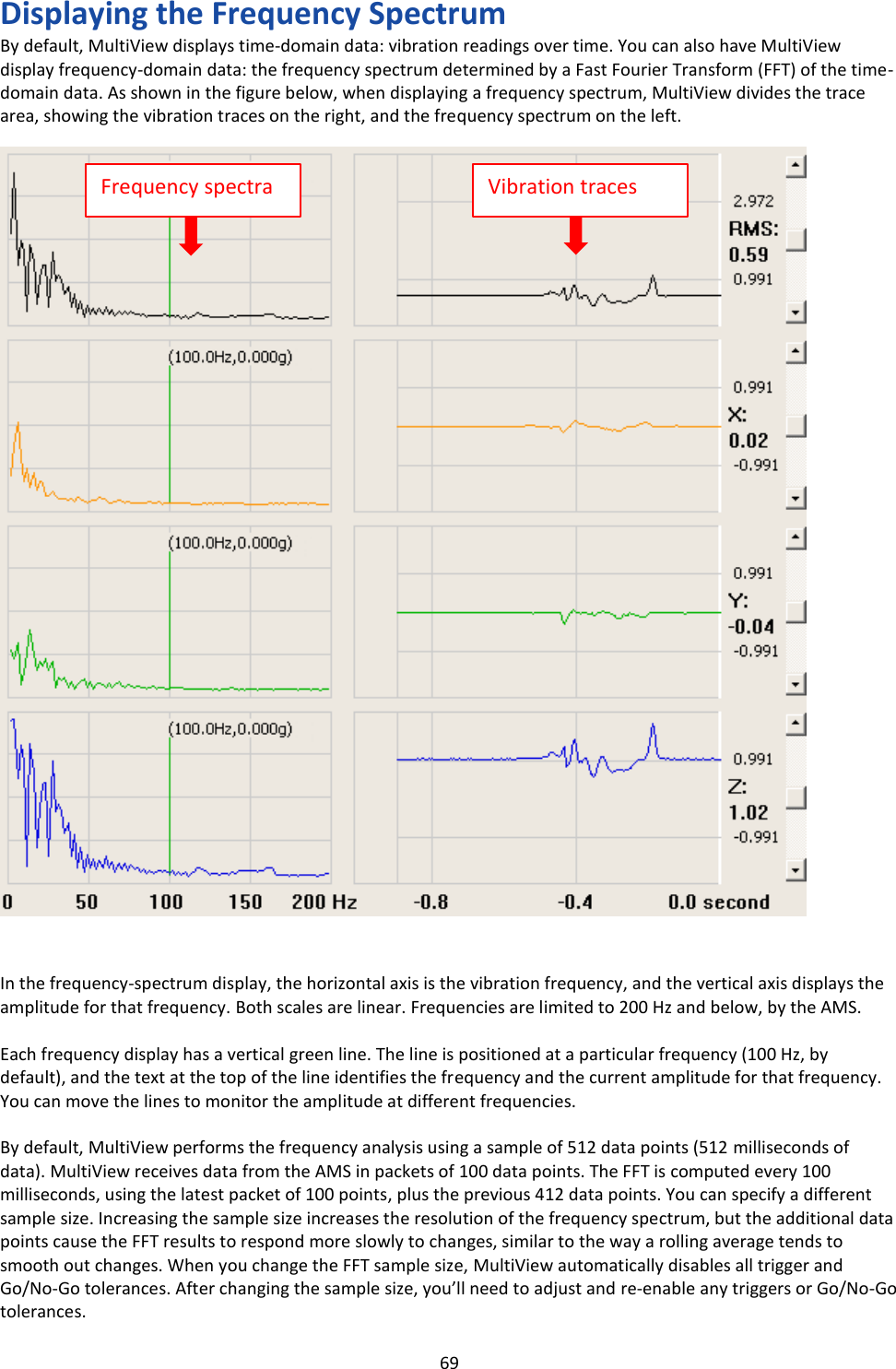
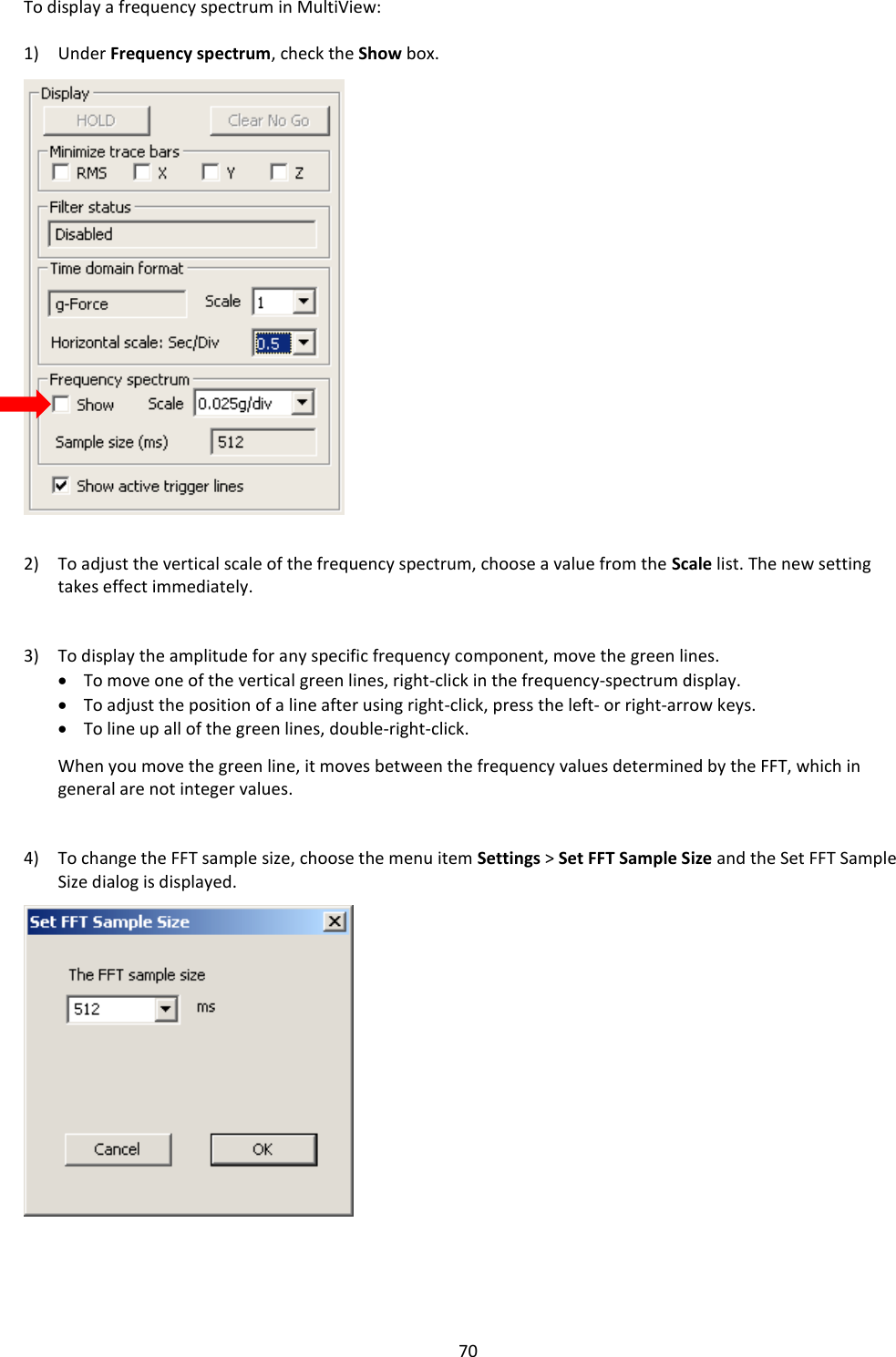

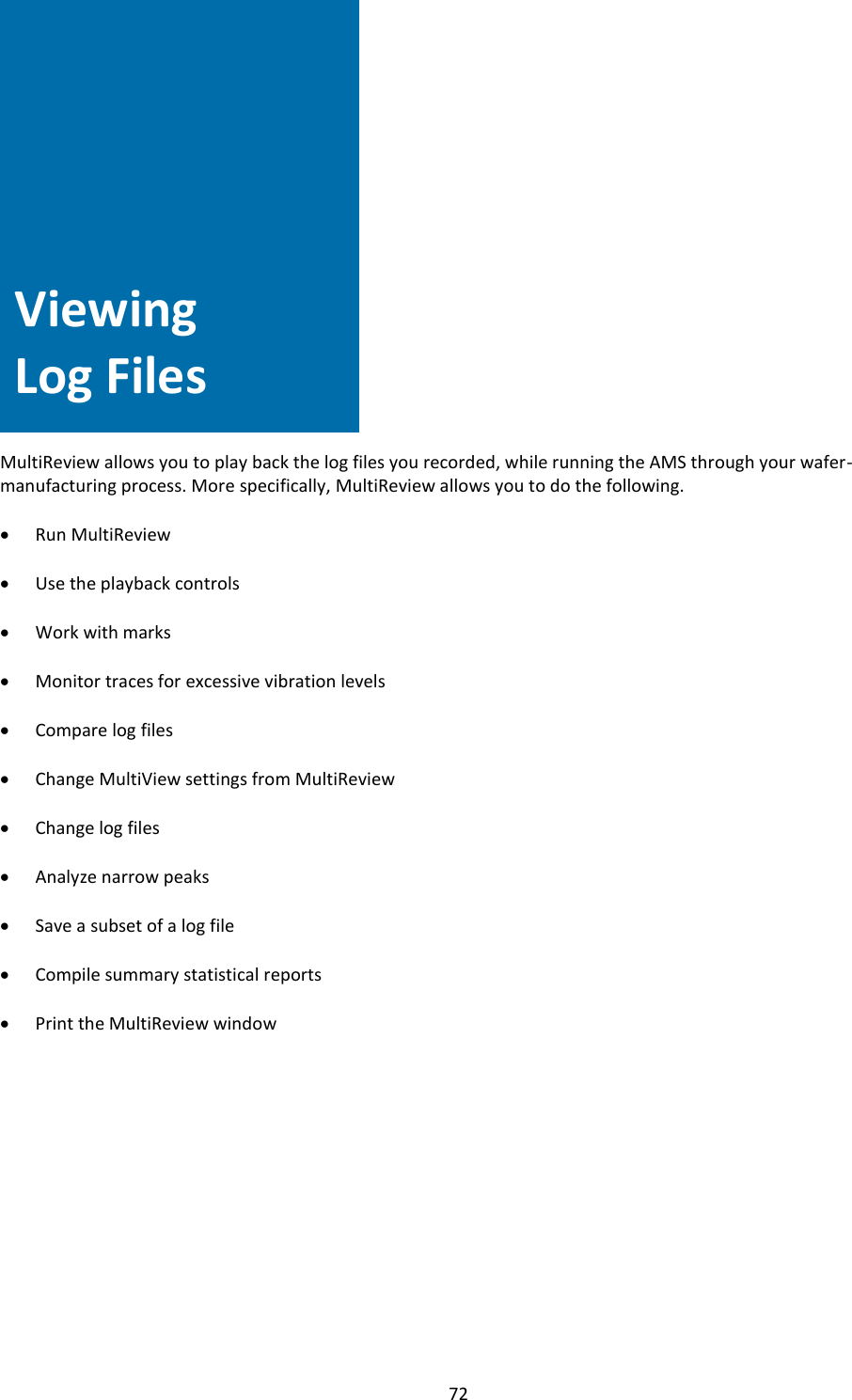
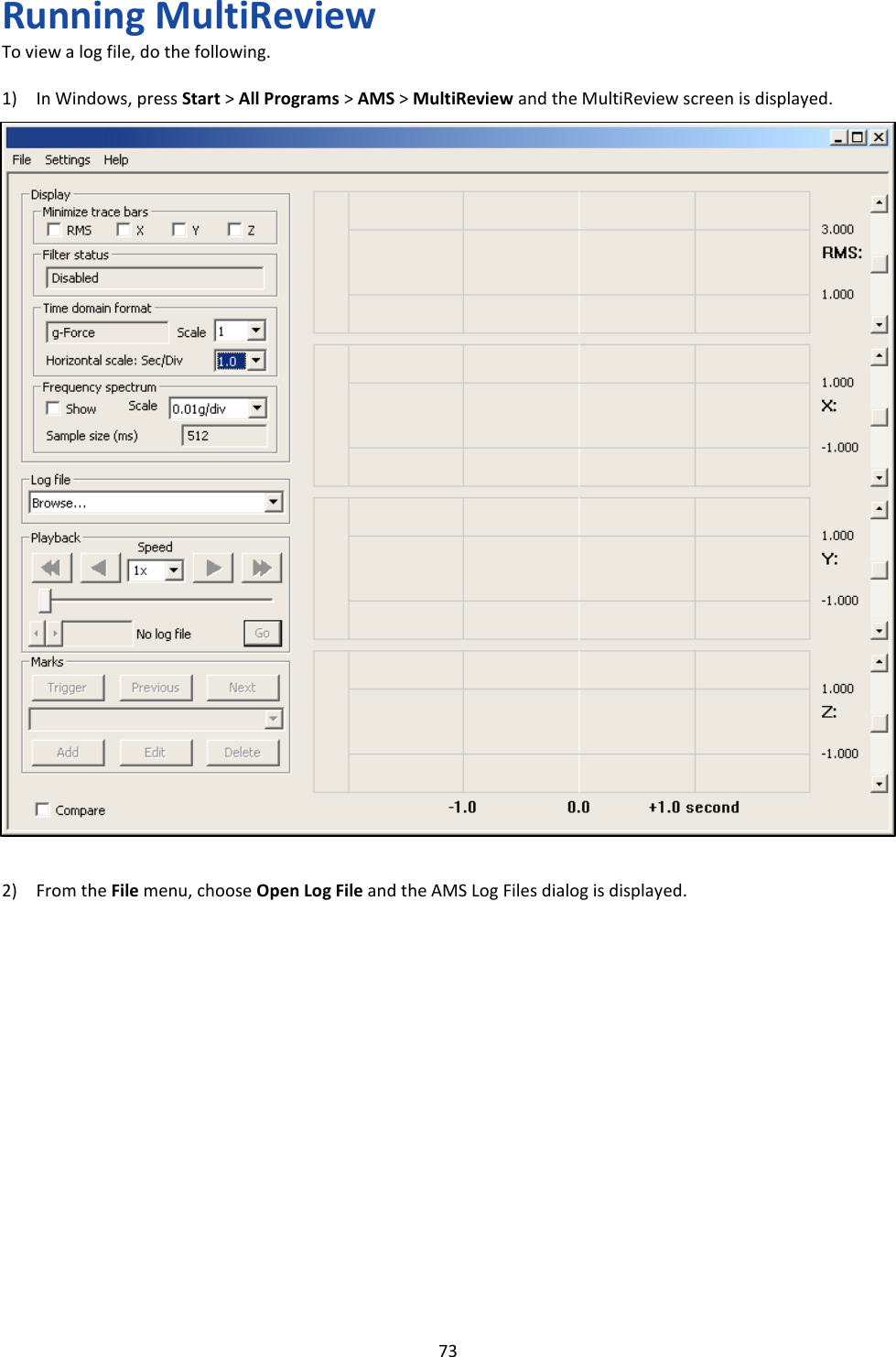
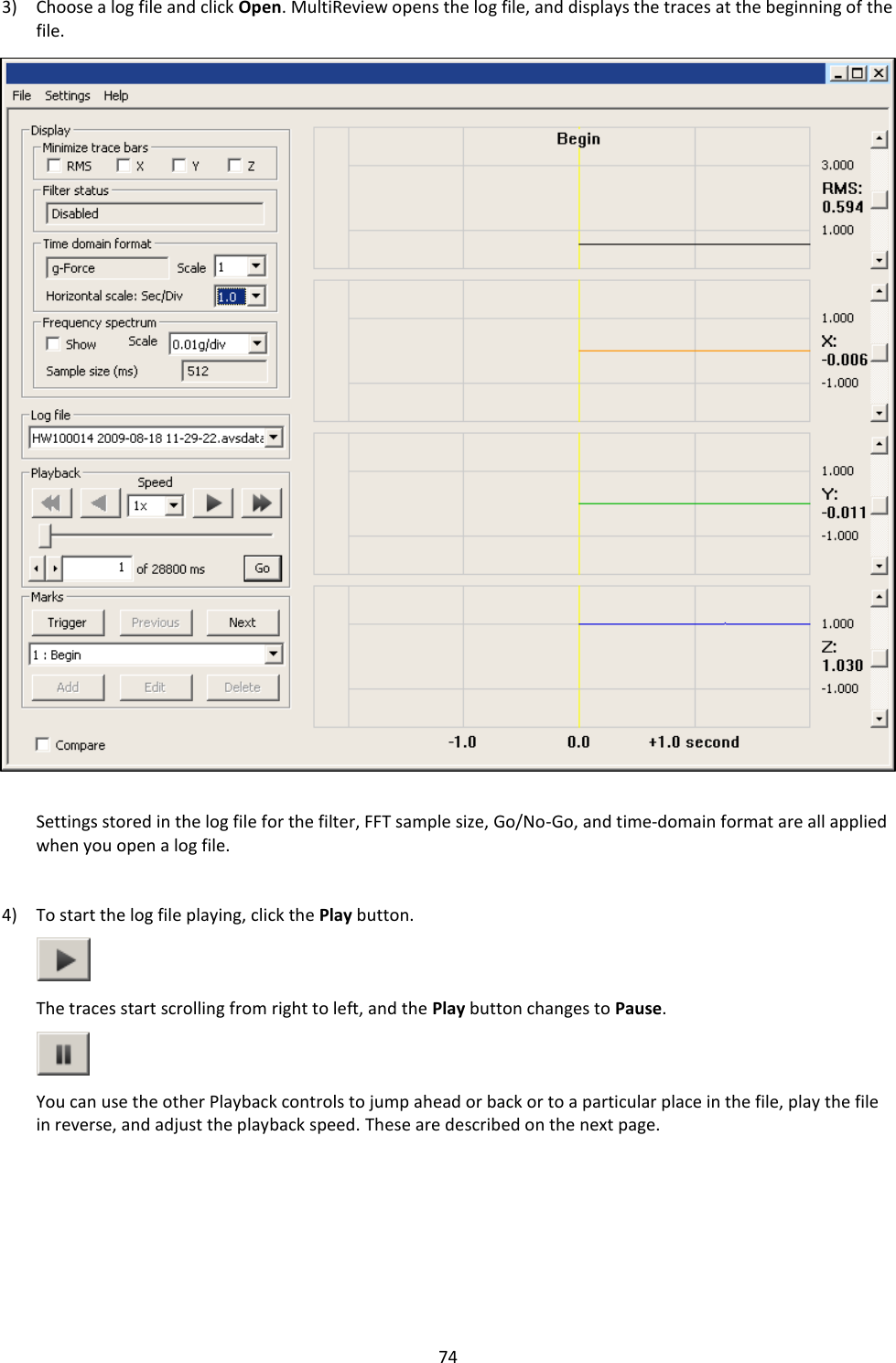
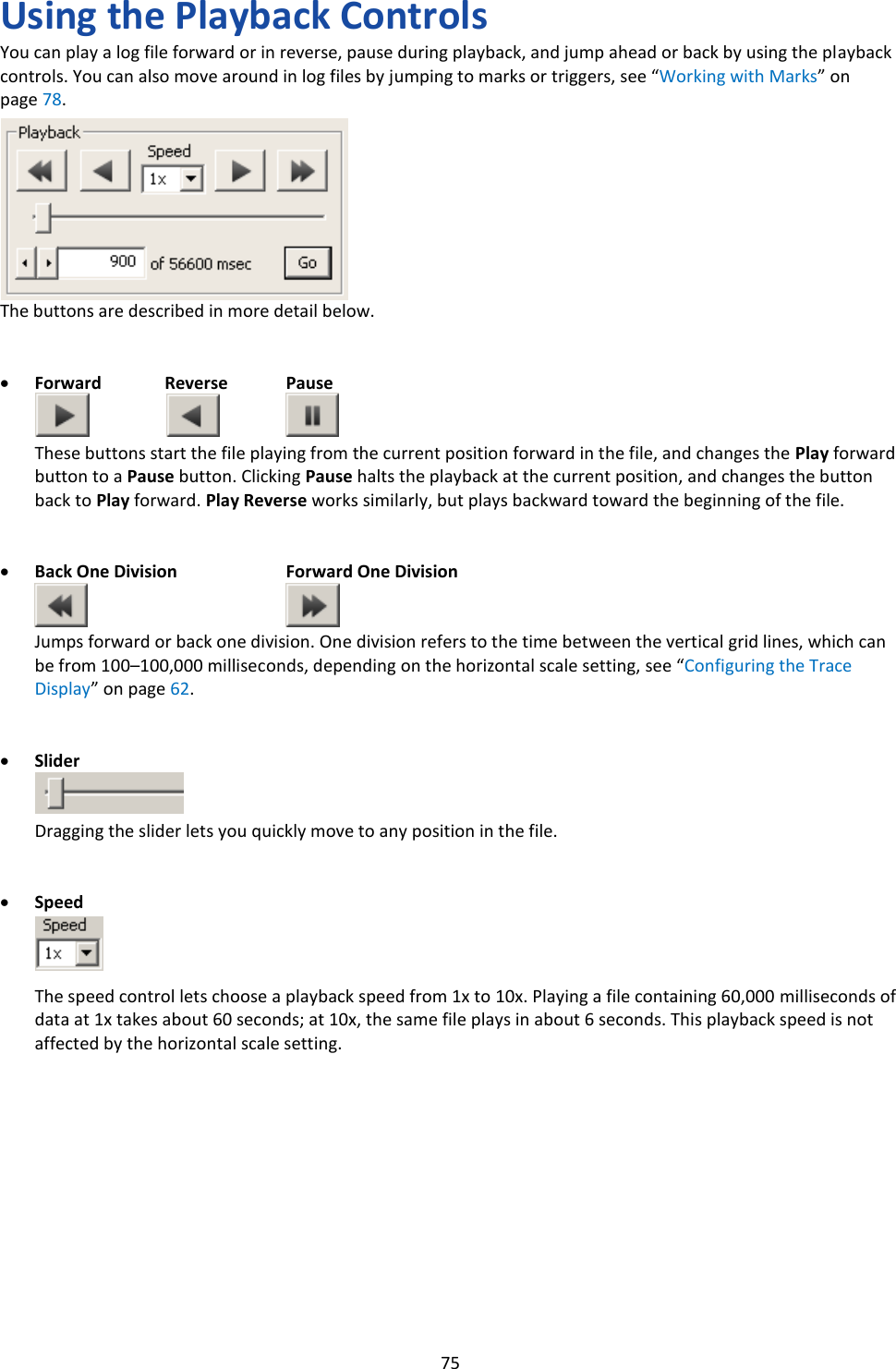
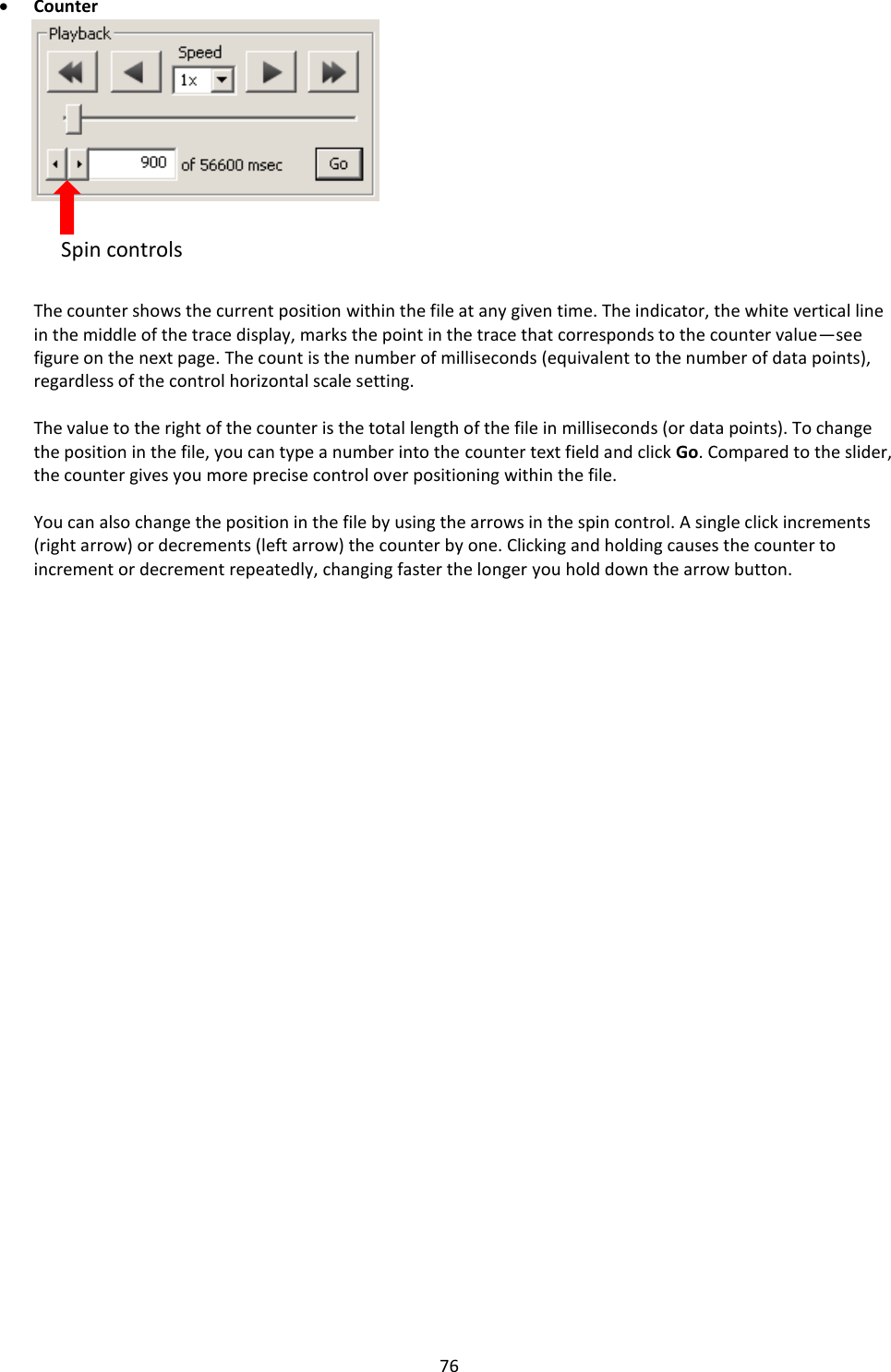
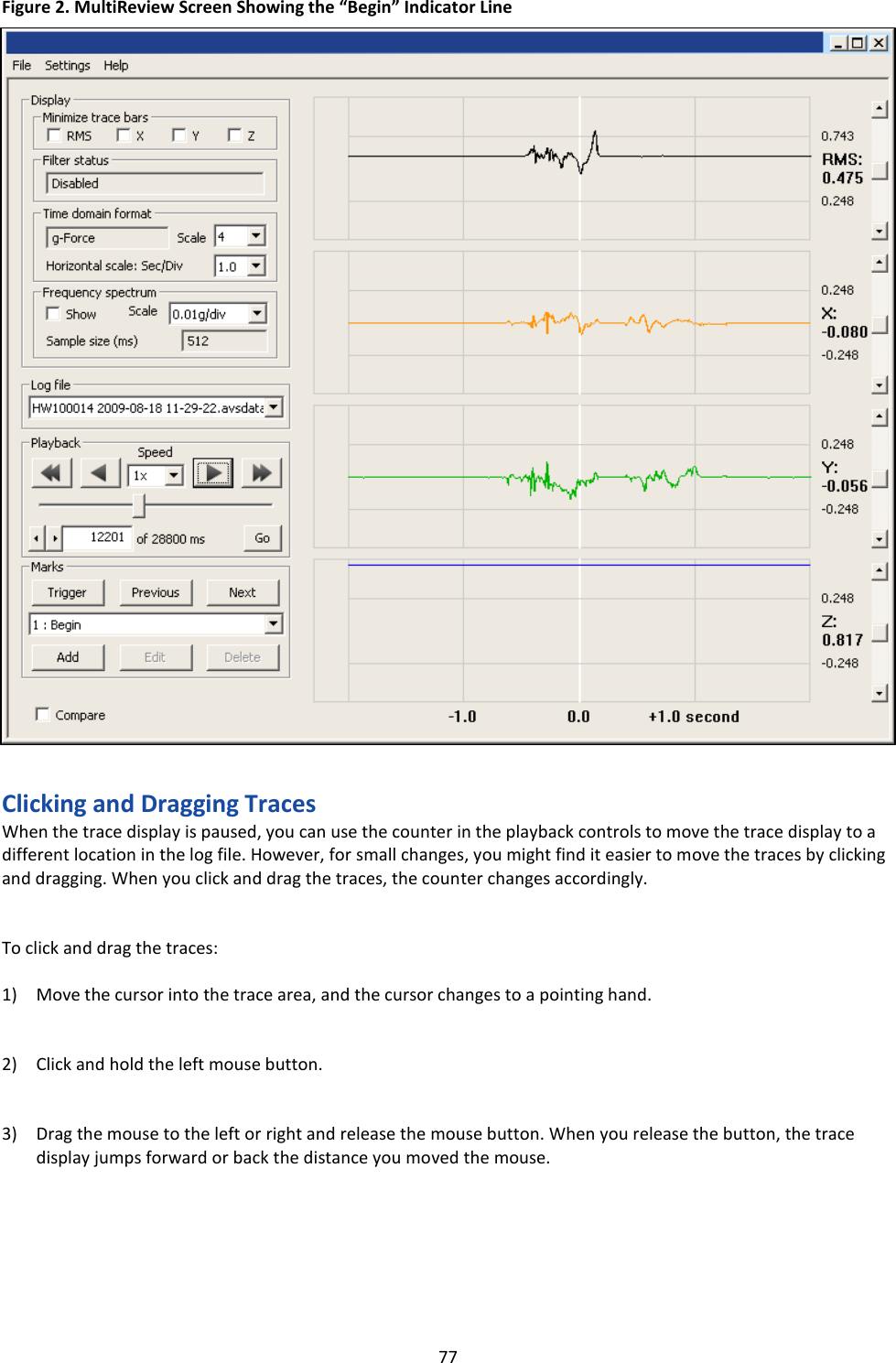
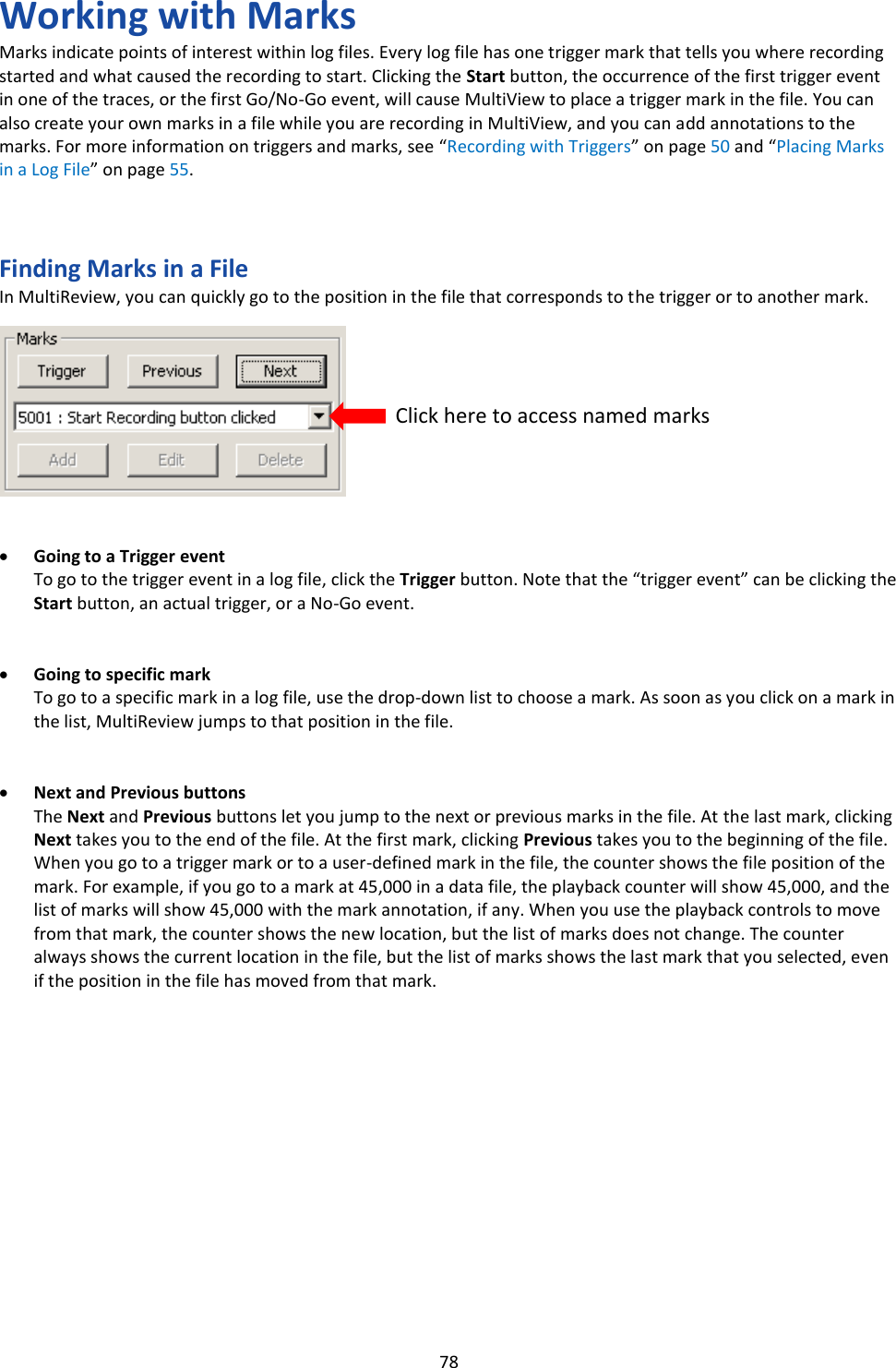
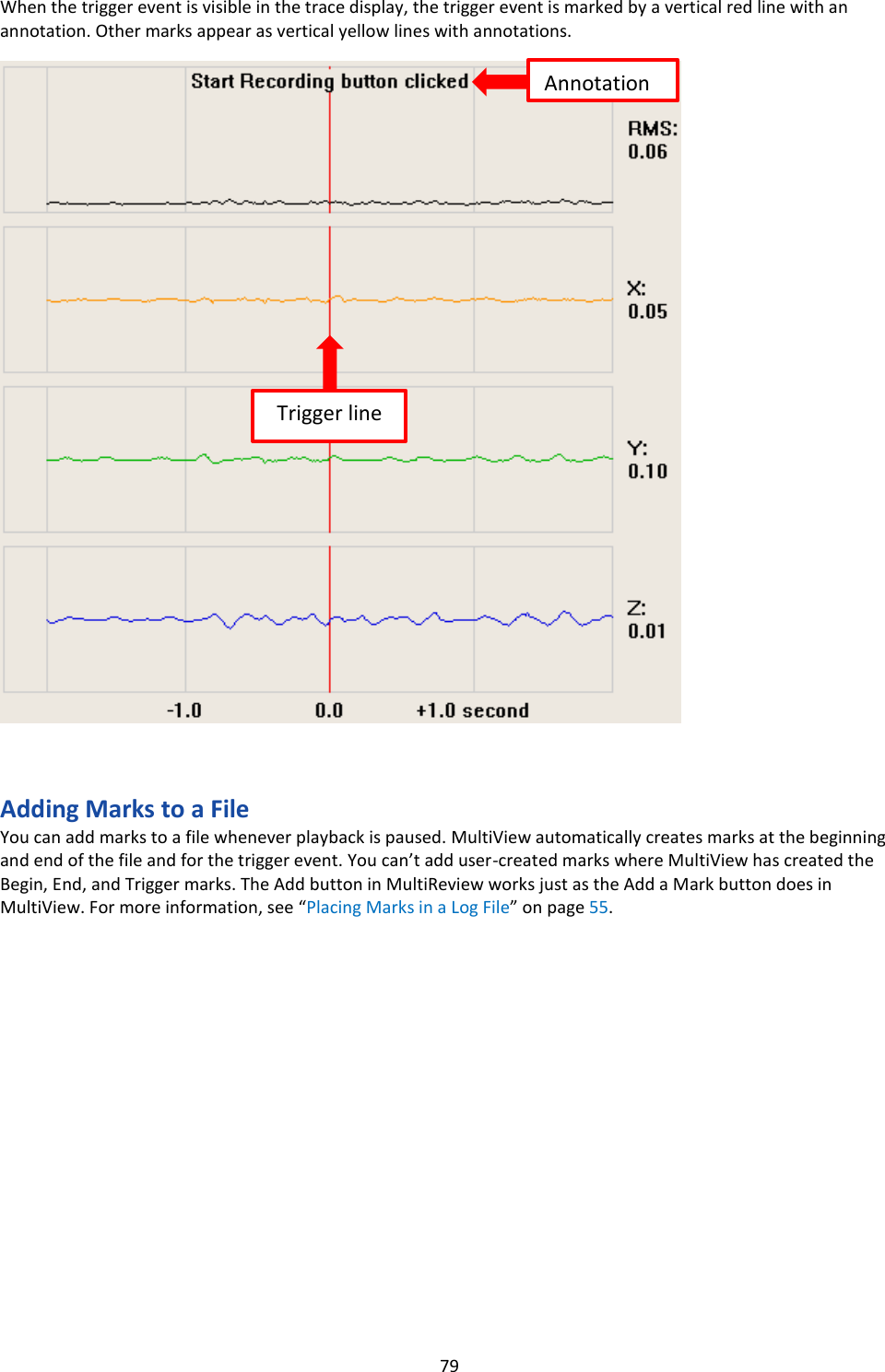
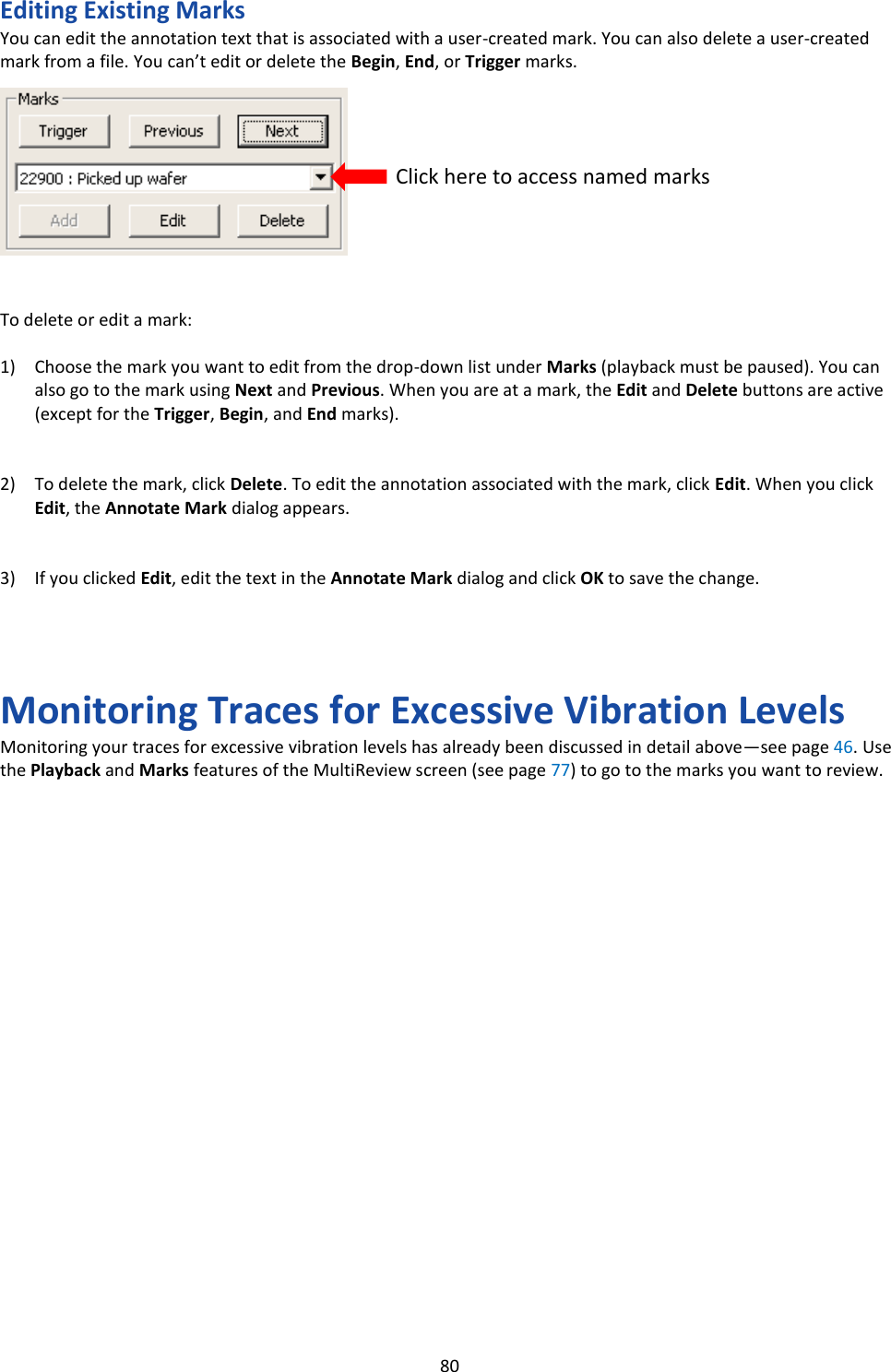
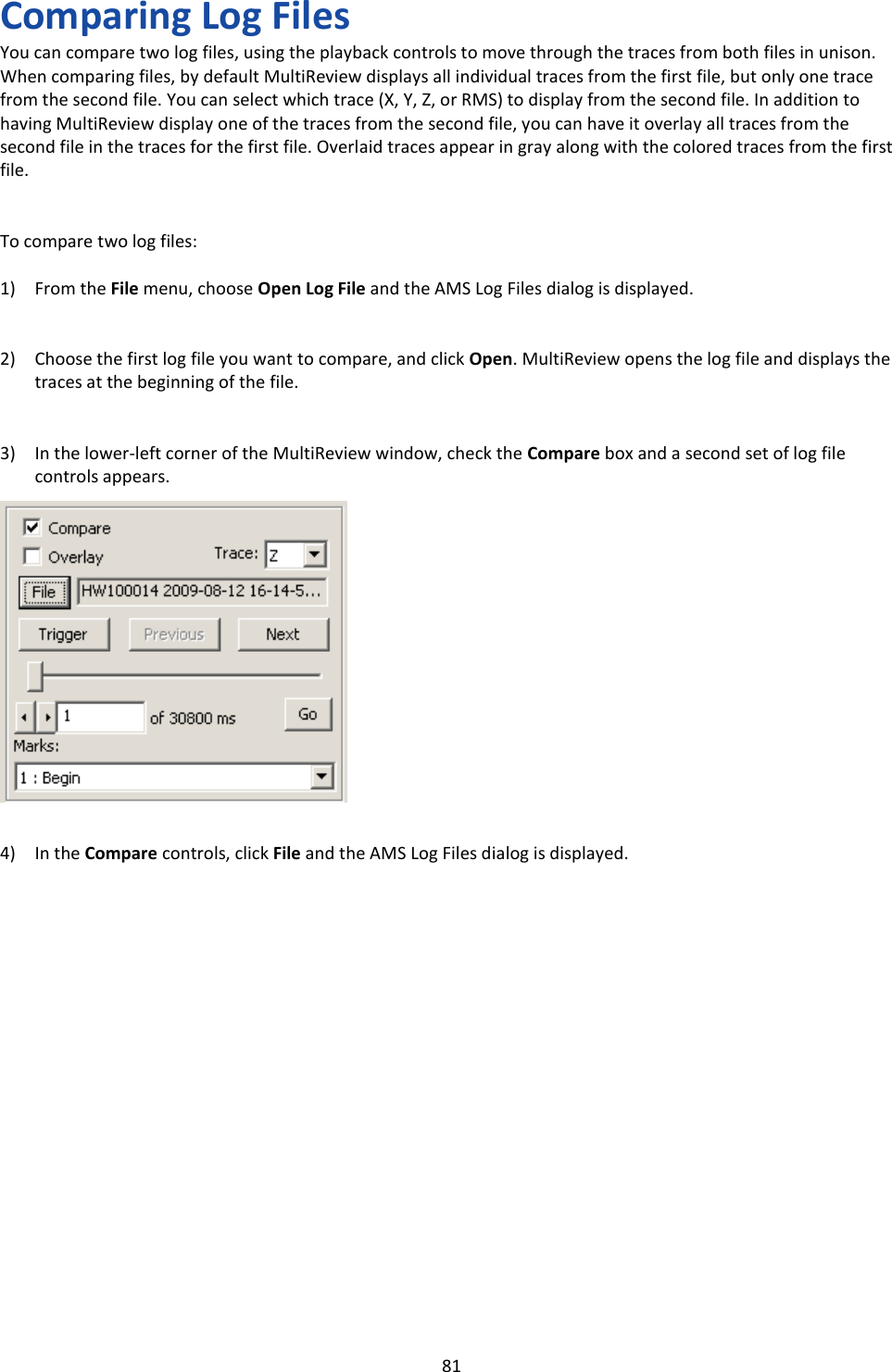
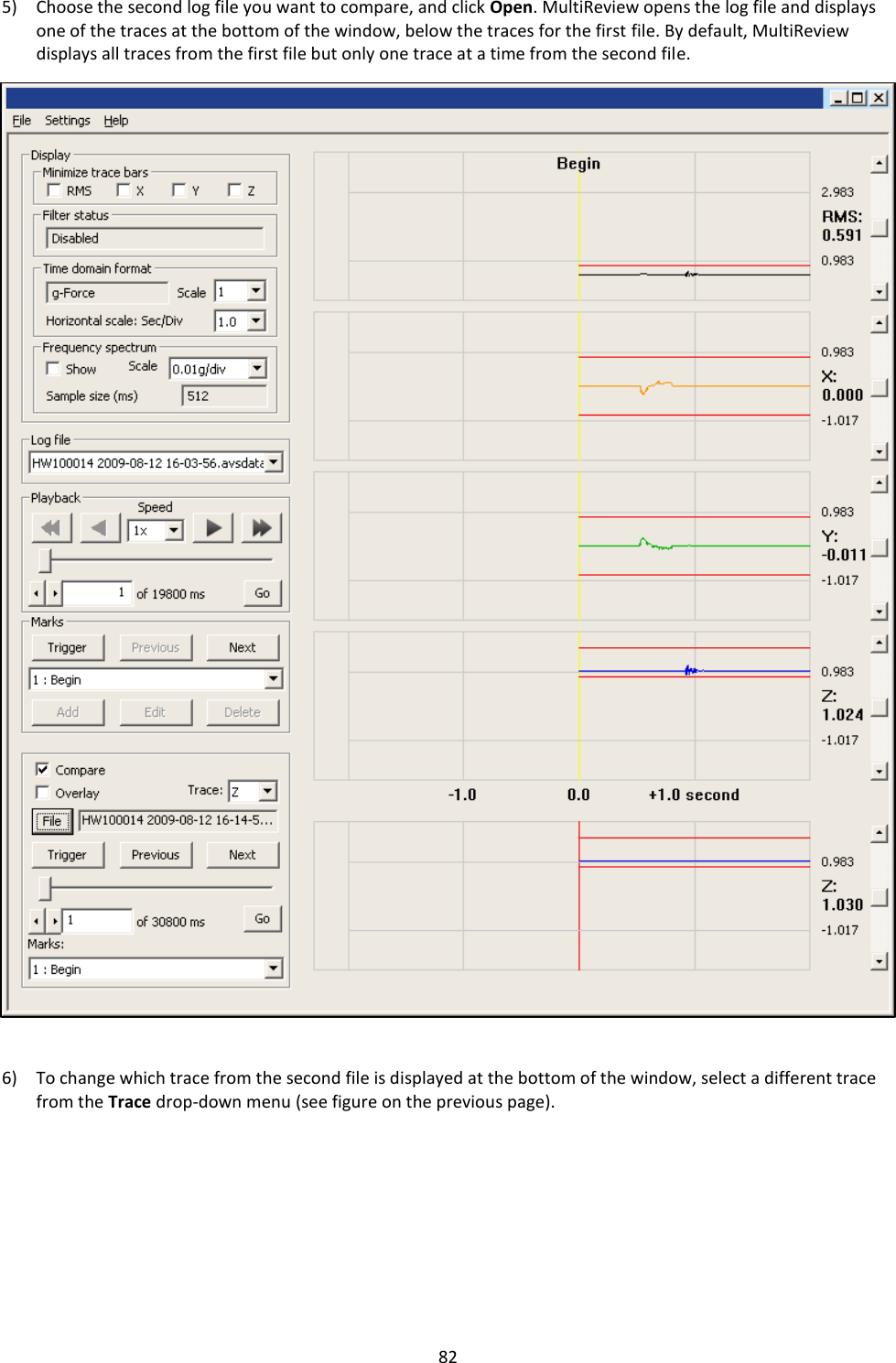
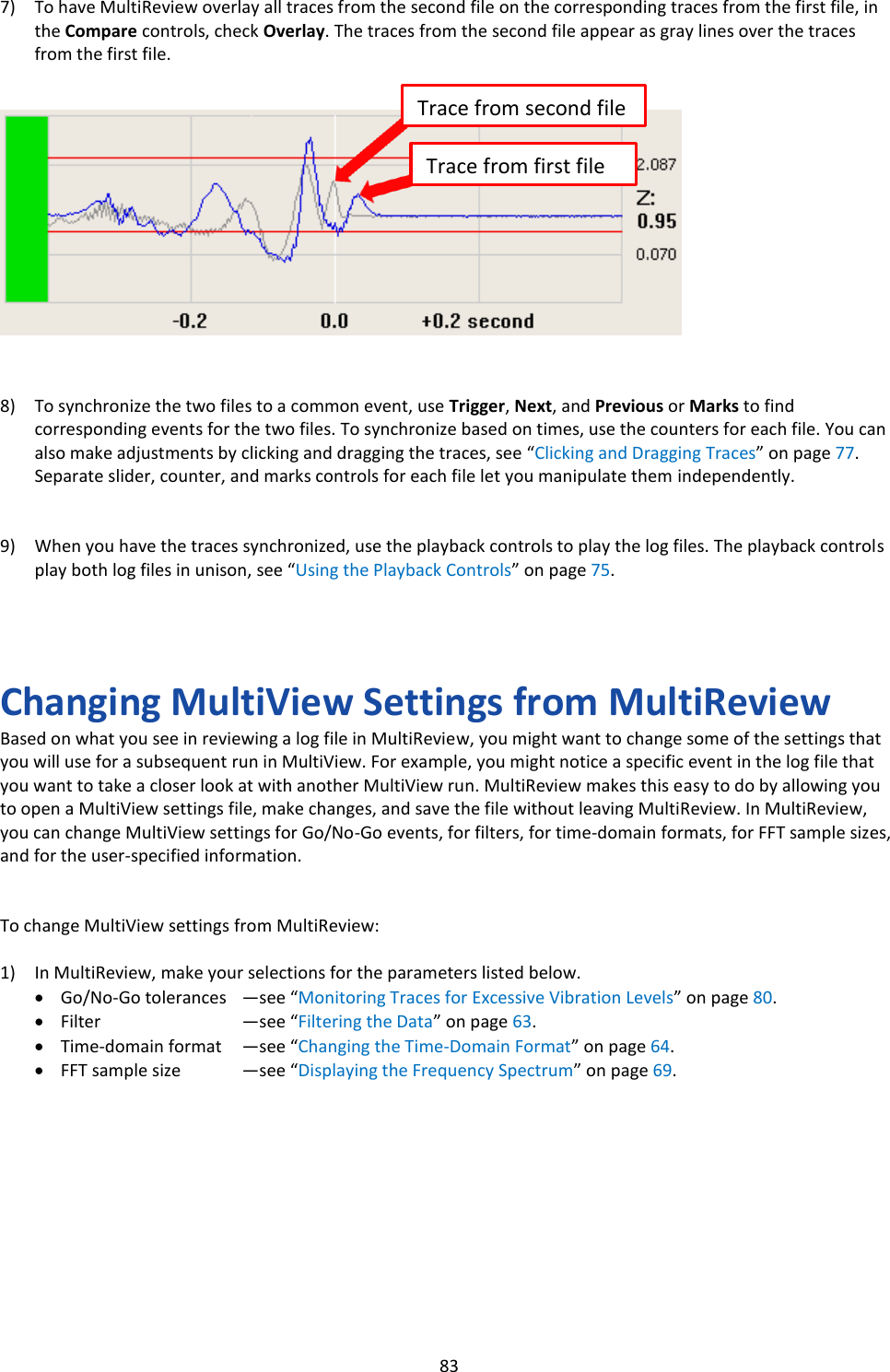
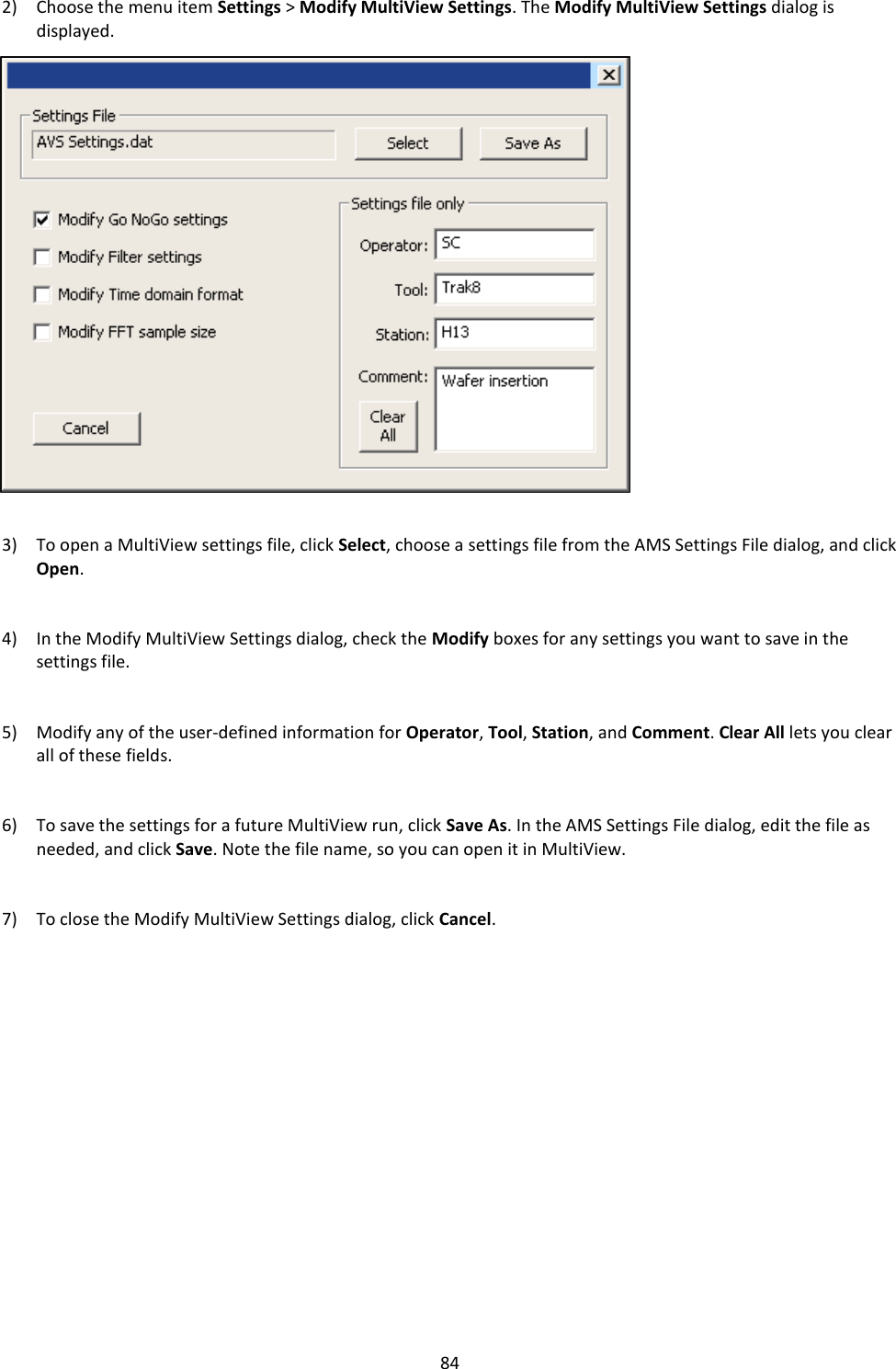
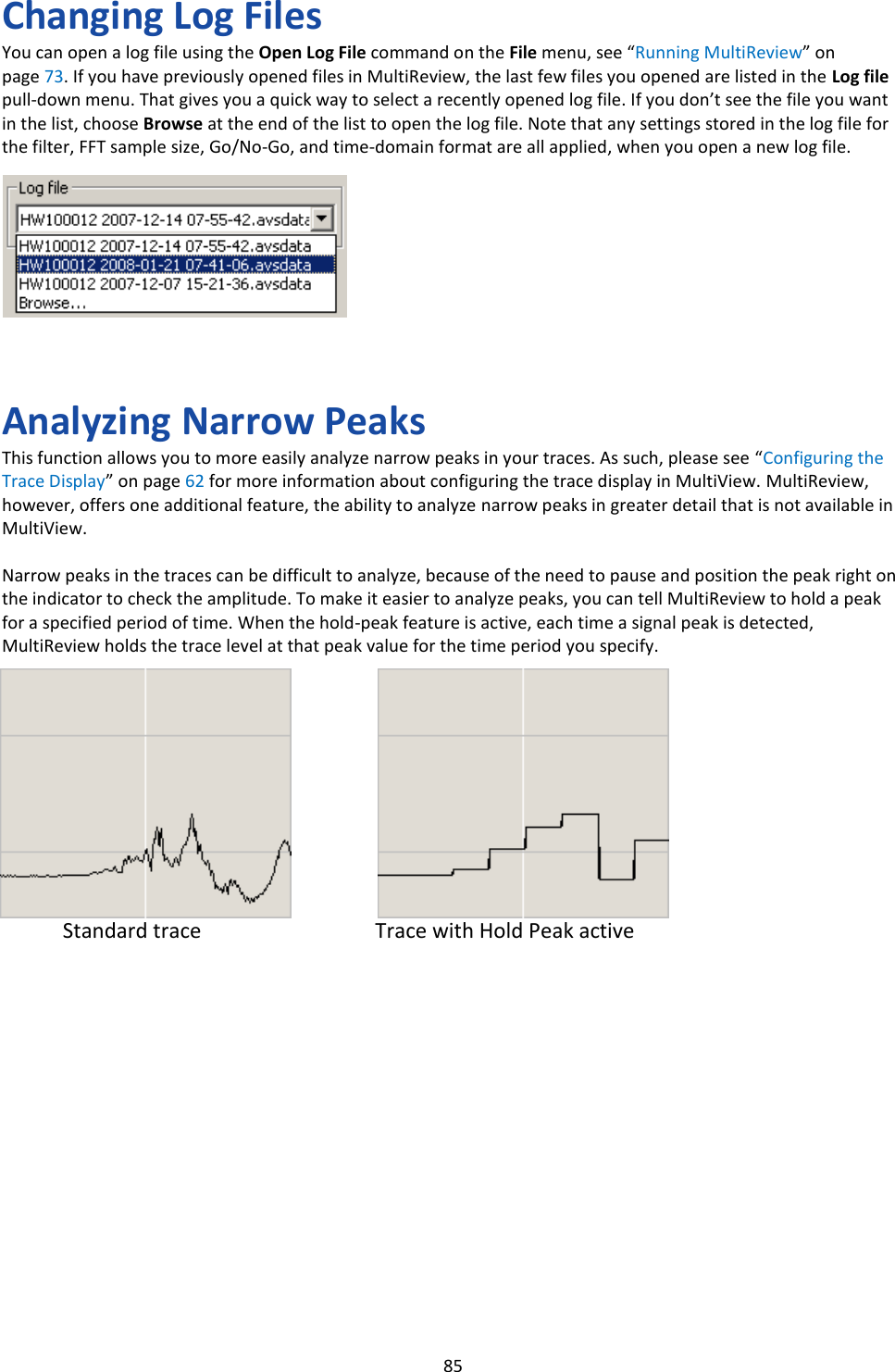
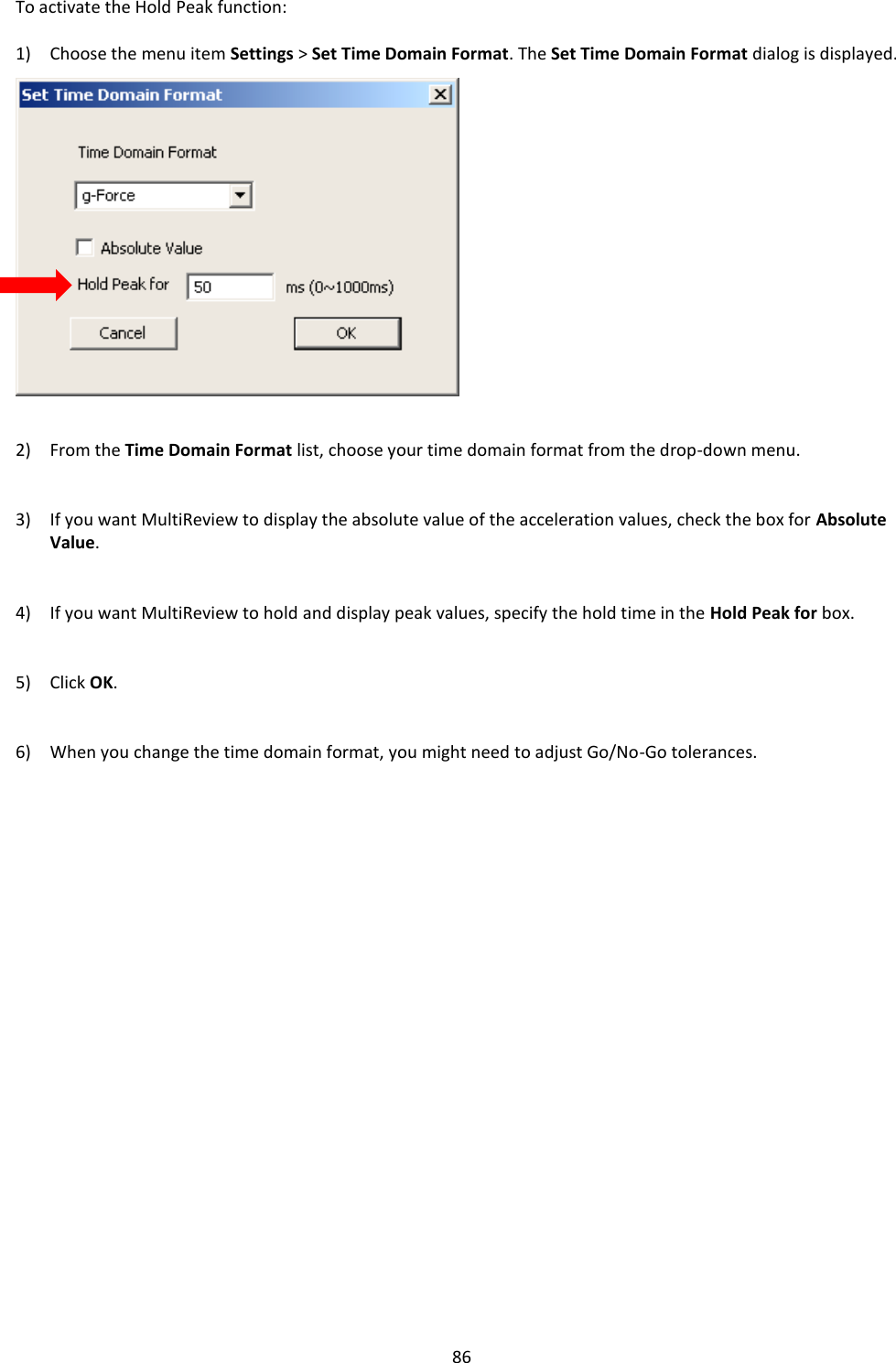
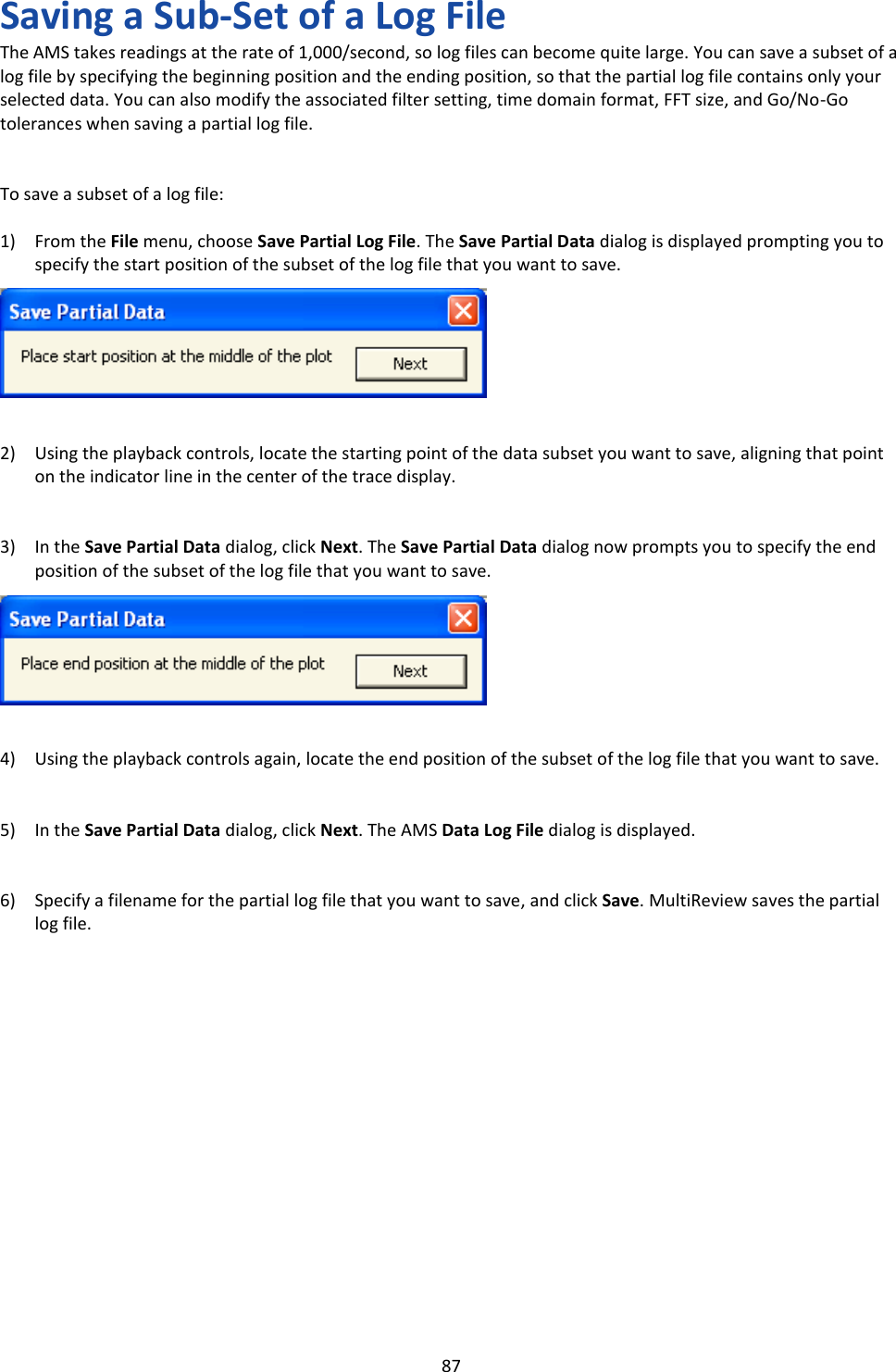
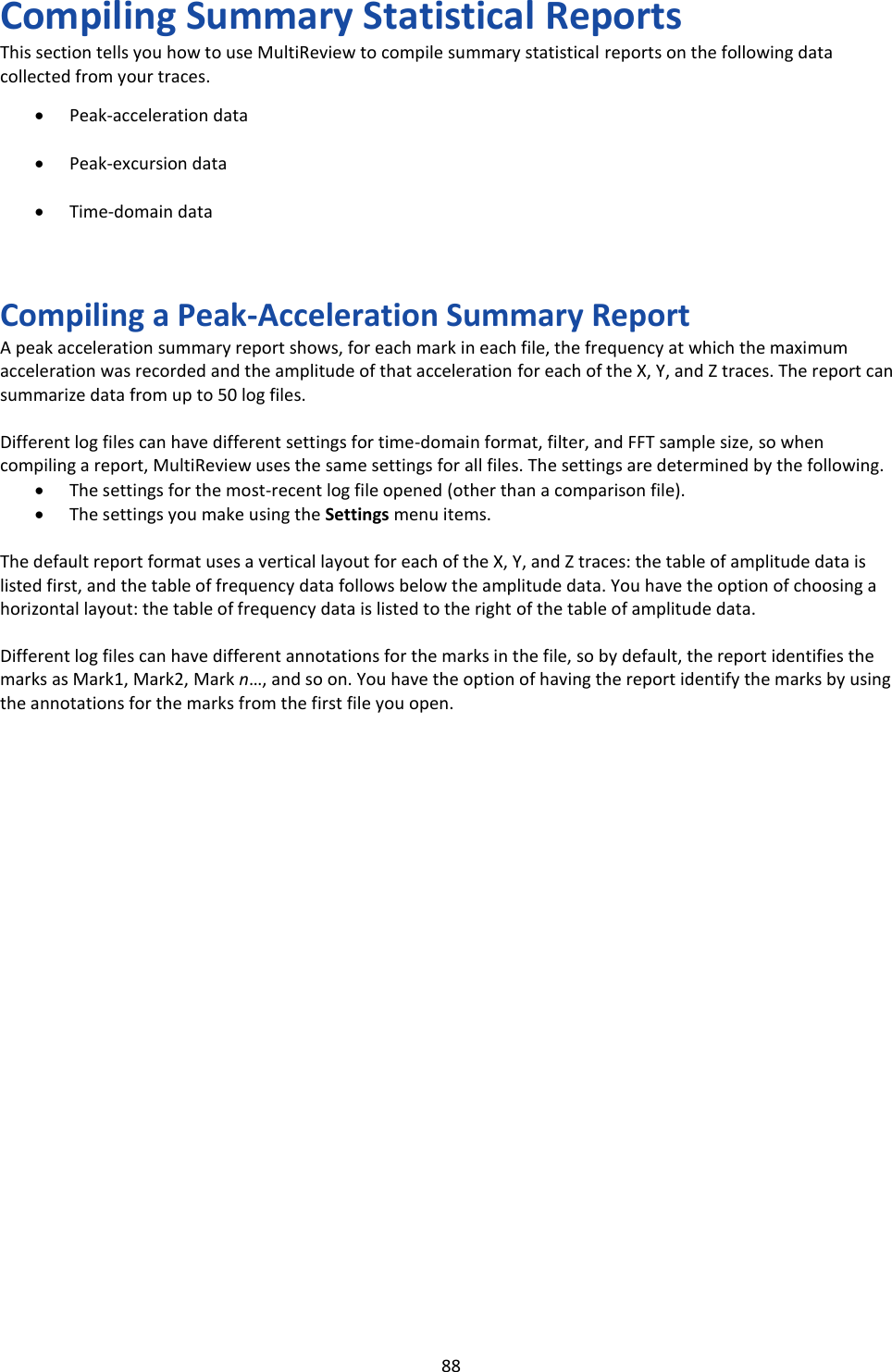
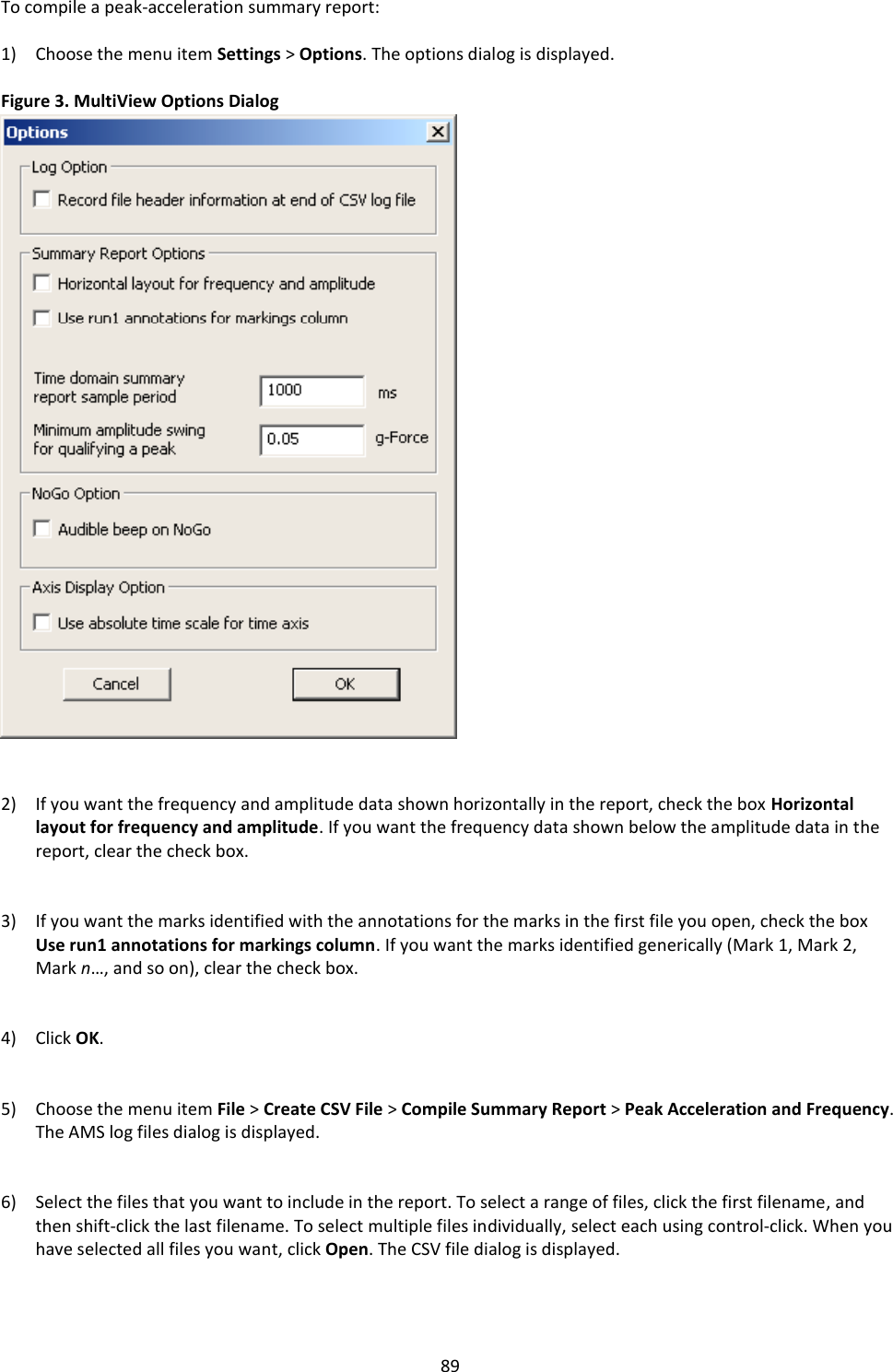
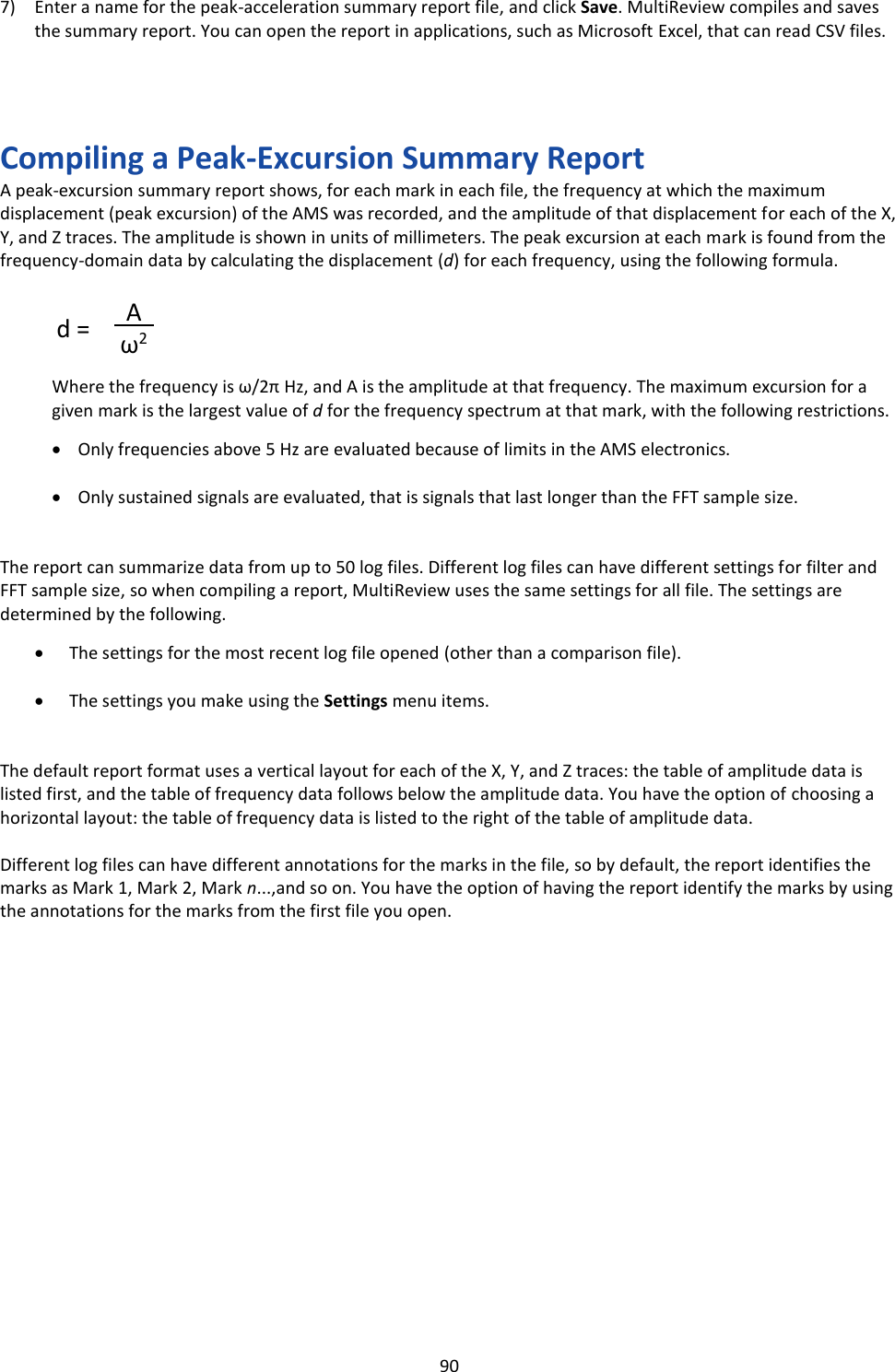
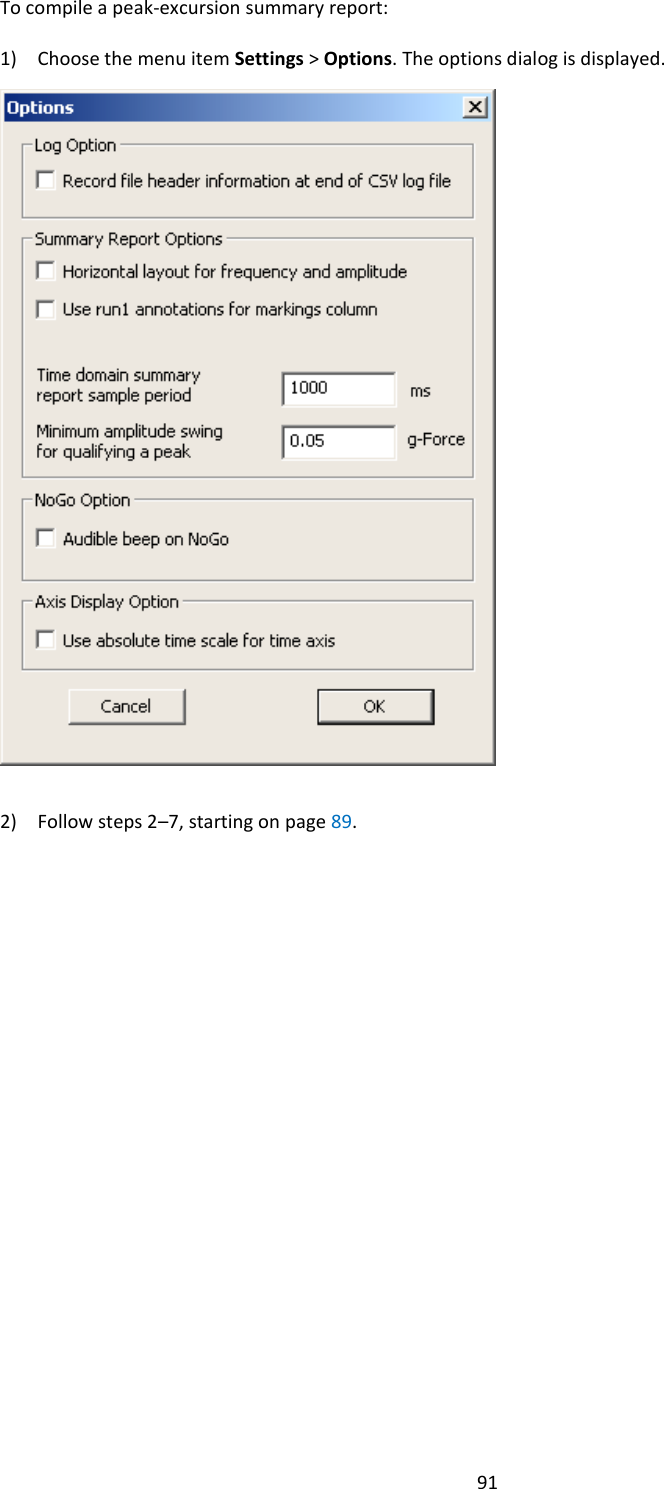
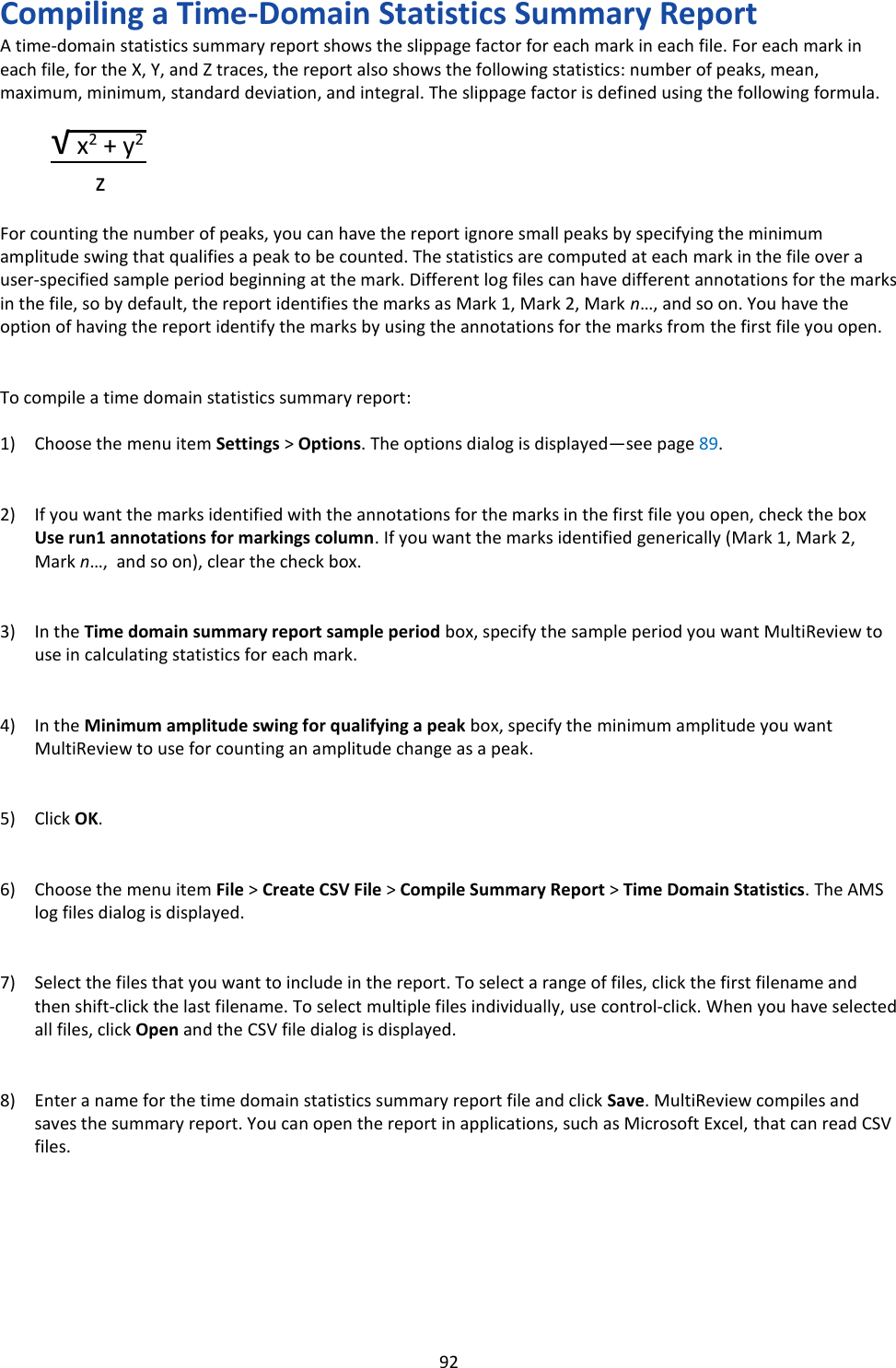
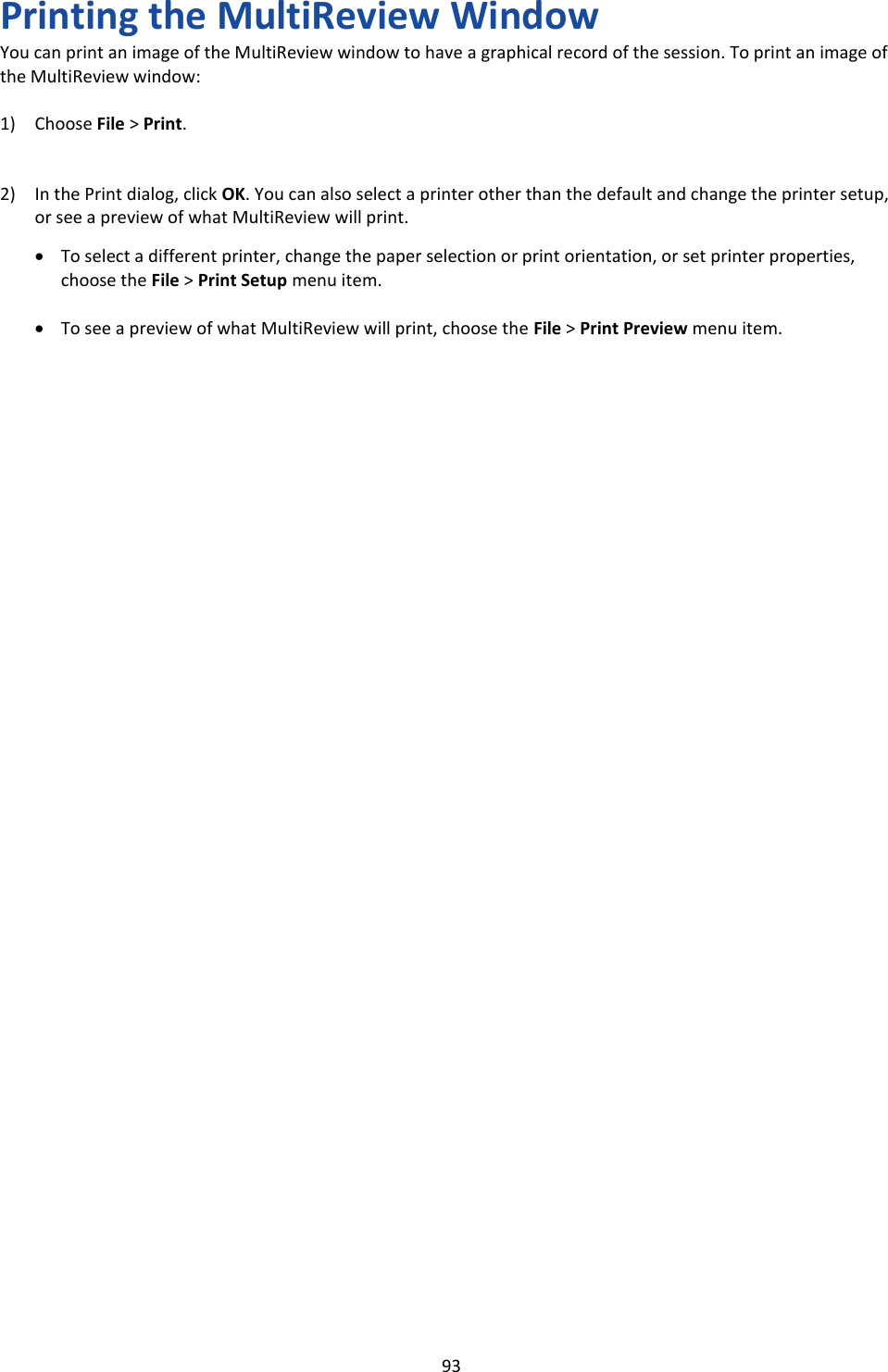
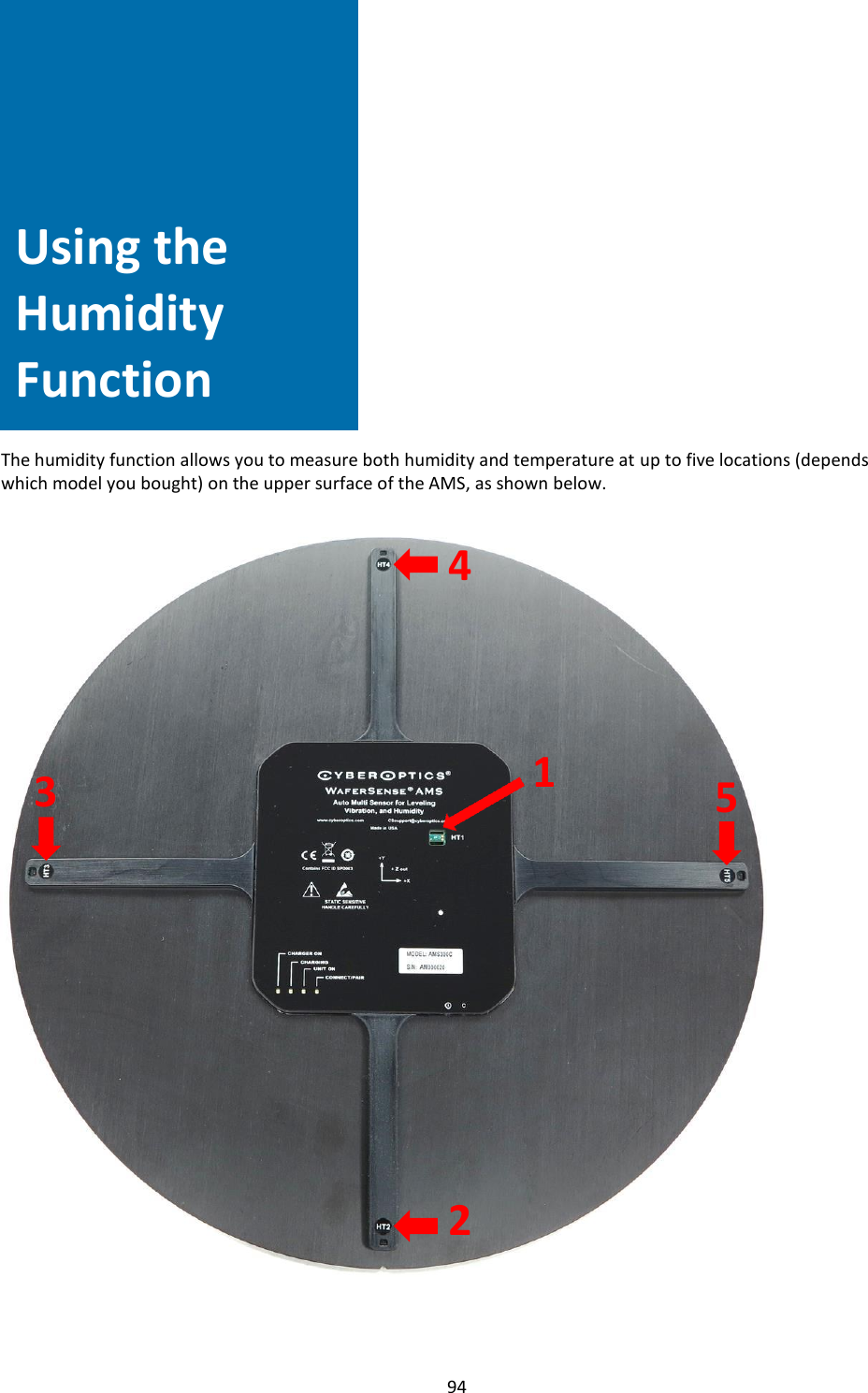
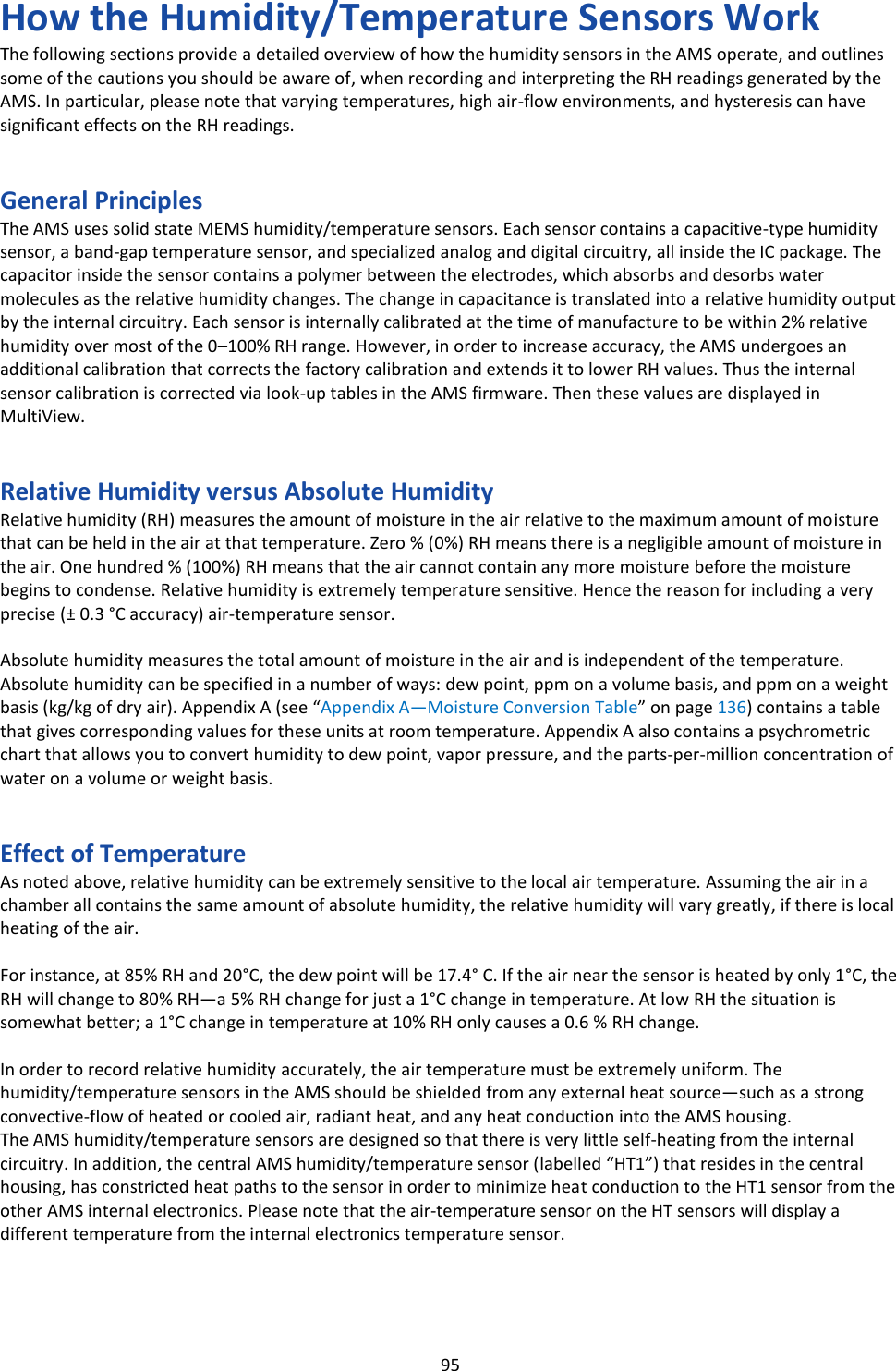
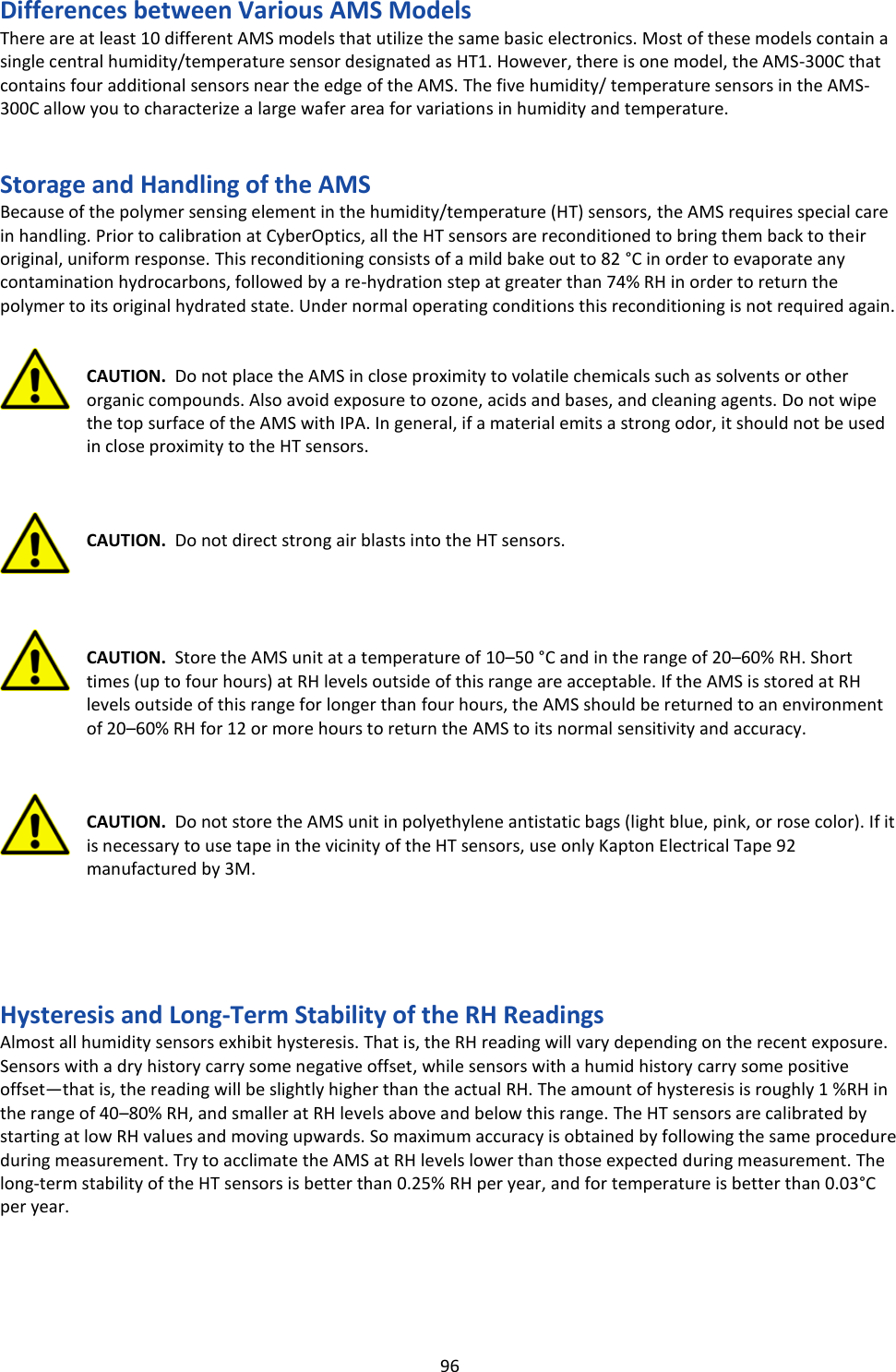
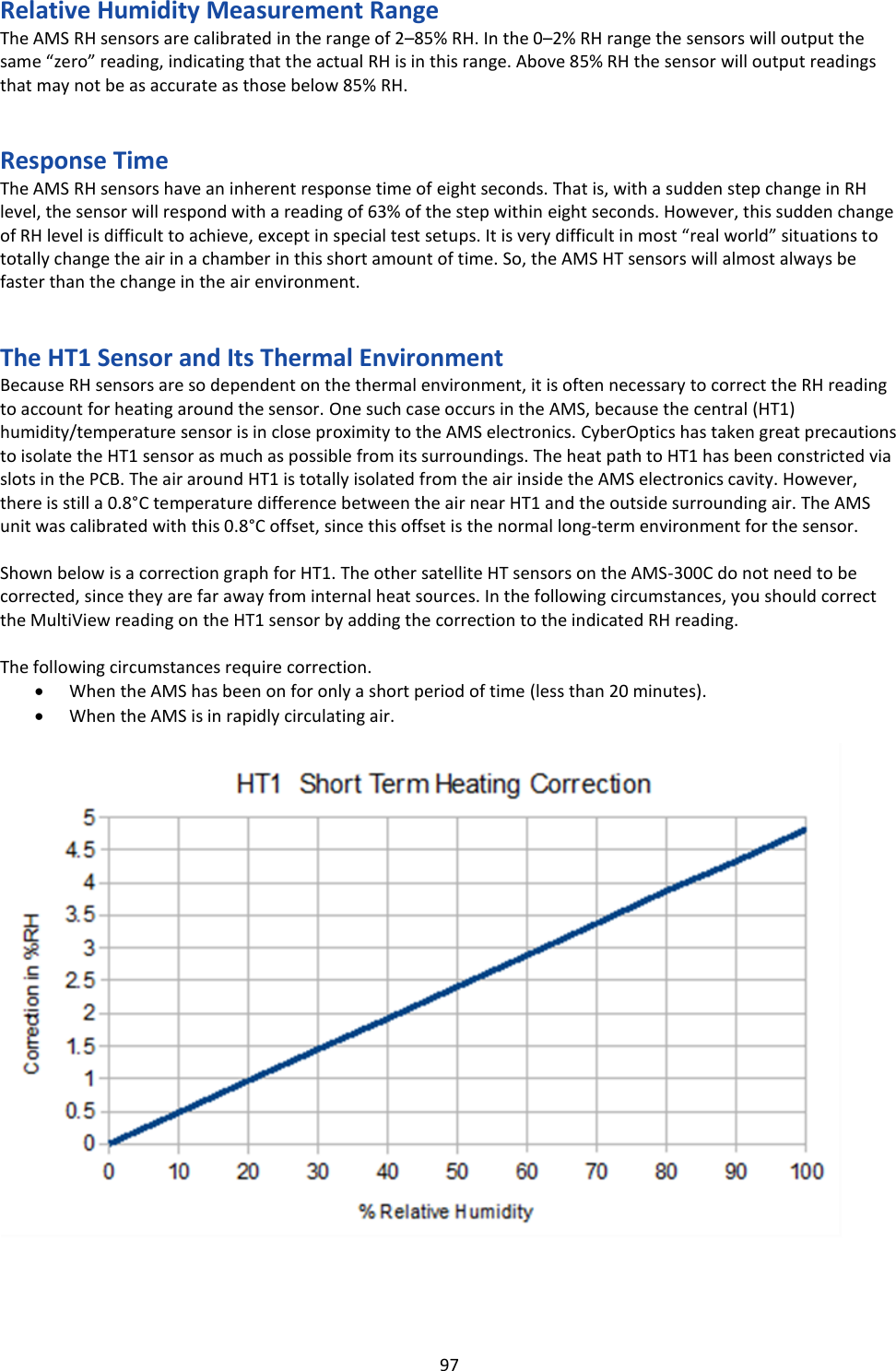
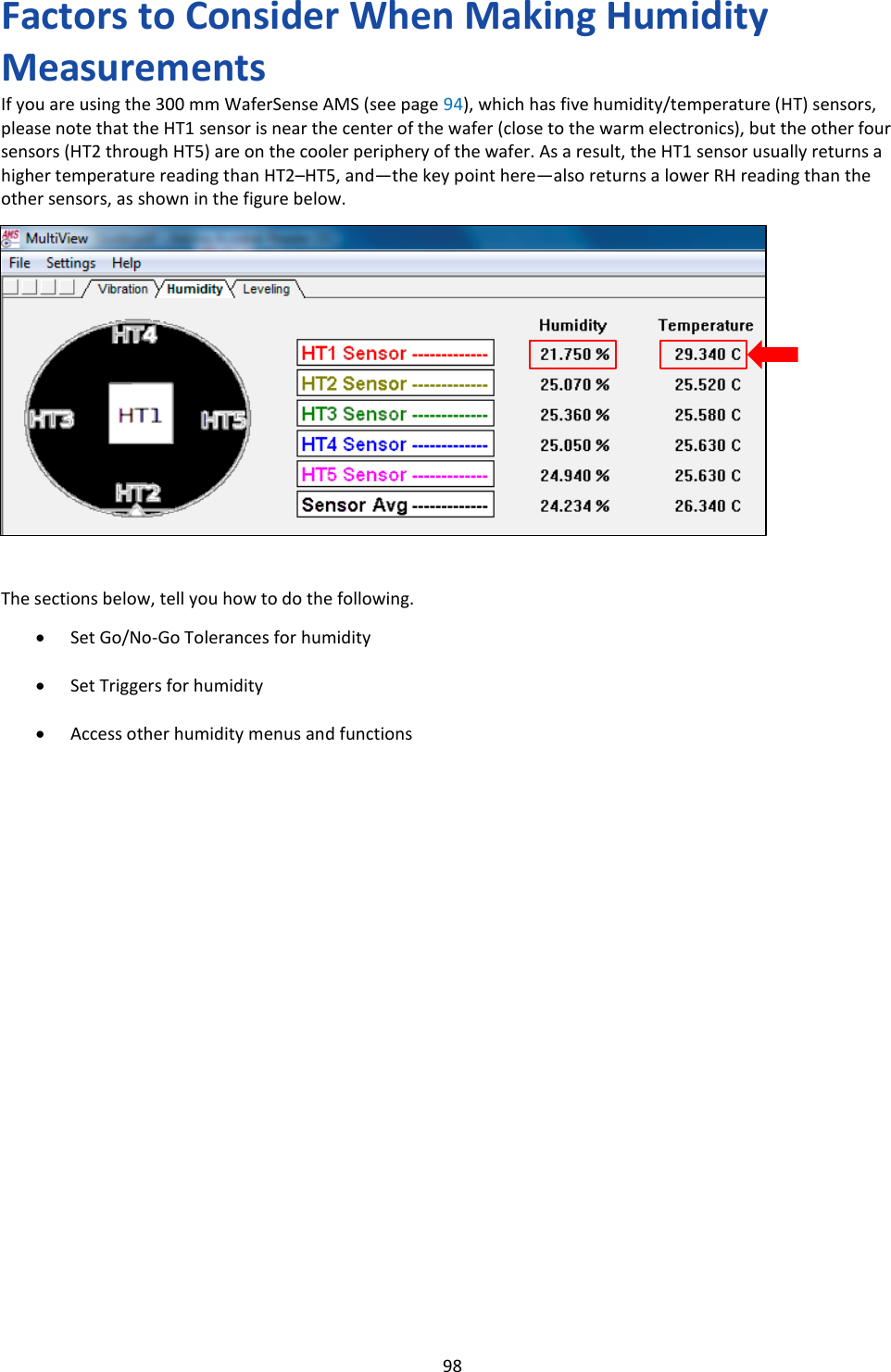
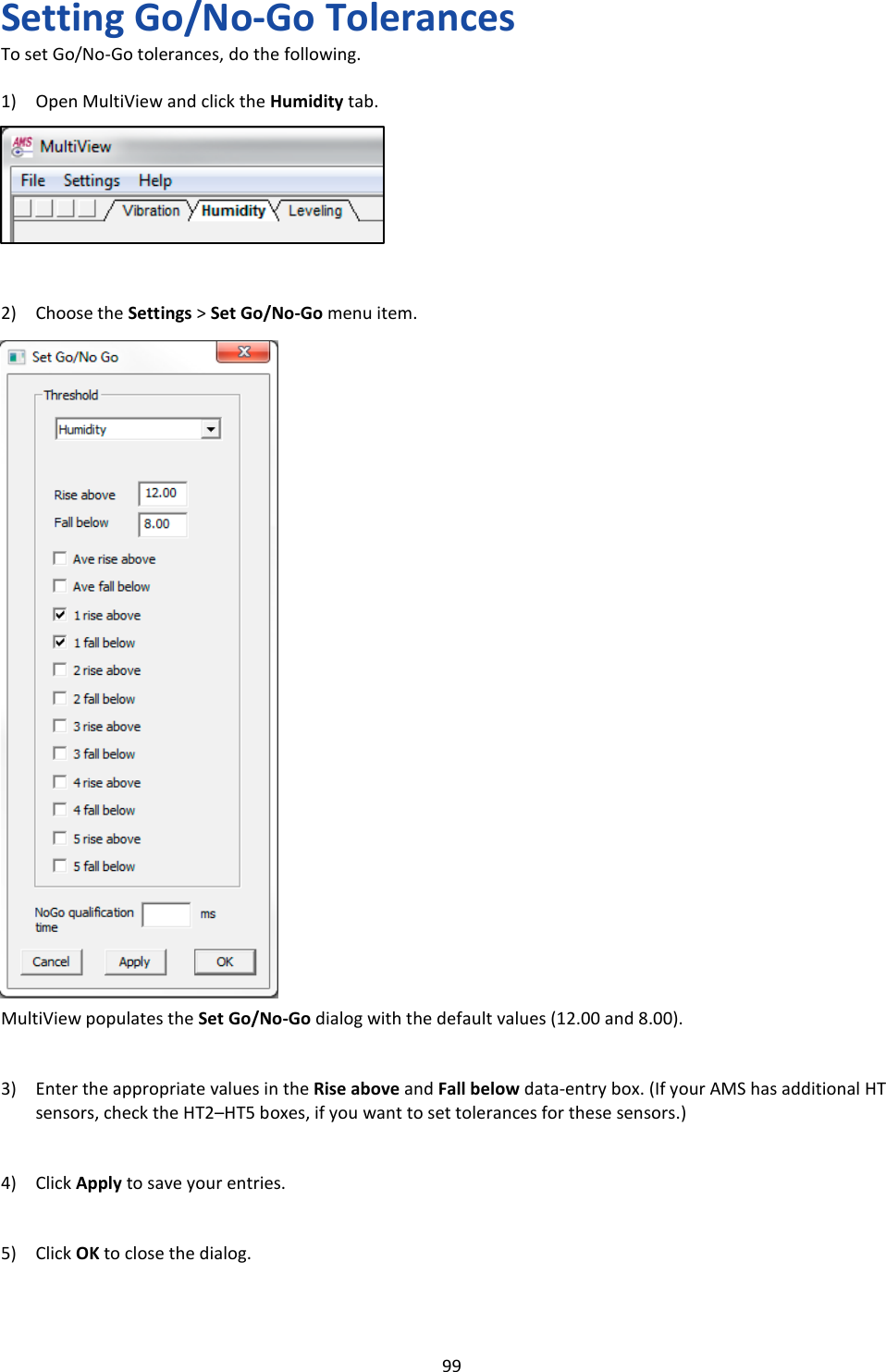
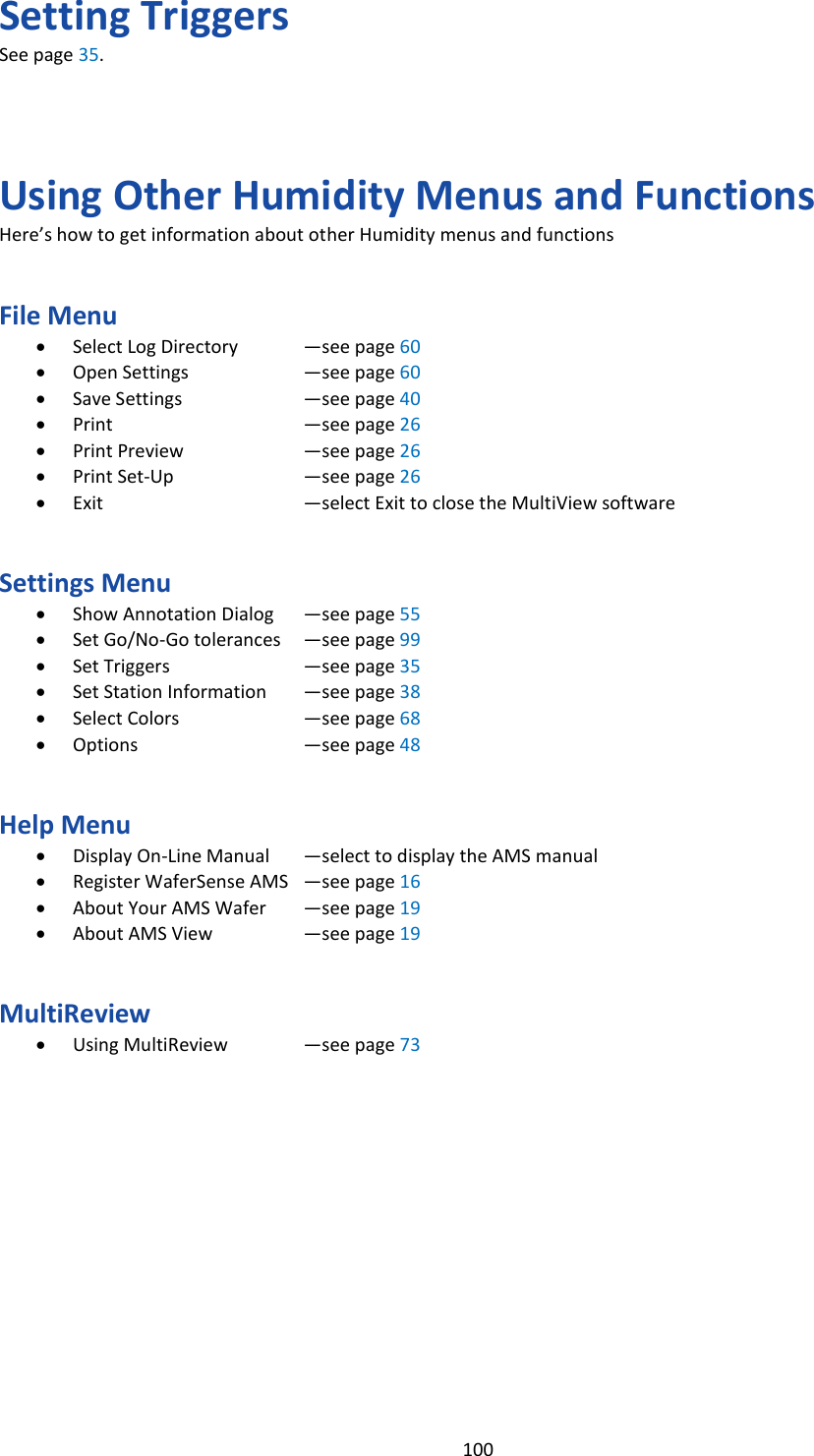
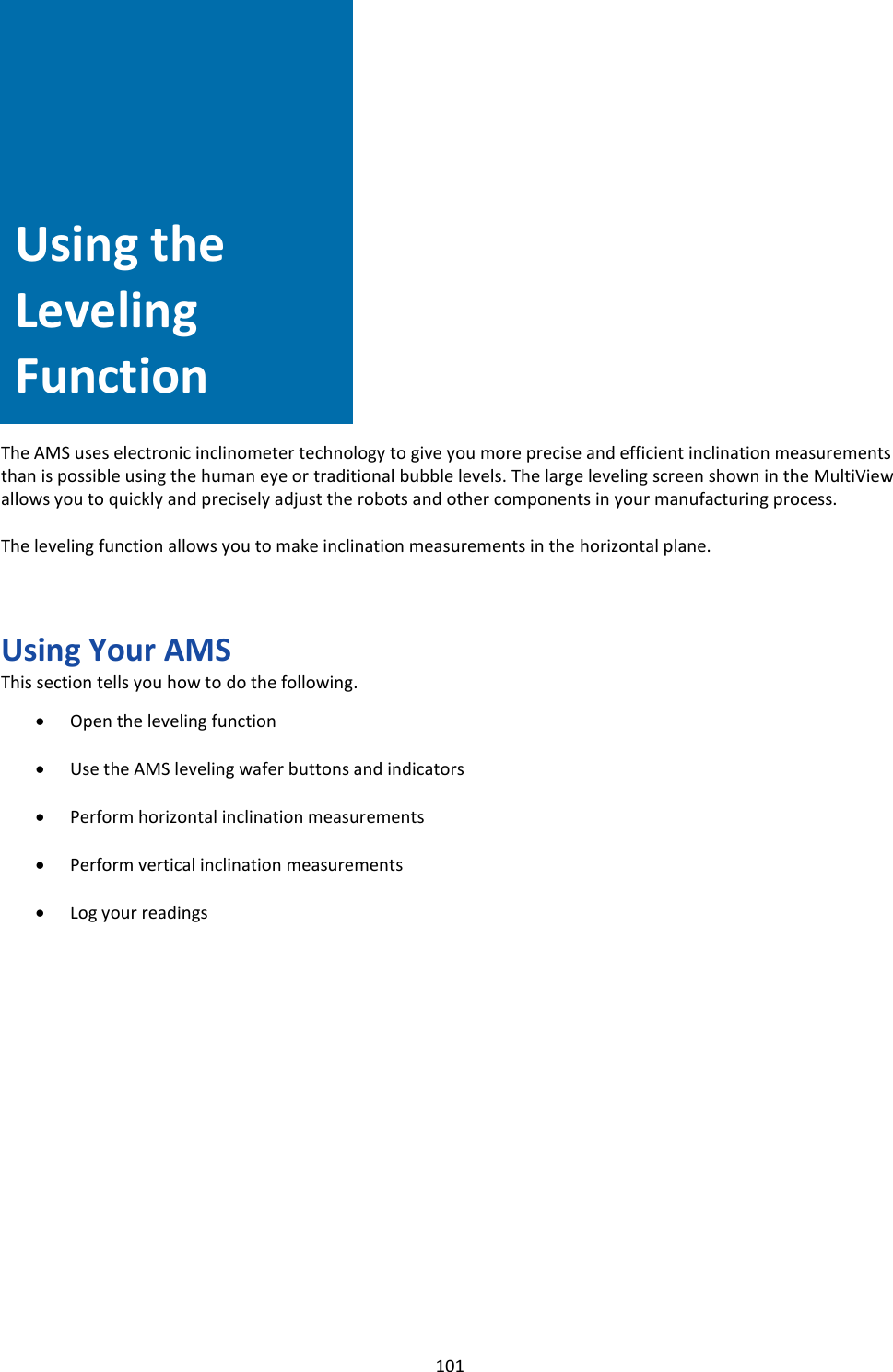
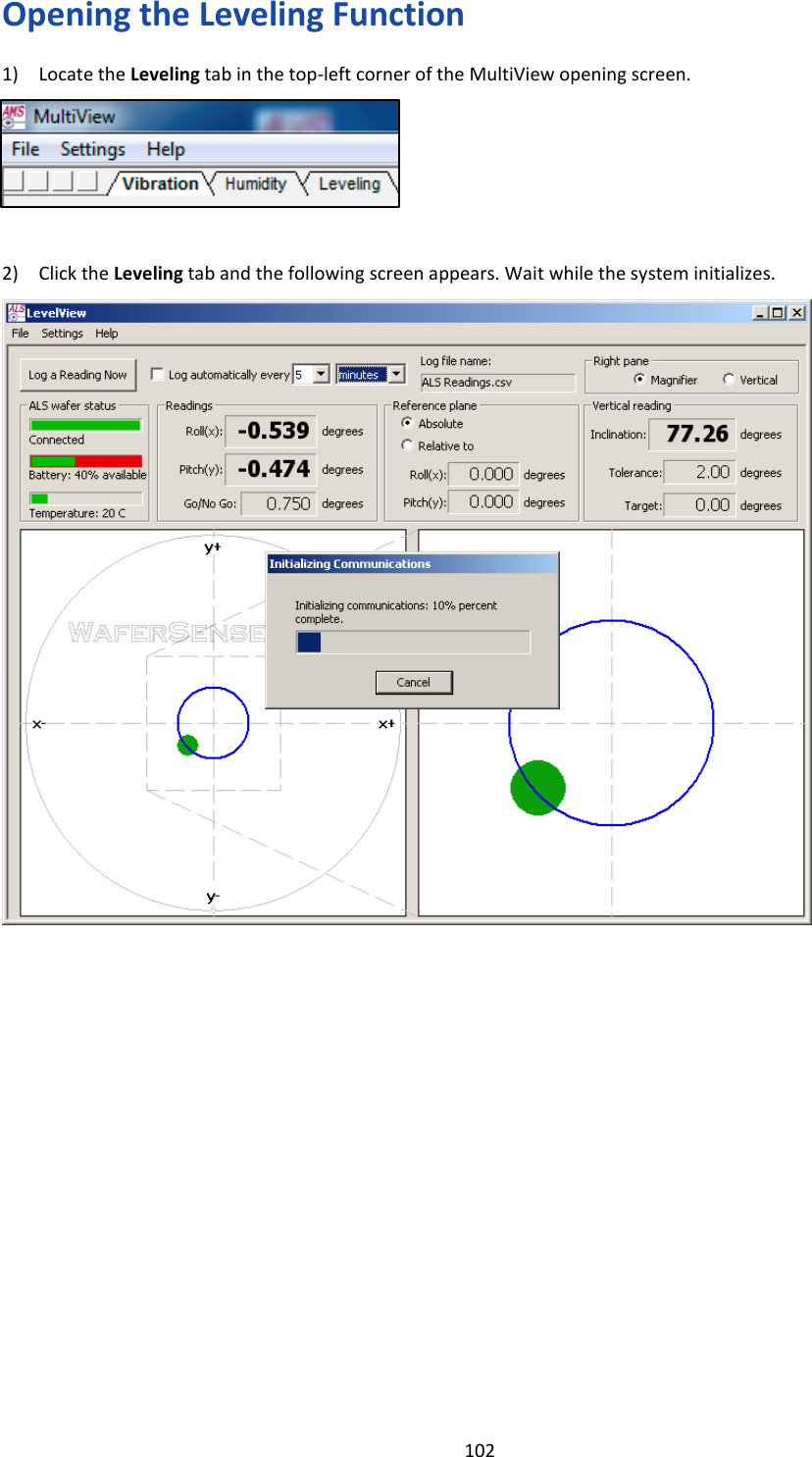
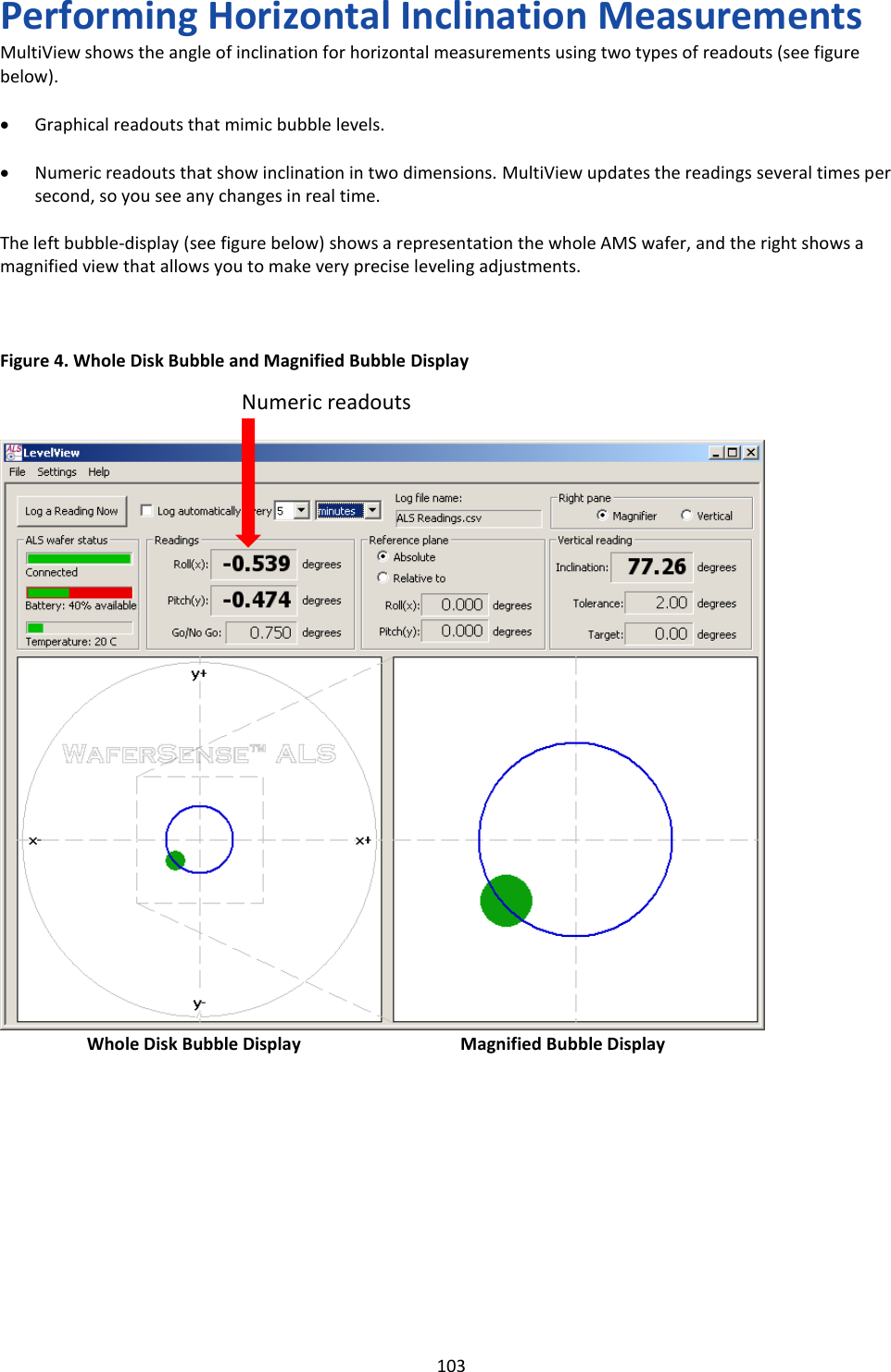
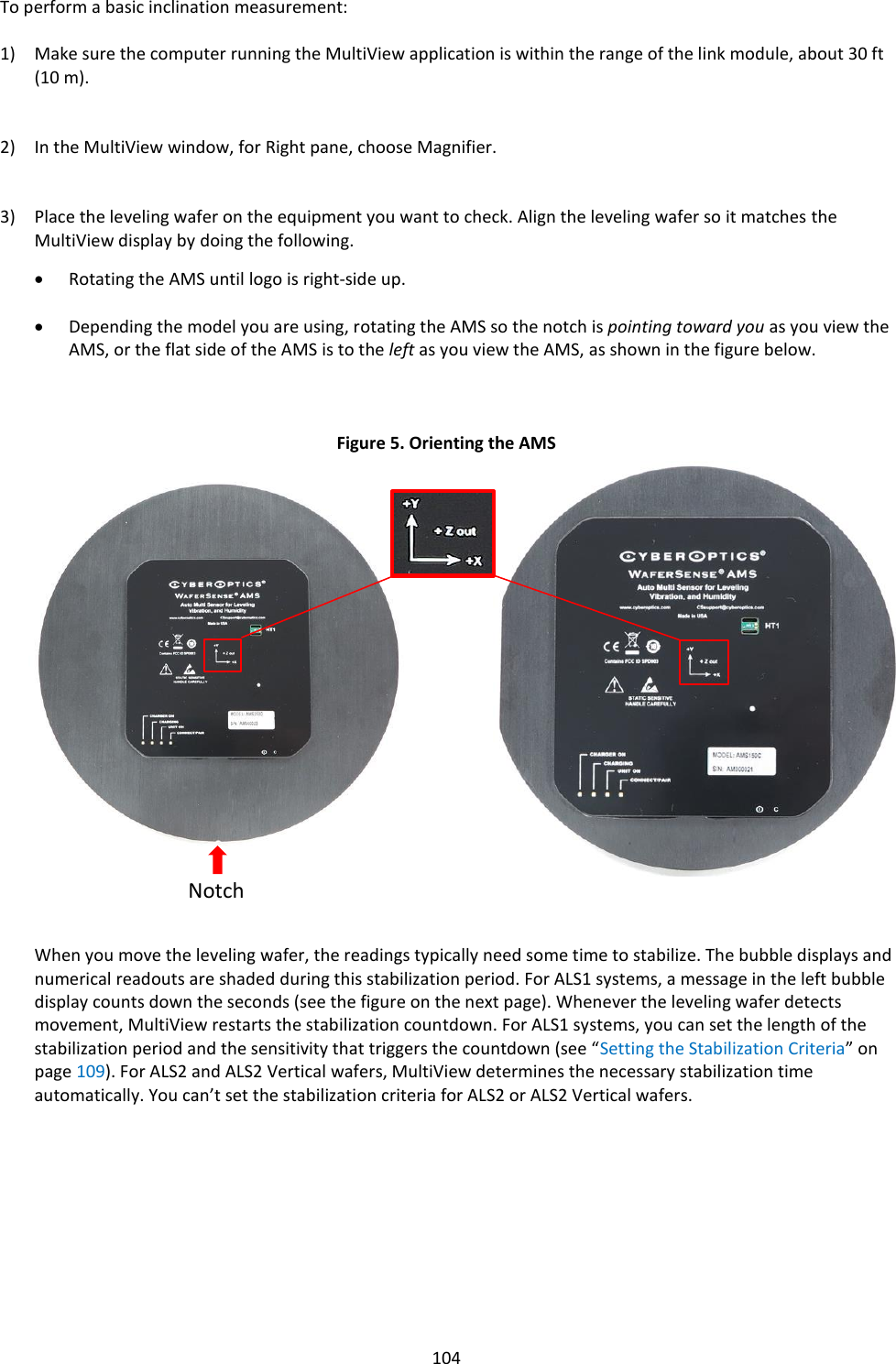
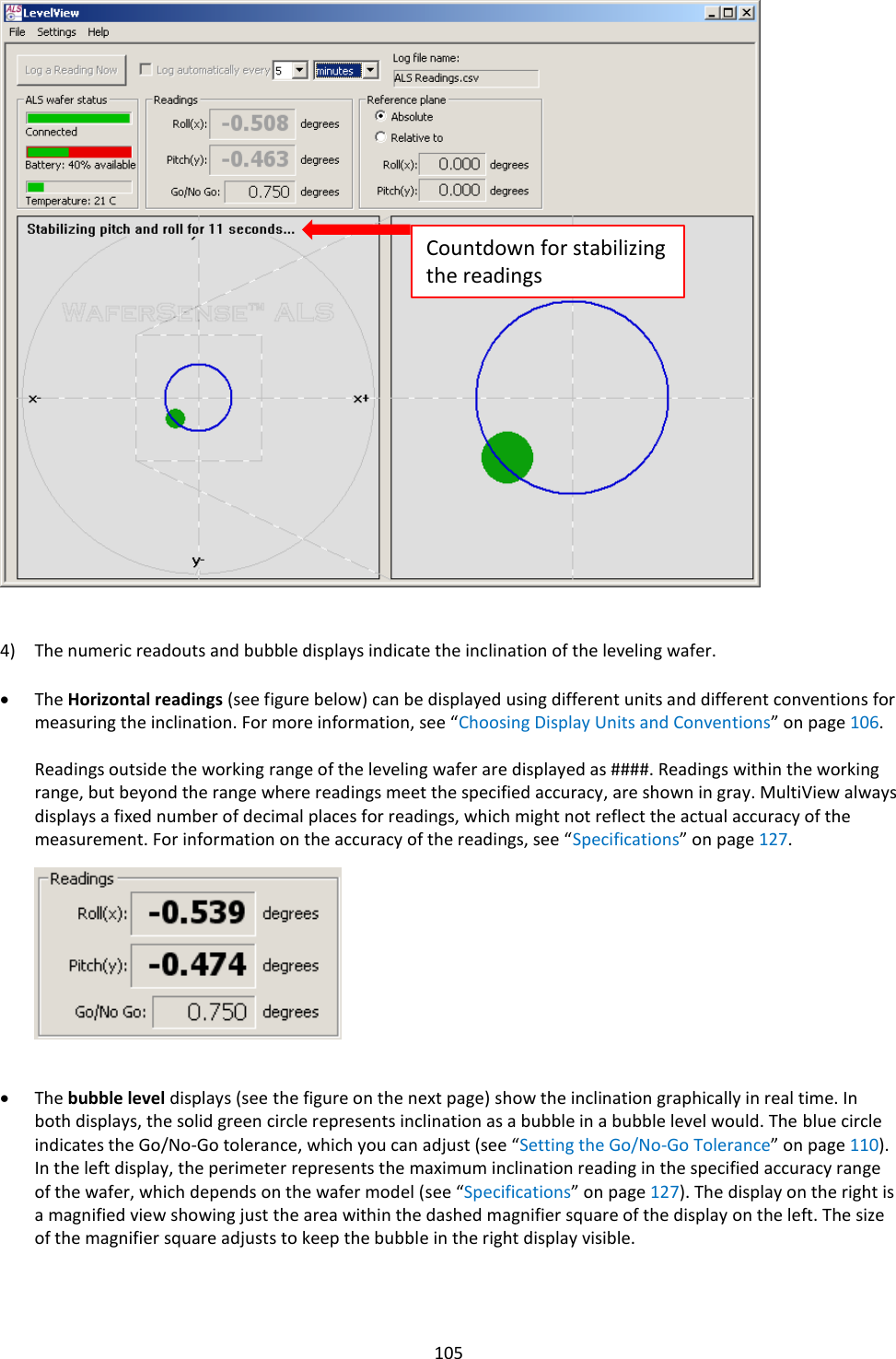
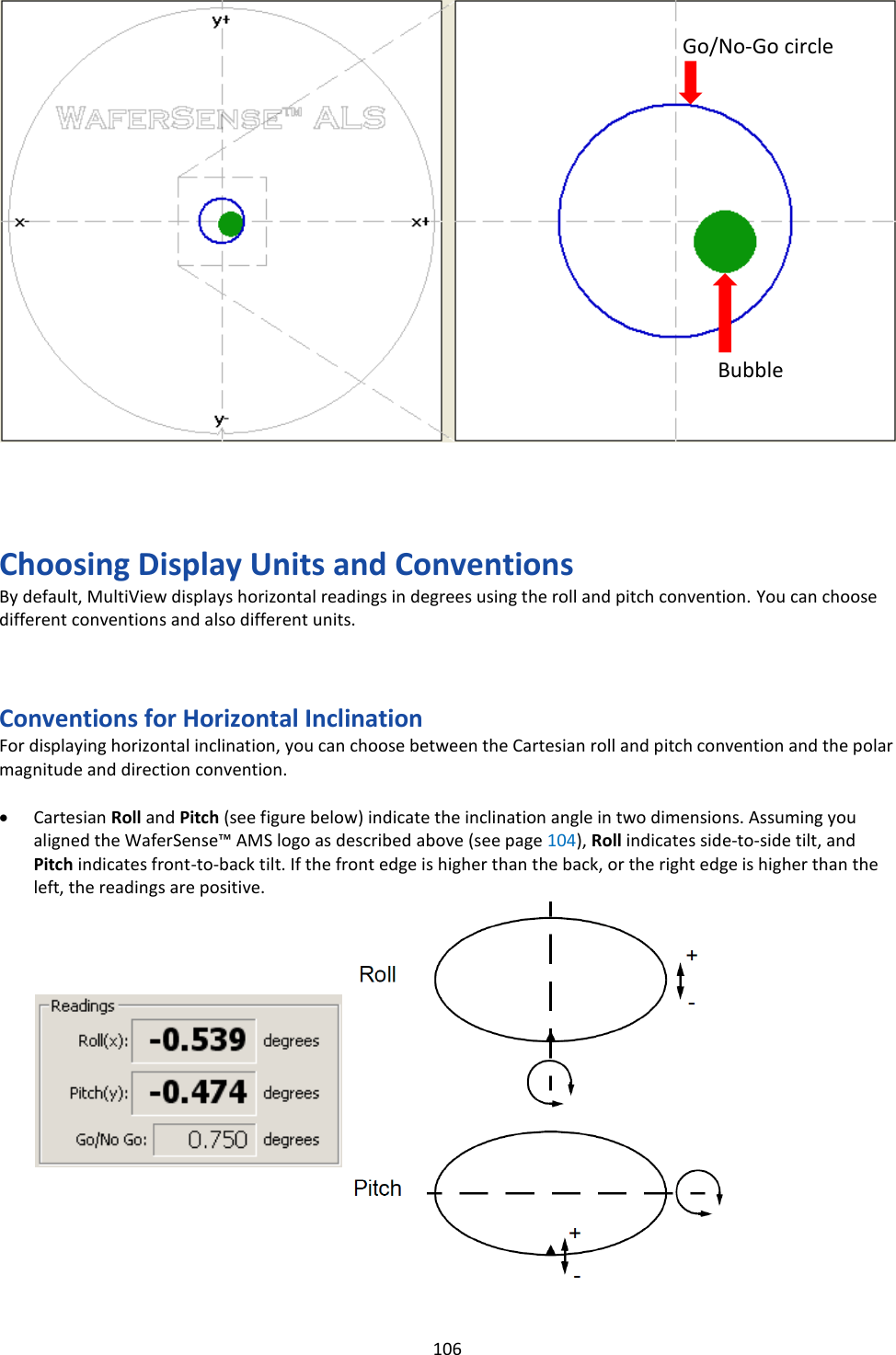
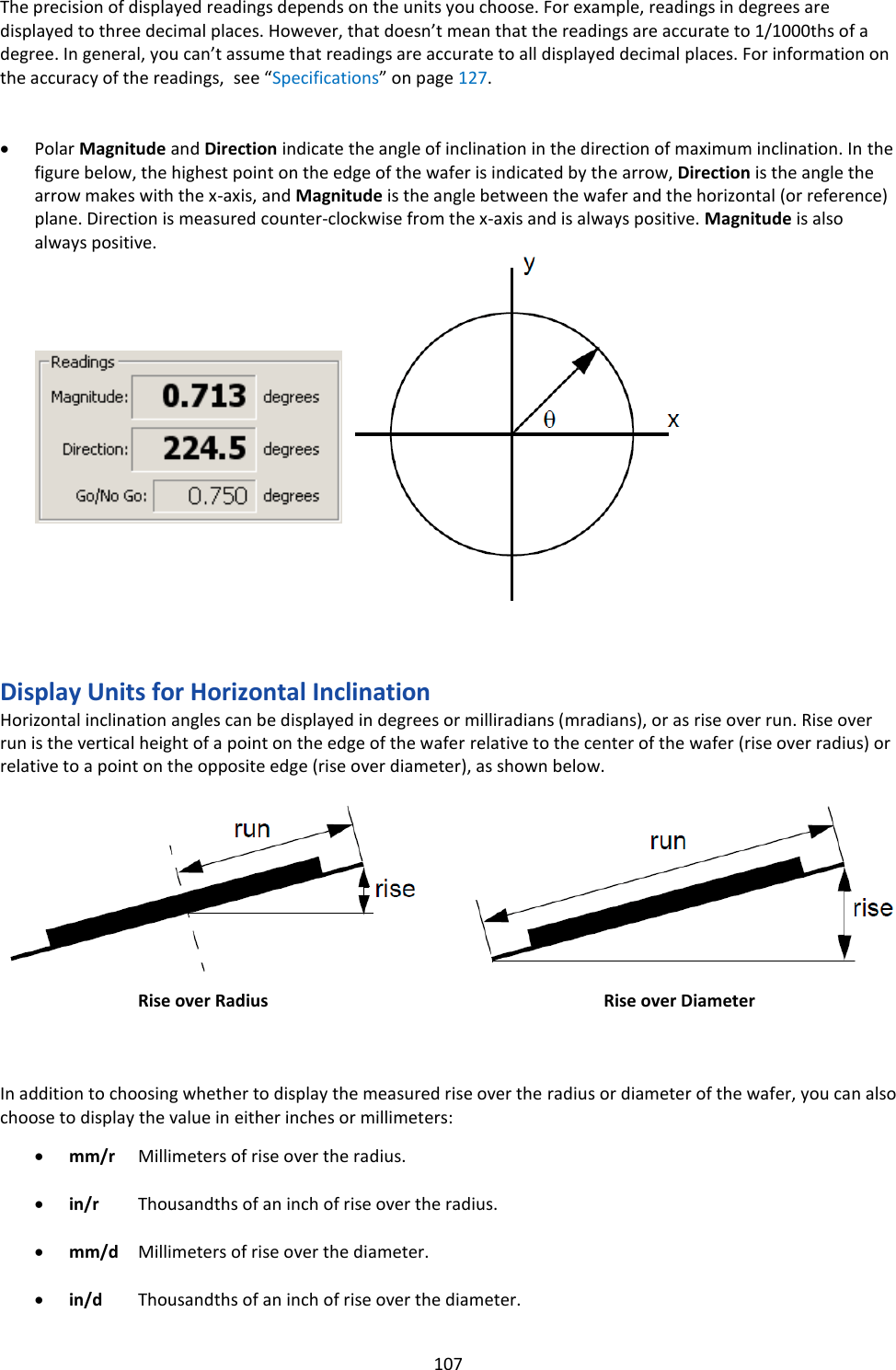
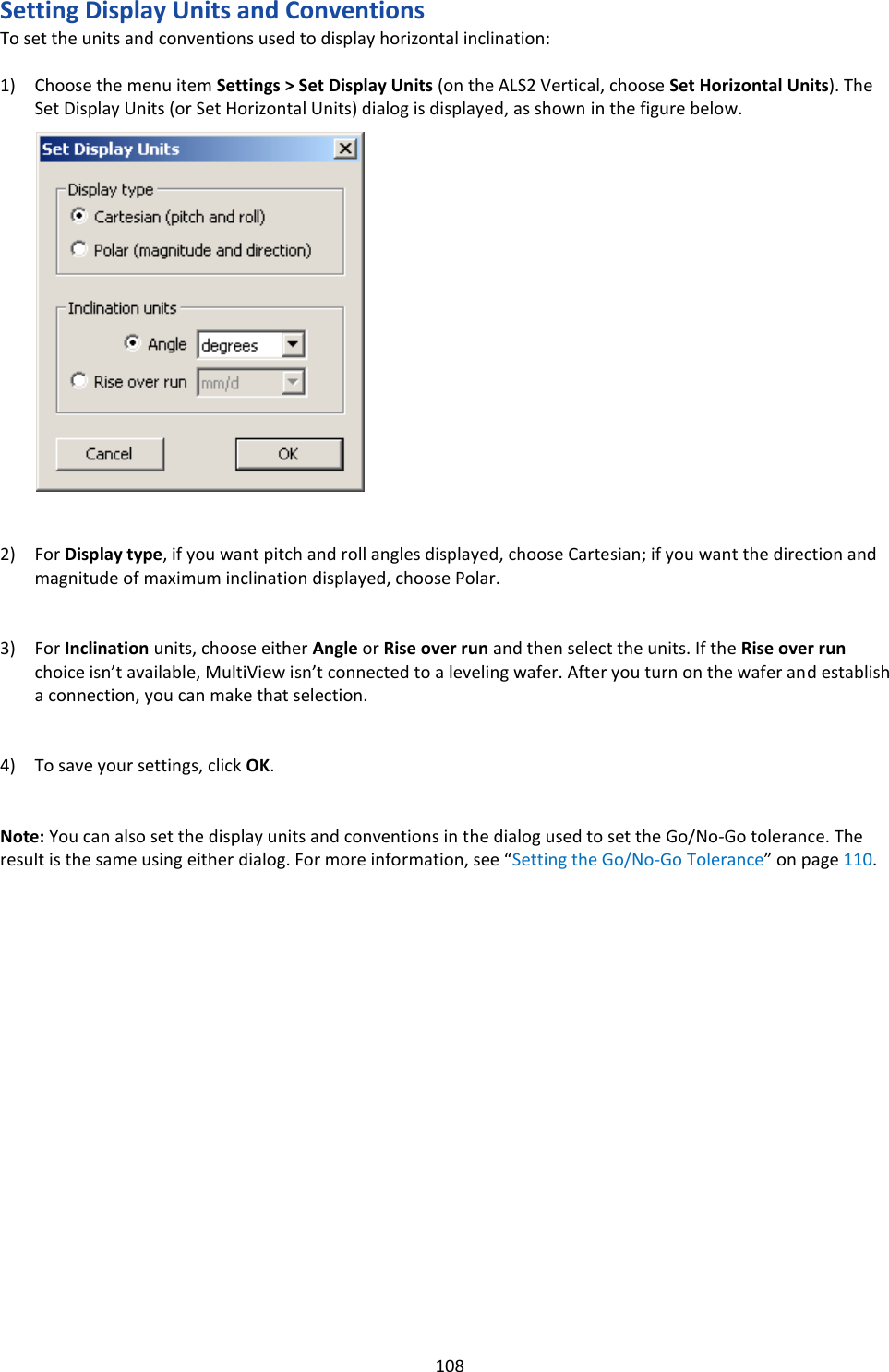
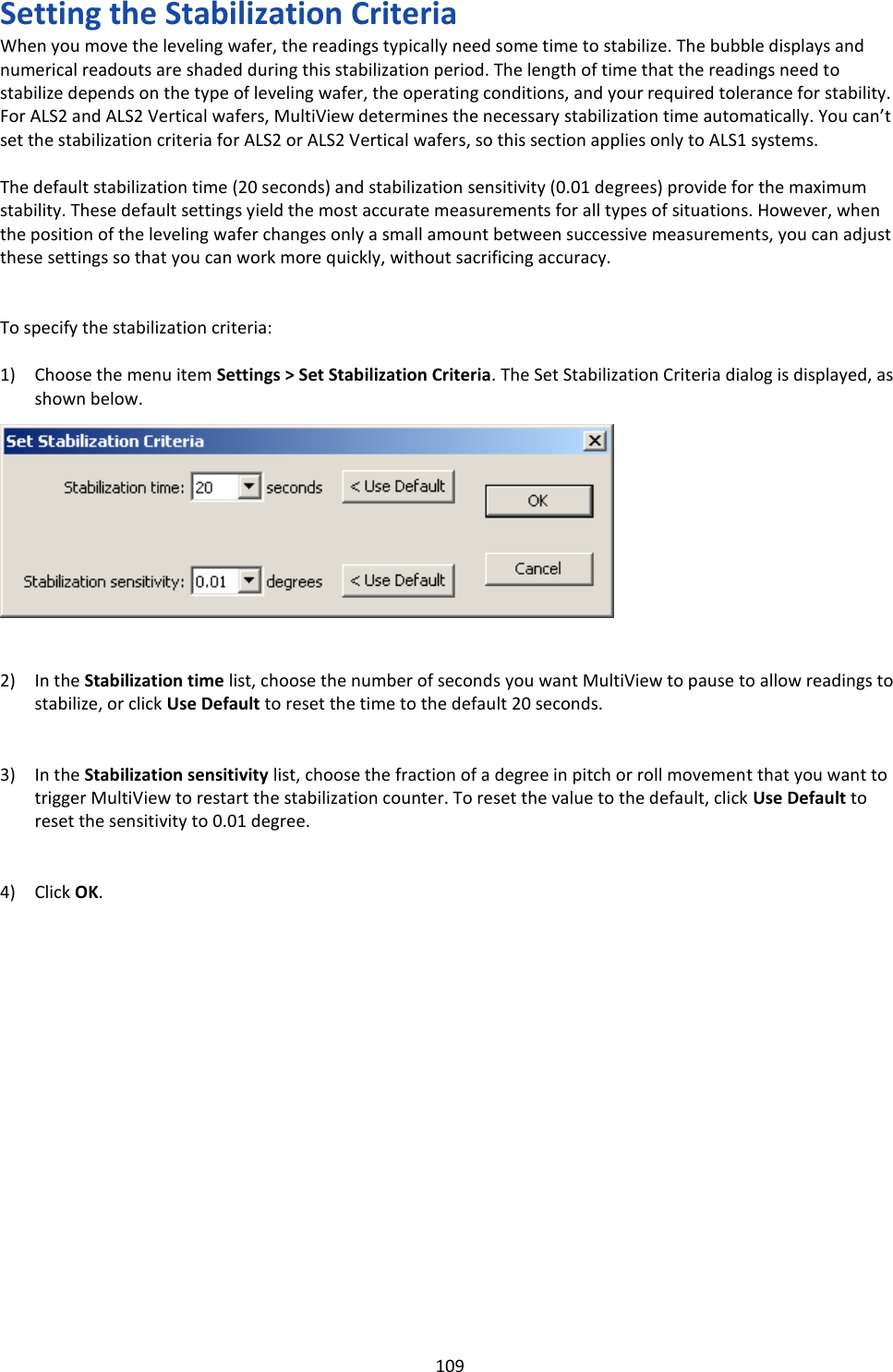
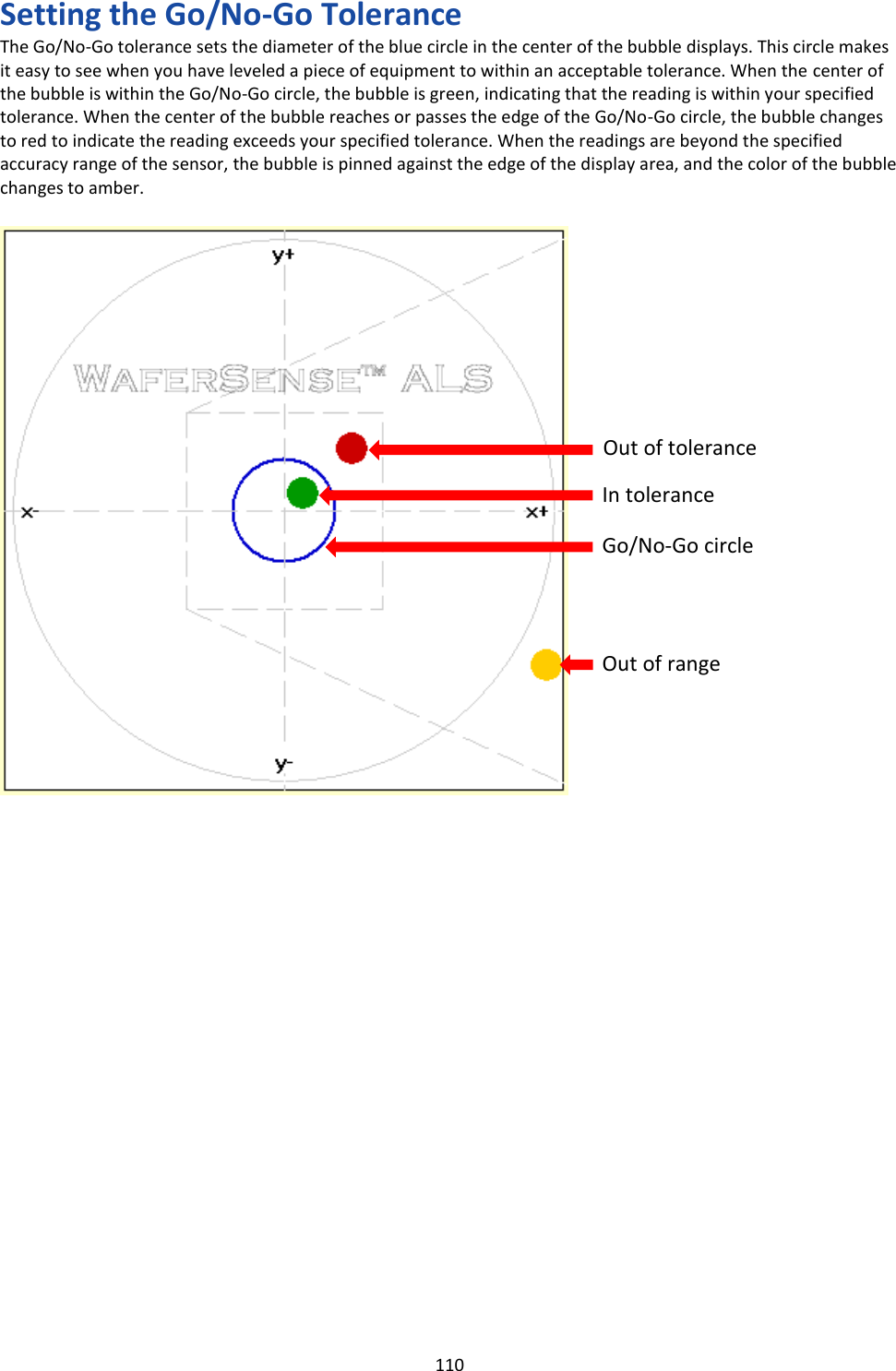
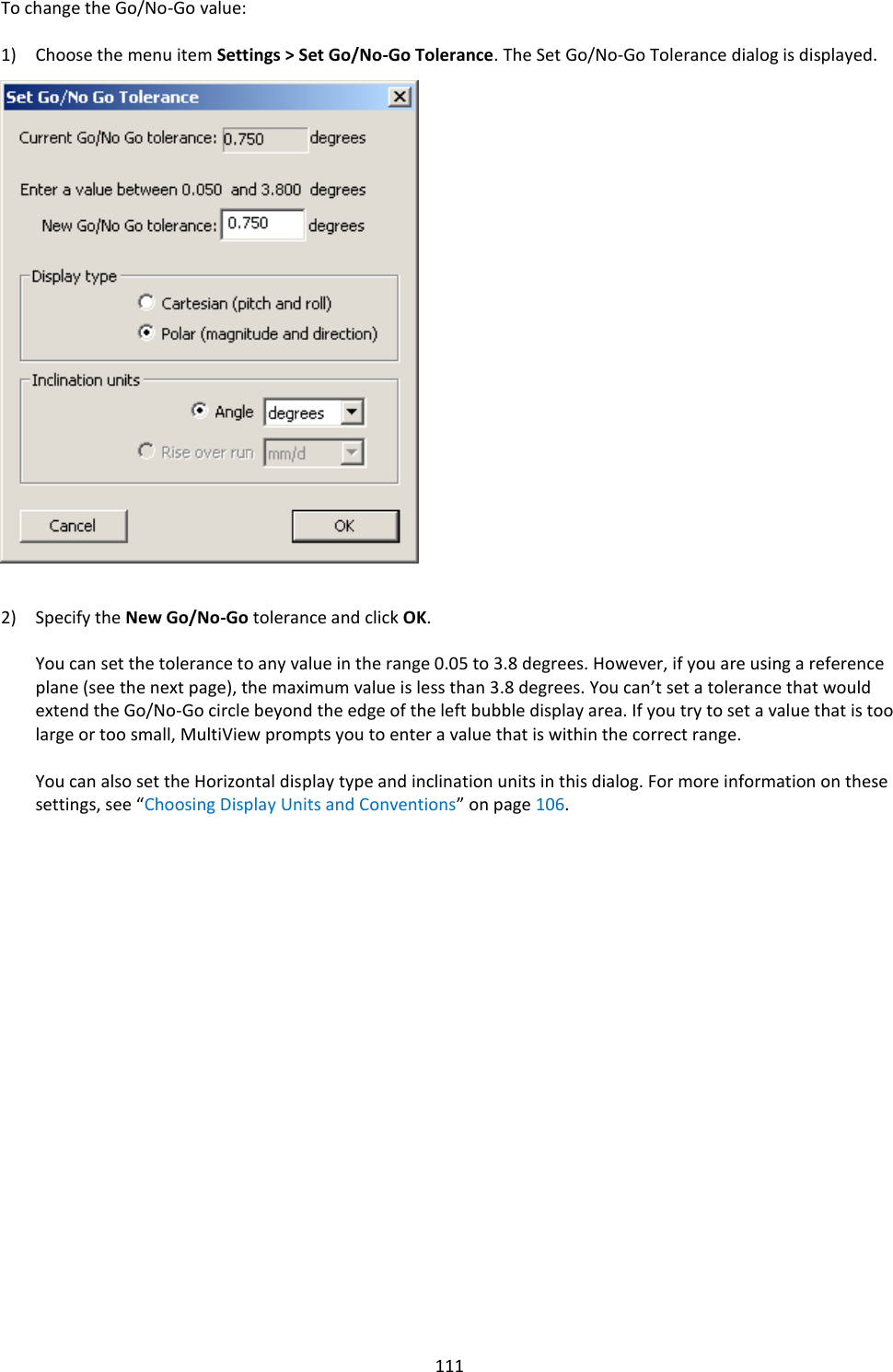
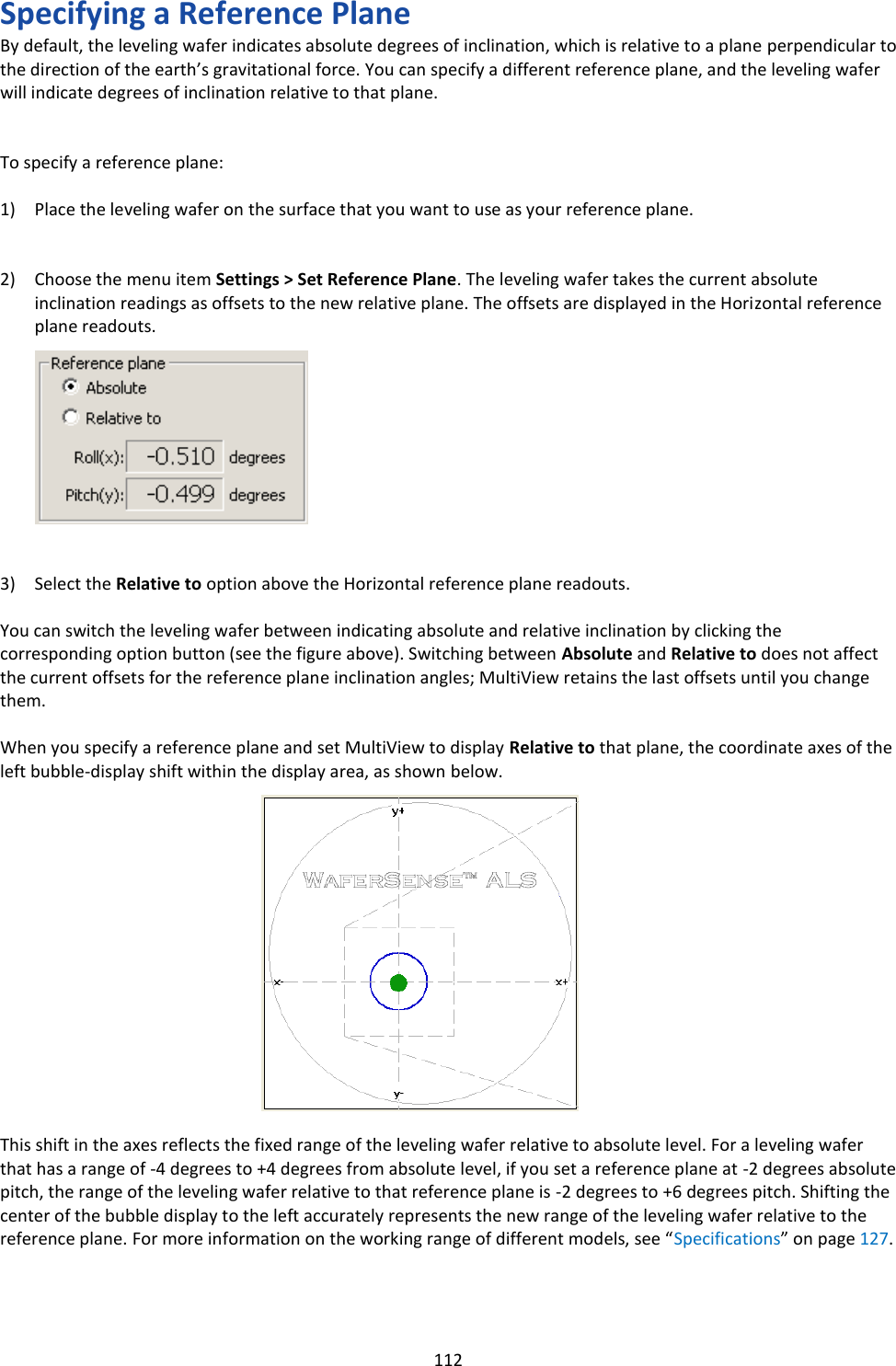
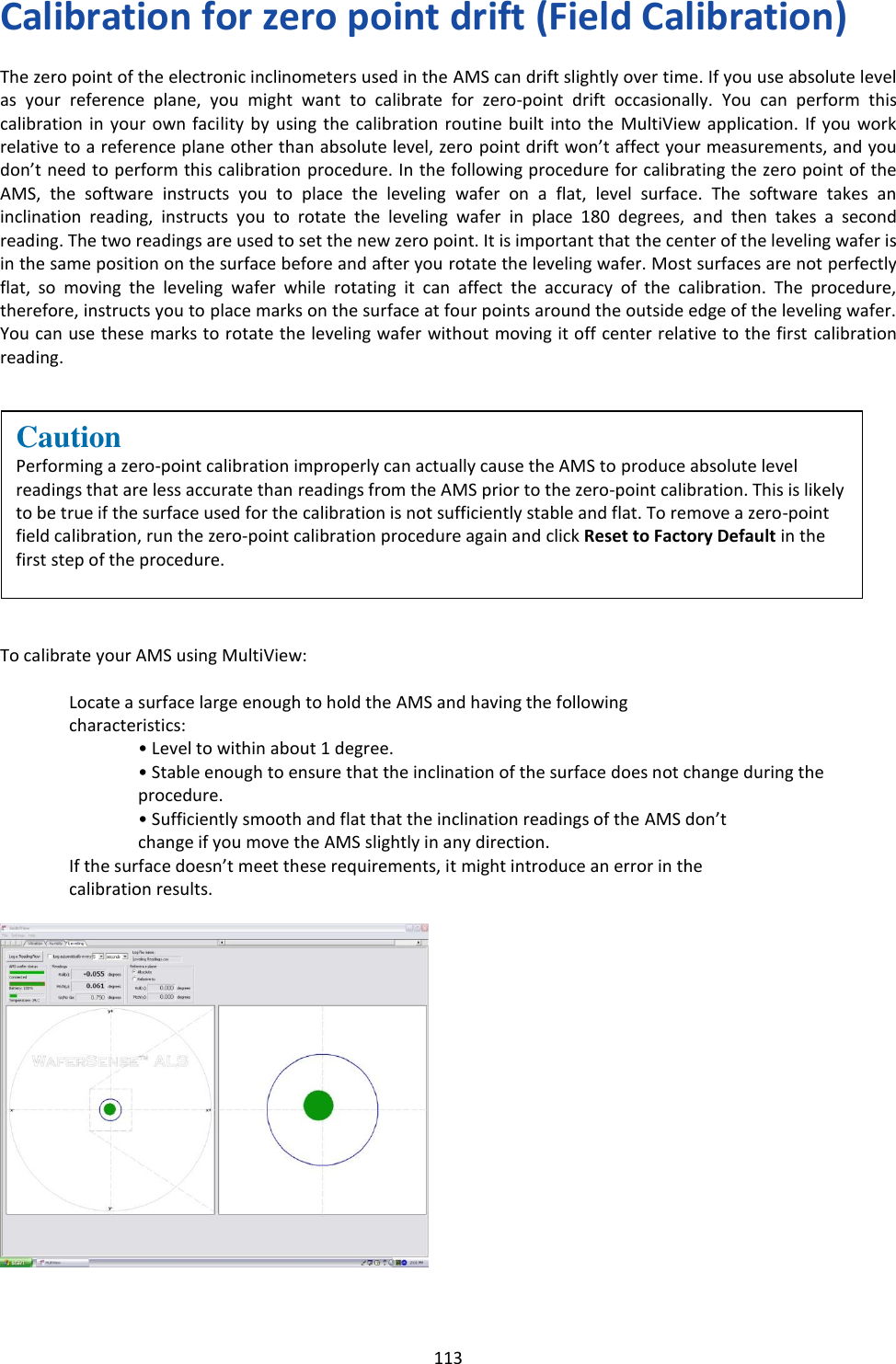
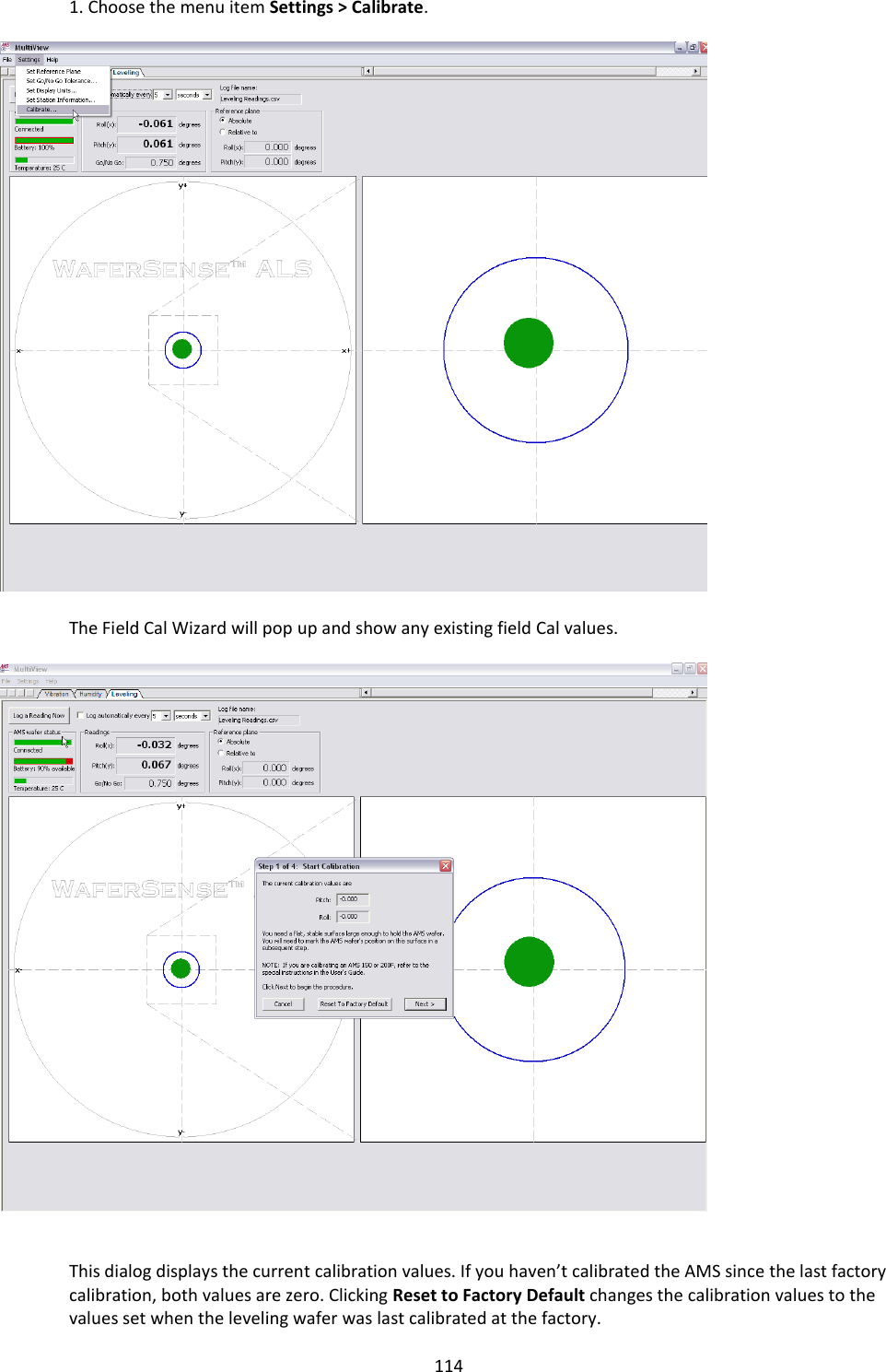
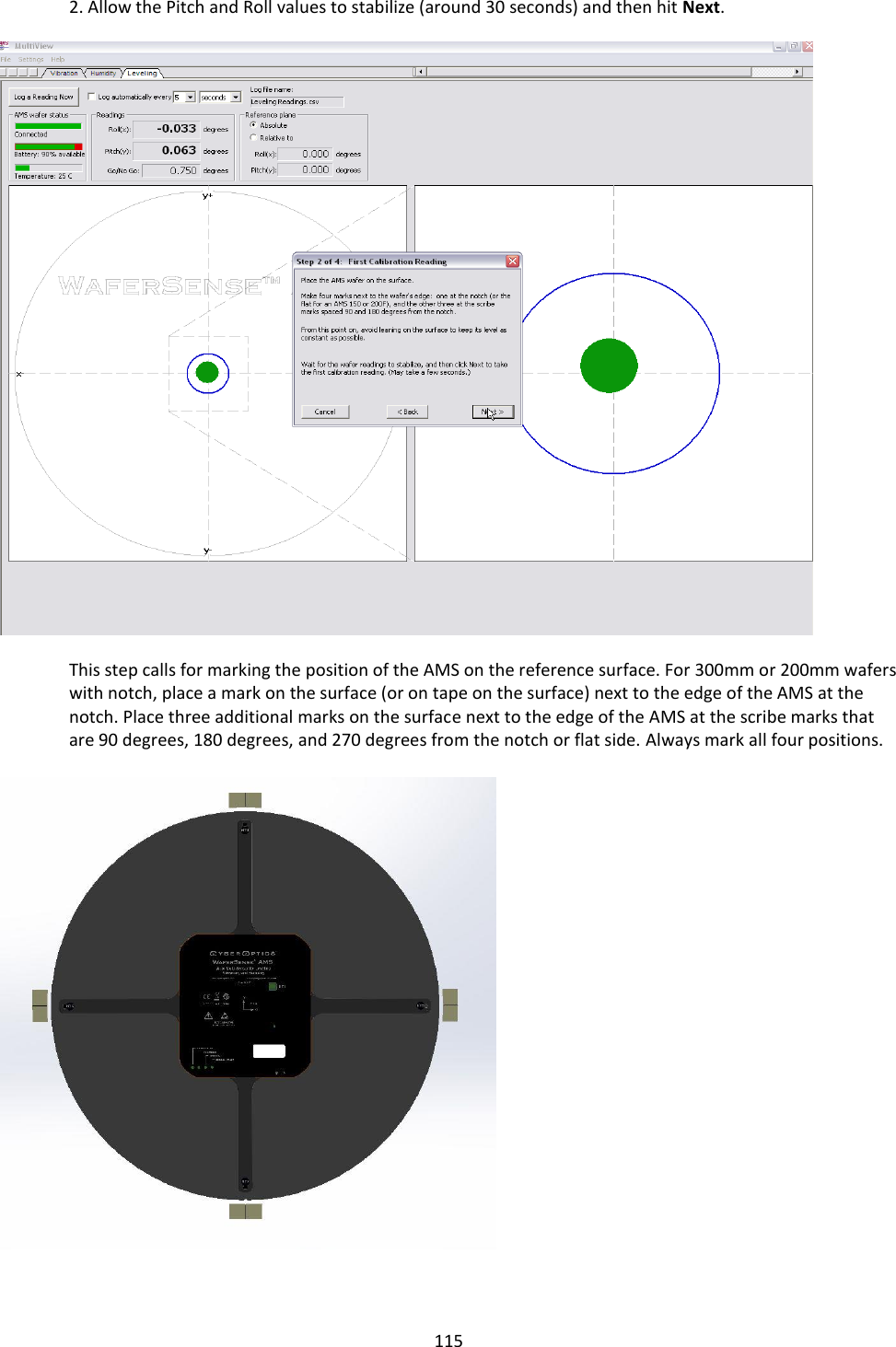
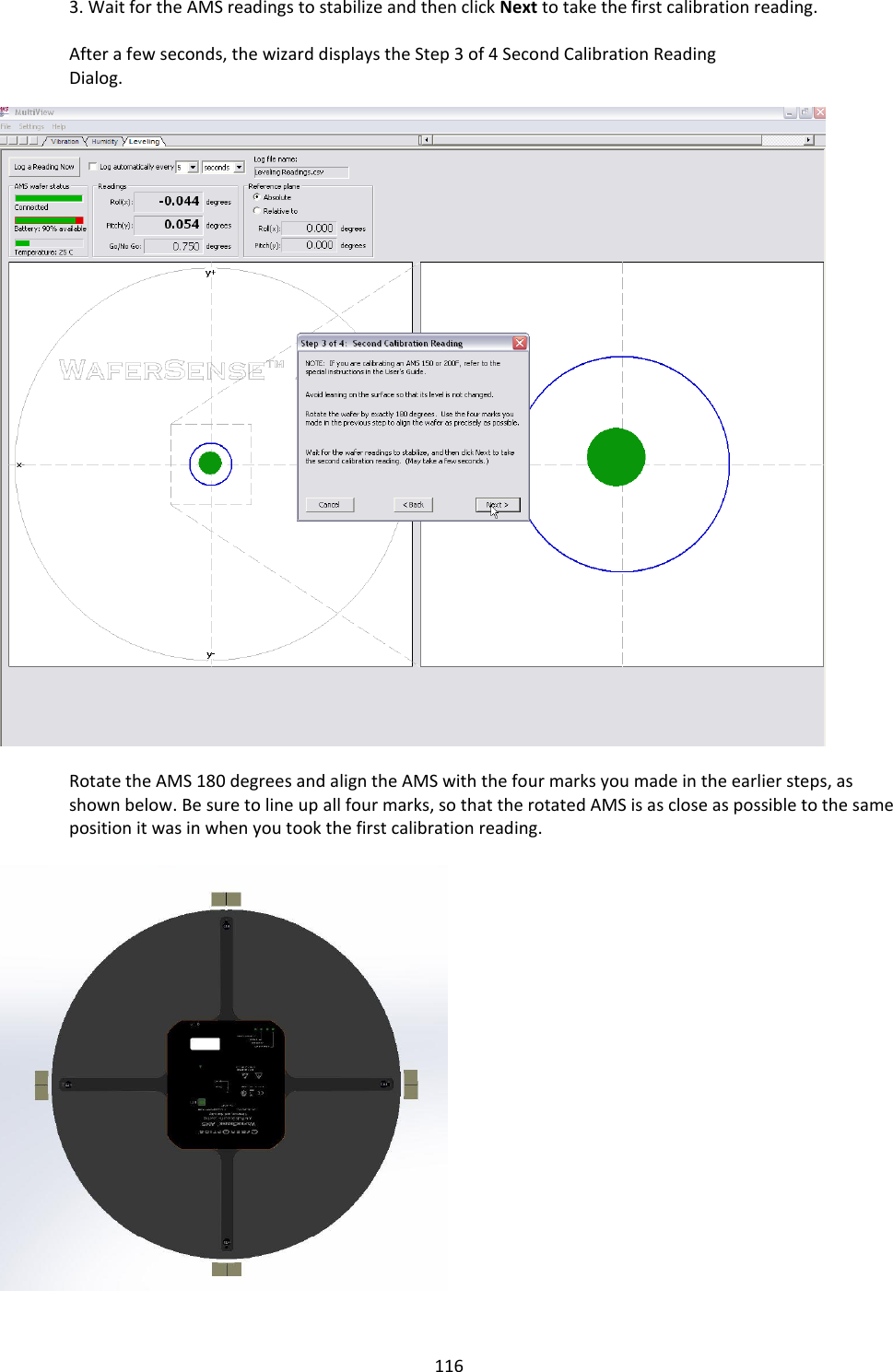
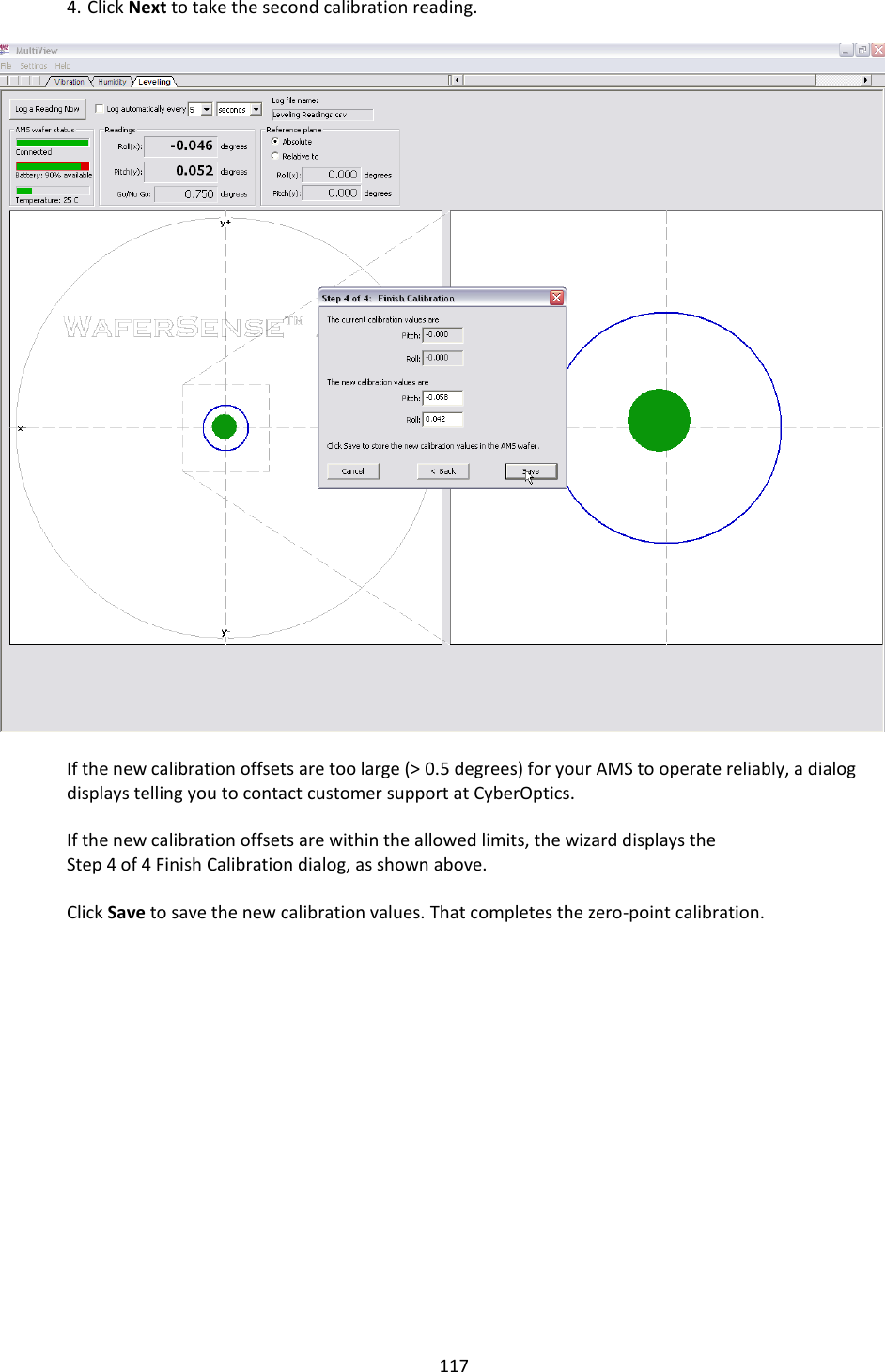
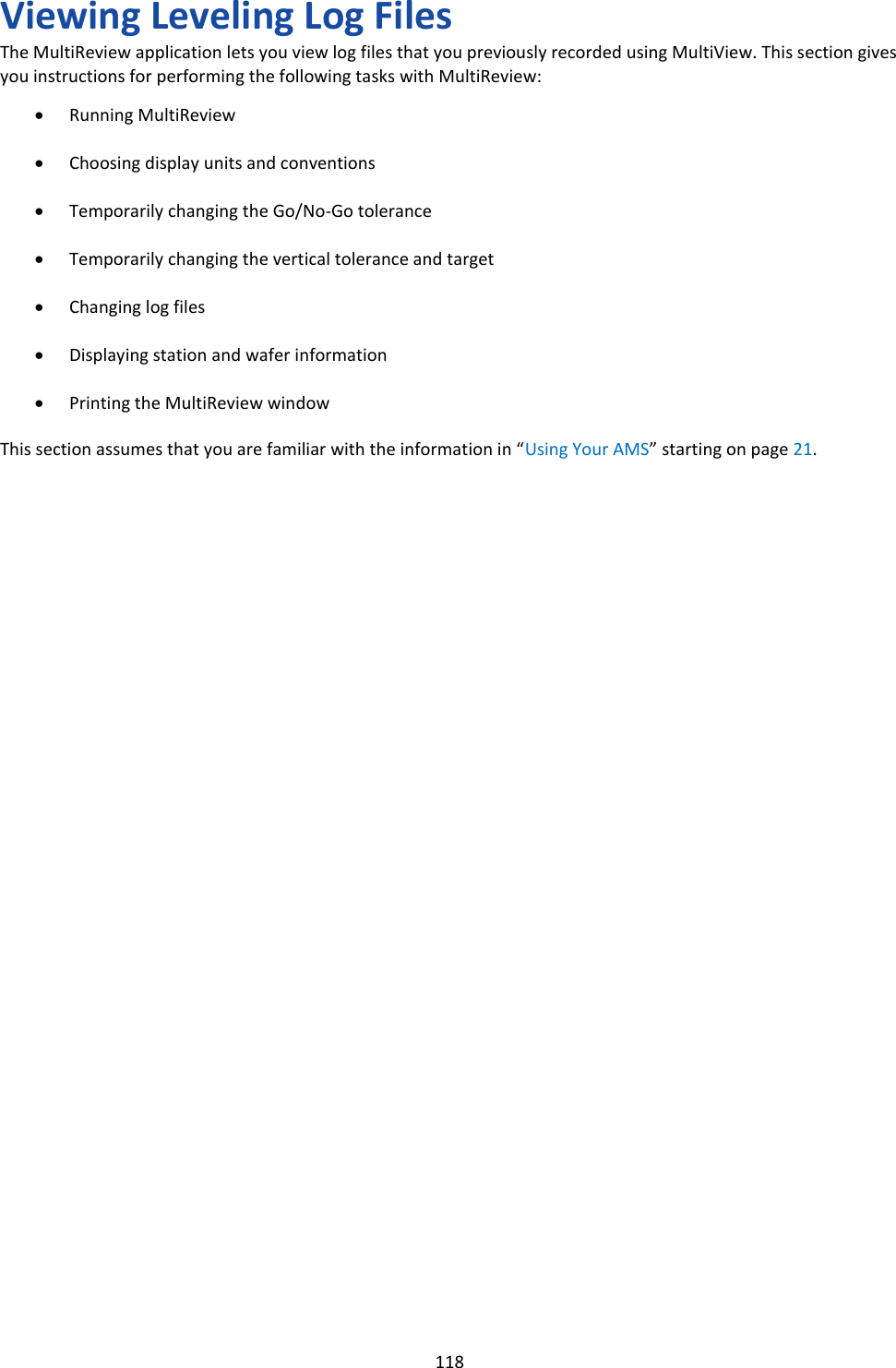
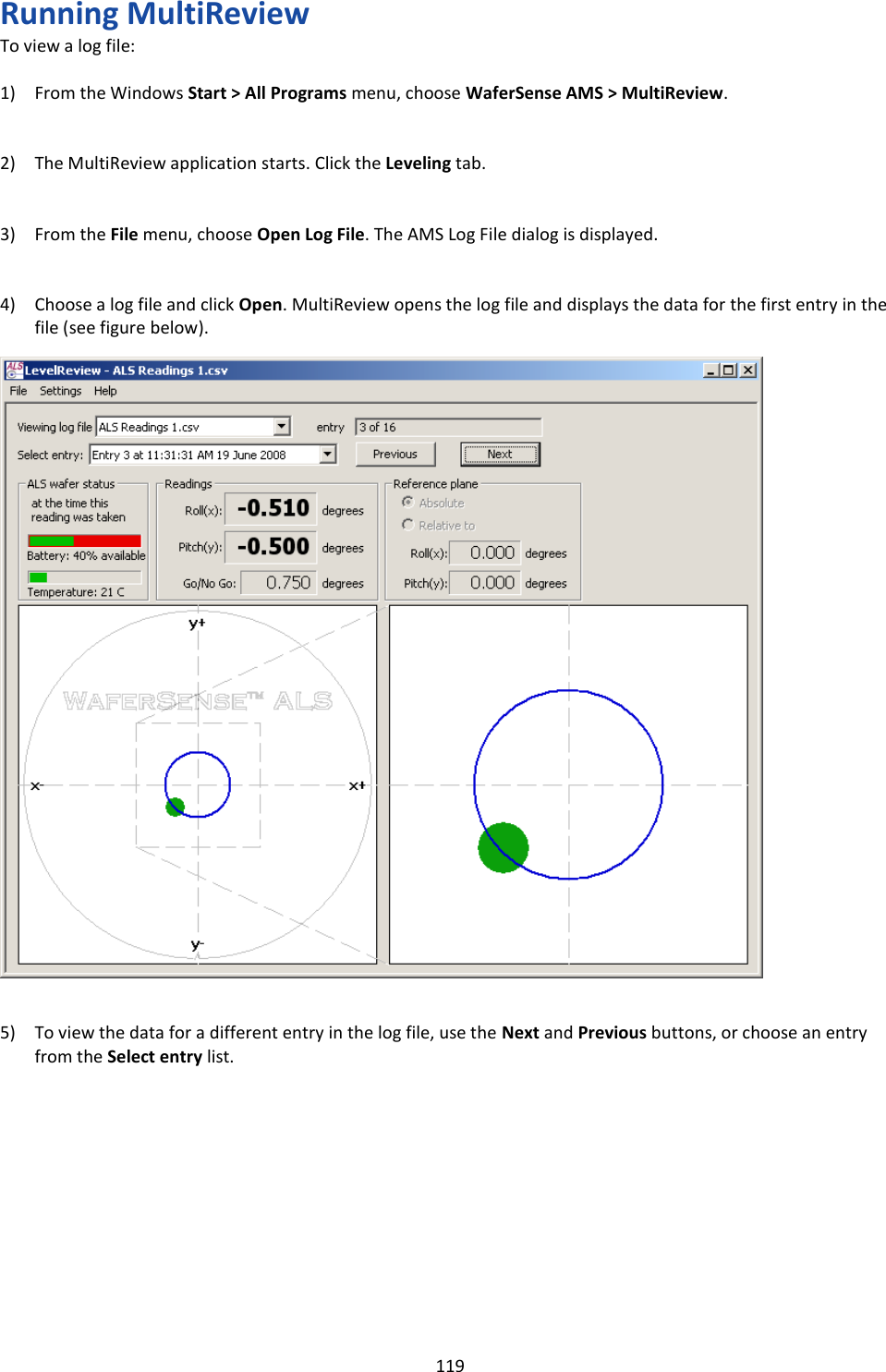
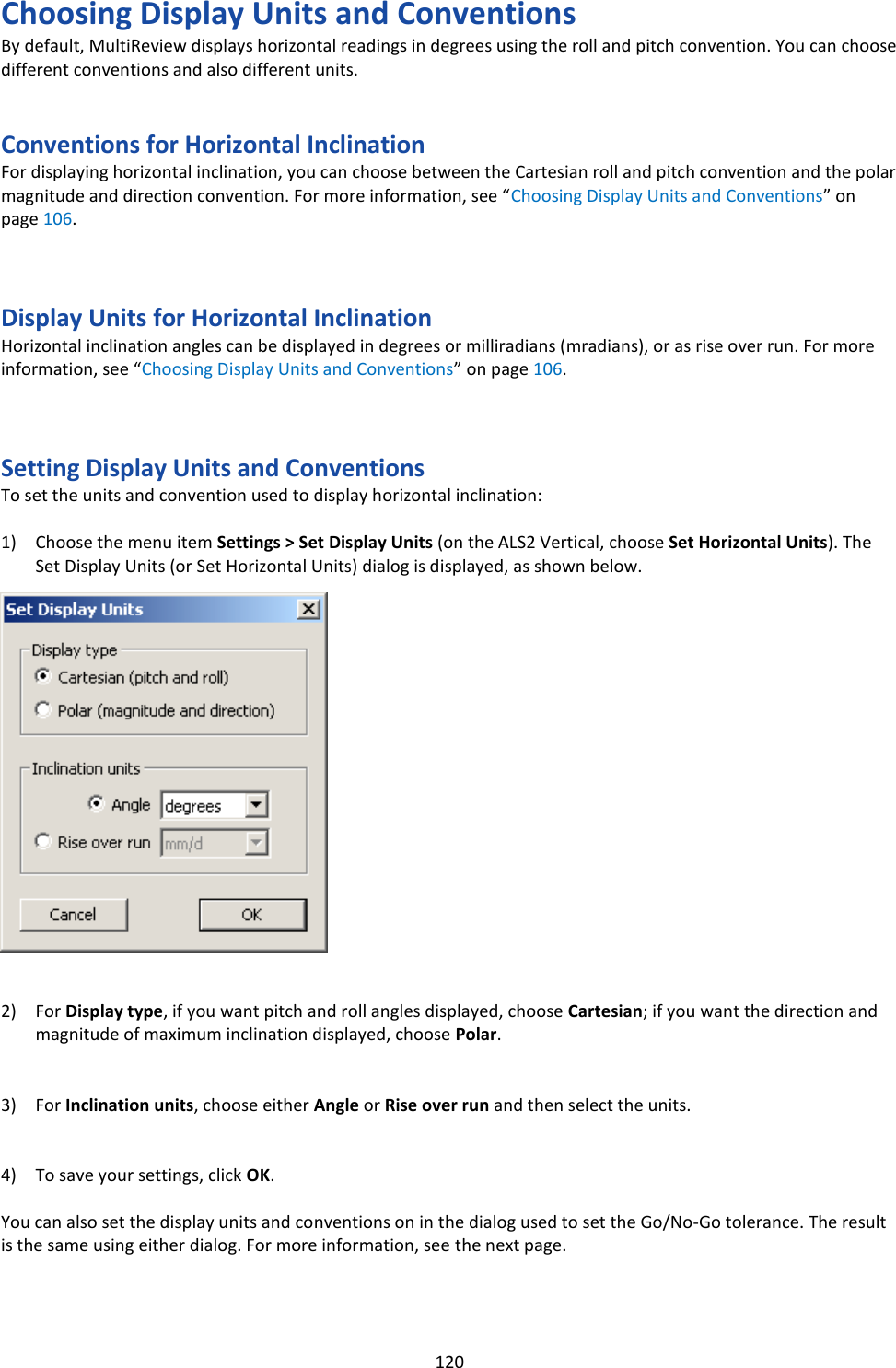
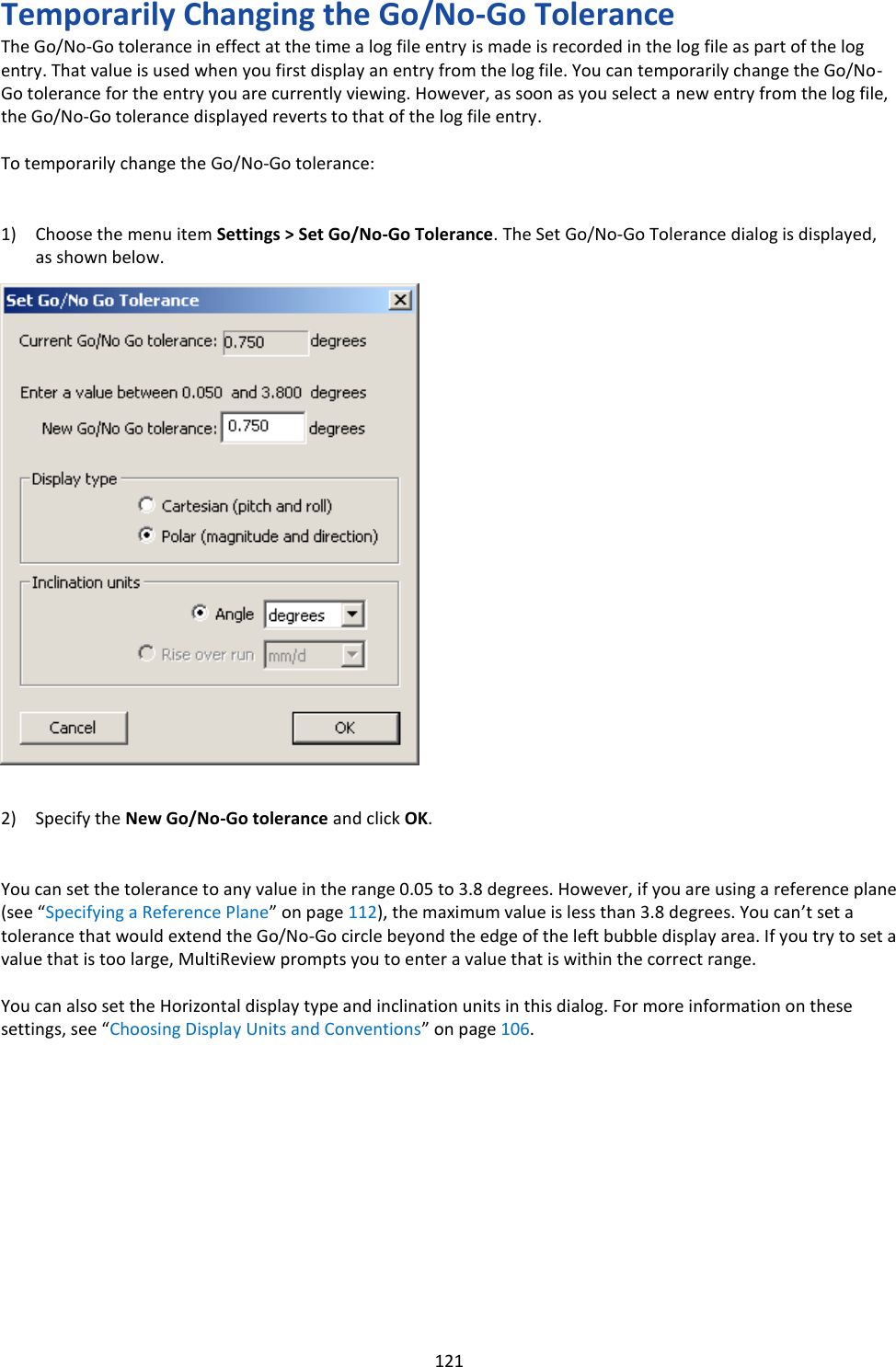
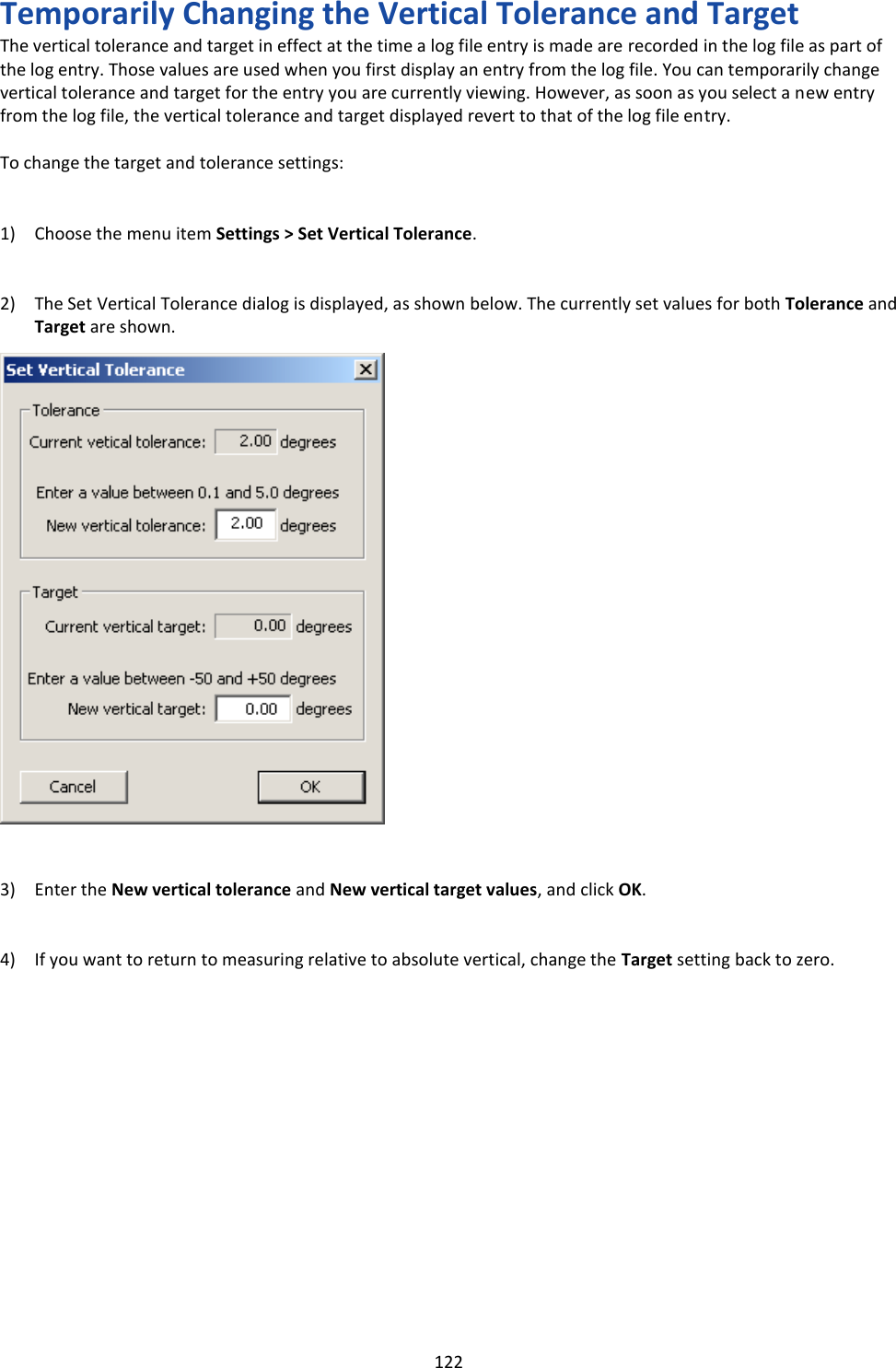
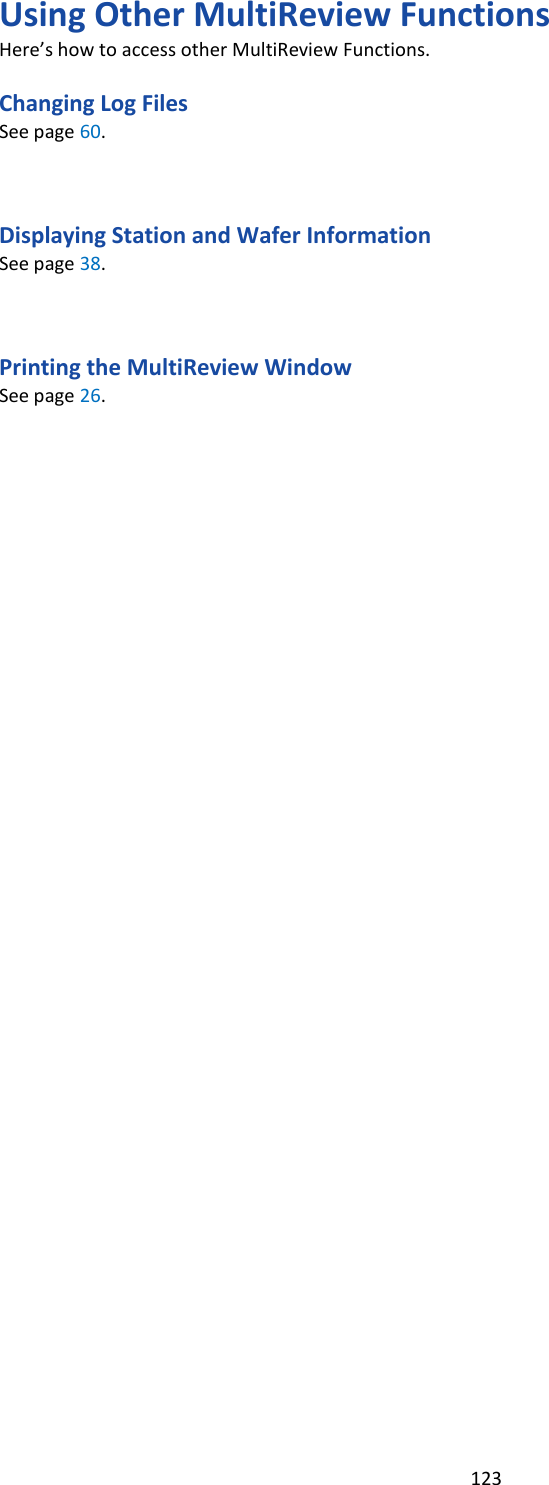
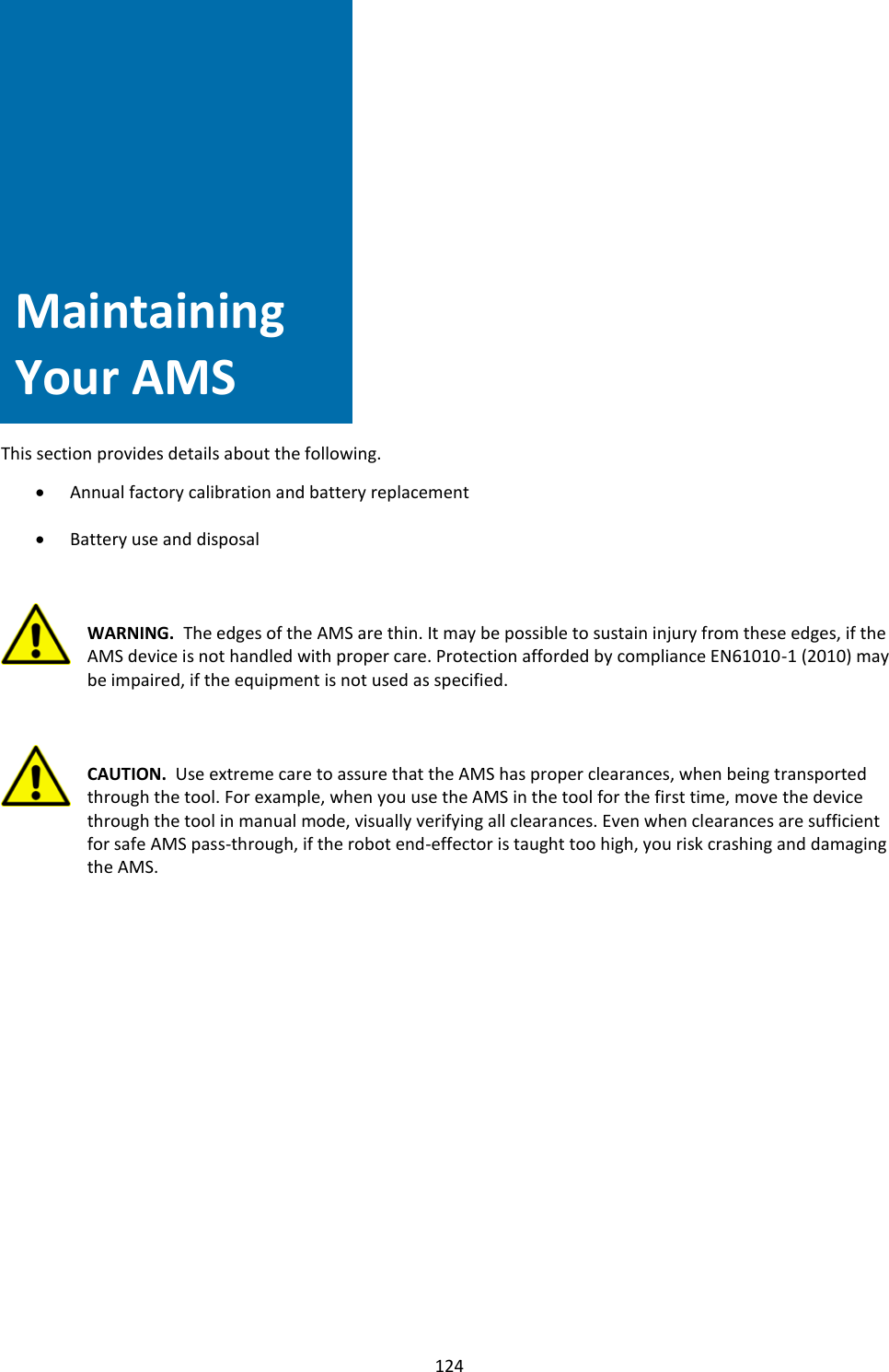
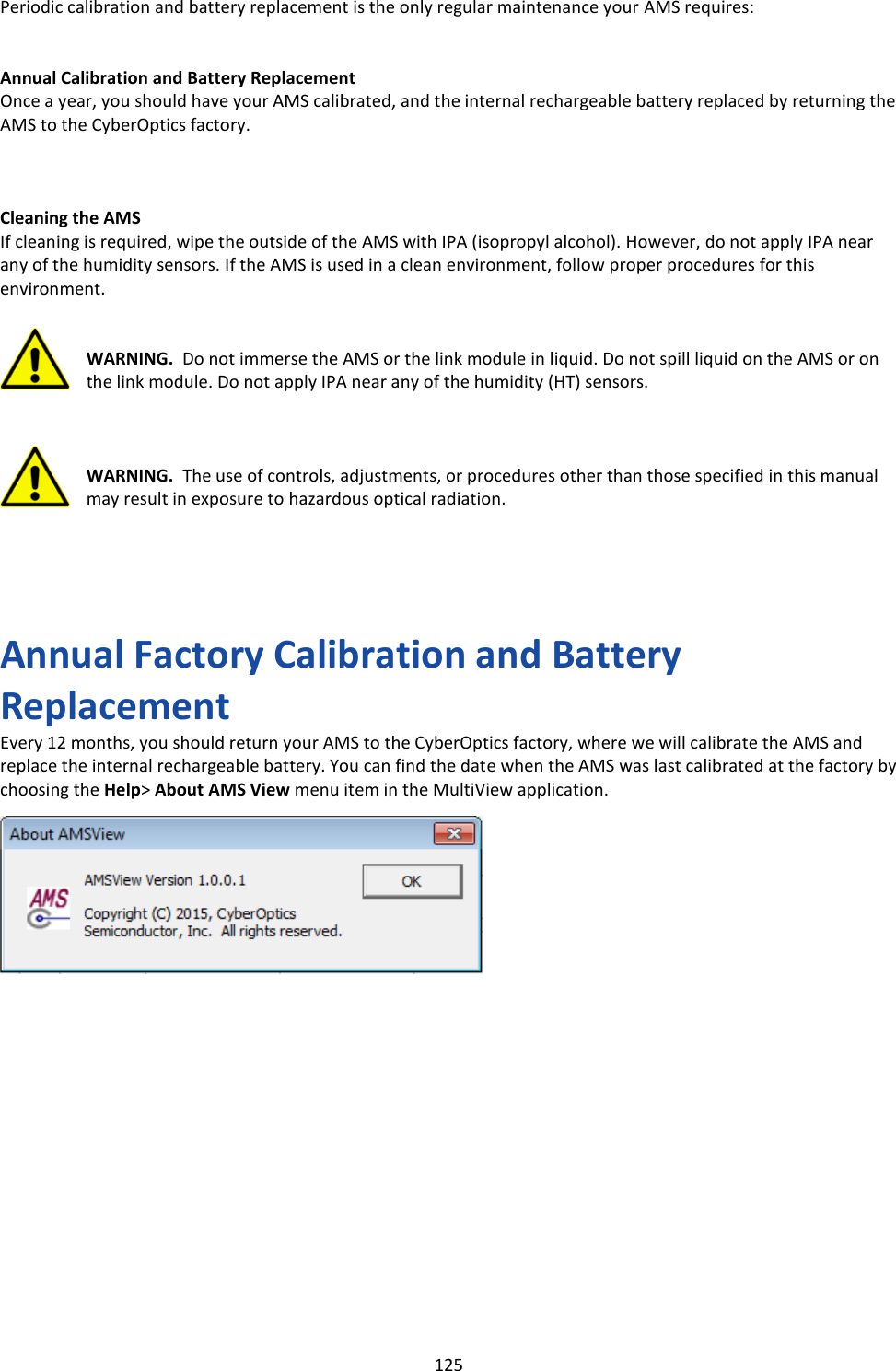
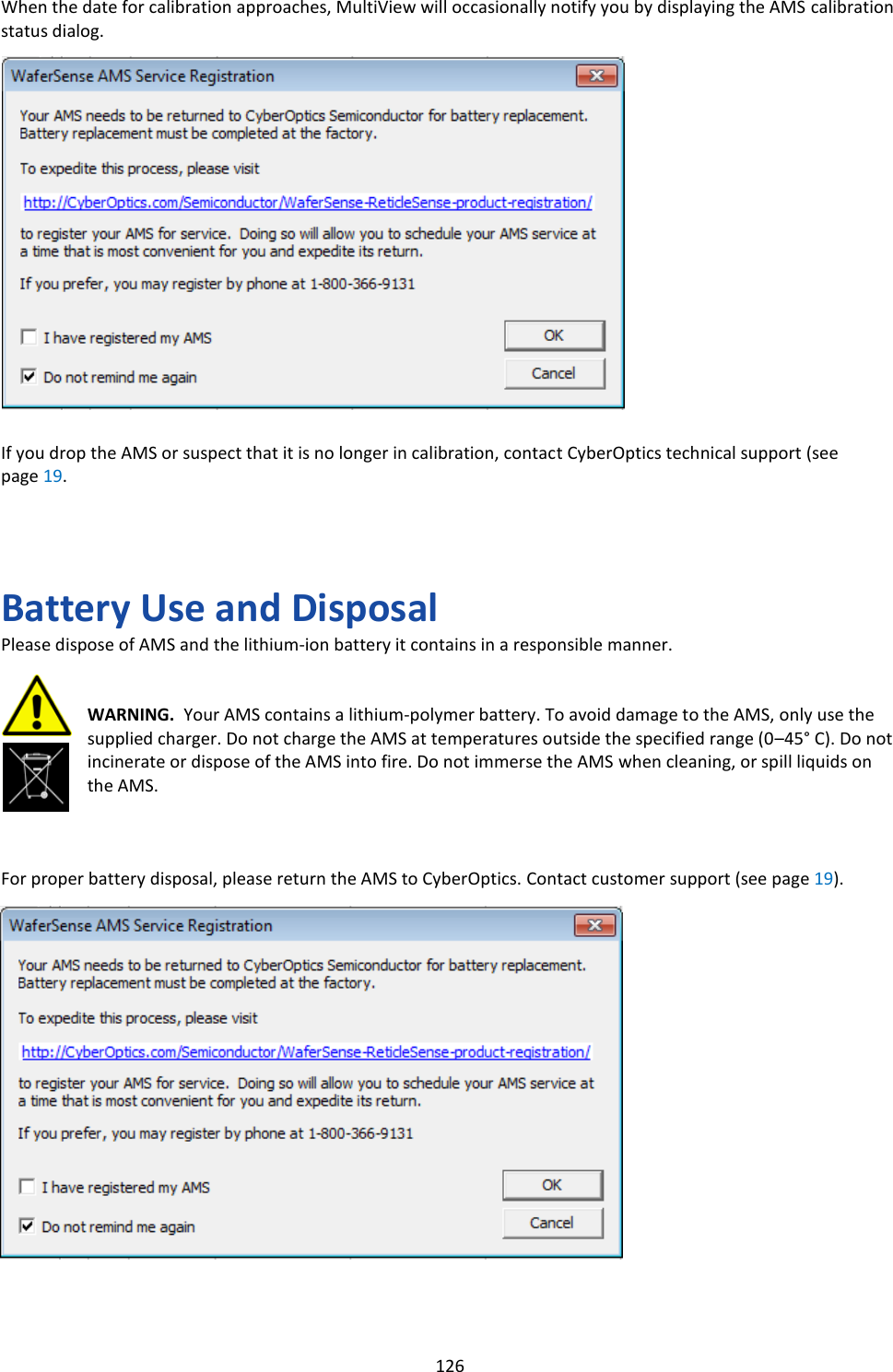
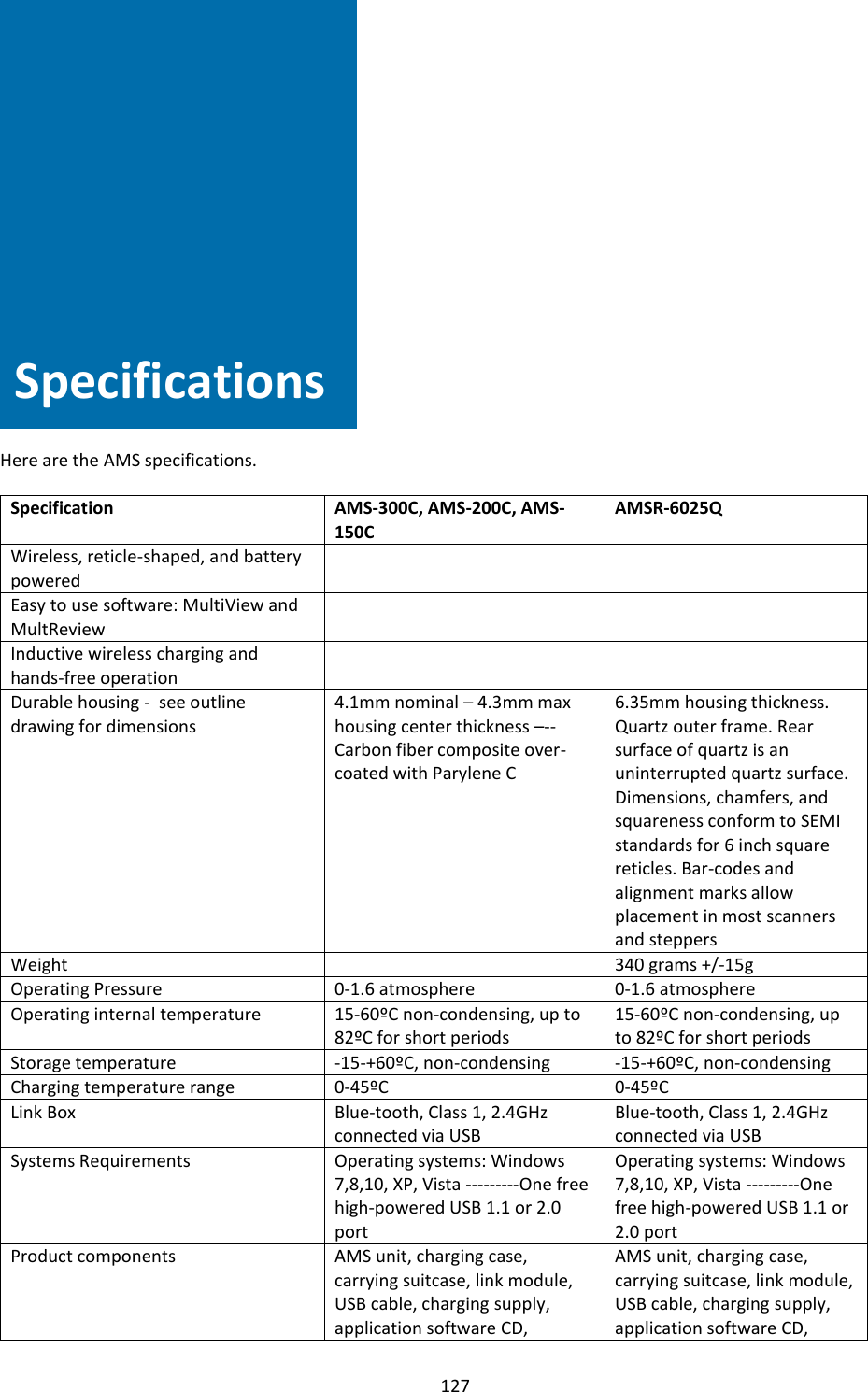
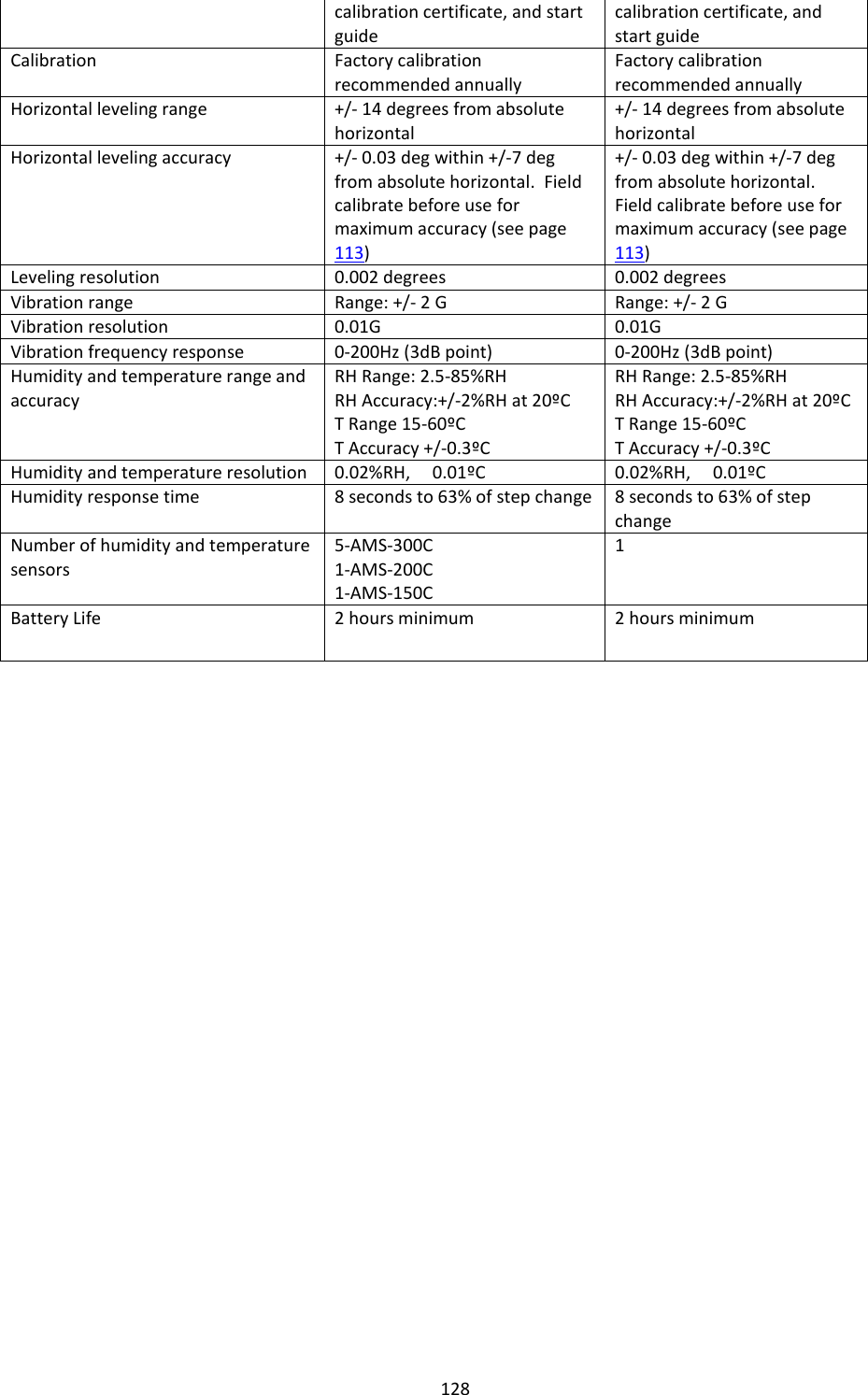
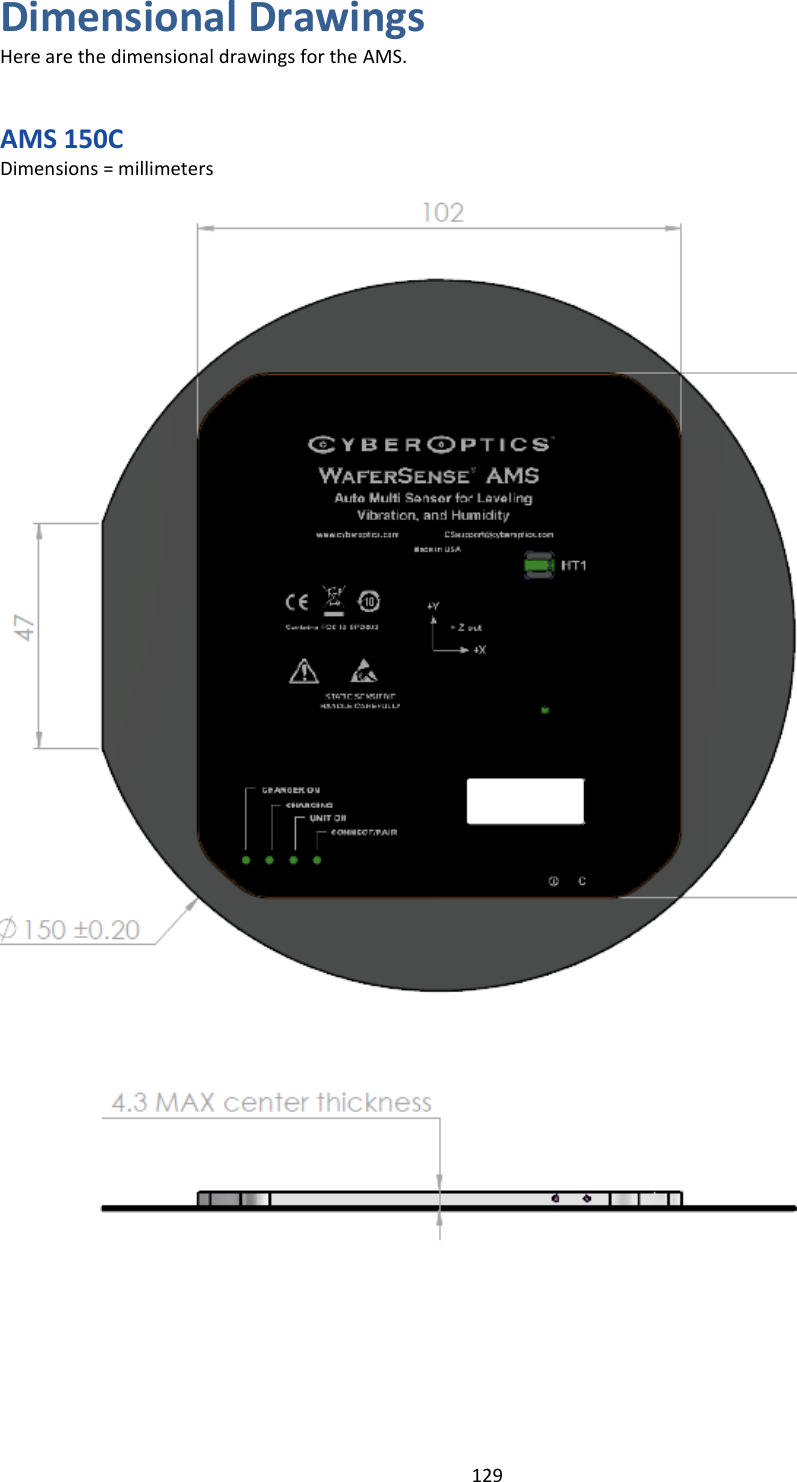
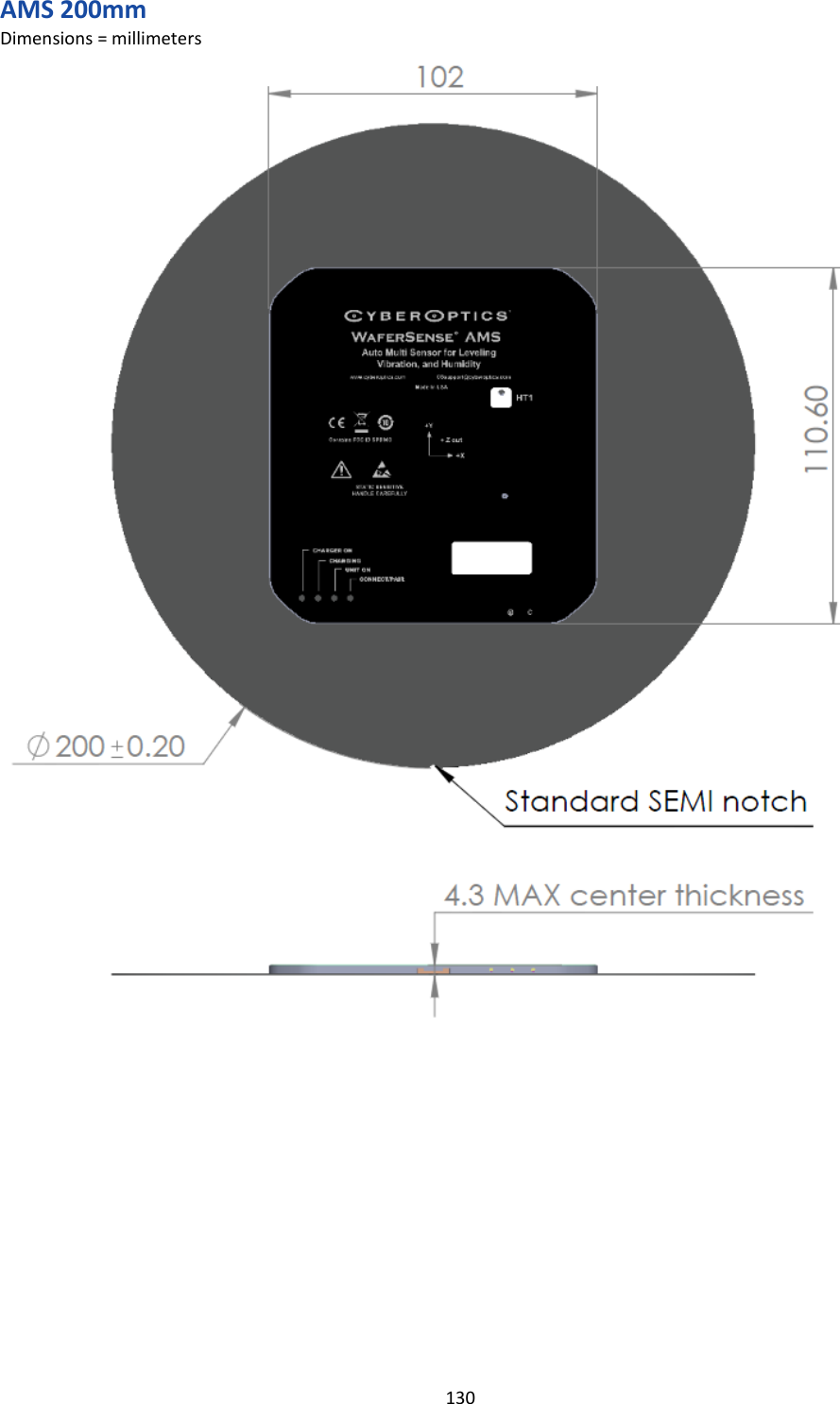
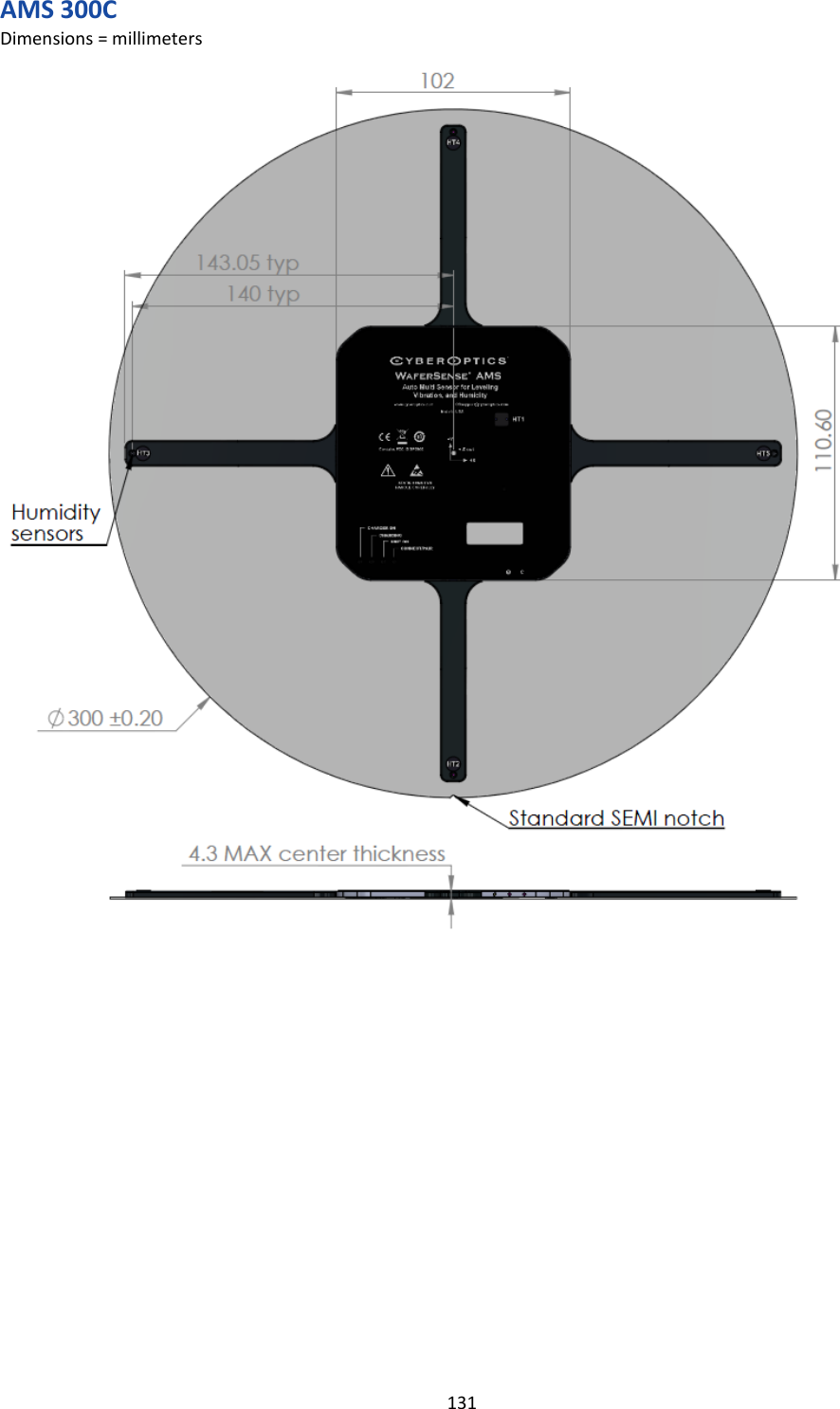
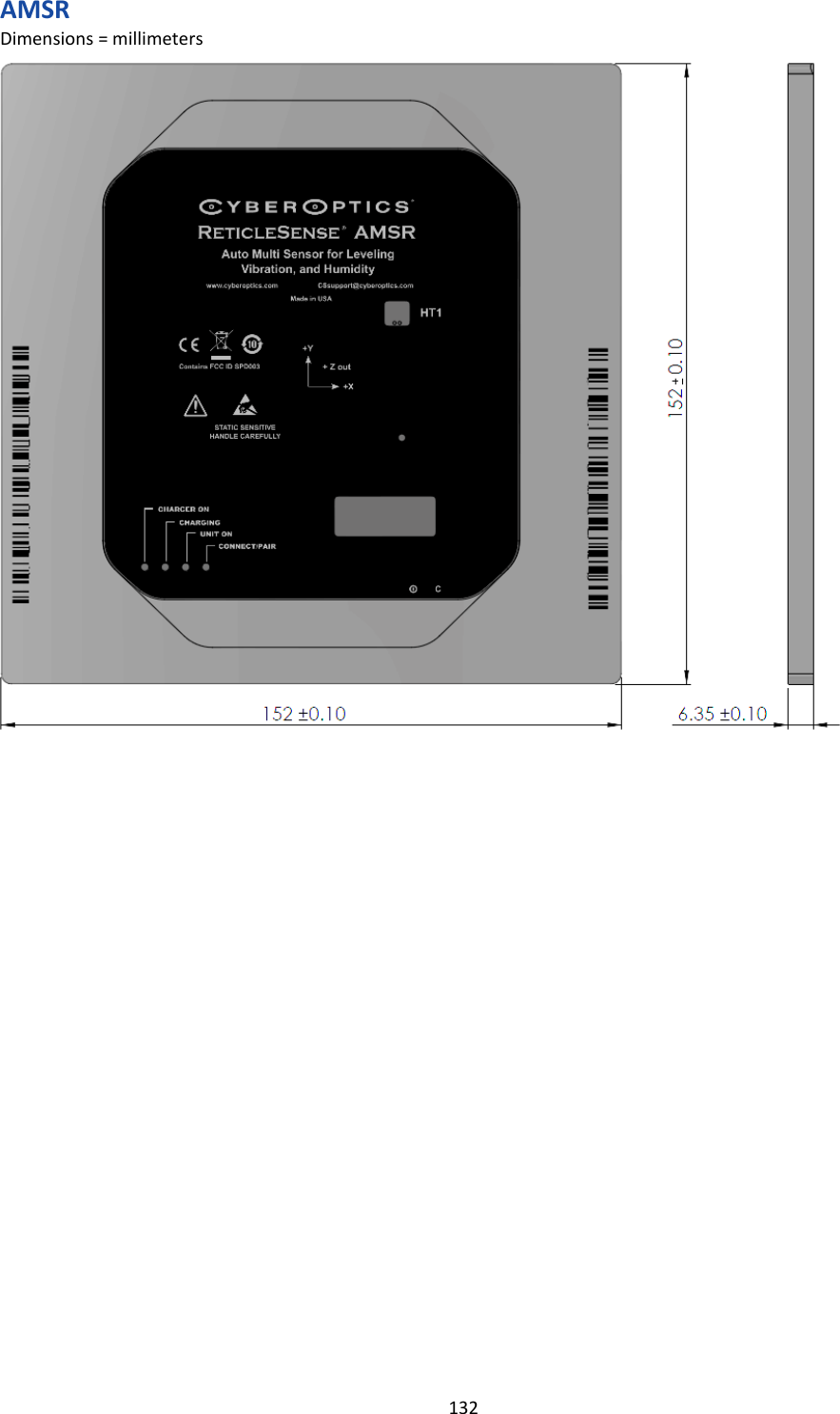
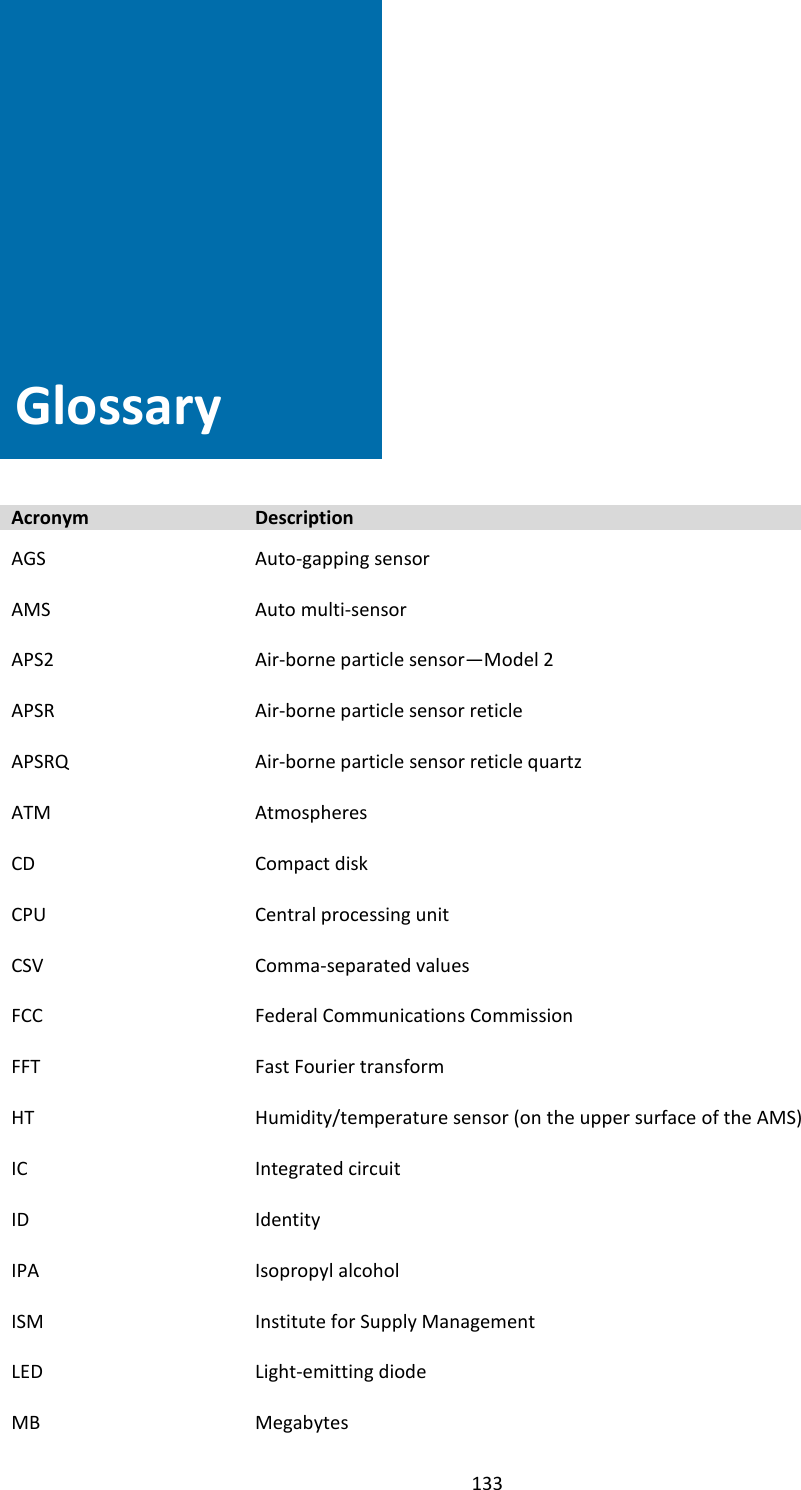
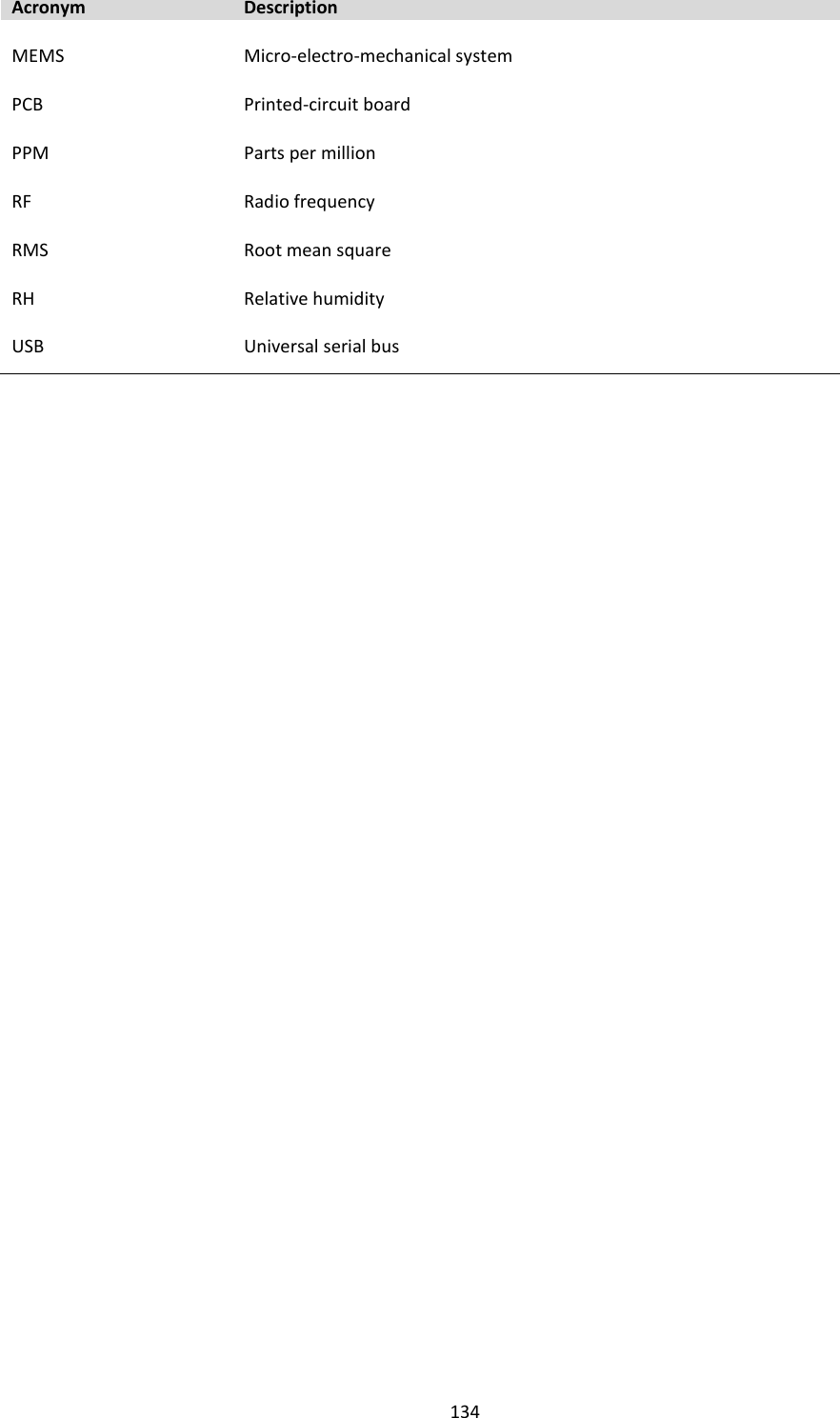
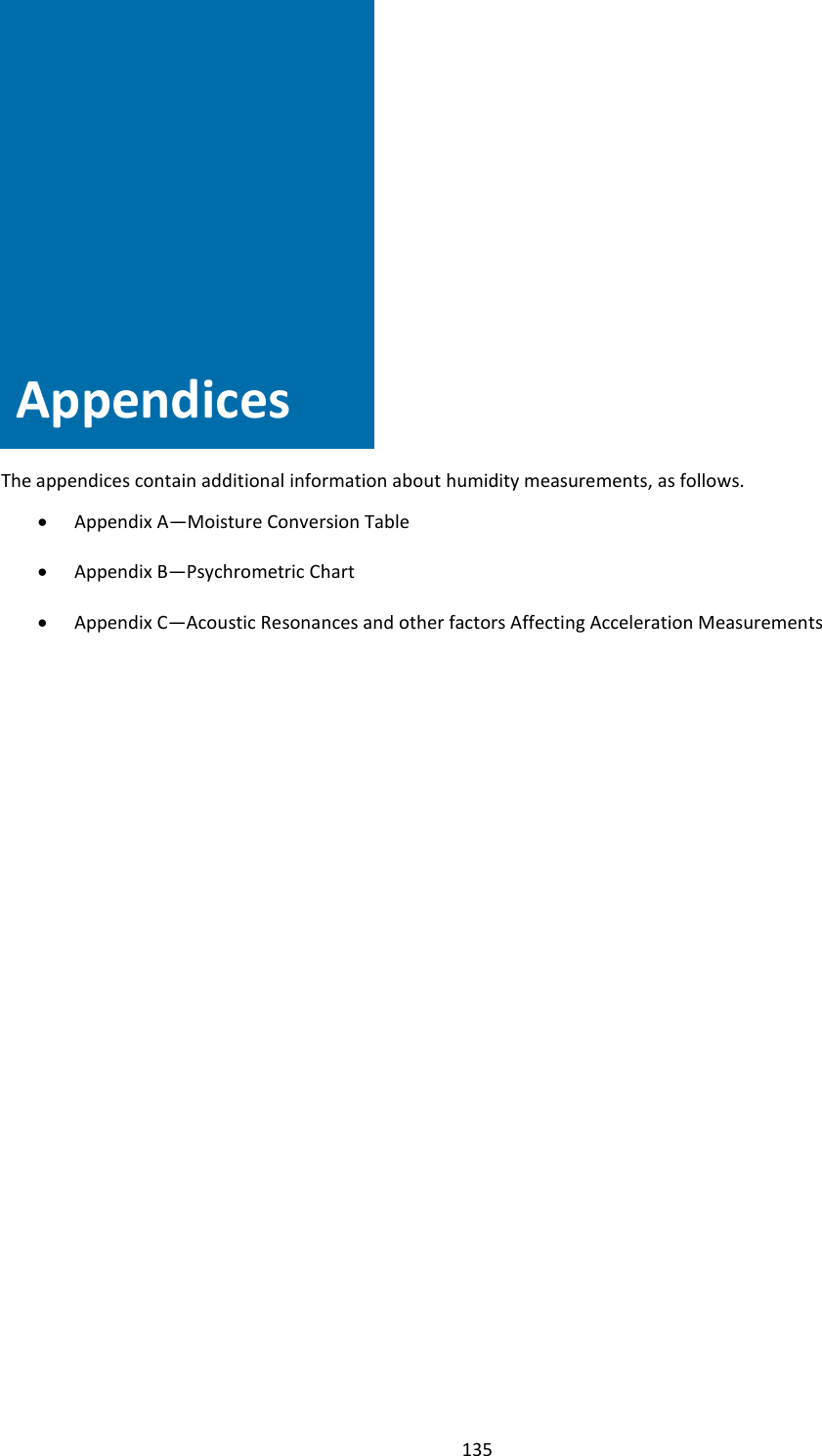
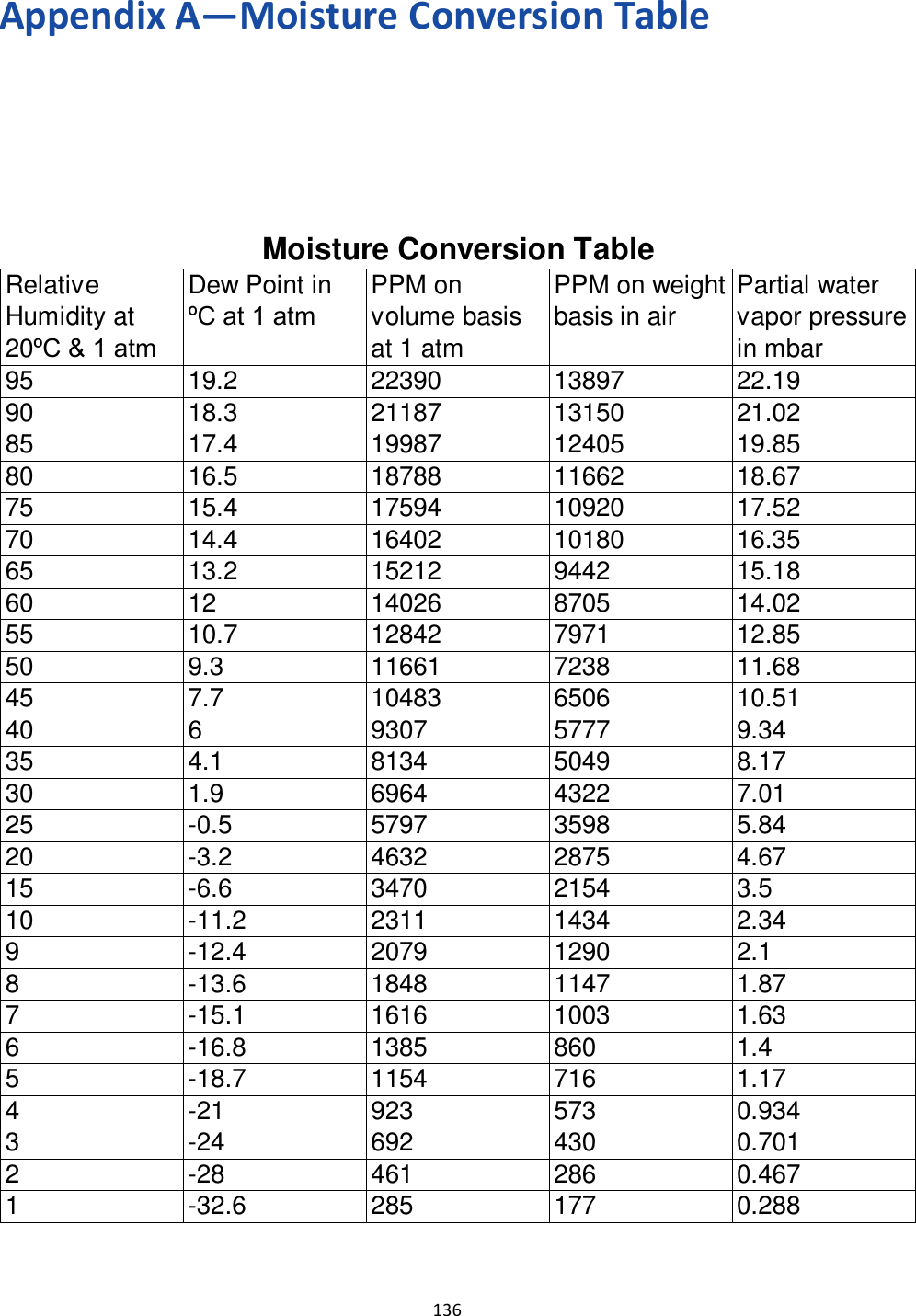
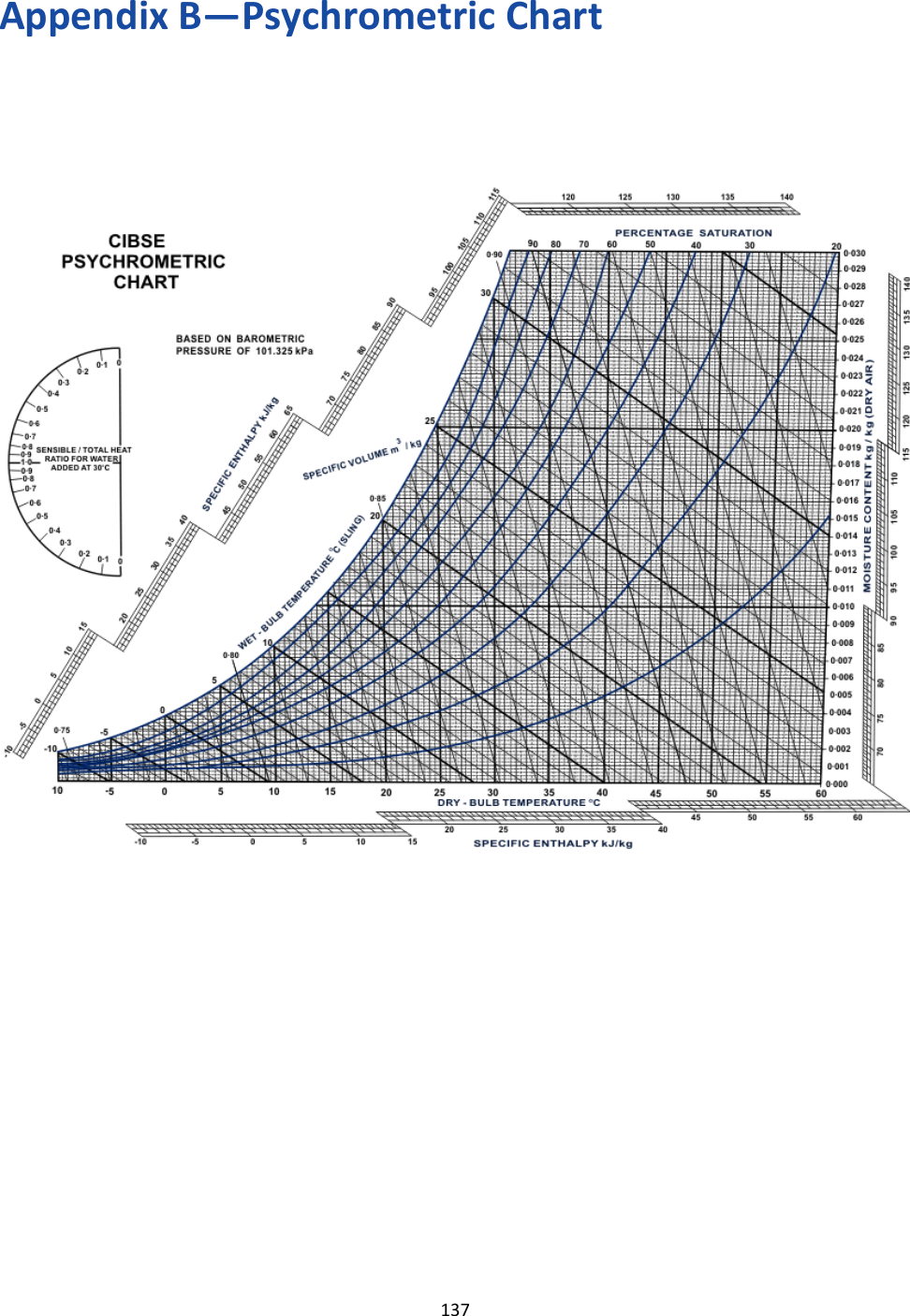
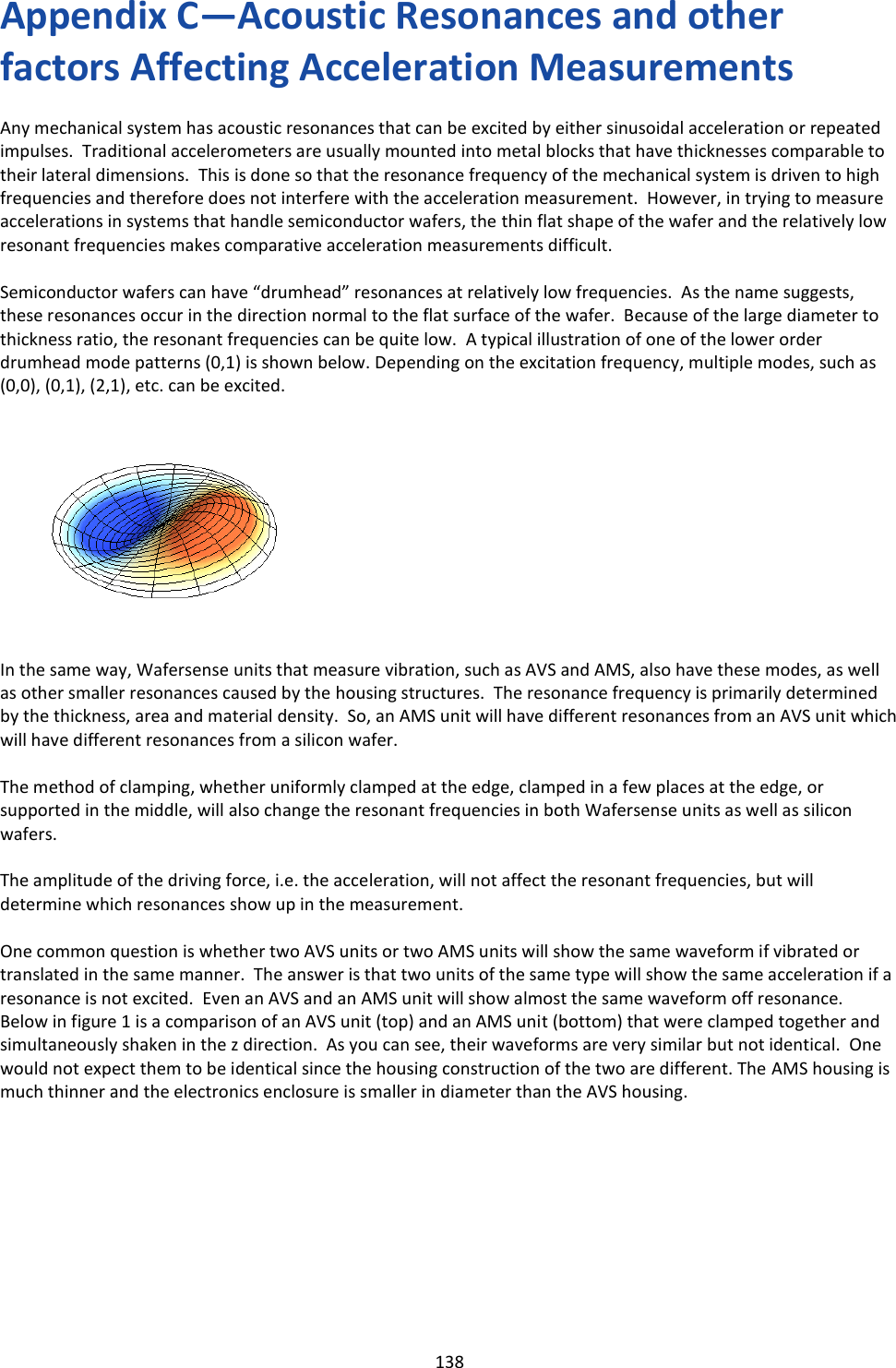
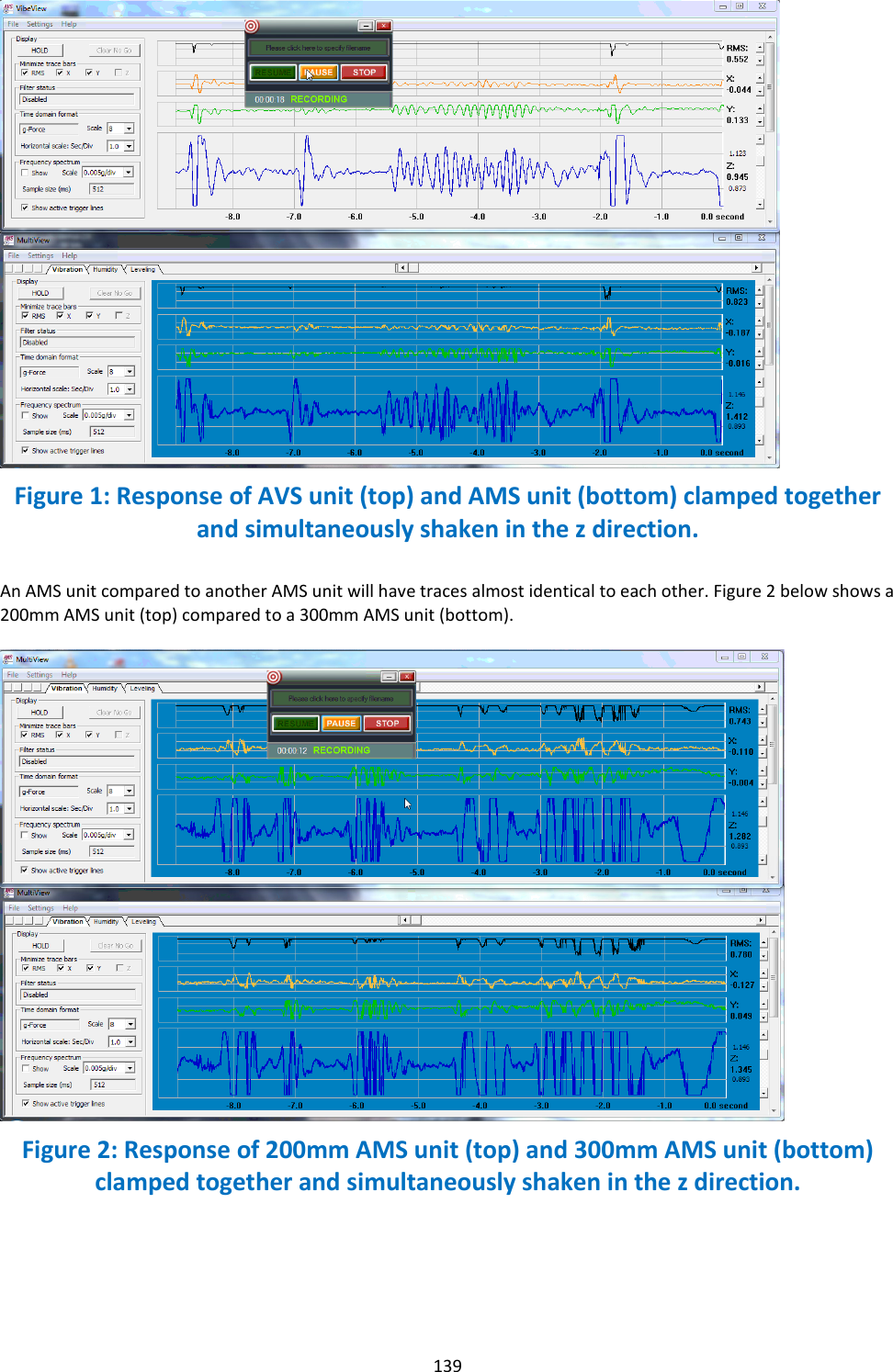
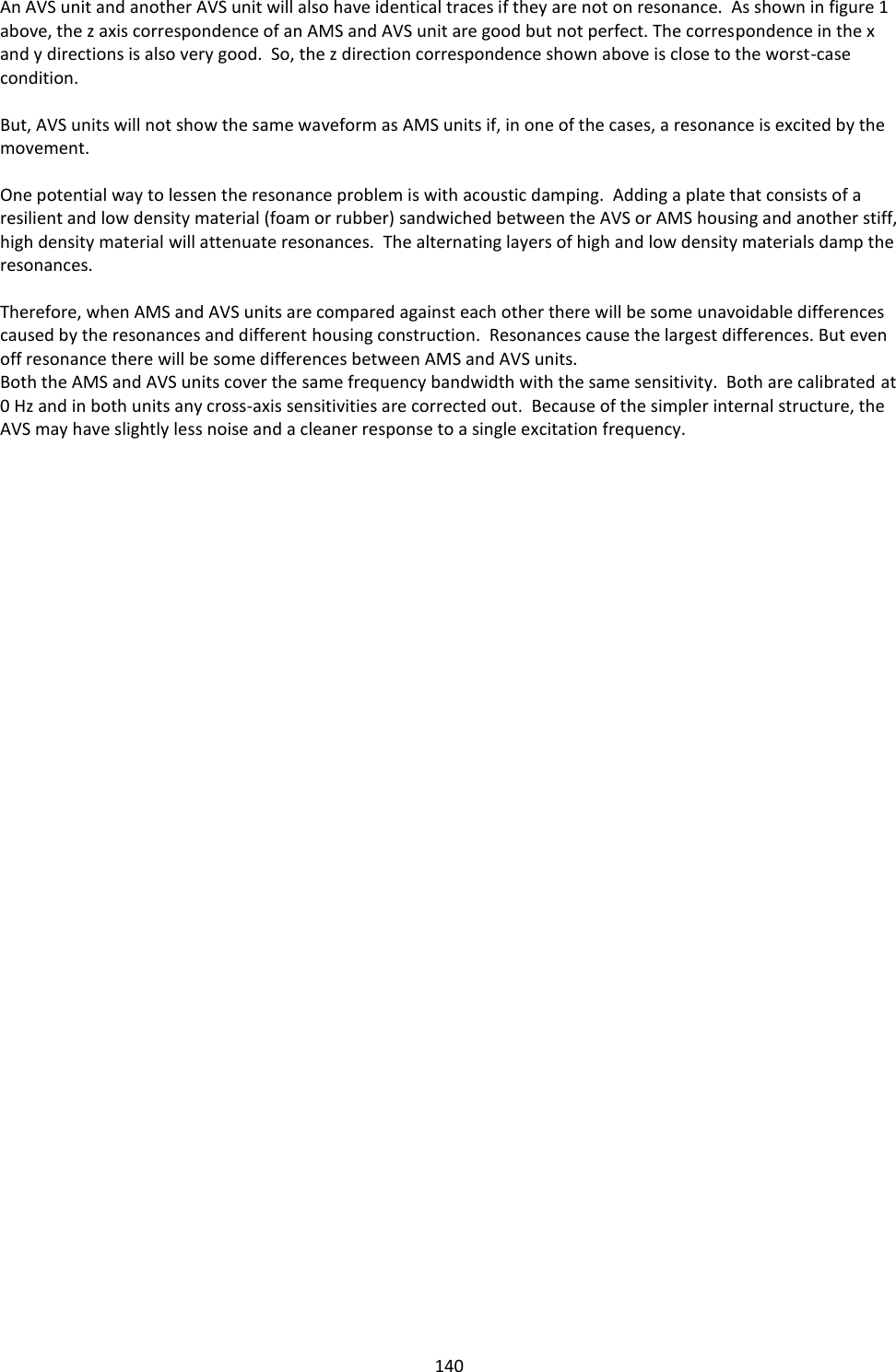
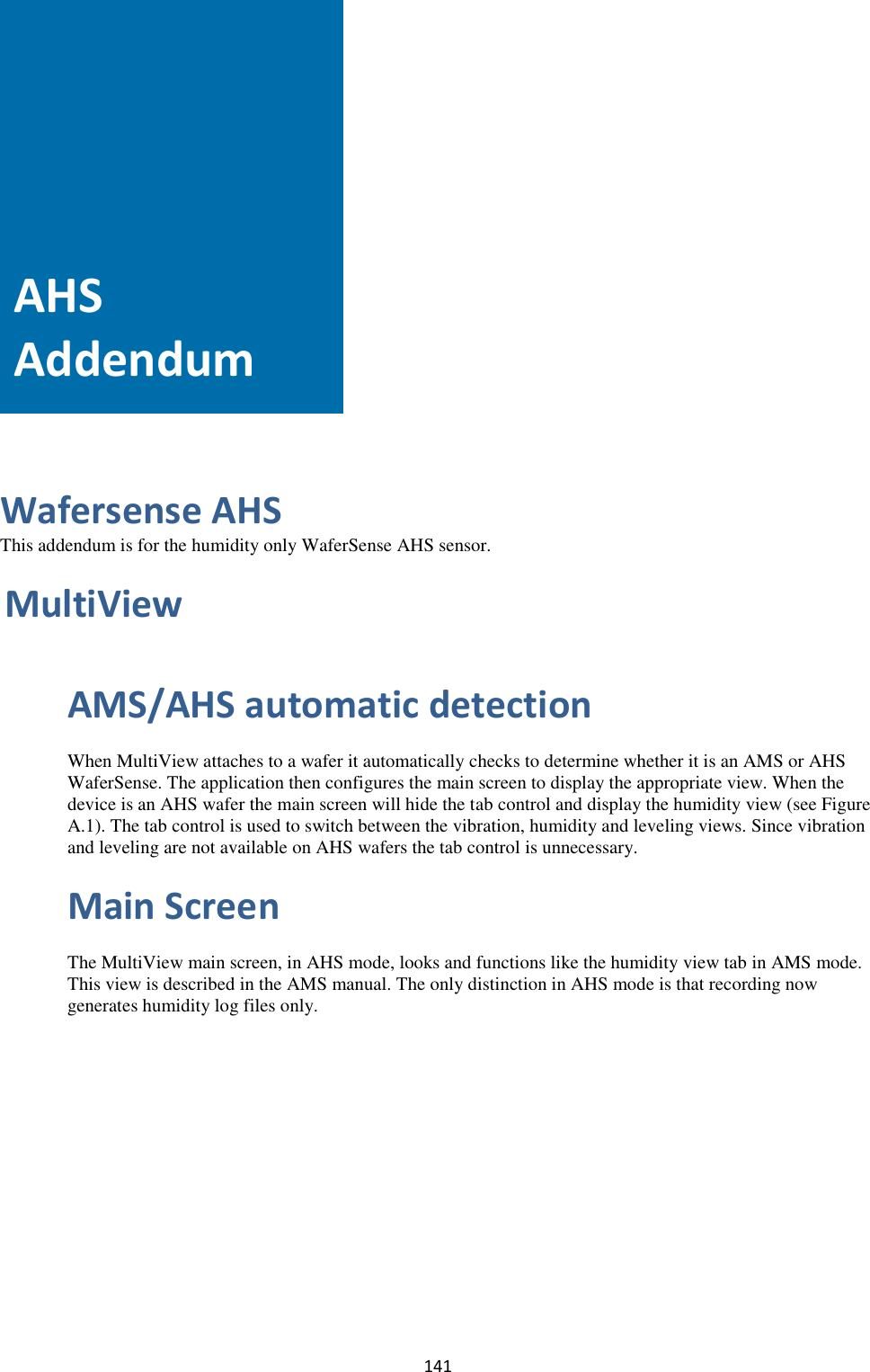
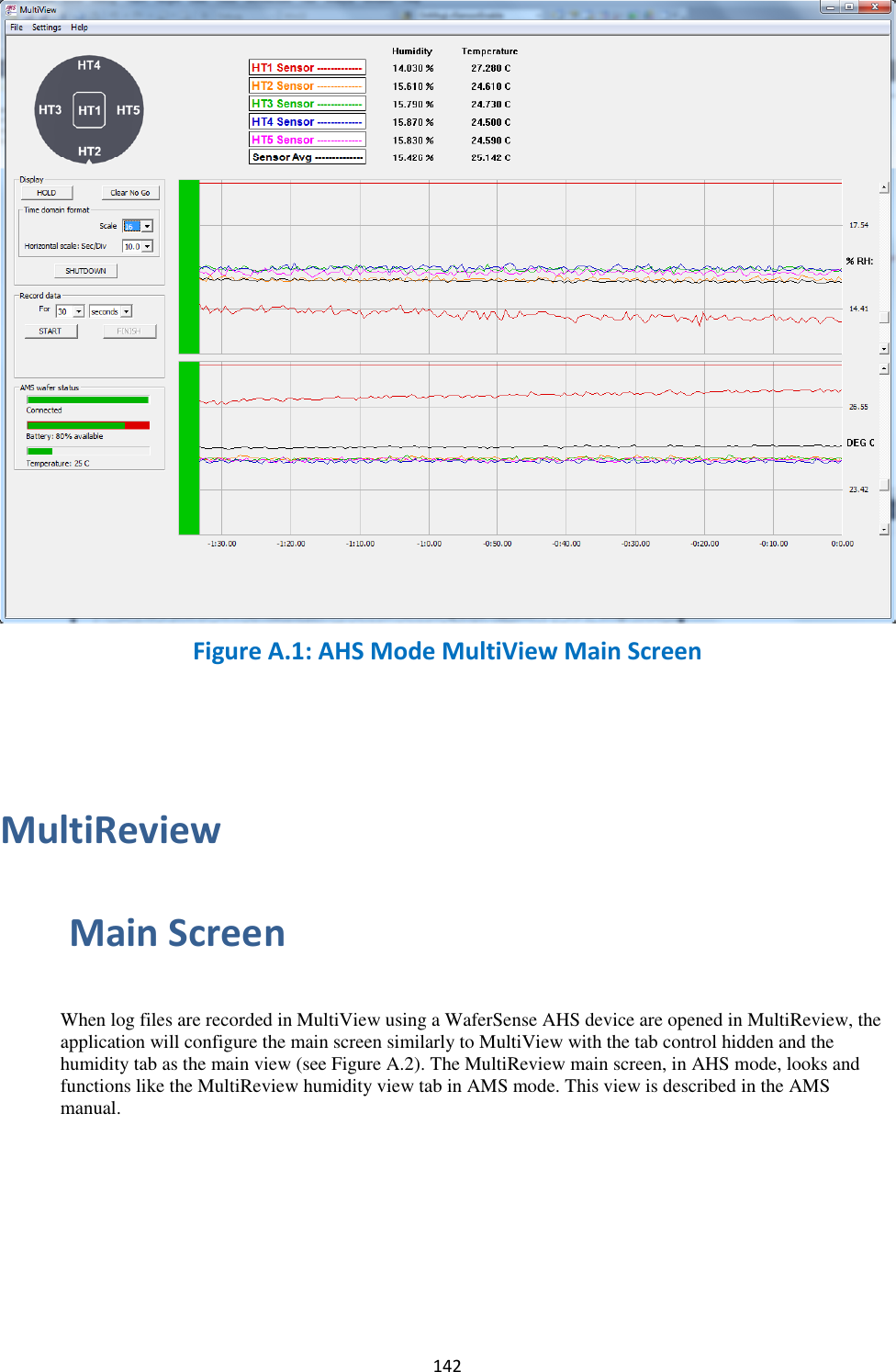
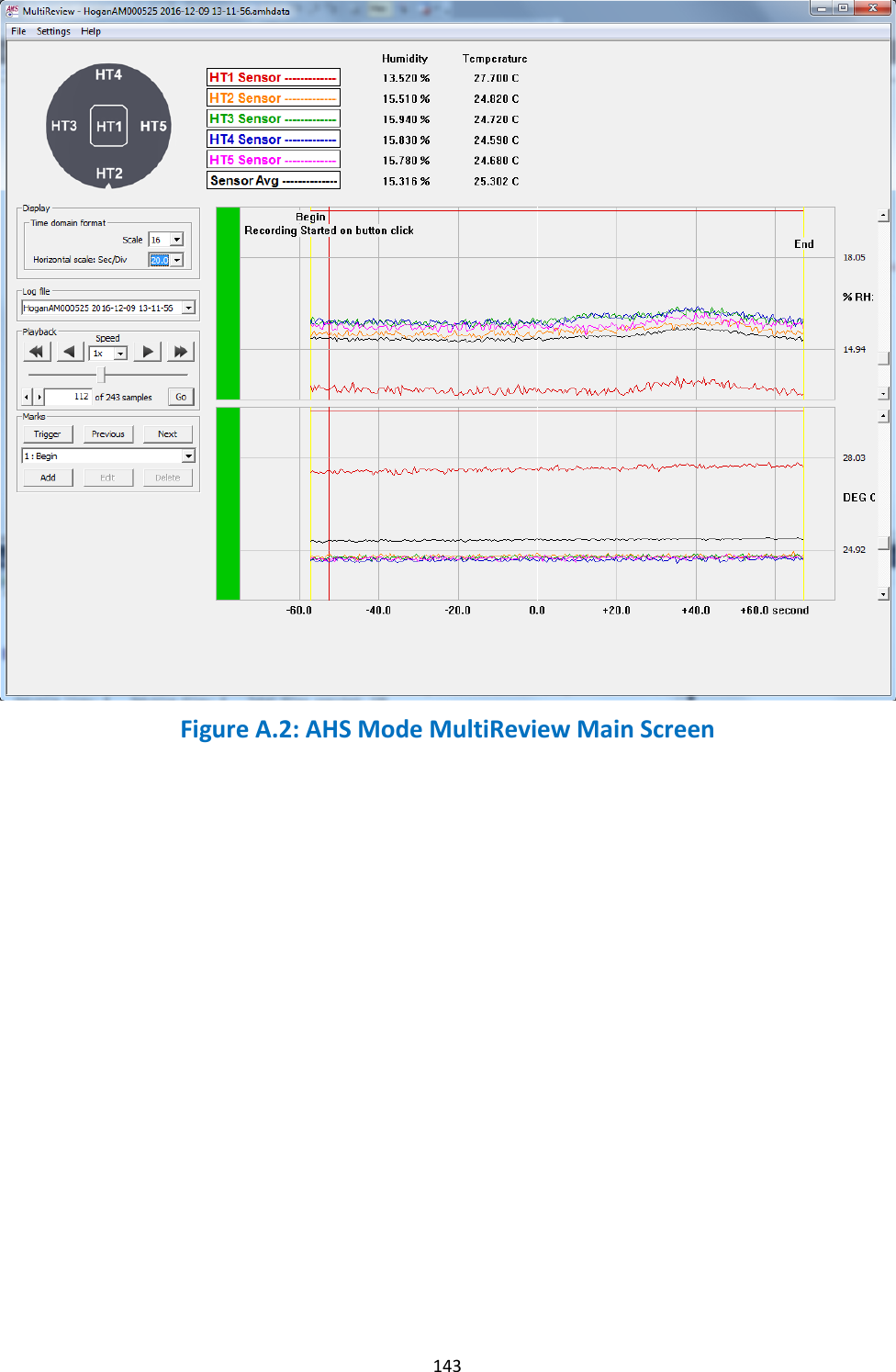